(2016.04)
日本接着学会誌 Vol.52 No.4 2016
真空紫外光を用いた高分子材料の直接接合
Direct Bonding of Polymer Materials Using Vacuum Ultra-violet
山田 剛(ウシオ電機)
重藤 暁津(物質材料研)
1.はじめに
Xe エキシマランプは中心波長172nmの真空紫外光(Xeエキシマ光)を効率よく放射する光源である。Xeエキシマ光を高分子材料に照射することによって表面を活性化し、更に活性化した表面同士を密着させることによって、大気圧下で低温の直接接合が可能である。本報では、代表的なシリコーン材料であるPDMS (ポリジメチルシロキサン)同士の直接接合を例に取り、表面改質および接合特性について報告する。
2.エキシマランプによる真空紫外光の発生
エキシマランプは単一波長、高効率、瞬時点灯/点滅が可能、低温処理が可能、ランプ形状・点灯方向の自由度が高い、水銀フリーと言った様々な特長を持った光源である¹⁾。中でも、中心波長172nmの真空紫外光を発生するXe エキシマランプは、精密ドライ洗浄、表面改質技術の要として、フラットパネルディスプレイ製造や半導体製造で広く利用されている。Xe エキシマランプによる精密洗浄・表面改質の原理は、高いフォトンエネルギー(172nm≒7.2eV)を持つXeエキシマ光が基盤表面の有機コンタミネーションを分解し、同時に、処理雰囲気中の酸素分子を分解して活性酸素(O(³P)、O(¹D)、O₃等)を発生させ、これらの活性酸素種が基盤表面の不純物を酸化除去するというものである。
このランプを搭載した真空紫外光照射装置の一例を図1に示す²⁾。Xeエキシマ光は酸素による吸収が大きいため、ランプを収納する容器(ランプハウス)内部は光を吸収しないガス(一般的には窒素)で置換され、合成石英ガラスからなる窓を通して放射される。ランプハウス内には照射面積に応じて複数本のランプが並べられ光を効率よく取り出すためにミラーが配置されている。通常は雰囲気の安定している大気中で使用されるが、より光の利用効率を高めるため、処理雰囲気の酸素分圧を下げて使用することも行われている。また。照射窓ガラスを無くしたタイプの照射装置も使用されている。
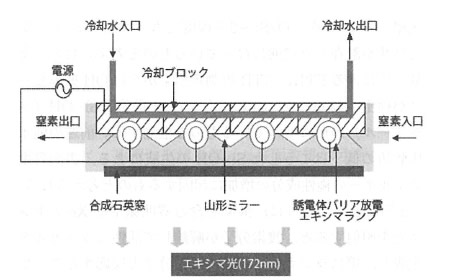
図1:真空紫外光照射装置の一例
3.真空紫外光を用いた高分子材料の直接接合
一般に、高分子材料の接合には接着剤が用いられているが、接着剤自身の耐候性や耐熱性が問題となる場合や、接着剤成分が製品機能に対して好ましくない影響を与える場合があり、また有機溶剤フリーの観点からも接着剤レスの直接接合が求められている、直接接合手段として、例えば溶着を利用した手法もあるが、高温プロセスが必要な点や材料の組み合わせによっては十分な接着性が得られない等の問題がある。またマイクロ流路プレートの貼り合せなど、接着界面に微細な空隙を形成したい場合には寸法安定性の点で溶着は難しい。
このような問題の解決手段として、真空紫外光を用いた接合技術が期待されている。³~⁸⁾酸素を含む雰囲気下で真空紫外光を高分子材料に照射すると、上述の精密洗浄と同様の原理により高分子材料表面の有機コンタミネーションが除去され、更に高分子材料表層の結合を切断/酸化してカルボキシル基、水酸基、カルボニル基等の極性官能基を生成する。これらの活性化した材料表面同士を重ね合せ、互いの表面を十分近くまで接近させると、界面の極性官能基間に主に水素結合力が生じて接合する。材料によっては、更に熱を加えることでより強固な接合が得られることが分かっている。真空紫外光源としてXeエキシマランプを用いることによって、大気圧下での接合プロセスの実現が期待できる。
