「電子材料」
特集 流体MEMSのすべて マイクロ流体デバイスの応用展開とその実用化
(2005年11月)
真空紫外線によるµ-TAS接着装置
ウシオ電機株式会社 システムカンパニー
福島 亮 川北 正人
1.はじめに
µ-TAS(micro Total Analysis Systems)は、医療分野のみならず環境など多方面で応用が期待されているマイクロ流体デバイスである。µ-TASは、流体の通る微細な流路を形成した基板とヒーターやポンプ、電極などを作り込んだ基板を貼り合せてできている この基板材料は、ガラス、PDMS(シリコーン・ゴム)ポリマー、Siなど多様である。今回は、特にPDMS/PDMS,ガラス/PDMSの貼り合わせに紫外光のみ使い基板表面を改質し、簡単に接着できる装置を紹介する。
2.開発背景
当社は工業用ランプ(光源)で世界的なシェア( 半導体・液晶・OA機器他)を持っている。かつ工業用ランプを搭載した製造装置メーカーとして、製造装置市場へも幅広く進出している。また、常に光源の幅広いアプリケーションを模索している。そこで、今後の市場と期待できるMEMS/ナノテク・バイオ市場への参入を 図るため、03年1月に京都で開催された国際会議MEMS2003へ出展した。それが本装置の開発のきっかけをつくった。
この会場で東京大学生産技術研究所の藤井輝夫助教授(当時)が当社の真空紫外線ランプユニットに注目し、声を掛けて頂いた。藤井研究室で開発中のµ-TASは、ガラスに電極などを作り込んだ基板と、PDMSという透明なシリコーンゴムで形成した流路基板を貼り合わせて作る。PDMSには自己吸着性があるが、パーマネントな接着をするためには、真空プラズマ処理で表面改質を行い、その後人の手により位置合わせして貼り合わせるといった手間が掛かるプロセスが必要だった。そのプロセスを紫外線のみの照射で表面改質し、当社が持っているアライメント技術で簡単に接着できないかというのが本装置の開発の背景である。
装置の開発は、研究・開発向けとして、コンパクトな卓上型とし、表面改質用の真空紫外線照射部とアライメント部の2つの構成とした。光源は、発光波長172nmの真空紫外エキシマランプを採用し、PDMSへの照射実験において、表面改質が確認され接着が実現できた(写真1)。また、アライメント部には、光学顕微鏡を採用し、誰でも簡単に位置アライメントできる機構とした。こうして、研究、開発向けでコンパクトなµ-TAS接着装置が完成した(写真2)。
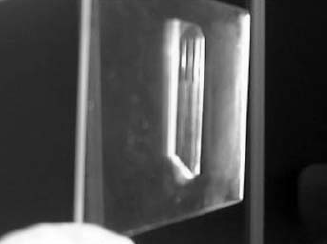
ガラス:プレクリーン品、VUV
8.7mWx60sec照射
PDMS:8.7mWx10sec照射
写真1 PDMSとガラスを接着した例
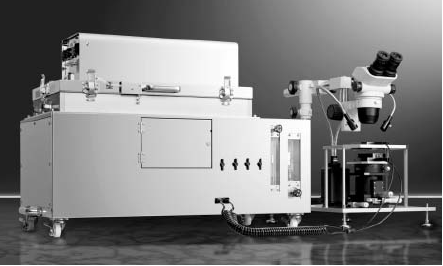
写真2 µ-TAS接着装置
3.装置の特徴
