光技術情報誌「ライトエッジ」No.7(1996年7月発行)
<特集>熱放射加熱
3 応用例
3.1 熱定着への応用
3.1.1 熱定着の現状
現在の熱定着の主製品として各企業・商店に広く導入されているPPC(普通紙複写機)、 PPF (普通紙ファクシミリ、LBP (レーザビームプリンタ)等OA機器が挙げられる。これらの定着方式は図3.1のように分類される。
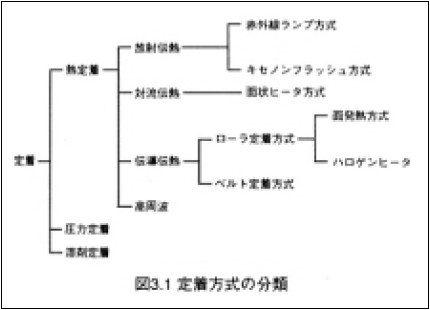
これらの方式の中で現在もっとも多く採用されているのが、ハロゲンヒータを使用したローラ定着方式である。その理由として熱効率が高く、使用温度が160〜200°Cと比較的低く安全性に優れていることと、輸送系と定着系が一体であり、装置が小型にできるためである。
3.1.2 ローラ定着方式
ローラ定着の例として図3.2にLBPの構造図と定着方法を示す。定着方式に示したヒー夕としては主にハロゲンヒータが使用されている。
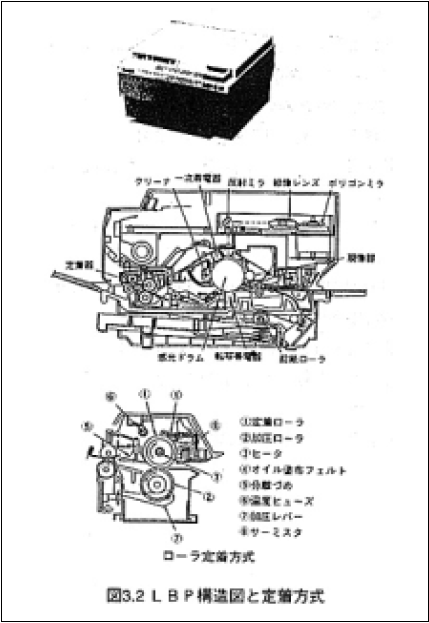
熱ローラの定着の機能図は図3.3の通りとなる。OA機器において紙に転写されたトナー (現像剤)は弱い力でしか付着していないため、簡単に落ちてしまう。そのため、定着ローラの熱と加圧ローラの圧力でトナーを押しつぶし、紙に浸透させることにより固着させる。
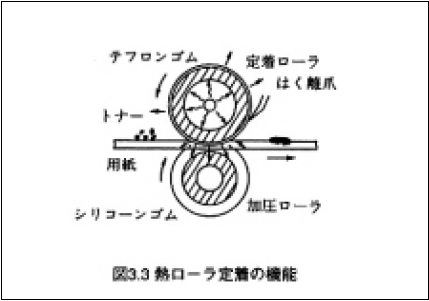
3.1.3 ハロゲンヒータの構造・特性
(1)ハロゲンヒータの構造例
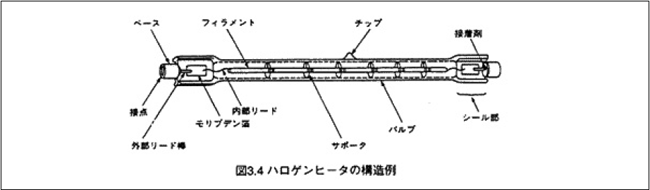
(2)ハロゲンヒータの特性
ローラ定着方式に使用されている一般的ハロゲンヒータの特性は下記の通りである。この範囲外のものも製作可能である
- ① 定格電圧100〜240V
- ② 定格電力300〜1000W
- ③ 色温度 2200〜2500K
- ④ 寿命 2000〜5000h
- ⑤ 配熱分布任意
3.1.4 応用例
(1)ハロゲンヒータ2本使い
① 待ち時間の短縮
PPC等は電源を入れてからローラが所定の温度に上がるまで使用できない。そのためローラに2本のヒータをいれ、ローラが所定の温度に達するまで2本のヒータを点灯し、待ち時間を短くする使い方をしているものがある。複写する時は1本を消し、機器の総消費電力を抑えている。ハロゲンヒータの場合、任意に電力を変えることができる特性を応用している。
② 紙幅対応
PPC等はサイズの異なる紙を定着させる場合がある。その場合図3.5のような発熱部分の異なるフィラメント配置の2本のヒータを使用し、紙幅に応じて1本または2本点灯し定着を良くしている。ハロゲンヒータの任意に熱分布を変更できる特性を応用している。特殊な例としては3本、4本のヒータを使い分けているものもある。
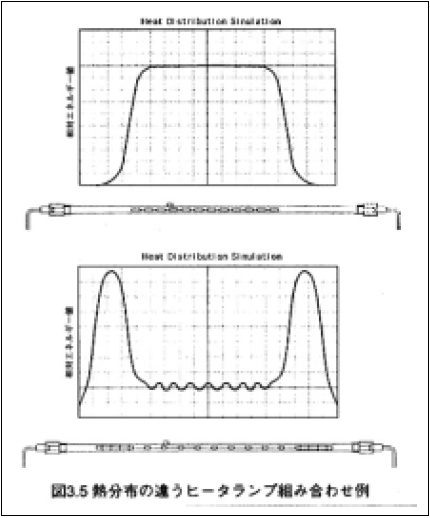
(河村忠和)
3.2 塗装乾燥への応用
3.2.1 塗料の成分2)
塗料の主成分は、樹脂類・溶剤・顔料の3 つである。樹脂類は塗料皮膜の性能を決定づけるもっとも重要な成分で①植物油、②天然樹脂、③合成樹脂、④セルロース(繊維素)などが用いられる。①②は天然の産物であるが、③④は石油化学製品を原料とする人工産物である。表3.1に代表的な樹脂区分を示す。
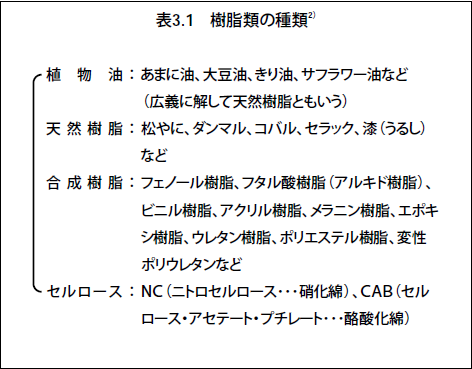
溶剤は樹脂類を溶解して塗りやすい状態、すなわち適度の流動性を持たせるもので、各種の有機溶剤が用いられる。この有機溶剤はほとんどが石油に由来するもので、無公害、省資源の見地からその節約が強く要請されている。表3.2に代表的な有機溶剤を示す。
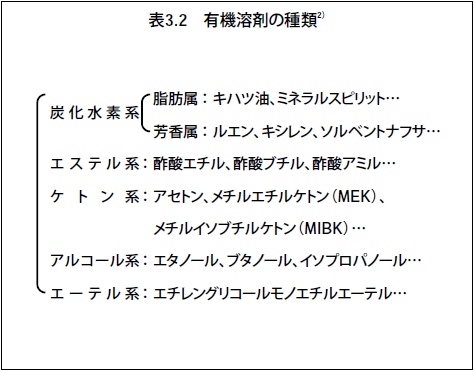
顔料は、塗膜を不透明にし任意の着色をするための色料で、鉱物質の無機顔料と人工の有機顔料とが用いられる。無機顔料は安価で隠ぺい力が大きく、日光・熱にも強いがさえた色ではない。有機顔料は鮮やかな色が出るが隠ぺい力はやや劣り価格も高い。例えば、一般の建築塗装用なら無機顔料間の調色で十分にまかなうことができる。標識やアクセントカラー、あるいは自動車、OA機器やFA機器、家電製品などの色のさえが求められる場合には有機顔料でないと色出しができない。
塗料の成分は、以上に述べた3成分のほかに、乾燥剤・可塑剤・分散剤・皮張り防止剤・沈殿防止剤などの第4成分が少量配合される。これらの諸成分がバランスよく配され、塗りやすく、良く渴き、はがれず、耐久性の優れたものがよい製品ということになる。表 3.3に色別の区分を示す。
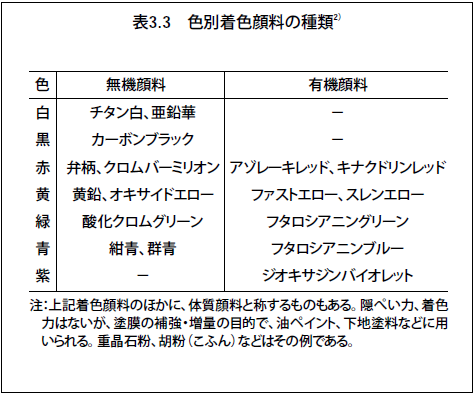
3.2.2 塗料の分光吸収特性3)
物質を構成している原子のつながりは、その構造に固有のいろいろな振動様式をもっていて、これらは分子振動、格子振動(結晶構造の場合)などと言われ、特定の振動数を有している。すなわちそれぞれの物体は、その物体を構成する物質に固有の(例えば)分子振動領域をいくつか持っている。このような振動数が遠赤外域にあるものは赤外活性物質と呼ばれる。遠赤外線の吸収とは物体に遠赤外線が照射されたとき、そのうち物質構造で定まる(分子)振動数に一致した電磁波と共鳴して(分子)振動が励起されることである。このような振動は熱振動として具現し、物体の温度は上昇する。
樹脂類・有機溶剤のうち、主なものについて、分光吸収特性を図3.6に示す。金属などを除いた多くの物質は赤外活性物質である。樹脂、塗料はその主たる物であるが、ほかにゴム、繊維、蛋白、でん粉などの食品成分、無機鉱物(セラミックス類)も同様に赤外活性物質である。さらに赤外加熱・乾燥にとって好都合なことは、水もまた赤外活性である。ここ数年、大気汚染公害および労働安全衛生面に優れていることから水性塗料の普及が著しい。
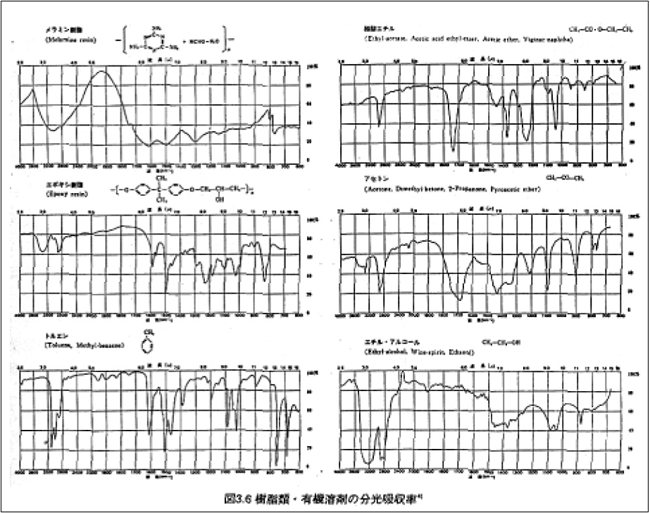
(水川洋一)
3.2.3 ハロゲンヒータによる加熱例
自動車の修理工場などで使用される塗料の乾燥用装置に用いられるヒータには従来、遠赤外線ヒータ、近赤外線ヒータ、または赤外ランプなどがある。
遠赤外線ヒータは全体が棒状で、フィラメントなどからの発熱を遠赤外線放射用コーティング層を介して遠赤外線が放射される。近赤外線ヒータも全体が棒状でフィラメントなどからの発熱により近赤外線が放射される。赤外線ランプは通常の電球形状でフィラメン卜などからの発熱による放射であり、フィラメントの後方のガラス部分にアルミの反射膜が施されている。
ところが、上記ヒータやランプを用いた乾燥装置にあってはそれぞれ一長一短がある。例えば遠赤外線ヒータを用いた乾燥装置では、塗料に対する熱吸収率において色による差がほとんどない利点があるものの遠赤外線放射までにかなりの時間がかかり(図3.7)迅速に乾燥温度に達しないというような問題があった。
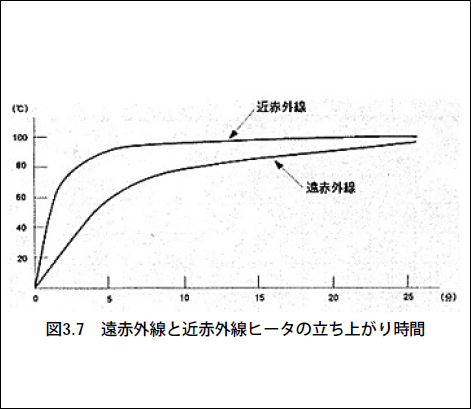
一方、近赤外線ヒータを用いた乾燥装置では、近赤外線の放射までの時間が短く迅速に乾燥温度に達する利点があるものの長手方向に長くセットされた構造のため、衝撃に弱いなどの問題があった。
これに対して赤外線ランプを用いた乾燥装置では、フィラメントの取付状態やその形状などによって温度分布が不均一になりやすく、塗料に対する熱効率が多少悪いものの、上記遠赤外線ヒータや近赤外線ヒータに比較して安価であること、口金として規格品(例えばE26の口金)を用いれば、ソケットを有する既存のほとんどの乾燥装置に簡単にかつ着脱自在に取り付けることができることなどの利点がある。
そこで、従来、自動車修理工場などで広範な用途に対応するためには、遠赤外線ヒータを用いた乾燥装置、近赤外線ヒータを用いた乾燥装置、赤外線ランプを用いた乾燥装置など数台を揃える必要があり、設備費がかさむこと、台数分の収納スペースが必要とされることなどの問題があった。そのため、もっとも広く普及されている赤外線ランプの乾燥装置に着目し、規格品の口金を有する互換性に富んだランプで遠赤外線を放射するランプと近赤外線を放射するランプとを提供して、ユーザが必要によって1台の乾燥装置を適宜使い分けることができるようにした、新しい乾燥用ランプ(ミラー体型ハロゲンヒータ)を提供している。
3.2.4 赤外線ランプ