特にシリコーン材料は、耐熱性に優れ、シロキサン骨格が丈夫で柔軟性に富んだ性質を持つことから、エレクトロニクス、光学、医療分野等で幅広く用いられている。しかしその表面エネルギーの低さから接着性に乏しい。本稿ではPDMS(ポリジメチルシロキサン)を例に取り、Xeエキシマ光による表面改質及び直接接合特性について説明する。
4.Xeエキシマ光を用いたPDMSの直接接合
4.1.試料
PDMS材料として、高精細転写用シリコーン印象剤(主剤:SIM-260、硬化剤CAT-260,信越化学)を用い、主剤と硬化剤を10:1の割合で混合し充分に撹拌して真空脱泡をおこなった後、所定の形状のモールドに流し込んで、自然対流式加熱炉で150℃、40分の加熱硬化を行った。試料形状は、後述の接触角測定及び引張破壊強度測定については10×10×t2㎜、XPS及びAFMについては約5×5×t0.5㎜の大きさとした。なお、表面分析及び接合面として使用する表面はホウ珪酸ガラスで型取りした面を用いた。ただし、本稿の最後で述べる、照射後の放置時間による表面組成変化を調べた実験に関しては、PDMS材料としてSylgard184(東レダウ)を用い、100℃、120分の加熱硬化を行った試料を用いた。
4.2.Xeエキシマ光照射による表面改質
Xeエキシマランプとして、Min-excimer(USHIO Inc.)を用いてPDMSの表面改質を行った。ランプ表面から試料までの距離を2㎜とし、大気中(20~23℃、RH30~40%)で照射した。なお、試料表面におけるXeエキシマ光の照度は約7mW/cm²である。
所定の露光量を照射した直後のPDMS表面の純水接触角を、接触角計(DMe-201、協和界面科学)で測定した結果を図2に示す。照射前に110°程度であった接触角が、Xeエキシマ光の照射によって低下していき、1000mJ/㎝²程度の露光量で接触角10°以下にまで低下した。このようにPDMSにXeエキシマ光を照射することで、表面を強力に親水化することが可能である。
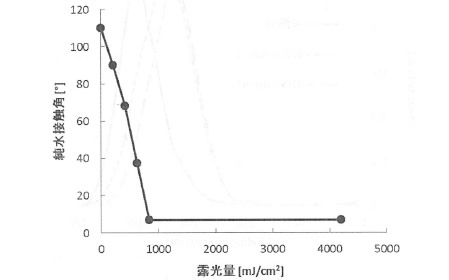
図2:Xeエキシマ光照射によるPDMSの純水接触角変化
次に、Xeエキシマ光照射後のPDMS表面のXPS分析をおこなった。XPS分析装置への試料導入時間が必要であるため、分析は光照射をしてから約30分後に行い、またXPSの検出角度は45°とした。検出された元素はSi、O、Cのみであり、Si2p、O1s、C1sスペクトルを用いてそれぞれの元素の定量分析をおこなった。Siで規格化したO及びCの元素比率を図3(a)に示す。1000mJ/cm²にかけてOが急激に増加し、ほぼ同時にCが減少していることが分かる。また、最大値で規格化したSi2pスペクトルを図3(b)に示すが、元々102eV付近にあったピークが露光量の増加とともに高エネルギー側にシフトし、最終的には103.5eVまでシフトした。これはSiに結合するO原子の数が増加したためと考えられ9.13.14.)、上述のC/Siの減少及びO/Siの増加は、主にPDMSの中のSi-C結合がSi-O結合に変化したものと考えられる。またPDMSに対してXeエキシマ光やO2プラズマを照射すると、表面が酸化されてガラス状のネットワークを形成することが知られている。11.~13.) ①純粋なPDMSの元素比率はO/Si=1.0であり、②完全にガラス状のネットワークを形成した場合(SiO2)にはO/Si=2.0、③CとOが全て置換した直鎖シロキサンではO/Si=3.0となるが、図3(a)では露光量の多い領域でO/Si=2.5程度となっており、主に②及び③が混在した状態になっているものと考えられる。文献9.10.)によるFTIR-ATRの測定結果からはOH振動ピークが検出されており、Siに結合したO原子はSi-OH(シラノール)の形になっているものと推測する。前述の純水接触角の低下はこうしたSi-OHの生成による、表面自由エネルギーの極性成分の増加に起因するものと考えられる。