今回開発したµ-TAS接着装置の特徴は以下である。
- ① 接着プロセスは、紫外線の照射、簡単な位置合わせ(アライメント)と非常にシンプルで、PDMS-PDMS,PDMS-ガラスの強固な常温での接着が可能である。
- ② メンテナンスはランプ交換のみと至って簡単。また、瞬時点灯・消灯ができるランプのため、必要な時だけの点灯ですみ、寿命長く使用できる。
- ③ 基板の接着のみならず、UV洗浄、表面改質装置としても利用できる。
参考のため、従来の真空プラズマ装置との比較表を作成した(表1)。
なお、大気圧プラズマ装置も市販されているが比較は別の機会に譲ることとする。
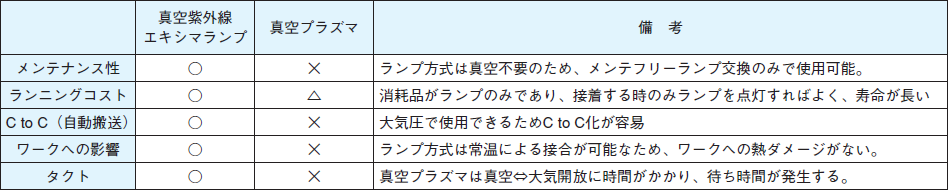
表1 真空紫外線エキシマランプとプラズマ装置の比較
4.要素技術
µ-TAS接着装置は、主として紫外線照射部(光源)とアライメント部の2部で構成されている。ここでは本装置の要素技術について述べる。
4-1.真空紫外線エキシマランプ
(1) 真空紫外エキシマランプの原理
本接着装置には172nmを中心波長に持つ単色光のランプを使用している(図1)。光の持つ化学エネルギーはその光の波長が短いほど強いことが知られているが、このランプはXeガスを封入し誘電体バリア放電をさせることで、発光ピークが1つのきわめて高効率な紫外線エネルギーを照射できる(172nmの変換効率は10%)。
そのランプの構造であるが、石英ガラスの2重構造になっており、内管の内側には金属電極、外管の外側には金属網電極がそれぞれ施されている。また石英ガラス内管には放電ガスが充填され、電極に交流の高電圧を印加すると、2つの誘電体の間で細い針金状の誘電体バリア放電が多数発生する。
この誘電体バリア放電は高エネルギーの電子を含有しており、かつ、瞬時に消滅するという特徴を持っている。この放電により、放電ガスの原子が励起され、瞬間的にエキシマ(分子状態なる直前の不安定な状態)となる。このエキシマ状態から元の状態に戻る時に、そのエキシマ特有のスペクトル(エキシマ光)を発光する(図2)。
上記の172nmの光エネルギーはほとんどの分子結合エネルギーを切る力を持っている(図3)。
原理的には洗浄能力が高いことが分かると思うが、実際にデータを取ったところ、濡れ性指数を確認すると照射後には短時間で限りなく0に近づいている(写真3)。XPS分析では、サンプル表面の炭素が減少していく(図4)。ガスクロマトグラフィの分析では、照射後はサンプル表面の有機物が除去されている(図5)。
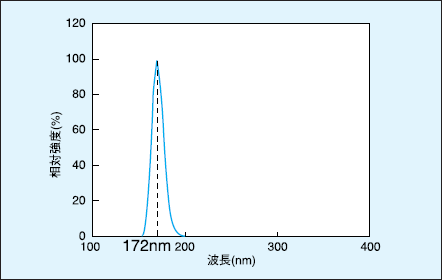
図1 真空紫外線エキシマランプ(172nm)の発光スペクトル
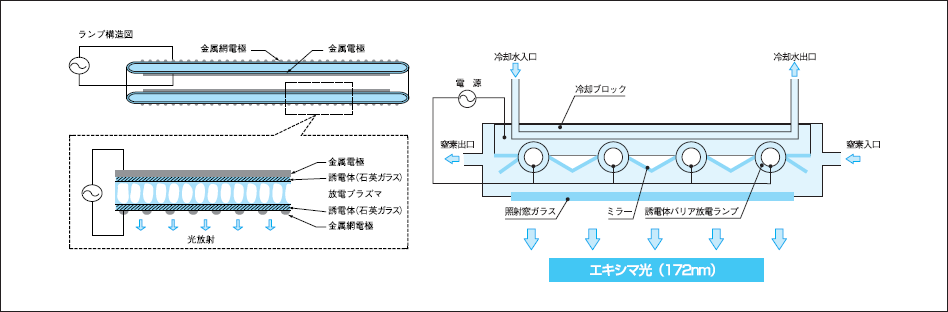
図2 発光原理とランプハウス構造
