光技術情報誌「ライトエッジ」No.31 (2008年10月発行)
「エレクトロニクス洗浄技術」技術情報協会
(2007年10月)
紫外線洗浄
ウシオ電気株式会社
遠藤真一
はじめに
紫外線(Ultra Violet ray)は比較的高いフォトンエネルギーを持つことから、有機化合物を分解することはか なり古くから知られていたが、30年ほど前にフォトレジスト高分子の分解に応用されたのが紫外線とオゾン(O3)による光洗浄の始まりと言われている[1]。
現在では紫外線による表面の精密洗浄や表面改質は、もはや一般的に使用されている技術である。UV/O3洗浄と呼ばれるこの技術は、半導体、FPD(フラットパネルディスプレイ)基板の製造工程のみならず、あらゆる産業分野で多用されている。
本稿では紫外線洗浄技術と応用例、最近の研究事例等について解説する。
1. 紫外線洗浄技術
1.1 紫外線洗浄の原理
UV/O3洗浄の基本原理は、酸素を含む雰囲気ガス中にUV照射で生成された酸素ラジカル(O3や原子状酸素など)が、汚染物である有機化合物のUVで切断された分子結合の箇所に直ちに酸化反応して、単純な分子であるCO2、H2O、O2などが生成され、これらが表面から揮発して除去(洗浄)されるというものである[2]。
このことを概念的に示したのが図1である。この図では従来から光洗浄で主に用いられている低圧水銀ランプと最近広く利用されるようになったキセノンエキシマランプの比較が模式的に示されている。ここでは波長(フォトンエネルギー)の違いから酸化能力が高いと言われている原子状酸素ラジカルをダイレクトに生成できるかどうかと、酸素による光吸収度合い(吸収係数)の違いから生成される活性酸素料の多少の違いが比較で示されている。
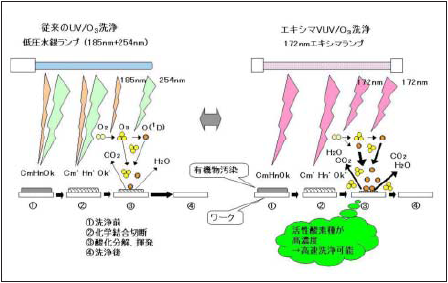
図1.UV/O3先浄の原理
1.2 光のエネルギーと物質の作用
紫外線は電波や可視光と同じく電磁波の一種であり、そのフォトンエネルギーEは次式(1)で与えられる。

ここでhはブランク定数(6.626 × 10-34 J·s)
c は光速(2.998 × 108m/s)
λ は電磁波の波長(10-9m)
この式ではフォトンエネルギーは波長に反比例するので波長が短いほどエネルギーが高いことが分かる。例えば波長172nmの真空紫外光(VUV)の場合、この式に当てはめるとフォトン1個当りのエネルギーは1.15 × 10-18J(7.22eV)で、モル(6.02 × 10-23個/mol;アボガドロ数)当りでは、167kcal/mol(698kJ/mol;1cal=4.19J)である。
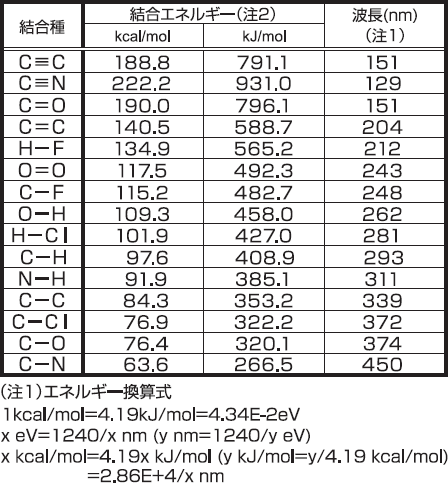
表1.分子の結合エネルギー
有機物の主な分子結合のエネルギーを表1に示す。低圧水銀ランプ(185nm;154kcal/mol)やキセノンエキシマランプ(172nm:167kcal/mol)では大半の結合を切断できることが分かる。