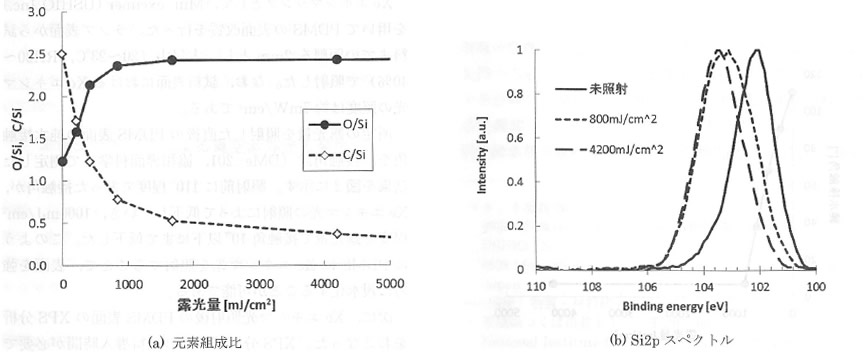
図3:Xeエキシマ光を照射したPDMS表面のXPS分析結果
2項で述べたように、酸素を含む雰囲気下でXeエキシマ光を照射すると、酸素分子が解離して活性なラジカルを生成し、更にラジカルが周囲の気体分子と反応することで種々の活性酸素を生成する。PDMS表面では、光子によりSi-C及びC-H結合の切断と同時にこれらの活性酸素による化学反応が生じ、酸化が進行するものと考えられる。
また、Xeエキシマ光照射前後のPDMS表面形状をAFM(L-traceⅡ、日立ハイテクサイエンス)で測定した。DFMモードで□2μmの領域の形状測定をおこなった結果を図4に示す。両者で測定位置が異なっていることに注意する必要はあるが、Xeエキシマ光照射によって表面の微細な凹凸が減少する傾向がみられた。表面を粗化するような高速原子が存在せず、光と活性酸素がPDMS表面を化学的に改質していくプロセスであるため、表面凸部が僅かに反応が速くなり平滑化したものと考える。このようにXeエキシマ光処理においては、表面に物理的なダメージを与えることなく、平滑な形状を保った表面改質が可能である。
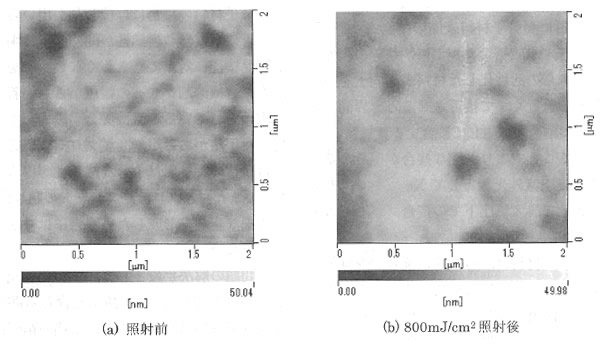
図4:Xeエキシマ光を照射したPDMS表面の表面形状(AFM)
4.3.直接接合および破壊強度試験
Xeエキシマ光を照射したPDMS表面同士を向い合せ、密着させることで直接接合をおこなった。試料形状は10×10×t2㎜とし、前述のエキシマランプで所定量露光した後に密着させ、加圧力0.2MPa、温度22℃もしくは100℃、300秒のプレスを行うことで接合させた。接着面の破壊強度を調べるため、接合後の試料を治具(□15×50、SUS)に接着剤で固定し、引張試験をおこなった(図5)。なお接着剤を完全に固化させるため、引張試験は試料作製の2日後におこなった。引張試験速度は10㎜/secとし、試料が破壊した時の最大荷重をデジタルフォースゲージ(ZTA-500N、イマダ)で測定した。破壊荷重を試料の接合面積で除すことによって破壊強度とした。破壊強度測定結果の一例を表1(プロセス①及び②)に示す。露光量200mJ/cm²において、100℃でホットプレスをした場合には、PDMSの接合界面以外からの箇所から破壊しており、これ以上の接合測定は不可能であった。一方、室温でプレスした場合にも1MPa程度の接合強度が得られたが、破壊個所は接合界面であった。加熱をすることにより接合強度が向上していることから、接合界面でSi-OHの脱水縮合反応が進行しているものと考えている。
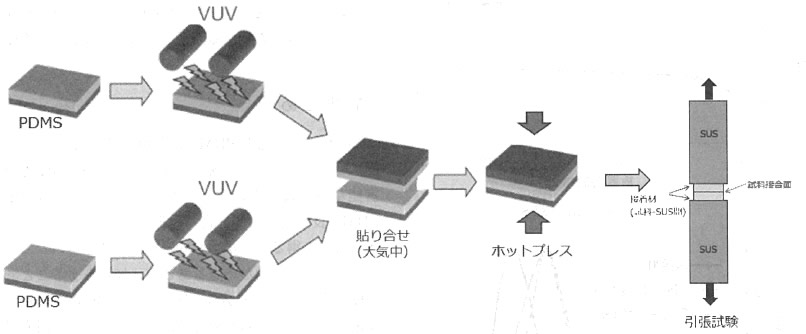
図5:直接接合及び強度試験方法
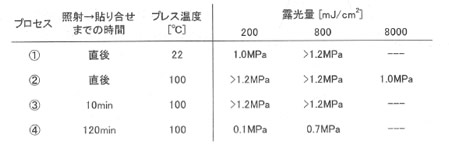
表1:破壊強度測定結果