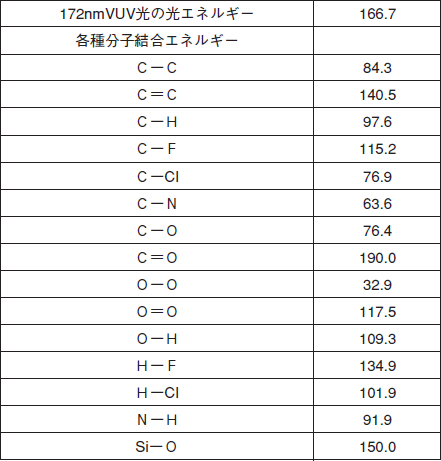
図3 有機物の結合エネルギーとフォトンエネルギー(Kcal/mol)
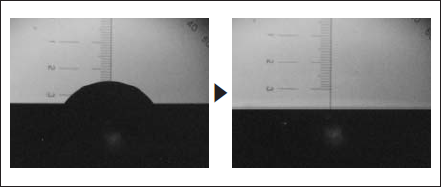
写真3 照射前後の接触角の変化測定
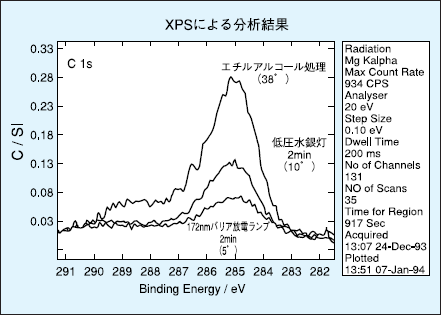
図4 XPSによる炭素量の減少測定
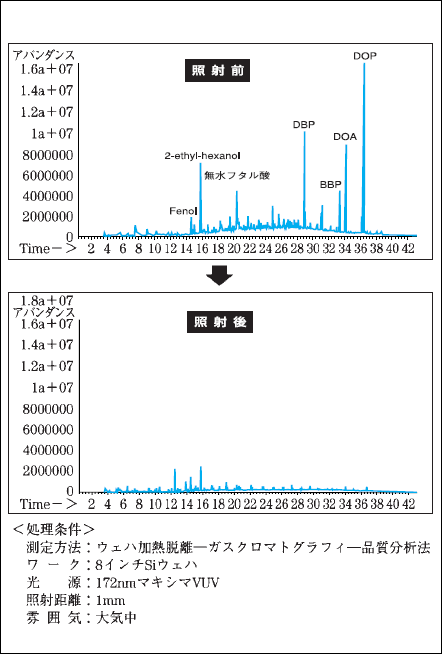
図5 ガスクロマトグラフィによる有機物除去の測定
(2) 真空紫外線エキシマランプの応用例
上記にて紹介した真空紫外線エキシマランプは産業界ですでに使用されている。特に液晶業界では、装置化され、①ランプの長丈化が可能なため、大きな基板に対応できる ②面内均一性が高い ③高照度・高タクトを実現しているという特徴を生かして、ドライ洗浄プロセスの標準機となっている。
また半導体業界では表面改質によるフォトレジストの塗布性向上目的で使われるなど、最先端で活躍している。
4-2.アライメント部
現状のアライメント部は市販の顕微鏡とXYZステージ部で構成されている簡易システムである。基板のエッジを顕微鏡を介し、人の目で合わせる(マニュアルアライメント)ため、アライメント精度は±100µm程度である。これは、操作の簡便性および装置のコストを優先させた結果である。今後、µ-TASは、ますます微細化が進むことが見込まれるため、接着装置にもより高度な位置合わせ精度が要求されてくる。当社では、高精度パターニング用マスクアライナを量産しており、そこで蓄積したオートアライメント技術で、±0.5µmの位置合わせ精度を実現できる。この応用で、今後予想される高精度アライメントにも対応が可能である。もちろん、自動搬送システムへの展開も可能だ。
表2に、今回開発したµ-TAU接着装置(UVS-2000ST)の主な仕様を紹介する。
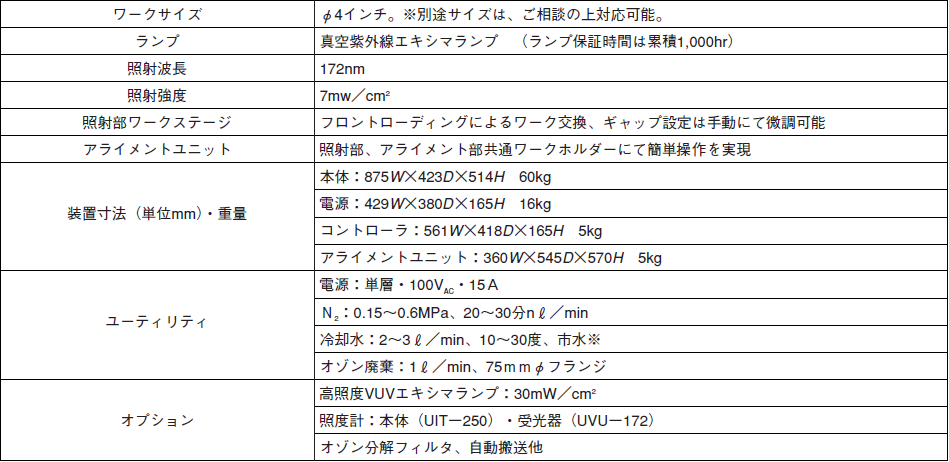
表2 UVS-2000STの仕様
5.今後の方向性と課題
接着、接合は、MEMS/ナノテク,バイオ市場にとって大きな課題である。PDMS、ガラスに留まらず、異種材料の接着、接合へ光の可能性を追求し応用範囲を広げていきたい。また、最近半導体製造プロセスへの応用として波長126nm真空紫外線エキシマランプを使った、300mmΦウエハ一括照射可能な装置を開発した。これは、ゲート酸化膜の高絶縁化(High-k)プロセスへの応用が考えられ、さらに大面積照射が可能になったことで、表面改質やエッチングその他、新しい用途開拓が期待できる。
このように、われわれは、今後も光技術でさまざまなニーズにお応えできるよう開発力を高めていく所存である。
最後に装置開発にご協力頂いた東京大学 藤井先生、山本先生には、この場をお借りしてお礼を申し上げる。
以上