従来、自動車修理工場などで使われている赤外線ランプは特性が100/110V、250Wで寿命が5000Hrs、形状は口径Φ130mmで全長が 177mm程度のものである(図3.8)。ガラス球内面に蒸着されたアルミ反射膜により一定の方向に赤外線を放射することができる。しかし、この反射膜はミラー設計がされてなく、またフィラメント自身も非常に大きいため熱効率が悪い。
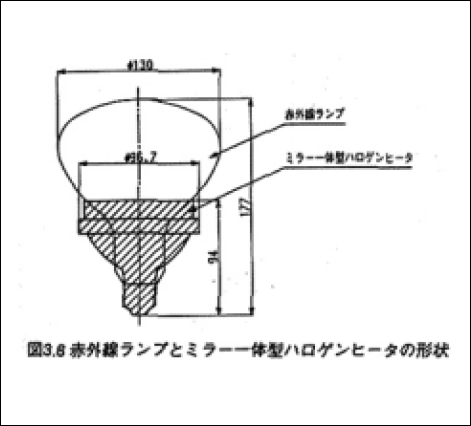
これらの問題点を解消し、熱効率が良く、小型でコンパクト、などの特長を持たすことができたのがミラー一体型ハロゲンヒータ (遠赤外線タイプ、近赤外線タイプの2種類)である。
3.2.5 ミラー一体型ハロゲンヒータ (遠赤外線タイプ、近赤外線タイプ)
ハロゲンヒータの使用と光学的な設計をした反射ミラーおよびミラー内面には金を蒸着したことで加熱性能を大幅に向上させることができ、従来の250W赤外線ランプの乾燥効果を、150W(遠赤外線タイプ)〜200W(近赤外線タイプ)で再現し、最大で40%の省電力となる(図3.9、図3.10)。
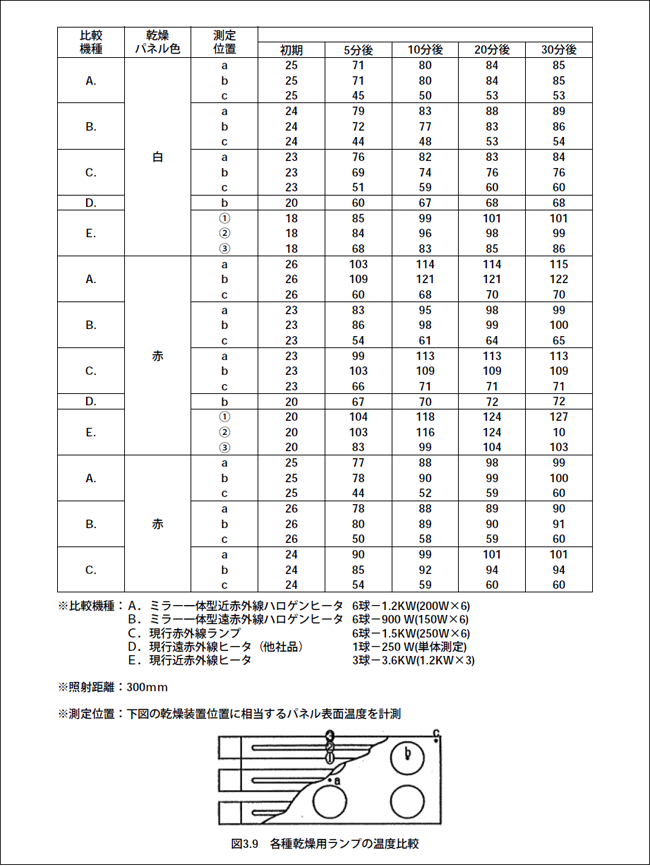
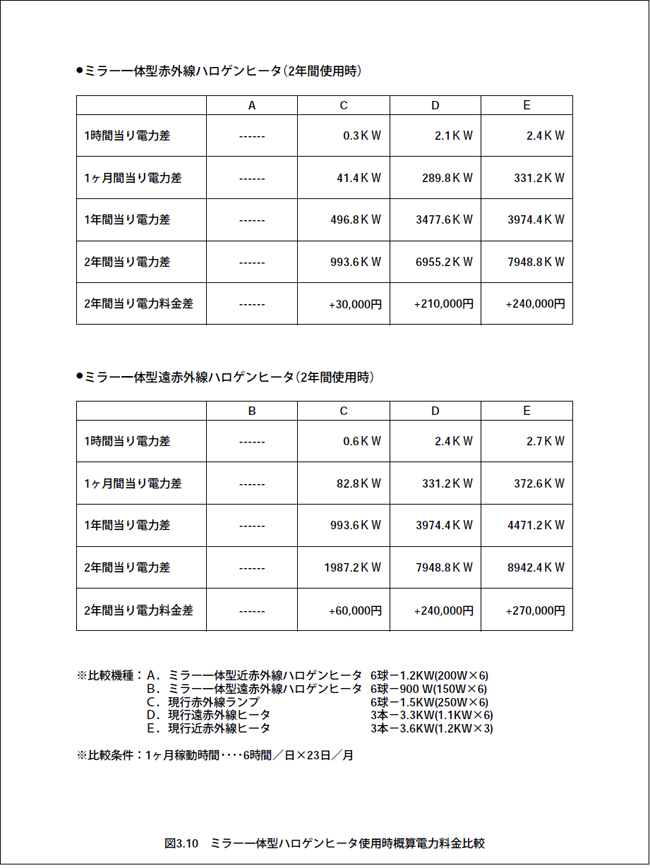
さらに、ハロゲンヒータの使用で小型でコンパクトになり容積比で1/3(図3.8)、ハロゲンサイクルの働きで、寿命末期までほぼ一定のエネルギー放射を維持できる。
また、遠赤外線タイプでもハロゲンヒータの使用で温度立ち上がりも近赤外線と同等時間となった。仕様は現在、遠赤外線タイプで特性が100/110V、150Wで、寿命が2000Hrs、近赤外線タイプで特性が100/110V、200W で、寿命が5000Hrsである(同一形状での出力アップも可能である)。使用方法が限定されているため、点灯条件も調査し、耐振性などを考慮した設計を施している。
(松岡智巳)
3.3 半導体製造工程への応用(液体加熱)
3.3.1 現状
半導体製造用の液体加熱器には、液体の汚染を極力抑えなければならないという厳しい制約がある。このため、使用できる材料は限定され(石英ガラス、テフロン)加熱器の構成もかなり限定されたものとなる。
これまでの加熱は、液体を使用する処理槽の内部に石英ガラスなどでカバーされたニクロム線ヒータやタングステン線ヒータ(図3.11)を入れて直接液体を加熱する投げ込み式が多く用いられてきた。
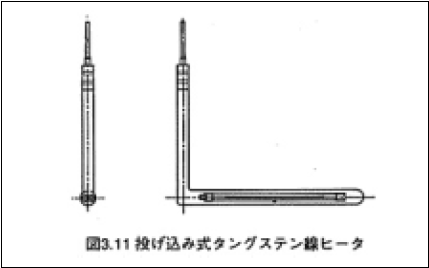
しかし、投げ込み式は、
- ・加熱ムラがある(液体が薬品の場合は、薬液の劣化が早い)。
- ・処理槽が狭くなる。
- ・熱応力によりヒータが破損しやすい(破損時は液体を汚染する)。
などの理由により、直接加熱方式とは使用方法や構成が基本的に異なる間接加熱方式への要求が強くなってきた。
間接加熱方式は、直接加熱方式の欠点を解消するだけでなく、加熱能力の変更にも容易に対処できるなど多くの利点を有している。
3.3.2 間接加熱方式
熱源(ランプ)からの熱放射が石英ガラスを通して液体を直接加熱する方式である(図 3.12)。熱源からの熱放射によって液体が直接加熱されるのは、液体の分子振動と同じ振動数を持った熱放射(電磁波)が液体の分子にあたり、共鳴吸収を起こし、摩擦熱に変換されるためである。このため、加熱性能は熱放射に対する各液体の分光吸収率に強く依存する。
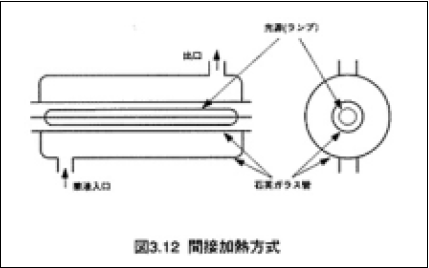
液体の主成分は水なので、水の分光吸収率(図3.13)から液体の加熱にもっとも適しているのは、水の槽の現実的な厚さ10mm程度では波長が約1.3µm以上の赤外線放射をすべて吸収することから、波長約1.3µm以上の熱放射をできる限り多く出し、これ以下の波長の熱放射を一切出さないものが良いことがわかる。
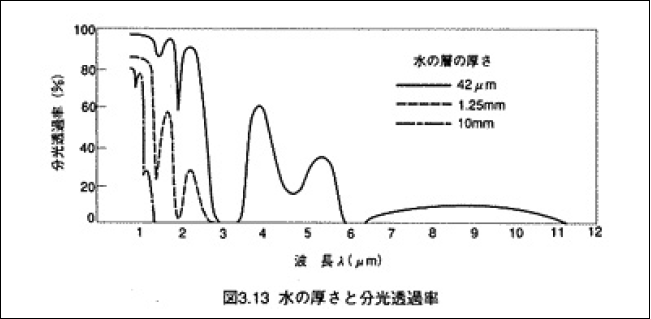
これらのことから熱源として適しているものはハロゲンヒータであり、出力(電力)、波長(色温度)、外観形状、使用条件(各部温度、点滅条件など)をユーザから確認し設計を行っている。
3.3.3 ハロゲンヒータの仕様
ハロゲンヒータには、各部の温度の制約がある(図3.14)。
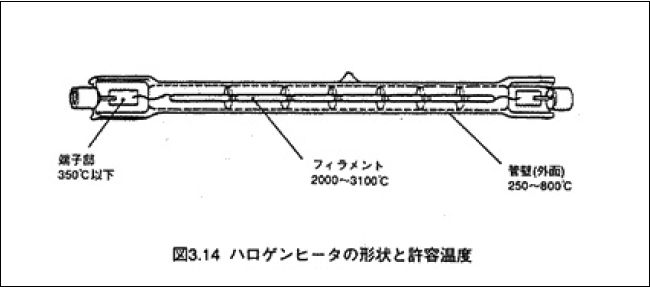
- ・封止部温度350°C以下
- ・発光管表面温度250°C〜800°C
最低限これらを考慮した上で仕様を決定しなければならない。
出力(電力)設定には、加熱する液体の上昇温度および必要時間により設定する。通常このような用途の場合は、1000W〜4000W程度(1本あたり)である。
波長(色温度)設定には、前述のとおり約1.3 以上の熱放射をできる限り多くする必要があり、付近にハロゲンヒータのピーク波長がくるような設計を行う。設計はヒー夕の色温度で行ったため、ウィーンの変位則により設定する。だと2230Kになるが、ハロゲンヒータの製作上の問題も考慮すると 2200K〜2600Kが良いと考える。
なお、ハロゲンヒータの寿命も色温度に左右されるが、2200K〜2600Kならば、5000Hrs 以上と考える。
また、使用条件も設計に十分反映させなければ早期不具合発生の可能性が高くなる。
封止部温度、発光管表面温度を規格内におさめるための、石英ガラス管の設定、発光部端部から封止部までの距離の設定、加熱能力の変動に対応するための過度の点滅、極端な調光で使用できるような設計を各部(モリブデン箔、フィラメント、封入ガス)に施している。
(松岡智巳)
3.4 半導体製造工程への応用(ウエーハの過熱)
3.4.1 現状
急速に半導体の大容量、高集積化が進む中で、半導体製造設備も技術面、コスト面での対応が要求され、ウエーハ上に施すさまざまなプロセスの新技術は0.5ミクロン以下の精度が求められるまでに至っている。
これまでの主流は一度に大量のウエーハを処理するバッチ方式で、この製造方法では加工処理における精密性、均一性の確保に限りがあり、装置の技術的な改革が必要となっている。そこで、新しいウエーハ処理方法として、枚葉方式がある。枚葉方式は、バッチ方式の欠点を解消するだけでなく、今後予想されるウエーハの大型化にも対応できると考える。
3.4.2 枚葉方式
枚葉方式では一度に処理できるウエーハが 1枚であるため、高精度の処理が可能で均一性も保たれ、精密な条件への対応に優れている。半導体製造のプロセスの中で特にEpi (エピタキシァル)、CVD (化学的気相成長法)、また各種のアニールにハロゲンヒータが使われている。いずれもウエーハ上の温度の均一性が重要で、昇降温時±3°C、安定時±1°C くらいが要求される。製造装置メーカ各社の装置の形状、加熱方法は種々であり、したがってハロゲンヒータの形状も種々である。
3.4.3 ハロゲンヒータの仕様
ハロゲンヒータの形状、仕様も種々であり、またユーザと協同開発であるため、明確にできない内容が多いが概略について説明する。
・サークル状のヒータ
サークル径(アール)の異なる数品種のヒー夕を円周状に配列する。
この場合、サークルの大きさによりヒータの出力を可変させ均一性を確保する。
サークル径はΦ50mm〜Φ250mm程度では出力は1000W〜4000W程度で、寿命は2000Hrs程度と考える。
・シングルエンド型のヒータ(図3.15)
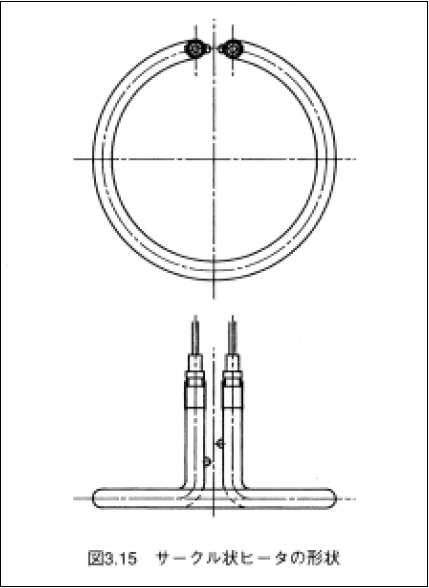
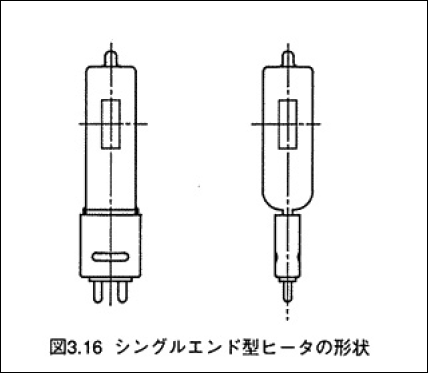
同品種のシングルエンド型ヒータを放射状、円周状に多数配置する。
均一性はヒータ配置の方法、ヒータ出力など、各装置メーカのノウハウによって決まる。出力は500W〜2000W程度で全長70mm〜 150mm程度で、寿命は2000Hrs程度と考えられる。
これらの用途の場合も液体加熱の時と同様で使用条件を設計に十分反映させ、ハロゲンヒータの各部温度の制約を考慮した設計を行っている。
(松岡智己)
3.5 暖房への応用
3.5.1 赤外放射と温熱感
光放射が人体に照射され吸収されると、生化学反応を生じない部分はそのまま熱エネルギーに変換される。この変換された熱エネルギーはその周辺の組織の温度を上昇させることとなるが、人体の組織の温度が適温に上昇したときに得られる感覚を温熱感といい暖房などの条件設定の場合の基準とされる。
光放射の中で、波長の長い赤外放射は、光量子のエネルギーが低いため、人体に吸収されても生化学反応はほとんど生じない(人体だけでなく、一般の物質に対しても、光化学反応を生じることなく、熱エネルギーに変換され、その物質の温度を上昇させるので赤外線は加熱用として利用される)。