酸素を含んだ雰囲気ガスにUV照射することにより各種酸素ラジカルが生成されるが、ラジカルの生成効率や寿命の違いなどからそれぞれの生成量に違いが見られる。生成されるラジカルの主成分は酸素原子3個からなるオゾンであるが、これ以外にも更に反応性に富むと言われている原子状酸素(O(1D),O(3P))などのラジカルが生成される。これらは寿命が大変短い代わりに反応性が高いため、洗浄に大きな役割を果たしていると考えられている[3][4]。
一般的にある吸収媒体を透過する光の強度Iは簡略的に次式で表すことができる[5]。

ここでIoは透過前強度
αは吸収係数(atm-1・cm-1)
pは吸収媒体の分圧(atm)
Lは透過距離(cm)
この式を使って172nmと185nmのVUVの大気中における減衰を計算した結果を図4に示す。吸収係数の大きな172nmVUVは大気中を数mm透過しただけでも大きく減衰するのに対し、185nmVUVはさほど減衰しないことが分かる。これは大気中でVUV照射する時に波長によっては照射距離が重要なパラメータとなることを示している。
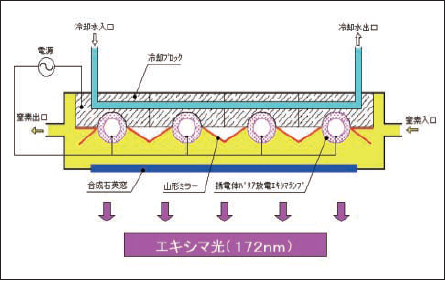
図4.エキシマ光照射装置の一例
1.3 紫外線光源
紫外線洗浄の原理を活用して、生産ラインへの導入を図ろうとする場合には、紫外線照射装置が必要となる。高エネルギーの電磁波を放射する光源は紫外線ランプのほかにもレーザーやシンクロトロン放射、電子線などがある。洗浄装置として検討する場合には、経済性、安全性、環境負荷も重要な検討項目であり、それらの面から紫外線ランプがすぐれている。
紫外線ランプには低圧水銀ランプとエキシマランプがある。低圧水銀ランプはランプ内に封入した水銀の共鳴線(185nm、254nm)を利用するものである。低庄水銀ランプの発光原理は、家庭用の蛍光ランプと同じであるが、発光管が紫外線を良く透過する合成石英ガラスであること、蛍光体が無いことである。点灯するには安定器とよばれる電源が必要である。比較的長寿命(2000〜4000時間)で安価ではあるが、点滅点灯では寿命が大幅に短くなること、水銀が含まれているので使用済みランプの廃棄に環境面での規制がある点に注意を必要とする。
エキシマランプは合成石英ガラスの発光管にキセノンガスを封入し、発光管の表面に設けた網状電極に高周波電圧を印加し高電界中でキセノンエキシマ(Xe2*:Xenon Excimer)が励起生成し、172nmの真空紫外線を放射するランプである。最近では高出力化、長寿命化(3000時間)がされている。
ランプハウスは紫外線ランプを搭載し、反射板や照射窓などを利用して紫外線を効率よく放射するように設計されている。ランプへの給電、冷却のほか、紫外線やオゾンが漏れないよう遮蔽する機能が備わっている。紫外線照射装置は光源の種類、照射方法など多様な形態があるが、次節では現在のエレクトロニクス分野で最も導入事例が多いエキシマ光照射装置について解説する。
