光技術情報誌「ライトエッジ」No.6(1996年5月発行)
月刊クリーンテクノロジー
(1995年3月号)
特 集
(半導体製造装置におけるパーティクル対策)
エッチング装置のパーティクル対策
ウシオ電機(株)仲田 重範
はじめに
従来より真空装置のパーティクル対策管理にはサーフェススキャナーが広く用いられており、数多くの実績がある。しかし使用方法、目的によってはサーフェススキャナーにも欠点や限界があることが指摘されている。
またパターン外観検査装置は実ウェーハを測定できるので最近多く使用されてきているが、スループットとコストの点で製造ラインで使用するには問題もある。
今回は最近注目されているin-situモニターをエッチング装置に用いた場合、どんなデータが得られどんなメリットがあるかについて日本での実測データを中心に述べる。
in-situモニターの特徴
測定の原理は気中カウンターと同じ光散乱方式であるが、エアポンプによる吸引を行わないので、真空装置においても圧力に関係なくパーティクルの自然な動きを検出できる。
エッチング装置へのセンサーの取付は、例えば第1図のようにロードロックやプロセスチャンバーの排気ラインに取付けられ、低圧ガスに乗ってポンプ側に運び出されるパーティクルを測定している(1)。
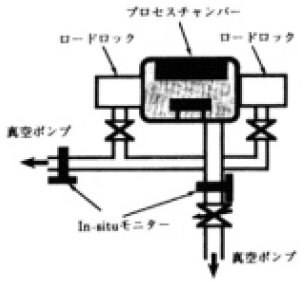
第1図 センサーのエッチング装置への取り付け配置図
In-situモニターの特長をサーフェススキャナーと比較してまとめると次のような点が挙げられる。
- (a)リアルタイム測定であり、異常をすぐ検出可能
- (b)連続測定であり断続的、突発的事象も検出可能
- (c)実プロセス中での測定が製造インにおいても可能
- (d)発塵源の推定にも有効
- (e)低コスト(モニタウェーハ、検査時間の大幅低減)
- (f)パーティクル管理の自動化が可能
ロードロックでの測定
真空装置における粒子汚染の原因の一つとしてロードロックでの排気時とベント時のパーティクルの舞い上がりが良く知られており、実際の装置においてもスロー排気、スローベント等の対策がよく行われている。それらの条件の最適化にもinsituモニターを効果的に使うことができる。
第2図にはロードロックにおける排気とベントサイクル時の、サーフェススキャナーとin-situモニターのそれぞれのカウント数の相関を調べた実験結果を示す(2)。両者のデータは比較的良い相関を示しており、insituモニターの有効性を示している。この例では実験開始直後にin-situモニターの値が高いカウントを示している。このパーティクルは排気時の減圧化によるガス温度の急激な低下によって、小さなパーティクルを核に水蒸気の凝結が生じ大きなパーティクルに成長したものと考えられる。水分に取り囲まれた状態のパーティクルはウェーハへの付着確率が高くなり、これも汚染を増加させる要因となる(3)。さらに気相から固相へのガス粒子変換のメカニズムについても研究されており(4)、ロードロックのドライ窒素ベントやスロー排 気等の条件最適化も重要なパーティクル対策であると考えられる。
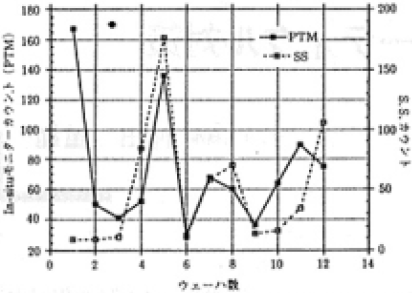
第2図 ロードロックにおける排気、ベントサイクル当たりのパーティクル数
プロセスチャンバーでのデータ
プラズマ中のパーティクル測定についてはSelwynらによりレーザ光とビデオカメラ等を使って計測されている(5)(6)。しかしこの方法は研究用には使用可能でも実際の製造装置での測定は非常に困難である。しかしin-situモニターは実際の製造装置でも比較的簡単に実プロセス条件下で測定できる。