温熱感は、感覚としても重要であるが機能的にも組織の温度を上昇させることによって、体内の血液の循環や新陳代謝の促進を行うので、人体の健康の保持増進をする効果がある。図3.17に人間の皮膚の分光反射特性の測定例を示す5)。赤外放射の中でも、波長2µm以上の長波長域で吸収効率が高いことがわかる。また、この長波長の赤外放射により、温熱感を生じ始める放射照度は、ほぼ20〜30 W/m2とされている。
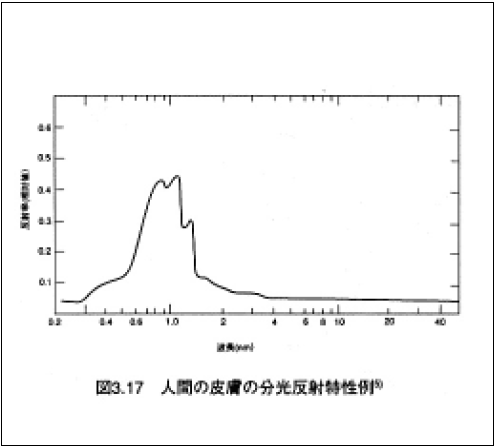
3.5.2 暖房用ハロゲン電球 (商品名ウォーミングライト)
上記の項目で述べたように波長2µm以上の波長が人体にはもっとも良い波長ということがわかる。ハロゲン電球で2µm以上の波長を出すには、主としてブラックコーティングを施す方法を利用する。
シングルエンド型ハロゲン電球(110V、 150W)の表面に特殊セラミックコートを施すことで可視光出力のほぼ100%、近赤外線(0.7 〜3.0µm)の70〜80%を遠赤外線(3.0〜100µm) に変換して放射させる。また遠赤外線を効率
よく制御するためゴールドミラーを採用している。さらに視覚での暖かさを持たせるためにある程度の可視光を照射できるような構造にしている(図3.18参照)。
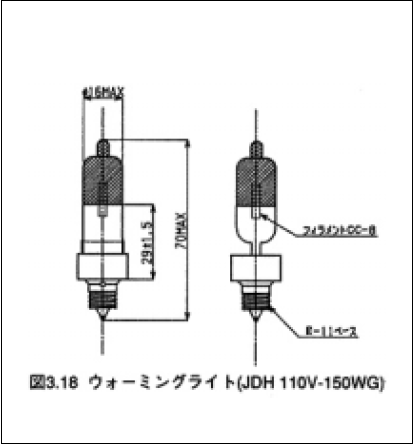
現在、ホテルのシャワールームや化粧室、タクシ乗り場、病院の診療室や病室、プールサイドなどに使われ、熱を嫌うコンピュータ室などでは室温を高めず人だけ温かくすることもできる。また、人体に限らず宴会場の料理も上から温かいまま保温もできる。なお、ウォーミングライトでは1000W程度の大型電球まで設計・製作することができる。
(松岡智己)
3.6 調理への応用
3.6.1 調理用熱源
調理用熱源としては薪・炭に始まり現在一般的にはガス・電気が広く使用されている。従来の熱源は対流および伝導を使用したものが主である。それに加え、近年放射加熱に対する注目が高まり、ハロゲンヒータを応用した調理器が普及してきた。
3.6.2 調理用としてのハロゲンヒータの有効性
- ① 熱源であるフィラメントがバルブ(石英ガラス管)内にあるため使用時一酸化炭素などの放出がなく、人体に無害である。
- ② 炎を使用していないため引火などの恐れがなく安全である。そのため、ガスが使用できない高層ビルなどでも使用可能。
- ③ 業務用の場合、厨房内の温度が上がりにくいため作業環境が良く、加えて、空調費用などの節約による省エネ効果がある。
- ④ 電圧を変えることにより、放射熱量を容易にコントロールでき、強火〜トロ火の調整が簡単である。
- ⑤ 電気を使用した他の調理用熱源と比較し、発熱量の立ち上がり、立ち下がりが早いため調理時間の短縮、熱量の微妙な調整や制御が可能である(図3.19、表3.4)。
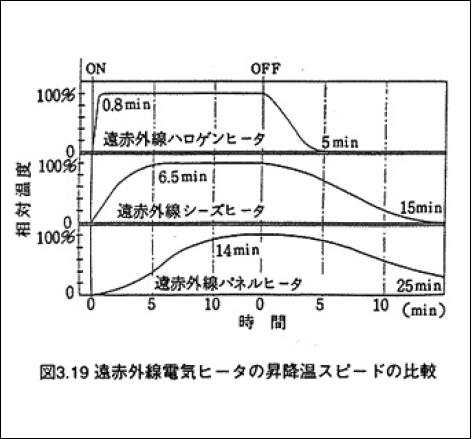
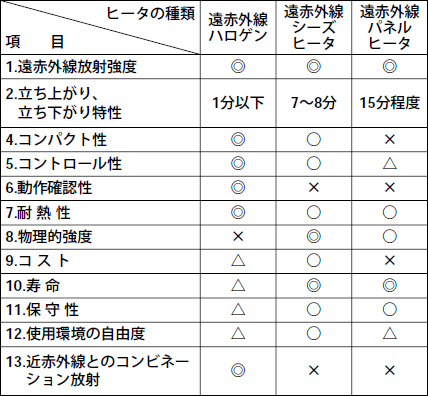
表3.4遠赤外線ヒータの性能比較
3.6.3 応用例
(1)調理用ハロゲンヒータ
① 近赤外線ハロゲンヒータ(クリアタイプ) (図3.20)
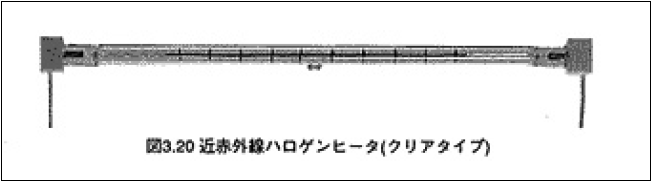
1〜15µmに分光ピークを持つハロゲンヒータ。調理全般に使用されている。
② 近赤外線ハロゲンヒータ(赤色石英タイプ) (図3.21)
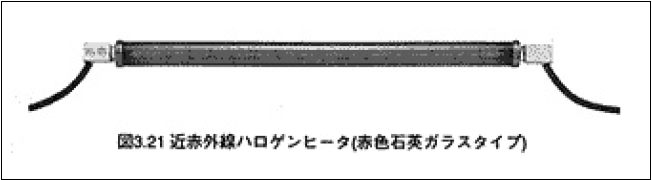
バルブに赤色石英ガラスを使用したハロゲンヒータ。
使用時の眩しさの緩和・暖かさを視覚的に訴える。
食品保温など消費者の目に触れる場面に使用されている。
③ 遠赤外線ハロゲンヒータ(ブラックコーティングタイプ)(図3.22)
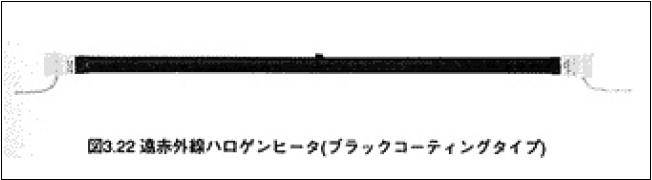
2〜4µmに分光ピークを持つハロゲンヒータ。
バルブ(石英ガラス管)に高効率放射セラミックスをコーティングしフィラメントから放射される可視光および近赤外線を遠赤外線に変換している(図3.23、図3.24)。炭焼きのような効果が必要な調理器の熱源として使用される。
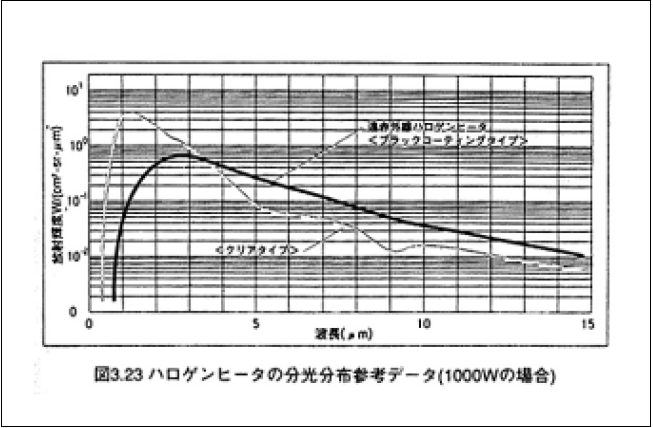
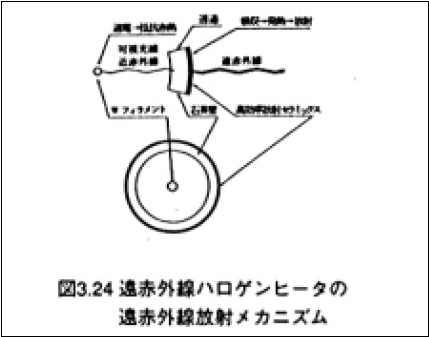
④ 反射膜付きハロゲンヒータ(半面ホワイトコーティングタイプ)(図3.25)
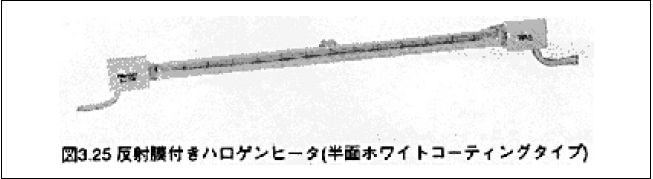
バルブの半面にホワイトコーティングすることにより、一方向への放射効率を向上させたもの(図3.26)。
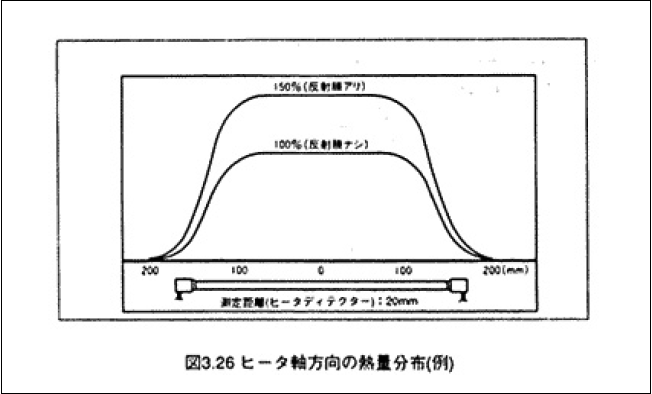
調理するものへの放射熱量向上とともに、調理機器への放射熱量の低減が必要な場合に使用されている。
⑤ 二重管ハロゲンヒータ(図3.27)
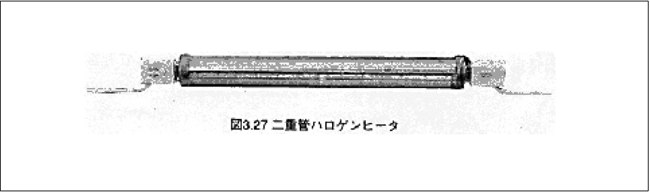
①のハロゲンヒータの外側にさらに石英ガラス管を付け二重にしたハロゲンヒータ。調味料などがヒータに直接かかるような場合に使用している。バルブを二重にすることによりバルブの耐久性を向上させ、より信頼性を向上させている。
(2)応用製品
① ハロゲンコンロ
図3.28のようにハロゲンヒータと温調機 (Temperature limiter)を組み合わせ、ヒー夕の点滅点灯を制御することにより温度を設定値に保つ。
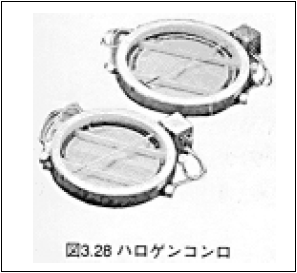
通常上面に耐熱ガラスなどが取り付けられている。
② 食品保温装置
図3.29の装置の下に食品を置き、食品を所定の温度に保つ。
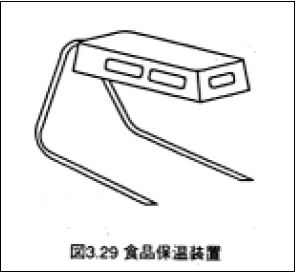
③ 電気調理機
図3.30のような装置に食品を置き、上方からハロゲンヒータで加熱する。
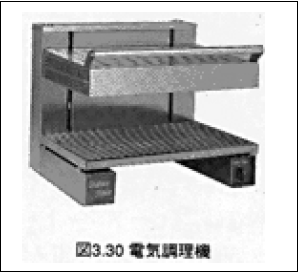
(河村忠和)
3.7 宇宙実験への応用
3.7.1 現状
宇宙空間は微少重力、広大な高真空、豊富な太陽エネルギーといった地上では得られない環境特性を有している。この宇宙環境を活用して、均一な超伝導合金や半導体の大型単結晶を熱エネルギーで創製するという世界的なプロジェクトに当社は10数年前より参画している。
NASDA (宇宙開発事業団)のFMPT (第一次材料実験)で光炉(イメージ炉)の熱エネルギ一源としてスペースシャトルに搭載されるなど、数多くのハロゲンヒータを宇宙で点灯させてきた。光炉(イメージ炉)は楕円ミラーを使用して光エネルギーを集光させ試料を加熱する炉である。ハロゲンランプに求められる性能としては、打ち上げ時の過酷な耐振、耐衝撃性、高真空、無重力空間における安定性、フィフメント精度および長寿命など通常商品をはるかに凌ぐ緻密な設計を施し、高い精度の製作を行っている。
現在は、スペースシャトルに搭載されたヒ一夕(500W程度)から宇宙ステーション(JEM)で使用される高出力(1500W程度)のハロゲンヒータを開発中である。なお、加熱性能は 1400°C〜2000°C程度である。
3.7.2 ハロゲンヒータの仕様
宇宙実験で使用される場合、もっとも重要視して設計しているのは、高真空中での使用による各部の温度上昇である。特に管壁温度 (発光管表面温度)は温度が900°Cを超えると短寿命となる可能性が非常に高い。図3.31からわかるように、大気中では高い管壁負荷 (高出カタイプ)まで使用できるが、真空中では極度に管壁負荷の上限が下がってしまう。高出カタイプの開発にあたっては、留意すべき点である。3.31を参考にしバルブ直径を選択し、管壁温度を下げ適正値を見つける。フィラメントの構造は、CC-8タイプで打ち上げ時の振動、衝撃に耐えられるように電圧、電力、色温度を調整し耐振、耐衝撃性を向上させている。
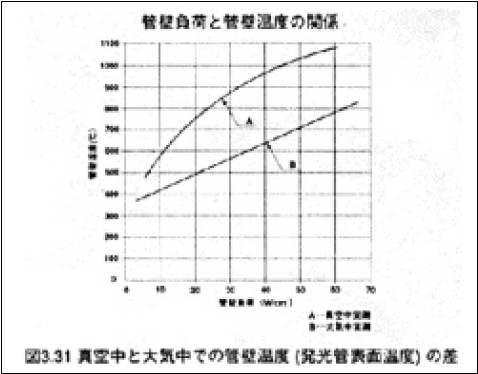
フィラメントの大きさも試料を目標温度まで加熱する上での重要なポイントとなる。また、精度はフィラメント径、長さとも土 0.25mm以内である。
3.7.3 光源の他への展開
集光性がよく、かつ比較的大電力のランプであるという特長を活かし、地上での光による非接触加熱炉にも使用されている。帯域溶解用、単結晶引き上げ用の炉に広く使用されている。