2. エキシマ光による洗浄技術
2.1 エキシマランプの特長
光洗浄に用いられる紫外線ランプは、従来185nmと254nmに主な放射強度を持つ低圧水銀ランプが主なものであったが、最近はより短波長の172nmに発光中心波長を持つキセノンエキシマランプがLCD製造工程等の洗浄プロセスで広く利用されるようになった。エキシマランプは従来のランプと違って単一波長、瞬時点灯・点滅点灯が可能、低温処理が可能、といった様々な特長を持った光源である6。予備点灯やシャッターが不要であり、必要なときにのみ点灯すれば良く、実質的にランプの長寿命化に繫がる。単一波長であることより赤外線を放射せず、低温での処理が可能となる。さらに、その高いエネルギーのため処理時間を短縮でき、効率的な光照射が可能である。またランプの点灯方向に制限が無く、ラインに合わせて立面での照射も可能である。
2.2 ランプハウス・点灯電源
エキシマランプを搭載したUV照射装置の一例を図5に示す[7]。キセノンエキシマ光(172nm)は酸素による吸収が大きいため、ランプを収納する容器(ランプハウス)内部は光を吸収しないガス(一般的には窒素)で置換、合成石英ガラスからなる窓を通して放射される。ランプハウス内には照射面積に応じて複数本のランプが並べられ、光を効率よく取り出すためにミラーが配置されている。
通常は雰囲気の酸素濃度が安定している大気中で使用されるが、光の利用効率を高めるため、ワークと光照射装置の間の空間を窒素パージすることにより酸素分圧を下げて使用することも行なわれている。窒素パージにより酸素分圧を5%以下に下げると、172nmの紫外線は酸素による吸収を受けにくくなるので、照射距離をおおきく設計することができる。また照射窓ガラスを無くしたタイプのUV照射装置も使用され始めている[8]。
エキシマランプを点灯するには専用の点灯電源が必要である(写真1)。エキシマランプは数十kHzの高周波で点灯されるが、点灯電源は電圧波形を最適化する ことで172nmの放射を高効率化している。また、安全機能、通信機能、リモートコントロール機能のほか、異常表示機能、トラブル解析ヘルプ機能など、安全性、信頼性、ダウンタイムの圧縮に配慮された設計がなされている。
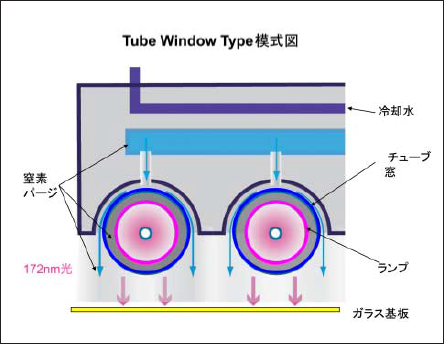
図5.石英窓なしタイプ光照射装置
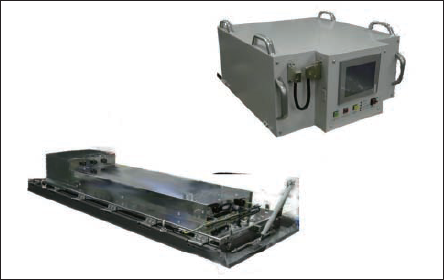
写真1.ランプハウスと点灯電源
2.3 光計測
紫外線洗浄技術の利点として、紫外線エネルギーの管理が容易である点も欠かせない。写真2は紫外線照度計の一例である。洗浄プロセスの管理は紫外線量を保っことであるが、紫外線量はランプの効率低下、反射板の反射率低下、異物の付着など様々な要因がある。したがって定期的なメンテナンスが必要であり、装置の状態を再現性よく計測できるのは大きなメリットである。最近では紫外線センサーを装置内に設置し、常時モニターしたり、紫外線センサーからの出力値を点灯電源にフィードバックして光出力の安定化機能を搭載した紫外線照射装置もある。