第3図には典型的な酸化膜エッチャーの排気ラインでの測定例を示す。発塵のタイミングとしてはRFをオンにした後に徐々にパーティクル数は増加していき、RFオフ時にピークカウントが生じその後急減している。またHeのガスフロー時にもスパイク的にパーティクルを検出しているが、その後の対策でこのタイミングでのパーティクルは検出されなくなった。
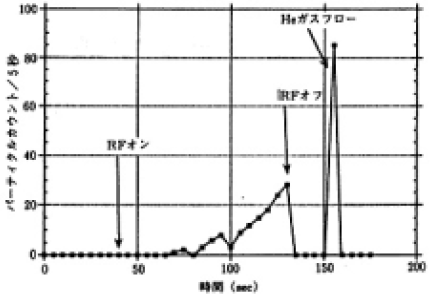
第3図 酸化膜エッチング中の発塵タイミング例
第4図に示すように粒径的にはRFオン後から徐々に大きくなり成長していることが分かる。この例では0.35μm以下の比較的小さい粒子がほとんどであった。これらのデータはパーティクルがプラズマシートにトラップされて成長していくというSelwyn等の発塵のメカニズムと矛盾しない結果である。
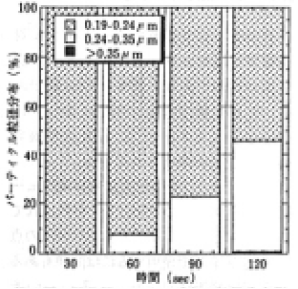
第4図 酸化膜エッチング中の粒径分布例
ただし装置クリーニング後には比較的大きな粒子が多数検出される場合もあるが、これらの異なる粒径分布を持つパーティクルは発生メカニズムも少し異なると推定される。このようにin-situモニターではプロセス装置内のパーティクルをリアルタイムで測定できるので、発塵のタイミングなどもわかり発塵源の推定や 効果確認も容易にできる。
製造装置での実測データ
製造ラインにおいてin-situモニターで長期測定を行えば、装置のクリーニング時期の確認やトラブル検出にも非常に有効である。次にその実例を紹介する。
第5図は条件の異なるA、B2つプロセスが混在した場合の30日間にわたるデータである。プラズマパワーが大きく印加時間が長いプロセスBの場合には、装置が汚れてきたと推定される後半においてパーティクルは急増している。それに対しプラズマパワーが小さく印加時間も短いAプロセスの場合は、パーティクルの増 加スピードはわずかであり、パーティクルレベルは装置内の汚れのみで決まるものではないことがわかる。
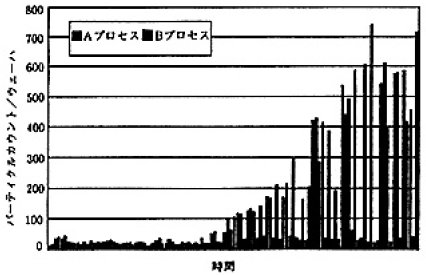
第5図 Sinエッチング装置におけるウェーハ1枚当たりの平均カウント数
第6図は装置のウェットクリーニング間のパーティクルレベルを測定したものである。この場合もパーティクルは増加傾向を示しているが、それに加えてスパイク的なカウントも生じている。
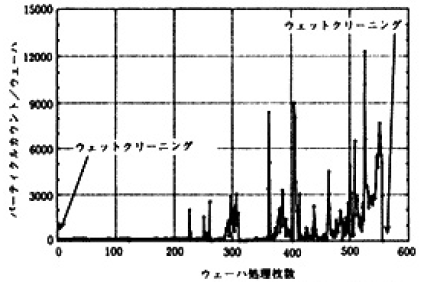
第6図 ウェットクリーニング間のパーティクルレベルの変化
実際の製造装置では、このようにゆっくりした増加トレンドを示す場合以外に、特定の理由により粒子数が突発的に増加する場合も多い。
その1例として第7図に示すように、製造ラインにおいてロット間の休止時間が長い場合に、処理再開直後に粒子数が急増する現象も観測した。この現象の詳細な原因は不明であるが、いつも現れるのではなく種々の要因が重なった場合に生じている。
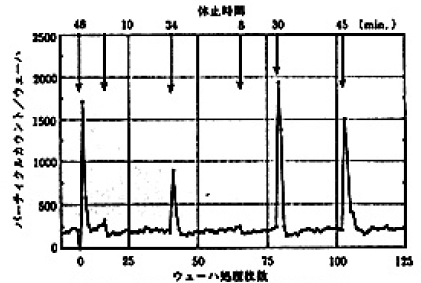
第7図 長い休止時間直後の突発的発塵の例
また第8図には異常放電時にパーティクルの急増を検出したデータの例を示す。この場合には日常のサーフェススキャナーでの検査では検出できなった。
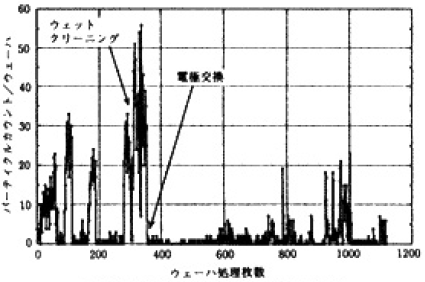
第8図 異常放電時のパーティクル検出例
その他にも電極要因のトラブルやメンテ時の作業に関係したトラブルなどが検出された例もある。このようにリアルタイム測定であるので、すぐにトラブル検出でき発塵源を究明し大きな成果を上げている。