(松岡智己)
3.8 光ビームはんだ付け-キセノンショートアークランプの応用
3.8.1 はんだ付けの現状と市場の要求
近年、電子機器の小型化、薄型化、高機能化に伴い、電子部品のプリント基板への実装は高密度化している。
また、電子部品そのものも半導体における集積度の増大と高機能化によりリード数が増加し、リードピッチの狭小化がますます進んでおり、デイッピングによるはんだ付けでは対応が困難となっている。
表面実装の分野ではペーストはんだによる印刷法が導入され効率化が進んでいるが局部的なはんだ付けや空中結線の場合は依然としてはんだごてによる方法が主流となっている。しかし、はんだごてによる方法は、
- ① はんだの残渣やこて自体の変形によるろう接部の不均一性
- ② はんだ付け時間の短縮化の要求
- ③ インライン化による人件費削減の要求
により最先端の実装技術に対応しきれなくなりつつある。
また、ピックアップレンズ、水晶振動子などの実装においてははんだごての接触に伴う位置ずれを避けるために非接触でのはんだ付けが必要となってきた。
実際に、非接触ではんだ付けを行う方法として
- ① 光エネルギーを利用したはんだ付け(光ビ—ムはんだ付け)
- ② 温風を利用したはんだ付け
- ③ その他
がある。
いずれの場合も良好なはんだ付けを行うためには、被はんだ付け部およびはんだを溶かすための加熱方法の最適化が不可欠である。
この加熱方法の最適化に対して、光ビームはんだ付けにおいては光エネルギーを照射時間および強度で制御し対応することが可能である。
3.8.2 現状の光ビームはんだ付け用光源
現在、光ビームはんだ付け用として数種の光源が使用されている。これらについて感単にまとめる。
(1)ハロゲンランプ
ハロゲンランプはフィラメントへ通電加熱することにより光エネルギーを得ている。しかし、フィラメントの長さにより発光部の長さが決まってしまうため、点光源として使用することができない。このため、集光ミラーを使用した際、集光径を小さくすることが困難という短所がある。
(2)CO2レーザおよびYAGレーザ
CO2レーザおよびY AGレーザは高エネルギ一が得られ、急速加熱でき集光径を極めて小さくできるという長所がある。また、はんだ付け条件を電気的、光学的に調整できるという特徴もある。しかし装置が非常に高価であるために用途は限定されている。
(3)レーザダイオード
最近、高出力のレーザダイオードも、光ビームはんだ付け用の光源として使用されだした。
(4)キセノンショートアークランプ
キセノンショートアークランプは発光部が小さくかつ陰極輝点の輝度が高い。したがって、狭い範囲内にミラーで効率よく集光することが可能である。
キセノンショートアークランプを使用した光ビームはんだ付け装置は出荷台数が増加してきているが、さらに普及させるにはコンパクトでかつ安価な装置とする必要がある。
3.8.3 キセノンショートアークランプの使用例および今後の課題
現在日本国内における製造業のはんだごて使用数量は約35万本といわれている。このうち、電子部品のはんだ付け、プリント基板のリペアでの使用をターゲットとして85Wキセノンショートアークランプを光源として使用した光ビームはんだ付け装置を開発した。この装置の外観を図3.32に示す。
また、この装置の特徴を簡単に紹介しておく(図3.33)。
■特徴
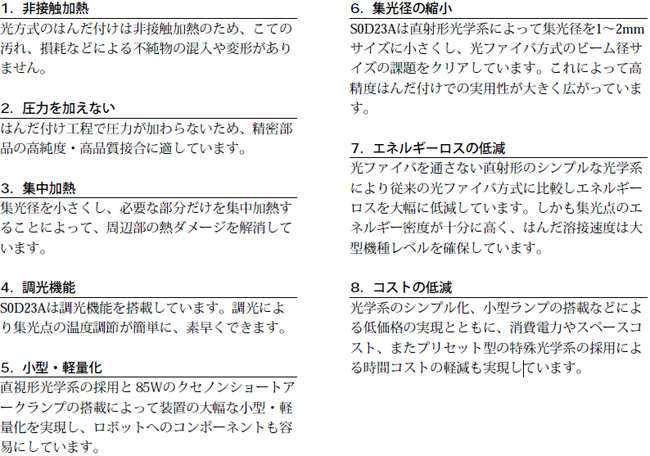
■外観図 S0D23A
ヘッド部
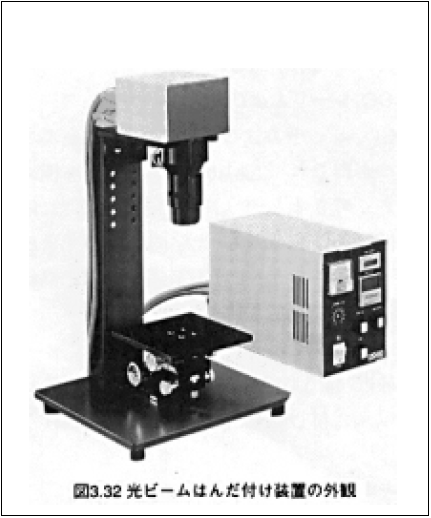
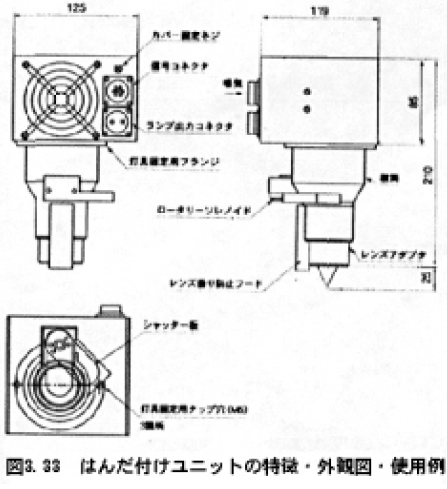
■仕様
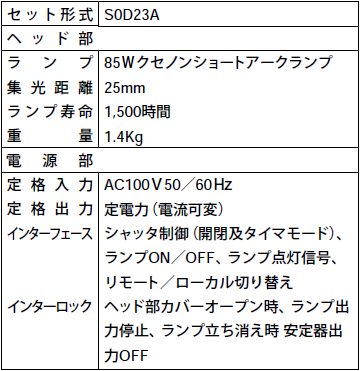
(1)ランプの特徴
- ① 一般に、キセノンショートアークランプは点灯に伴い陰極が摩耗し、陰極輝点輝度の低下および極間ののびが発生する。楕円ミラーにて集光する際、これらの現象はいずれも集光部でのエネルギー減衰の原因となる。そこで、陰極には摩耗の非常に少ない特殊モールド型陰極を採用した。
- ② 楕円ミラーにて集光する場合、ミラーの第一焦点を陰極輝点に合わす必要がある。この調整作業を省略するために、ランプ取付け基準部分と陰極先端の位置精度を向上した「高精度型ランプ」とした。
(2)装置の特徴
- ① 光ファイバを使用するとファイバ内でのエネルギー伝達ロスが生じる。そこで光ファイバを使用せず直射加熱方式とすることでエネルギー利用効率を高めた。
- ② ランプ電流の可変により、ワークに応じた温度コントロールを可能にした。
- ③ シャッタ機能を装備し加熱時間の制御を可能とし、ワークへの長時間の加熱を防止した。
参考までに本装置使用時の集光点の温度分布および集光点での温度立ち上がり特性を図3.34、図3.35に示す。
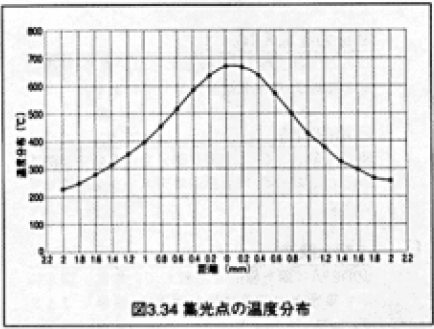
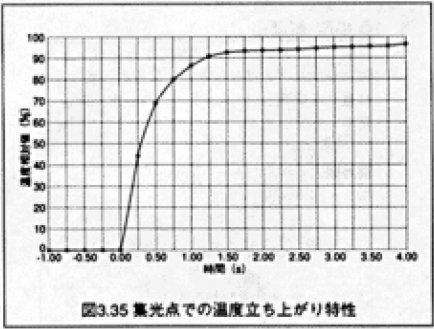
集光点での温度分布は半値幅として約2.5 mmであり、またピーク温度の90%に達するまでの時間は1.2である。
実際にΦ1糸はんだを使用した場合、2秒以内にはんだ付けを完了させることができる。
(3)今後の課題
冒頭にも述べたようにリードピッチの狭小化に伴い局部加熱の要求はますます増加してきている。このためより集光径の小さい装置が望まれている。
現在半値幅として約2.5mmである集光径を全エネルギーは維持したまま1mm程度まで小さくすることができれば用途をさらに広げることが可能である。
(4)まとめ
はんだ付けはさまざまな用途で使用されているが最先端の実装には対応しきれなくなりつつある。
キセノンショートアークランプを光源として光ビームはんだ付けを利用することにより、非接触、局部加熱という要求に対応することが可能である。
しかし、さらに光ビームはんだ付けが普及するためには、より小さな集光径を持ちコンパクトで安価な装置が必要であり、当社としてもそれに取り組んでいる。
光エネルギーの密度を向上させ、金属加工用の実用熱源として、光ビームを用いる加工方法の特長としは、次のような諸点が挙げられる7)。
- ① 被加工物に対して非接触加工である。
- ② 電場、磁場の影響は全くといってよいほど受けない。
- ③ 所望する雰囲気の中で純度の高い熱加工ができる。
これらの特長が各方面によって再認識され、本稿で取り上げたはんだ付けのみならず、溶接、ろう付け、金属の熱処理、非鉄金属を含む溶接加工など、エレクトロニクスや医療器具など些細な汚れ、粉塵を極度に嫌う部品や微小な素材を加工する分野において活用されるようになっている。
光ビーム加工といえば、CO2レーザやYAG レーザの応用がまず思い浮かぶが、ハロゲンランプやキセノンランプを応用したコンパク卜で安価な装置が今後その用途を広げると考えられる。
(安達和浩)
3.9 フラッシュ定着-キセノンフラッシュランプの応用-
3.9.1 フラッシュ定着法
(1)歴史的背景
情報化時代の到来で、情報の入出力技術の発達には目を見張るものがある。その中で情報の出力技術の代表にトナー定着法がある。紙の上に形成されたトナー像をヒートロールで加熱押しつけて行うものであり、最近普及の著しい産業用レーザプリンタのほとんどがこれである。
一方、瞬間的に強い光を照射しトナーを溶融させて定着する技術が約20年前8,9)に登場した。実用化に向けた研究の後、フラッシュ定着方式が大型計算機の高速プリンタに採用されてからはや15年近く経過した。当初、2000 行/分でスタートした印刷速度が、現在では高速化が進み15000行/分を超えるものが登場している。
フラッシュ定着法の使用は、依然大型計算機の出力装置に限られ、他分野への普及は進んでいないが、これはランプ点灯に専用の充放電用電源が必要なことから、ヒートロール方式に比し大型でコスト高なことである。しかし、最近の大電力の電源にもスイッチング方式が採用されるようになり電源の小型軽量化が進んできている。
(2)フラッシュ定着の原理
通常、定着といえば、トナーを熱で溶かし圧力を加えて紙に定着させることをいう。一方フラッシュ方式は、フラッシュ時の光エネルギーをトナーが熱吸又し瞬間的にトナーが溶融し定着する。光を使用し非接触で定着することから光定着とも呼ばれる。フラッシュ定着を用いた電子写真プリンタの概念図をヒートロール方式と対比させて図3.36、図3.37に示す10)。