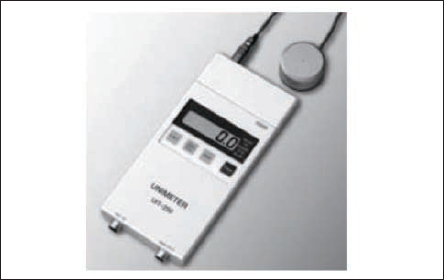
写真2. 172nm用紫外線照度計
3. 紫外線洗浄の応用事例
3.1 応用例と評価法
現在光洗浄は各方面で広く用いられているが、その中でも特に洗浄プロセスの多いLCD製造工程では、近年の大型化に伴い高速洗浄性、装置の小型化、低温処理性が要求され、このニーズにマッチしたエキシマランプを搭載したUV照射装置が数多く稼動している。
基板表面の有機汚染に対する評価法としては、最表面分析法である光電子分光分析法(XPS)や、昇温脱離ガス分析法(TDS)などがあるが、これらはいずれも評価に時間がかかることや、分析装置が高価なことなどにより、一般には表面の濡れ性を評価する接触角法が簡易な方法として用いられている[9]。清浄度を示す尺度は純水の接触角度で表され、10度以下が一般の目安となっている。
3.2 半導体製造工程と紫外線洗浄技術
図6は半導体製造の前工程における紫外線洗浄導入箇所を示す図である。レジスト塗布前のウエハの表面洗浄、露光前•露光後の洗浄に用いられている。また、レジストのアツシングにも用いることができる。
図7は有機物汚染されたシリコンウエハの洗浄前後のサンプルについて、加熱することにより表面から脱離してくる汚染成分をガスクロマトグラフィ質量分析法(GC-MS)により成分分析した事例である。
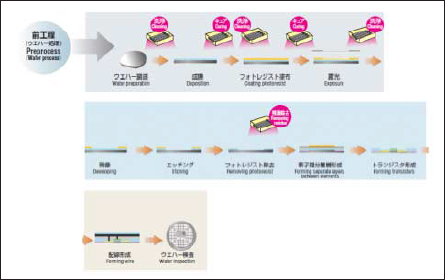
図6. 半導体前行程における光洗浄技術
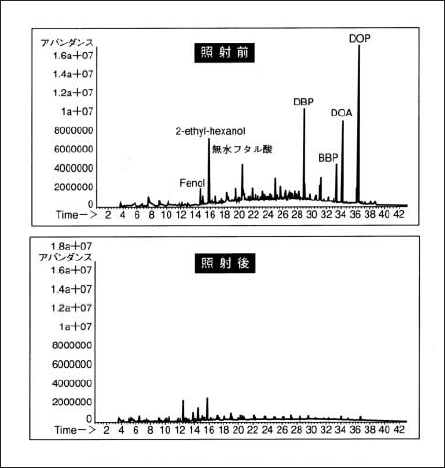
図7. シリコンウエハのGCMS分析データ
3.3 液晶パネル洗浄工程と紫外線洗浄導入箇所
図8はLCDパネル製造工程における紫外線洗浄の導入箇所を示す図である。LCD製造工程では、アレイ/カラーフィルタ工程では基板投入前、成膜前、レジス卜塗布前、エッチング•剥離前後の各洗浄プロセスで、セル工程では配向膜塗布前、COG実装前の洗浄プロセスで導入されている。図9にはLCD基板の素ガラス(無アルカリガラス)を光洗浄した事例が示されている。この例では水の接触角により清浄度が評価され、低圧水銀ランプとキセノンエキシマランプの洗浄能力の比較が示されている。
図10にはポリイミド(PI)膜の表面改質前後の水の接触角の変化を示したものである。改質前72度であった接触角が改質後6度にまで大きく低下して濡れ性が大幅に向上しているのが、目視ではっきりと確認できる。
図11は石英ガラス上の最表面をXPSにより分析したもので、有機物汚染の主成分としてカーボン(C)に注目し、洗浄前後で大きくCのピーク強度が変化する様子を示したものである。