露光量を変えた場合の破壊強度測定結果を表1に合わせて示す。露光量800mJ/cm²では強固な接合が得られたが、かなり露光量を増やした8000mJ/cm²では接合強度が低下した。8000mJ/cm²照射した後のPDMS表面を顕微鏡で観察すると、表面に亀裂が発生していた。これはPDMS表面のSi-C(メチル基)がSi-OHに変化し、更に脱水縮合してガラス状のネットワークを形成することで体積収縮したために引張の内部応力が発生し、ガラス化による材料の脆化と相俟って亀裂が生じたものと考えられる。このような表面同士を貼り合せた界面では、亀裂部分から破裂が進行しやすいこと、及び、亀裂部分の凹凸が大きくかつ材料表面の柔軟性が失われているために表面同士が十分近くまで近づくことができず相互作用力が弱まったことにより、接合強度が低下したものと考えられる。このように露光量を増やしすぎることは材料表面を過度に劣化させることになるため、露光量の管理を行うことは重要である。
4.4.照射後の引き置き時間が接合強度に及ぼす影響
真空紫外光やプラズマで表面を活性化したPDMSの表面状態は、活性後の時間経過とともに変化することが知られている14.~19.)。ここでは一例として、文献15.~19.)等で広く用いられているPDMS(Sylgard184)に対してXeエキシマ光を照射した後の表面状態の変化を、接触角及びXPSで分析した結果を示す。Xeエキシマ光を800mJ/cm²照射した後、クリーンルーム環境下(20~23℃、RH30~40%)で放置したPDMS試料の純水接触角を図6(a)に、XPS分析結果を図6(b)(c)に示す。照射直後には10°以下まで低下していた接触角が放置時間の経過とともに増加していき、また元素比率に関してはC/Siが増加し、O/Siが減少している様子が分かる。またSi2pスペクトルが低エネルギー側に膨らんでおり、元素比率の変化が単に表面に有機不純物が付着したのではなく、Siの結合状態に変化が生じていることを示唆している。文献18.)では資料内部の低分子シロキサンが表面へ析出することによって、時間経過とともに表面が疎水化すると言われているが、本実験結果もこれと矛盾しない。
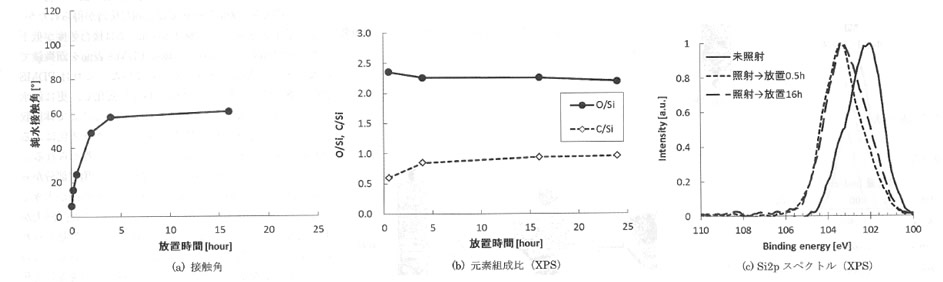
図6:Xeエキシマ光を照射後,CRに放置したPDMS表面の経時変化(Sylgard184)
こうした照射後の放置時間が接合強度に及ぼす影響を調べるため、以下の実験をおこなった。200mJ/cm²および800mJ/cm²照射したPDMS試料をクリーンルーム環境下(21℃、RH32%)で10分もしくは120分放置した後で接合し、引張強度試験をおこなった。照射後に放置する時間を設けた以外は、4.3節と同じ条件で試料を作製した。引張破壊強度の測定結果を表1(プロセス③及び④)に示す。120分放置した場合には、照射直後に接合した場合に比べて強度低下しており、特に露光量が200mJ/cm²の場合には接合強度が非常に弱くなった。このようにPDMS直接接合において、Xeエキシマ光照射後の引き置き時間は接合強度に大きく影響する因子であるので注意する必要がある。
5.まとめ
Xeエキシマ光をPDMSに照射することによって、表面に物理的なダメージを与えることなくSi-OH等の酸化官能基を形成することができる。このように活性化したPDMS表面同士を向い合せ、貼り合せることによって強固な接合を得ることができる。接合のメカニズムについては未だ分かっていない点もあるが、加熱をすることで接合強度が向上することから、接合界面でSi-OHの脱水縮合反応が進行しているものと考えている。また、露光量が大きすぎると材料を過度に劣化させてしまうこと、及び照射後の引き置き時間が接合強度の大きく影響することに注意する必要がある。
本稿ではPDMS同士の直接接合を例に取って説明を行ったが、他のシリコーン材料やガラス、石英、Si酸化膜についても同様の接合機構が働くと考えられ、実際に強固な直接接合をおこなうことが可能である。
今後は他の高分子材料や無機材料についてもプロセスの検討をおこない、適用範囲を広げていきたいと考えている。