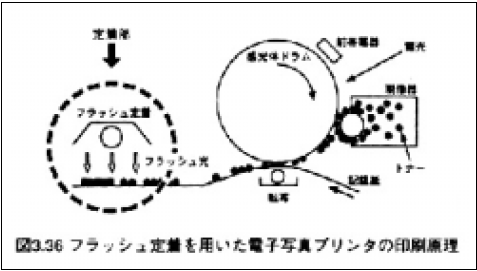
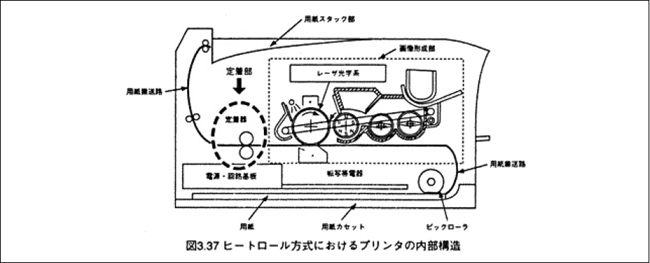
3.9.2 フラッシュ定着方式の特徴
(1)フラッシュ方式とヒートロール方式の比較
ヒートロール方式において、連続紙に高速で定着する際に起こった最初の問題は、紙が熱で反り紙の折りたたみが困難なことであった。また、大容量のヒータから発生する熱が装置内に籠もり加熱することであった。
フラッシュ方式の特徴は、フラッシュ光の吸収がトナーに限られ、用紙自体ほとんど光を吸収しないため、装置の加熱もなく定着熱による紙のダメージが少なくて済む点にある。トナーおよび用紙での光吸収率のカーブを図3.3811)に、フラッシュランプの発生スペクトルと合わせて示す。トナーの光吸収率は 90%以上であり、かつ波長依存性が無いので全波長の光はすべてトナーの加熱に使われる。一方、紙の吸収率は30%前後と小さく光のほとんどは反射するので紙は不要に加熱されない。
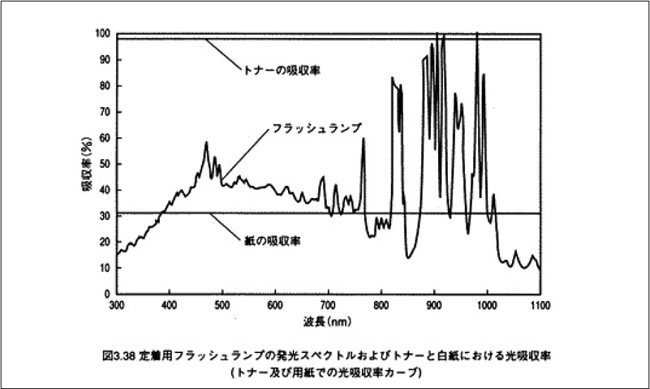
定着装置側から見たフラッシュ定着の特徴を下にまとめると4つになる。
- ① 非接触法であるので、記録媒体の種類と厚さを選ばない。
- ② 定着機の保守がフラッシュランプのみの交換で済むため保守が容易。
- ③ 瞬時点灯瞬時安定であるので、予熱や装置起動時の待ち時間が必要としない。
- ④ たとえ紙詰まりしても発火の可能性がない。
さらに、最近の技術動向を入れ、ヒートロール方式と比較したフラッシュ方式の特徴を表3.5にまとめる。
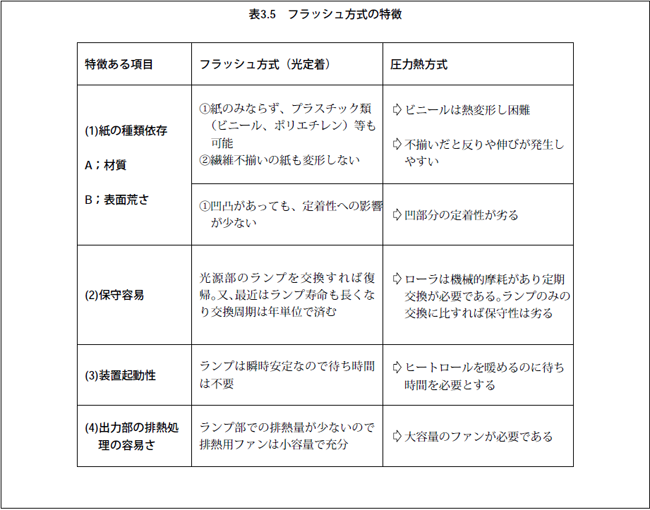
(2)使用条件例
ランプ1灯の使用例と、複数のランプで点灯周期も増し印字速度を6倍に高めた場合の2 例を表3.6に示す。
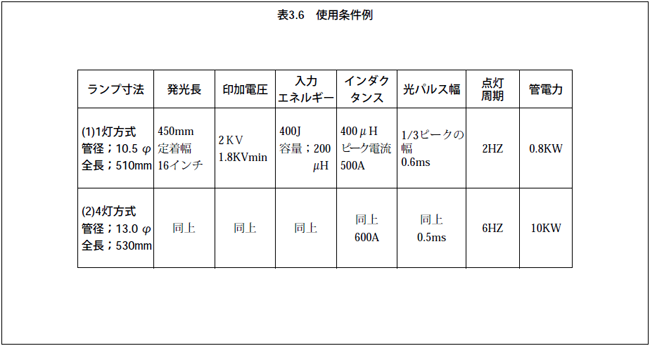
(斉藤滋)
3.9.3 点灯装置
フラッシュランプ用点灯装置(以下FL点灯装置と略)は主コンデンサの充電装置であり、一定の周期内に所定の電圧にコンデンサを充電し、ランプ発光により瞬時にコンデンサが放電した後、再度充電を繰り返す動作を行う。
現在放電ランプ点灯装置は一般のDC定電圧電源と同様に、商用周波数で動作する大型で重いトランスを使用する銅鉄型から、パルス巾変調(以下PWMと略)のスイッチング方式に切り替わっているものが多い。一方FL点灯装置は、Xeランプなど連続光を発生するランプ用点灯装置と回路動作が異なる部分が多く、この部分の技術対応が困難なためスイッチング化が大幅に遅れた事情がある。
FL点灯装置特有のコンデンサ充放電による出力電圧変動が非常に大きいこと(充電完了時と放電直後では10倍以上の差がある)に対応するため、トランスの一時側にインダクタンスを接続したスイッチング方式点灯装置が開発された。しかしこの方式はPWM技術がベースでありスイッチング動作時、インダクタンスに蓄積されたエネルギーが入力側に回生され効率が悪く、ノイズも大きいものであった。
しかし数年前より共振型スイッチング電源技術が開発され、当社においても共振型FL 点灯装置の開発に成功し、'95年の主力新製品より共振型スイッチング方式に完全に切り替わっている。
(1)共振型FL点灯装置に代わって改良された主な項目
① 小型、軽量化
PWM方式のDC定電圧電源も同様であるがスイッチング化により動作周波数が商用周波数に比し3桁程度高いため、銅鉄型で必要な大型トランスが不要となり大幅な小型、軽量化が可能となった。
一例をあげると3000行/分の印刷速度のプリンタ用FL点灯装置の場合銅鉄型点灯装置に比し、重量で1/4程度に、体積で1/2程度である。
② 高効率化、低ノイズ化
従来のPWMベースのスイッチング点灯装置の効率は70〜75%程度であるが、共振型FL 点灯装置の場合、入力側へのエネルギー回生が無いこと、主スイッチ素子の電流波形が矩型波ではなく正弦波であることによるスイッチング損の低下により、効率が85〜90%に改善されている。電流波形が正弦波であることにより電流ゼロでスイッチング動作を行うため、ノイズの発生が大幅に低下している。
③ 制御回路の高精度化
FL点灯装置は組み込む機器により決まる発光周期内にコンデンサを設定電圧まで充電する必要がある。制御回路には電圧比較器があり、コンデンサ電圧を分圧した検出電圧が設定基準電圧に達した後は充電動作を停止するように制御している。入力電圧変動を考慮すると、充電能力が一番低下する入力電圧下限値においても発光周期内にある程度の時間的余裕を持って充電動作が完了するように充電能力が決定される。
従来型点灯装置の場合、逆に入力電圧が上限値になると充電が非常に早く完了し、発光周期の1/2程度の時間で充電動作を完了し残り1/2の時間は動作を停止していた。このような動作では、平均出力電力が1KWの場合でも充電動作時には2KW程度の出力が要求され、動作にムラ、ムリが多くピーク電力に対応するため大型、高価な点灯装置になっていた。
当社の共振型FL点灯装置は制御回路内部で理想的な出力電圧上昇曲線に対応した充電基準電圧を生成し、出力検出電圧とこの基準電圧を誤差アンプで比較しフィードバック制御を行っている。このため、動作にムラ、ムリが少なく入力電圧が変動しても必要以上に早く充電することなく、常に発光周期の95%程度の時間で充電動作を完了し、かつ動作中は出力電力がほぼ一定になるように制御される。
(2)今後の課題
① 高調波規制対応
スイッチング電源は入力AC電圧をコンデンサ入力型整流回路で整流するため、入力電流が正弦波から大きく歪み、入力周波数の整数倍の大きな高調波ノイズが発生する。この高調波ノイズを規制する法律が近く発効し、 FL点灯装置も規制の対象となる。実際には自主規制により、対応が進んでいるが、FL点灯装置の場合対応するためには、入力電流を強制的に正弦波に制御するスイッチング電源の一種であるアクティブフィルタを入力に追加する必要がある。現在のアクティブフィルタはPWM方式であり、ノイズ発生も多く損失も10%程度増加するため、共振型のメリットである低ノイズ、高効率の特性が損なわれ、また点灯装置が大型、高価になる。
今後、アクティブフィルタにも共振型スイッチング技術を応用し、低ノイズ、高効率なアクティブフィルタの開発を進める予定である。
② 低コスト化
共振型FL点灯装置の開発により、従来の銅鉄型点灯装置に比し20〜30%程度の原価低減が可能になったと思われる。しかしヒートロール方式などの競合する他方式に比し、灯具などを含めた総合コストはまだ非常に高くコスト優先の用途では使用される可能性は低いと言わざるを得ない。FL点灯装置の新規用途への採用の可能性を高めておく必要があり、主要部品の見直し、再開発、回路の標準化とハイブリッドIC化などによりさらに原価低減を進める予定である。
3.9.4 灯具
(1)構造
灯具は通常、フラッシュランプ、反射用ミラー、およびトナーの飛び散りによる汚れ防止用ガラス、およびそれらを保護するケースで構成されている。
また、イグナイタについても、電圧がピーク丨・数kV、周波数が数百kHzの減哀型の高周波のため、中継ケーブルよりの電圧の漏れを防ぎ、発生ノイズを少なくするためにも灯具に内蔵する場合が多い。一般的な構造を図 3.39に示す。
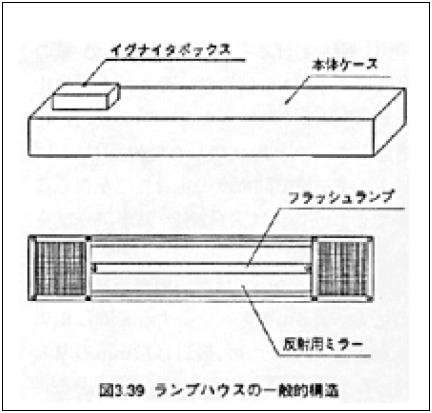
(2)冷却
灯具内はフラッシュランプからキロワットクラスのエネルギーを放散するため、相当発熱する。そのため、灯具内部に風の流れを作り冷却することが必要となる。ランプ回りは反射用ミラー、保護用ガラスに囲まれてダク卜状になっており、冷却には通常静圧の大きい遠心ファン(シロッコファン)が用いられる。冷却温度としては、フラッシュランプの最高温度を200°C程度を目標とする。最近では電極、トリガワイヤの改良などにより300°C程度でも耐えるランプも登場している。
またケースの温度も安全規格からの要求もあり、機器内部で人の触れるところの金属の温度を70°C以下にしなければならない。
(3)最近の傾向
ランプ入カエネルギーに対する効率を上げるには、反射用ミラーの反射率を上げる方法もあるが、これは期待するほど効果が上がらない。そこで、最近は定着面へのエネルギーをより均一化させるミラー形状を検討することにより、必要エネルギー量を下げる方法が採られている。