液晶ディスプレイには表示面周辺にドライバーIC等を接続する為の配線パターンが施されている。ここにドライバーIC等の電気部品を接合する際に異方性導電フィム(ACF)が使用される。ACFの接着信頼性は液晶ディスプレイの品質に重要な役割を果たす。配線パターン上を光洗浄することで、接着信頼性を向上させることが出来る。図12に洗浄の有無による接合部のシェア強度の分布を示す。洗浄は窓面放射照度20mW/cm2のエキシマ光源を使い、大気中,照射距離1mm,照射時間5secで行った。光洗浄により密着強度が向上し、バラツキが小さくなっている事が分かる。
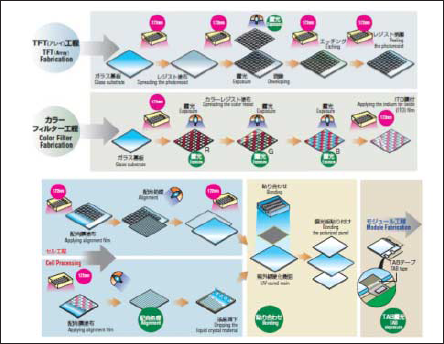
図8. LCDの製造工程と光洗浄技術
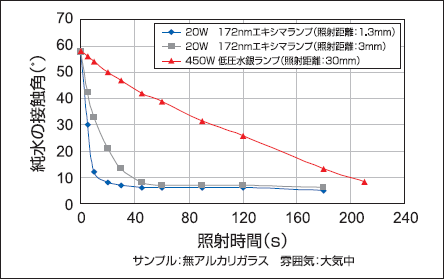
図9. LCD素ガラス洗浄データ
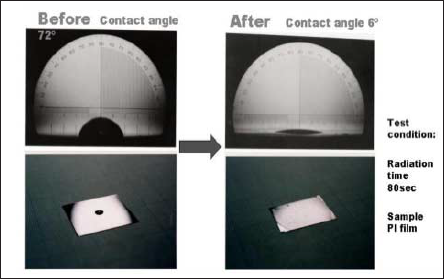
図10. PI膜の接触角変化
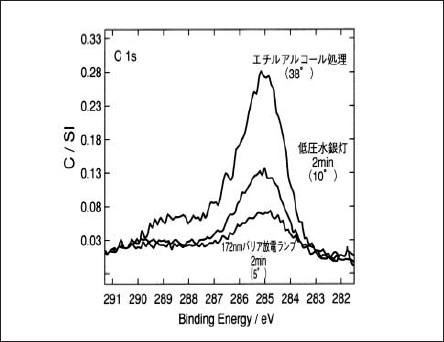
図11. XPS分析データ
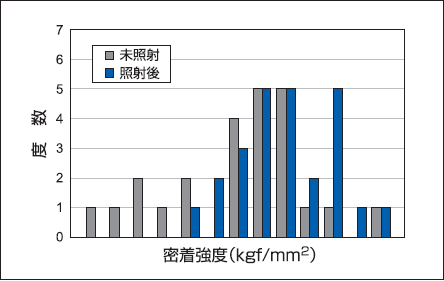
図12. ACPの密着強度の分布
3.4 その他の用途
現在主に使われている有機ELディスプレイは発光層に低分子有機材料を使用したものである。低分子有機材料は、極めて水分に弱く、大気に曝すと湿気を吸い込み、輝度が低下してしまう。そのため、大気を遮断した雰囲気で金属やガラス製の封止用キャップを紫外線硬化型接着剤で封止(カプセル化)して、大気と完全に遮断させる。封止部分の密着信頼性は製品の品質に大きく影響し、接着面の有機汚染を光洗浄で除去する事によって接着信頼性を向上させることが出来る。
シリコンウエハや液晶ガラス基板の洗浄だけでなく、ハードディスク洗浄、金属表面や金型の洗浄など最近では様々なワークへの応用が展開されている。従来は僅かの有機物汚染除去に対象が限られていたが、最近ではエキシマランプの高出力化が実現したことにより、プラズマ処理に比べてダメージレス化が図れるということから、レジスト除去などにも注目が集まってきている。
また、紫外線とは相性が悪いといわれていたプラスチック基板の洗浄や繊維の改質など新しい用途も開発・研究されている。
4. 最近の研究事例
エキシマ光照射装置はドライ洗浄装置として稼動しているラインが多数あるが、処理条件を最適化し少ないランプ灯数で処理ができるようプロセスの改善を図ったり、前後のプロセスや加熱条件をインテグレートしたプロセス開発が行われている。
基板サイズが大きくなると試作機,実験装置が大型化し、開発費,検証時間に影響を及ぼす。弊社ではこの問題に取り組むため、シミュレーション技術を製品開発に取り入れている[10]。以下にその技術の一例を解説する。