以上述べたように実際の製造時のパーティクルレベルは、装置の汚れ具合の他にプロセス条件、膜種、装置の運転状況等が複雑に影響しており、突発的に多くのパーティクルが生じることも多い(7)。この様な場合定期的なミラーウェーハによるチェックでは検出が困難であり、実プロセス中のパーティクルを連続でリアルタイム測定することの重要さが分かる。
サーフェススキャナーとの相関
製造ラインにおいて、プラズマをかけないで測定したサーフェススキャナーのデータとは相関が得られない事も多い。しかしこれはミラーウェハでは実プロセス中の正確な粒子汚染状態を測定できていないためであると考えられる。従ってin-situモニターとの正確な相関を調べるには、ウェーハ上のパーティクルはできるだけ実プロセスに近い条件で測定する必要がある。例えば第9図に示すように実ウェーハを検査できるパターン外観検査装置とはかなり良い相関が得られている(8)。
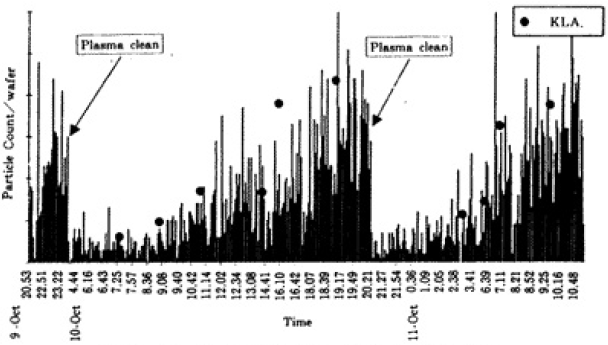
第9図 パターン外観検査装置とin-situモニターとの相関例
in-situクリーニングとin-situモニター
第10図に示す様にin-situクリーニング時には、エッチング時に比べても効率良く多くのパーティクルをカウントをしている。実際にウェーハが処理されているという点ではエッチング時のカウントがより重要である。しかしエッチング時のパーティクル増加を引き起こす潜在的な要因としてのチャンバー内の汚れを効果的にモニターできるという点で、in-situクリーニング時にin-situモニターで検出することは今後有効な方法になると考えられる。
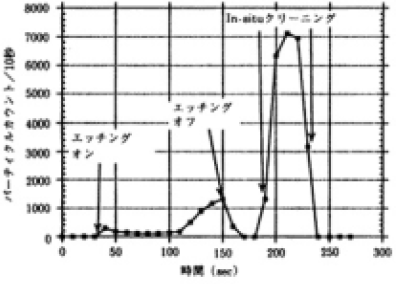
第10図 エッチング及びin-situクリーニング時の発塵タイミング例
問題点と課題
現在in-situモニターはエッチャーをはじめ種々の真空プロセス装置で使用されてきている。しかし日本においては米国に比べると製造ラインでの導入が遅れている。その理由と今後の課題を整理するとつぎのような点が考えられる。
(a)量産ラインでのメンテナンス性および信頼性
従来は一部のエッチャーやCVD等において、デポによる汚れの点で量産ラインで使用するには若干問題があった。しかし現在の新センサー(M-70)ではほぼクリアできたと考えられる。
(b)アプリケーションのノウハウ
一般に装置構造やプロセス条件が異なるとパーティクルの発塵レベルやパーティクルの挙動も大きくことなる。したがってどの装置のどの場所にどのように取り付ければ良いかが重要である。今後は米国製の装置での成果を参考にして、日本製の装置についても装置メーカーやデバイスメーカーの御協力を得て更にノウ ハウの蓄積が必要である。
(c)センサーの改良
最新の製造装置にも対応出来るようにするためには更なるセンサーの高感度化が重要である。同時にターボポンプの直前でも測定のできるプラズマ光ノイズに強いセンサーの完成が待たれる。
まとめ
In-situモニターは実際の製造ラインにおいてもリアルタイムで連続測定できる特徴があり、種々の有効なデータが得られている。プロセス中の発塵状態を調査研究する以外にも製造ラインにおいて汚れの程度をモニターし、クリーニングの時期を知るためにも有効である。
またサンプル測定では検出の難しい突発的な発塵も検出でき、製品の歩留り向上や検査コストの低減にも大きく寄与できる。今後日本においても製造ラインで有効利用ができるよう更に努力していきたい。 データ取得についてご協力いただいた各ユーザーの方々に感謝致します。