その一例をあげると、定着幅が同じで、紙の送りスピードが1.2倍になったものを製品化したが、定着面でのエネルギーのより均一化を考慮したミラー形状にした結果、旧品と同じエネルギー量で同程度の定着性能を得ることができた。これは実質2割の効率アップをしたことになる。
ケース本体については薄い板金で対応したものもあったが、フラッシュする瞬間に相当の振動音を発するため、最近は数mmの厚みを持ったアルミ材が使用される傾向にある。
(横田英樹,中山峰男)
3.10 イメージ炉への応用
3.10.1 イメージ炉(まえがき)
熱源にランプを使用して、楕円ミラーやレンズの光学系を組み合わせ、その集光した光エネルギーで試料を加熱する炉をイメージ炉と呼んでいる。最近では、熱源に炭酸ガスレーザを使用して、直径約1mmの原料棒を融点 2700°C付近まで加熱を行い、引き上げ機構による帯域溶解法でマイクロ単結晶の生成が行われている12)。
そもそも、アークイメージ炉を使用した高温研究の歴史は古く、1960年代の始めにアメリカのADL(アーサ・ディ・リトル)社がキセノンランプ2KWのアークイメージ炉を完成させている。この時期は全米でイメージ炉の開発と利用が盛んになり、その研究の様子が 1904年にThermal Imaging Techniquesという図書にまとめられた。この図書には全米の高温研究者の方々が工夫されたさまざまのイメージ炉が紹介されている。この当時のイメージ炉の熱源はカーボンアーク、プラズマアークが多く利用されたが、それらのアークは不安定だったので、キセノンランプに移行していった様子がうかがえる13)。
1960年の後半から1970年にかけて、日本でもアークイメージ炉による高温研究が開始された。その熱源は欧米のキセノンランプ化が反映されて、はじめからキセノンランプが利用された。この導入期にあたり、ウシオ電機 (株)はNTTやシャープ(株)殿にキセノンランプ 5KWおよび6.5KWのアークイメージ炉を納入している。
1970年の前半には、ウシオ電機(株)はアークイメージ炉用に30KWキセノンランプを開発して、ウシオ電機(株)の横浜事業所に実験用30KWアークイメージ炉を設置し、イメージ炉の集光特性について研究され、その研究発表はその後のイメージ炉の基礎を築いた14,15)。
ハロゲンランプを使用したイメージ炉は日本電気中研で1970年に開発されたもので、単結晶引き上げ装置がつき、コンパクトな楕円ミラーによるイメージ炉であった。このハロゲンイメージ炉は単結晶の研究に多大の貢献をもたらした。フィラメントコイルを熱源としたイメージ炉はアークを熱源としたイメージ炉のように加熱の揺らぎがなかったからである。このハロゲンイメージ炉は直径5mmのフェライト棒の単結晶が生成されることがわかり、それ以来、多数の単結晶研究者により多くの利用がされている 16)。
やがて、ハロゲンイメージ炉は宇宙開発事業団の計画したスペースシャトル内での宇宙空間の溶融実験に使用された。
キセノンランプを利用したキセノンイメージ炉は1970年の前半にフランスでキセノンランプ6.5KWを使用したイメージ炉が開発されて、高融点材料の溶融実験が行われた17)。
日本でも、1970年の後半から東京工業大学において、ウシオ電機(株)のキセノン10KWイメージ炉を使用した高融点材料の研究が行われた18,19)。
同じ1970年後半、東京大学ではキセノンランプ5KWによるイメージ炉で高温での帯域溶融法の単結晶育成の研究が行われた 20)。
旧ソ連では、1980年前半において、キセノンランプ10KWを使用したイメージ炉で高温高圧での溶融実験が行われた21)。
1980年前半までは、キセノンアークイメージ炉の応用は単結晶の育成に努力が払われたが、アークの揺らぎがこの進展を妨げていた。しかし、1980年後半になって、キセノンアークイメージ炉は高温における材料評価のための装置(以下、高温評価装置と略す)として応用するアイディアが生まれた。東北大学や航空宇宙技術研究所が開発したキセノン30KW イメージ炉は高温度落差評価試験機として、傾斜機能材料の試験に応用された22)。
さらに、この高温評価装置の応用は1990年前半において、(株)超高温材料研究センターで企画され、キセノン30KWイメージ炉がウシオ電機(株)から2台納入された。カーボン/カーボン複合材料の熱サイクル/熱衝撃試験機と酸化/揮散試験機としてそれぞれ応用されている23,24)。
3.10.2 単結晶引き上げ炉としての応用
単結晶引き上げ炉の熱源に、ハロゲンランプが使用された結果が日本の単結晶研究を加速できた。ハロゲンイメージ炉は試料を加熱するときに、加熱温度の揺らぎがなく帯域溶融ができたからである。
3.10.3 温評価装置としての応用
イメージ炉を計画する場合、試料の加熱温度、その加熱面積、温度分布をどの程度にするか、とくに、高温評価装置の場合は試料の加熱上昇温度、冷却速度はどれくらいか、その必要度によって熱源が異なる。例えば、直径1mm以下の線材試料を2000°Cに加熱するには、レーザイメージ炉となるだろう。直径 5mm以上の試料を2000°Cに加熱するには、キセノンランプを使用したキセノンイメージ炉となる。ハロゲンランプを使用したハロゲンイメージ炉は1800°Cまでの加熱となる。
高温評価装置として、イメージ炉を使用する最大の利点は試料の急速加熱/急速冷却が行えることである。抵抗体を使用した雰囲気炉と決定的に異なるのが、この急速加熱/急速冷却の時間である。イメージ炉では数分間(1分とか5分)、雰囲気炉は数10分(30分か50分)と1桁異なるのが一般的である。
イメージ炉はその光学系の特徴から、片方に熱源があり楕円ミラーによって離れた位置に集光されるため、熱源がもつ固有の制限条件にしばられることがないので、イメージ炉においては、試料の回りの雰囲気が真空から大気圧まで自由に選べる。通常、試料回りは雰囲気制御のために、透明石英ガラスのパイプやドームを使用して試料の回りが囲われる。
イメージ炉は単純な光学系で、単楕円ミラ一方式の場合はランプと楕円ミラーがそれぞれ1台から構成される。双楕円ミラー方式ではランプが1台と楕円ミラー2台から構成される。単楕円ミラー方式は第一焦点にランプの輝点をおき、第二焦点は集光位置となる、試料の表面加熱の形態となる、試料の裏面は冷却されることで、試料の急速加熱/急速冷却状態での評価に適している。
双楕円ミラー方式は片方の楕円ミラーの第一焦点にランプの輝点をおき、他方の楕円ミラーの第一焦点にランプの輝点の像を写す形となる、この機転の像の位置に試料がおかれる、それぞれの楕円ミラーの第二焦点は共有点である。高融点材料の融解や放射温度の測定に適している。
3.10.4 ランプイメージ炉の特性
ランプイメージ炉は抵抗加熱による雰囲気炉やレーザ炉、高周波加熱炉と比較してかなり特徴がある。
(1)急速加熱/急速冷却
ランプイメージ炉は物体のみ集光するために、熱容量が小さく、その加熱は急速である。一般的には、到達温度2000°Cまで3分間ぐらいである。ランプを消灯すれば、加熱エネルギーは0となり物体のみの放熱で急速に温度がさがる。これは雰囲気炉と比較すると、かなり様子が異なる。ランプイメージ炉は点滅して加熱できるが、雰囲気炉では到底、不可能である。
(2)放射加熱
ハロゲンイメージ炉やキセノンイメージ炉は集光しているだけで、基本的には雰囲気炉と同じような黒体放射加熱である。イメージ炉は色温度2900Kとか5800Kの連続した波長による放射加熱である。
それに対して、レーザ加熱は特定の波長による単色光加熱である。また、高周波加熱は高い周波数による電磁波加熱である。
(3)スループット
半導体の生産用熱処理炉として、ハロゲンランプを熱源としたランプアニール炉がある。単位時間当たり何枚のウエーハの熱処理ができるか、この処理能力はスループットと呼ばれている。研究用の炉にイメージ炉を使用して試料を加熱し、測定はコンピュータによる計測を行えば、研究の現場にスループッ卜の概念を持ち込める。たとえば、成分の異なった試料を数多く用意して、いろいろの温度条件で試験を行う場合、イメージ炉ならばスループットが多くとれる。イメージ炉は試験の回数をあげたり、試験時間を短縮できたり、研究の効率アップが実現できる。
(4)雰囲気/試料台
イメージ炉においては、試料回りの雰囲気の制約がない。大気中、加圧ガス中、真空中、いずれの場合でも試料の加熱が可能である。イメージ炉の試料台は、応用にあたり工夫を必要とする。試料の加熱は断続加熱か、急熱/急冷か、融解か、その加熱の目的によって試料台の形態を選び、それから試料台の材料を考える。たとえば、断熱加熱では試料の裏面まで高温になるので、試料台は熱衝撃に強く、試料との反応がないことが重要である。