UV/オゾン洗浄における照射雰囲気の制御は従来から知られている技術[11]である。減圧または窒素パージによって酸素濃度を制御し紫外線の吸収ロスを減らし、光エネルギーを有効に利用できるが、大型基板の処理においても同様に酸素濃度が洗浄処理に影響をおよぼす。
図13は、基板上の酸素濃度と光洗浄処理後の接触角を示すデータである。
図中、酸素濃度20%のデータは、大気中照射のデー夕である。照射距離によっても違いはあるが、基板上の酸素濃度を低下させてゆくと、接触角は低下する傾向がある。酸素濃度が低下することにより酸素による紫外線の吸収ロスがへり、基盤に紫外線が効率よく到達するためである。
しかし、実際に光照射装置の下に基板を搬送すると、基板の先頭では大気を巻き込むため酸素濃度が高いが、中央から後部に向かっては完全に置換されてしまい、有機物の酸化に必要な酸素が欠乏してしまう現象がみられる。動的な酸素濃度の変化や分布は解析が難しく、従来は詳しい研究がされていなかった。
コンピュータ上に構成したエキシマ光照射装置と処理室形状や排気条件を入力することで、さまざまな条件を作り出し酸素濃度と窒素パージ条件の最適値を容易に出すことができる。図14は最新の照射窓なしエキシマユニットのシミュレーション結果であるが、窒素パージ量が適正になっており、基板面の酸素濃度の均一性がよいことがわかる。このような解析により窒素使用量の低減をはかりランニングコストを抑えること可能となっている。このようにエキシマ光照射装置の開発評価だけでなく、セットアップ時の工数低減、装置導入後のラインプロセスの最適化に役立つ技術開発がなされている。
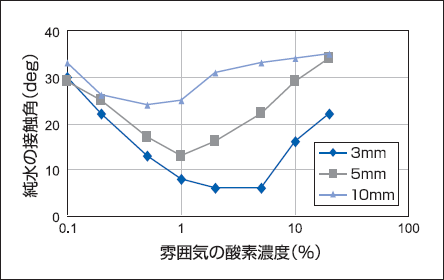
図13. 酸素濃度と接触角
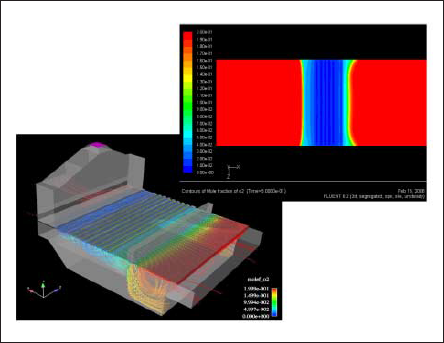
図14.流体解析酸素濃度シュミレーション
おわりに
エレクトロニクスデバイスでは僅かの表面に付着した有機物汚染が原因となって電気特性の劣化を招くことが多い。そのため光洗浄は精密ドライ洗浄として有効な洗浄法となっている。
今後、紫外線洗浄技術には大型化、低コスト化だけでなく高速化、省メンテナンス化、省スペース化の要素も付加されてゆくものとみられる。さらに接触角だけでなく、工程ごとに重視される性能(コンタミ低減、帯電防止、濡れ性向上など)が要求され、処理装置全体の多様なニーズへ応える必要がある。たとえばウエットエッチングの前洗浄として光洗浄を導入することにより、ウエットエッチング時の薬液の濡れ性向上、微細な表面凹凸の隅々まで薬液の浸透化が図れることから、薬液使用量の低減が図られ、エッチングをより効率的且つ効果的に行なうことが可能となる。
紫外線洗浄装置には、光処理であるため電気的ダメージが無い、光の計測・制御が可能である、プロセス効率が良い、コスト低減の余地がある等、実績が豊富なプロセスでありながら、次世代へ向けて多くの可能性がある。