(天羽弘)
3.10.5 ユーザ紹介
(株)超高温材料研究センター岐阜センター殿
1991年、キセノンランプ30KWを使用した極超高温酸化/揮散試験機が設置されている。この5年間に数多くの超高温材料の評価試験が、この試験機で行われた。
ここに揚げる写真は(株)超高温材料研究センターの外観と超高温酸化/揮散試験機の外観である。
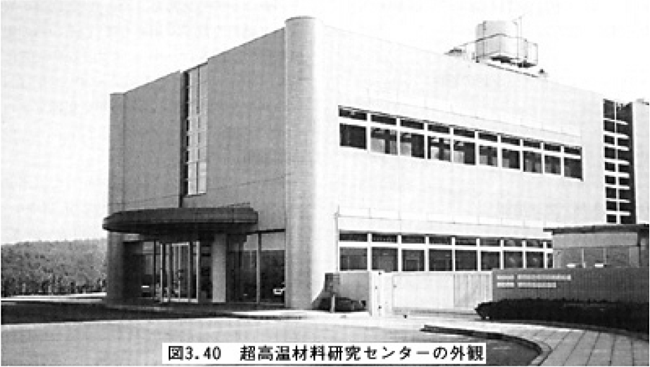
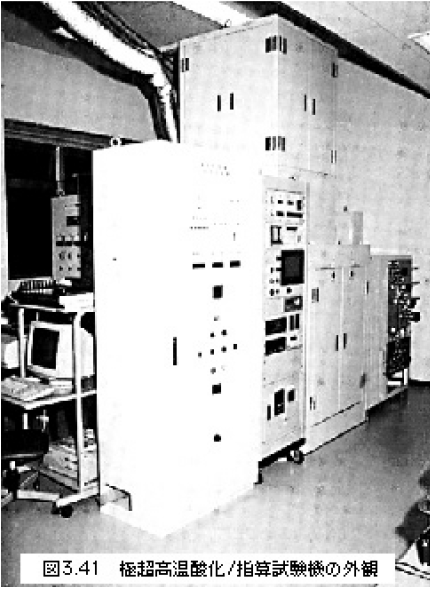
3.10.6 投稿文献
(株)超高温材料研究センターの鎗居俊雄氏らの超高温酸化/揮散試験機への応用に関する報文を再録させていただく。
解説
ランプイメージファーネスによる極超高温酸化/揮散試験機
Ultra-High Temperature Oxidation/Sublimation Testing Machine
伊藤 好二(Kohji Itoh)※ (株)超高温材料研究センター 岐阜センター長
鎗居 俊雄(Toshio Yarii)※ (株)超高温材料研究センター 岐阜センター技術部長
五十嵐龍志(Tatsushi Igarashi)※※ ウシオ電機(株)・次長
守屋 賢策(Kensaku Moriya)※※※ 群馬ウシオ電機(株)副社長
天羽 弘(Hiroshi Amoh)※※※ 群馬ウシオ電機(株)技師
① はじめに
21世紀の航空機や各種エンジンは超高温材料によって推進されることは,ナショナルプロジェクト超高温材料研究センターの竣工1)により,いよいよ現実のものとなってきた。本稿はこの超高温材料研究センター岐阜センター内に設置される超高温酸化/揮散試験機について紹介したい。
次世代の航空機として,構想されているものに東京-ニューヨーク間を約2.5時間でむすぶ極超高音速旅客機と,宇宙基地と地上をむすぶ宇宙往還機とがある。
これは,いずれも極超音速で飛行するため機体先端部分の材料は,2000°C近い超高温の加熱を受けるといわれている。従って,材料は超高温状態での酸化と真空中で,表面からのガス状の材料揮散による劣化を受けることになろう。
この状態を地上で再現するために,ここに極超高温酸化/揮散試験機が企画/開発された。試験サンプルは真空中でのガス分析と重量変化によって評価するために,真空チャンバー内には試料以外の高温揮発成分は置けないため,加熱源は真空窓である石英製ドームの外部からふく射エネルギー,“光”を利用している。この“光”は0.25〜2.5µmにわたり広範囲の発光スペクトルをもち,それは極めて太陽光と近い発光スペクトルをもつクセノンランプ30kWを光学ミラーの集光によって加熱に使用される。このような加熱方法はランプイメージファーネスと称したい。
② ランプイメージファーネス
2.1 ランプイメージファーネスとは
ランプイメージファーネスとは,セラミック材料,金属材料,半導体材料の加熱に際し熱源にハロゲンランプ, クセノンランプ等の高光カランプを使用し,ランプからの光エネルギーを高精度ミラーで構成される光伝送系で加熱物の表面に照射して加熱する装置の総称とする。
ハロゲンランプを使用するものをハロゲンイメージファーネスと呼び,クセノンランプを熱源とするものはクセノンイメージファーネスと区別している。
ランプイメージファーネスは加熱する表面に,5W/mm2〜12W/mm2の高密度の光エネルギーを集光できるので,加熱表面は数秒間で1,000°C〜3,000°Cの加熱を行うことが出来る。この加熱特性によって,高温加熱シミュレーション,高温表面処理,焼成等の熱源として利用されている。
その応用範囲は,宇宙船材料開発分野,ジェットエンジン等の航空分野,電子材料分野のように先端技術分野の加熱に利用されている。
2.2 ランプ加熱の特徴
ランプからの発光は連続した光の波長から成っており,その光の波長域は可視光,近赤外,遠赤外の領域までカバーしている。従って,加熱物の表面の光吸収は材質にあまり影響されずに加熱することが出来る。セラミックスを表面から加熱することが容易に行えるわけである。
ランプイメージファーネスの機能として,
- ① 加熱は上限3,000°Cまで行える。
- ② 加熱速度は速く数秒で加熱することが出来る。
- ③ 加熱速度コントロールは光出力を可変して行える。
- ④ 雰囲気を加熱することなく,目的物のみ集中加熱出来る。
- ⑤ 目的物はセラミック,金属,半導体,物性を問わず加熱出来る。
- ⑥ 照射エリアを特定して加熱出来る。
例えば,表面のみ,裏面のみ,側面のみ,両面から目的に応じて設定出来る。
応用:
- ① セラミックスの焼成
- ② 熱衝撃テスト/シミュレーション
- ③ セラミックスの溶融テスト
- ④ 新素材の温度特性評価
- ⑤ セラミックファイバーの熱処理
- ⑥ 超高温材料の酸化/揮散試験
2.3 ランプイメージファーネスの種類
このファーネスは用いる光学系と加熱方式により以下のように分類される。
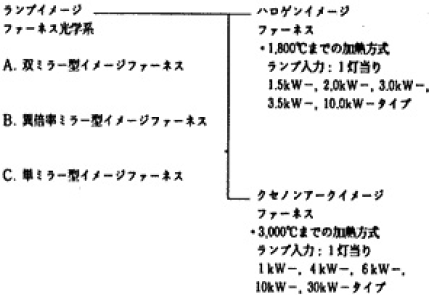
ファーネス:
加熱する試料温度によって,ランプはハロゲンランプを使用する場合とクセノンランプを使用する場合に分けることが出来る。加熱温度が1,800°C以下の場合はハロゲンランプが使え,1,800°C以上になるとクセノンランプを使用する必要がある。
各ファーネスにより加熱できる試料の面積と温度は図1に示した。
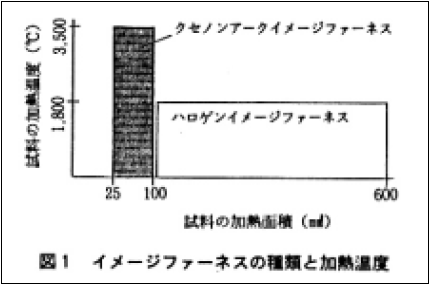
ランプイメージファーネスの形:
イメージファーネスはランプを熱源として,ミラー光学系と組合せ,ランプの熱現像をミラーの焦点に集光し空間に光エネルギーを集中させる装置である。ミラー光学系は放物面鏡を一対にした形式,楕円面鏡を一対にした形式があり,加熱する用途に応じることが出来る。
ランプイメージファーネスは,図2のようにランプとミラーの組合せで加熱イメージを形成することで色々な加熱ニーズに応じることが出来る。

双ミラー型イメージファーネスは,ランプアークまたはフィラメントの大きさと同じ大きさのイメージを形成することが出来る。
異倍率ミラー型イメージファーネスは,ランプアークまたはフィラメントの大きさの2倍程度のイメージを造る場合に適している。
単ミラー型イメージファーネスの場合は,2〜5倍程度の拡大イメージの形成により使用する。
ミラー組合せの倍率により最高加熱温度と加熱面積が異なってくる。クセノンランプ10kWの例で光学系を変えることによる光出力の変化を図3に示す。
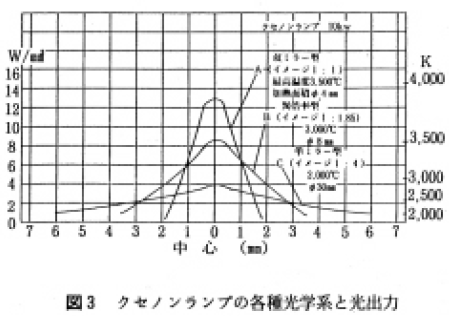
クセノンアークイメージファーネスに利用できるランプは,短アークでアークの安定度の高いことが,加熱を行う上で重要である。ランプの諸元は図4に示し,用途に応じて選定出来る。
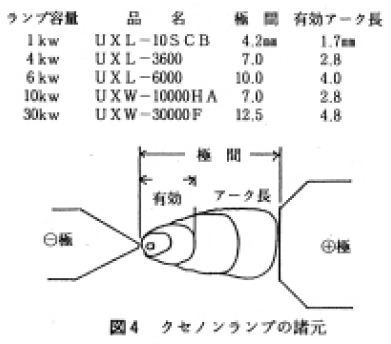
イメージファーネスに使用するハロゲンランプは高密度に巻いたタングステンフィラメントが特徴である。ランプの諸元は図5に示す。
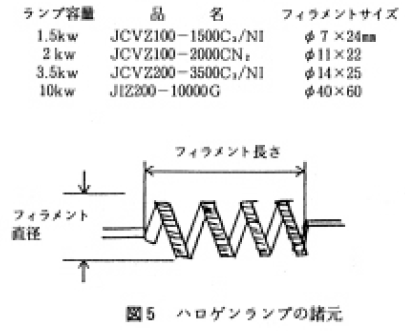
③ 極超高温酸化/揮散試験機
3.1 極超高温酸化/揮散試験機とは
はじめに述べたように,次世代の航空機は超高温に加熱される。一方において,大気圏外を長期に飛行するとそこに存在する原子酸素と太陽光の紫外光によって有機材料が劣化することが知られている。この環境を地上で再現するための試験機の概念と主要仕様を図6に示す。図の真空チャンバーから上の部分はクセノンランプ加熱装置又は原子酸素/紫外線暴露装置のどちらかを選択することで両方の試験が行える様になっている。
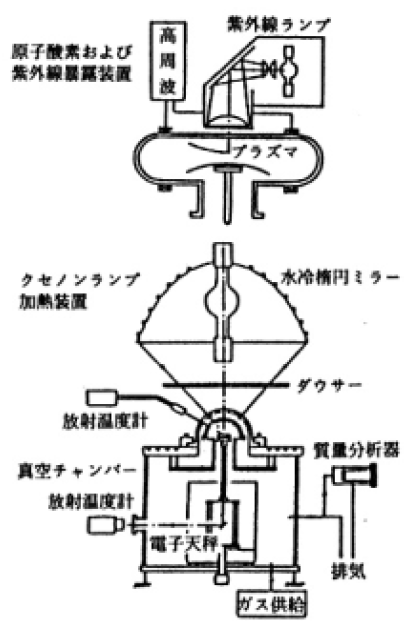
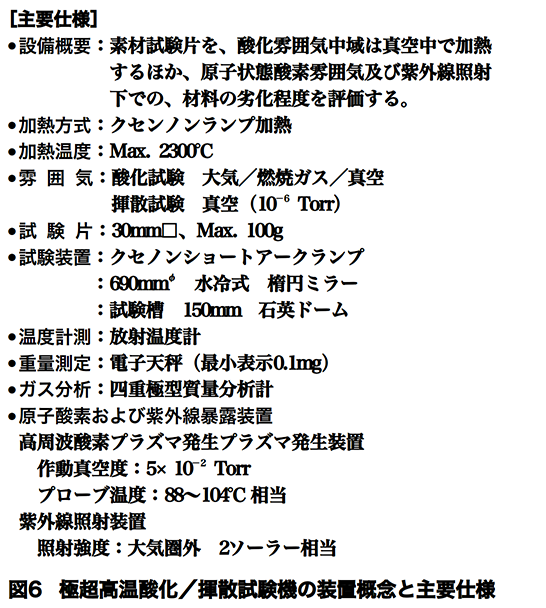
クセノンランプ加熱はクセノンランプ30kWを使用し, 30mm□の試料を最高温度2,300°Cまで加熱できて,その雰囲気は大気/燃焼ガス/真空を可能としている。
真空チャンバーには温度計測/重量測定/ガス分析が同時に測定できるデータ処理系がつけられる。
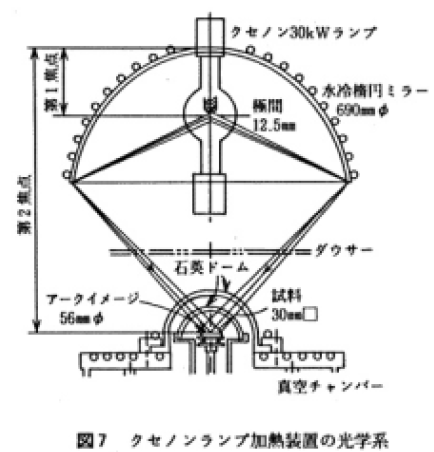
3.2 アークイメージによる加熱
前記試験機で加熱する試料は30mm□とし,断熱支持台の上に置かれる。30mm□試料を加熱するアークイメージはクセノン30kWランプの極間12.5mmを楕円ミラーの倍率によって56mmΦのアーク像として形造られる。これは単ミラー型イメージファーネスで構成する光学系から成っている。
クセノン30kWランプの極間に生じたランプアーク像は12.5mmの極間とほぼ等しい寸法で形成され,その極間の中間6.25mmの位置を楕円ミラーの第一焦点に位置合せを行った時に楕円ミラーの第2焦点にアークイメージ 56mmΦを得られる光学ミラーとする。
光学系による光エネルギーの伝送は次の様になる。クセノン30kWランプのアーク特性は光となるのが入力の半分0.5である。楕円ミラーは光学研磨され表面は金めっき処理が施されるためミラー反射率0.9,ミラー集光率は楕円ミラーの笠の深さの度合でこの場合ランプの配光の 80%をカバーする形0.8となる。石英ドームは光の透過と反射を合せて0.85となる。
従って,ランプイメージファーネスのエネルギー伝送はランプ放射率0.5,ミラー反射率0.9,ミラー集光率0.8,石英ドーム大0.85,石英ドーム小0.85をかけ合わせた光学効率η=0.26となる。
エネルギー密度Eはランプ入力P,光学効率η,表面積Aにより,
E=(P×η)/A
で示される。本イメージファーネスの場合は,A:アークイメージの大きさ56mmΦであるので,2,460mm2, P:30kW(30,000W), η = 0.26となるのでE=(30,000×0.26)/2,460=3.1W/mm2となる。
試料の表面ふく射率を0.8として, 3.1W/mm2×0.8 = 2.5W/mm2 この値は2,600Kに相当する(約2,300°C)以上の様に真空中において,30mm□試料を最高2,300°Cに光加熱するシステムをもつ極超高温酸化/揮散試験機となる。
3.3 ガス分析/重量分析
(1) 真空中での測定
排気系の概要を図8に示す。主排気に 550l/sのターボモレキュラーポンプを使用し,試料チャンバーを10-4Pa以上に排気した後,アークイメージファーネスで,試料を加熱する。試料の揮散減少は,真空仕様天抨で測定する(分解能0.1mg)。放出ガスの全圧はヌード型B—Aゲージで測定し,分圧は四重極型質量分析装置で測定される。
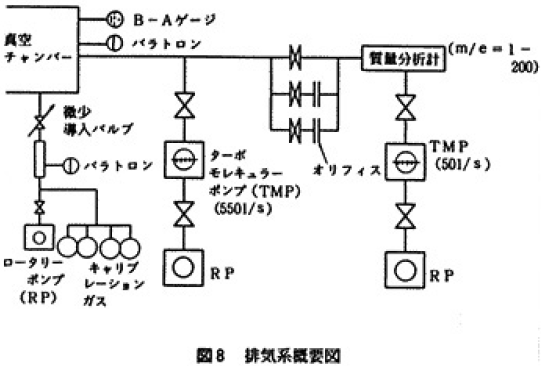
放出ガスは,あらかじめ,標準ガスを使用し,各ガスの実行排気速度,質量分析装置の相対感度係数を求めておくことにより,定量測定が可能である。本法を用い (加熱方式は異なる),各種材料の放出ガスが測定されている。図9に石英ガラスのガス放出測定結果を示した2)。加熱は抵抗炉である。このように,何度で,どんな種類のガスが放出するか知ることが出来る。上述したように,ガス放出曲線を積分し,目的のガス種の実行排気速度を乗じることにより,定量も可能である。
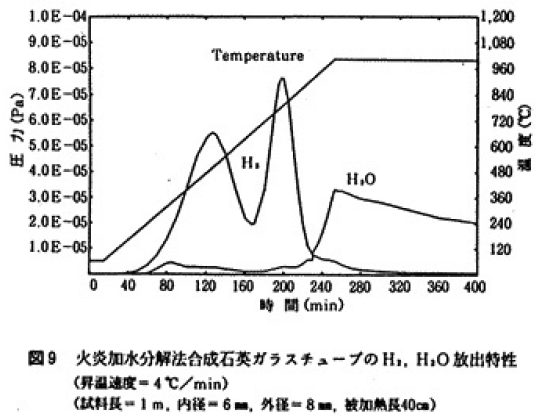
(2) 酸化雰囲気での測定
本装置は酸素などのガス雰囲気でも測定可能である。
重量測定は問題はないが,質量分析は10-3Paより真空度が低いと動作出来ない。そこで10-2Paでも測定出来るように,質量分析は50l/sのターボモレキュラーポンプで作動排気されている。放出ガスはオリフィスを通して質量分析に導入され,分析される。
④ おわりに
超高温材料研究センターの岐阜センターには超高温材料の各種の評価装置が設置され,この極超高温酸化/揮散装置の他に5種類の装置が完備される。21世紀の航空機材料の他,自動車,電力機器,高温ガス機器等の超高温材料の評価にも応用されるであろう。
3.11光(ハロゲンヒータ)の市場性とその拡大
3.11.1 現状
民生分野・工業分野を問わず、ハロゲンヒータの市場は拡大を続けている。当社では 1980年代の民生分野における調理用・暖房用ヒータと電子部品業界の加熱用ヒータへの採用を皮切りに、半導体製造工程・塗装乾燥・真空機器分野などの工業用途における採用が顕著になってきている。これらの産業分野拡大の基本的背景には、ハロゲンヒータの持ついくつかの性能のうち、特に電気からの熱交換が高効率で実現されることと、コンパクト、被加熱体の温度への応答性と制御性の良さが、共通して評価されている点が挙げられる。また一方で、非接触で加熱ができ、ガスを放出せず、チリ、ホコリも巻き上げないという、光加熱ならではのクリーンな熱源である点も、半導体や塗装関連で採用を伸ばした大きな理由であろう。以下に主要な採用例におけるハロゲンヒータのメリットを特徴づけるため、各ユーザのコメントの中から特に大きなメリットについてのみまとめた。
この他、ワークのサイズに合わせて、ヒータ部の変更が容易であるとか、工程内不良に対応する際、加熱工程のロスが極小化できるなど、特異なメリットを見出すケースも少なくはない。光(ハロゲンヒータ)加熱の利用は、大幅な処理時間の短縮や、作業環境の改善にとどまらず、多種多様な効果が期待されている。
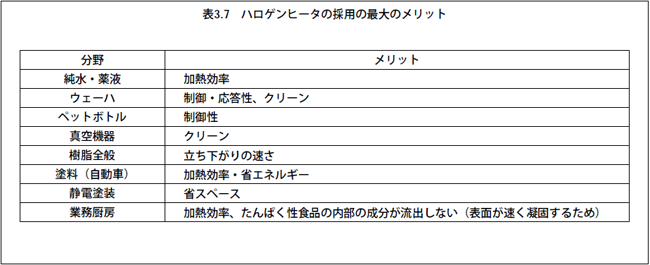
3.11.2 ハロゲンヒータの展望
今後の光加熱、特にハロゲンヒータの市場性について2つの展望を提起したい。第1は、各産業界の製造ラインの乾燥工程における、生産性向上、省スペース化を目的としたハロゲンヒータとその加熱システムの展開である。世界のトップクラスを行く、日本の製造業の現場レベルでの改善意欲は、日々の歩留り向上や品質改善のみならず、生産方法の改善、設備、治工具の革新的な改善によるコストダウンに直結する作業時間の短縮や、製品の画期的な性能・品質の向上である。様々な熱源が乾燥工程に採用されている中で、光(ハロゲンヒータ)加熱の決定的な違いは、通電後1秒以内に立ち上がるその応答性の早さである。つまり、ラインにおいて設定温度到達までの予熱は不要となり、電源オフ後の立ち下がりの遅さからくる製品への熱の悪影響も回避できる。さらに、ミラーとの組み合わせによる、集光(熱)技術の利用により、必要な部分のみ乾燥させることも可能である。そして採用が実現すると同時に省スペース化が達成されるという大きなメリットも光加熱の魅力である。なぜなら、ハロゲンヒータそのものがコンパクトなことに加え、ダクトなど付帯設備が不要で独立した加熱源であるためである。現在、ウシオ電機(株)ではコンベアを含めた製造ライン向けの乾燥テストラインを準備中であり、様々なユーザの乾燥工程にこれまで以上に積極的な光(ハロゲンヒータ)加熱の提案を展開していきたい。
もう1つの展望としては、高齢化社会、環境重視の生活の構築という時代の要請に対応した、効率的で省スペース、安全かつクリーンな、照明暖房としてのハロゲンヒータの提案である。ウシオ電機(株)は3年前より大手住宅メーカとの共同研究による高齢者対応住宅向け、暖房照明システムの開発をすすめてきた。一般住宅にとって、トイレ、浴室、洗面脱衣室向けの応答性の良い快適暖房システムは大きな魅力であり、ハロゲンヒータは視覚にも訴え得る“光のシャワー”を可能にする。また、数種の配熱ミラーとセンサの組み合わせにより、距離による配熱不良を緩和しながら、必要な時に必要な配置へ効率よく配熱するスポット照明暖房も様々な空間で採用され得るであろう。
3.11.3 ウシオ電機(株)のめざす方向
ハロゲンヒータを軸とする光加熱の市場性は、今後ますます拡大していくものと思われる。ウシオ電機(株)は光の専門メーカとして、光加熱市場において、2つの方向性を明確にしていきたい。まずは、ハロゲンヒータ加熱システムとしてのバックアップデータの蓄積と、採用用途の拡大である。そもそも、赤外放射加熱は、特定波長による加熱を意味するものでなく、赤外域すベてのワークに対する効果を問うべきであろうが、その中で、ハロゲンヒータの存在位置、さらにウシオ電機 (株)の開発した遠赤外線ハロゲンヒータの加熱源としての効果を、ユーザとの積極的なかかわりの中から明確にしていきたい。その延長線上に、複合加熱というコンセプトにおける他熱源とのインターフェースが実現するからである。
2つ目は、ウシオ電機(株)がこれまで、情報機器の露光ユニットで培ったミラーの設計・量産技術の光加熱への応用である。感光体と高効率にマッチングする最適スペクトル、均一な配光パターンを実現する光の技術は真に熱に展開されるべきものと確信している。
ウシオ電機(株)にとって“光の時代”それは、熱の時代なのである。
(濱田恭造)