大学研究室を訪ねて Campus Lab㉒
主な研究発表
アンモニアラジカルインジェクション
による同時脱硫脱硝
神原信志, 早川幸男, 増井芽(アクトリ-)
緒言
我々はこれまでラジカル連鎖反応を利用したラジカルインジェクション脱硝装置の開発を行ってきた1-4)。このラジカルインジェクション法※は、従来のプラズマ利用脱硝装置のように排ガス全体を励起するのではなく、脱硝剤のみを励起するため、電力消費量が極めて少なくなることに加え、装置が小型で単純なこと、冷却水を必要としないことなどの利点を有する。
燃焼排ガスには、通常、NOxのほか硫黄酸化物(SOx:主にSO2)が含まれる。温度域により、SO2はNH3と反応するため、SO2の存在はラジカルインジェクションによる脱硝特性に影響を及ぼすものと考えられる。
本研究は、ラジカルインジェクションによる同時脱硫脱硝における反応メカニズムを解明する第一段階として、脱硝性能に及ぼすSO2の影響を調べた。
実験装置および実験方法
モデルガス中NO濃度は500ppm、SO2濃度は250ppmとした。O2濃度は2.1%または8.3%とした。NH3/(NO+SO2)モル比は1.0または1.5とした。モデルガスと脱硫脱硝ガスの合計流量は3.0SLM一定である。モデルガス予熱部の温度は500 °C 一定とし、反応部温度を500°C~850°Cに変化させた。
インジェクター部では、澤藤電機製パルス電源を用いて、誘電体バリア放電(DBD)により大気圧プラズマを発生させた。ラジカルインジェクターは石英製円筒二重管構造であり、外筒外径4 5 m m( 厚さt = 2mm)、内筒外径38mm(t=2)、長さ490mmの石英管であり、ギャップ長1.5mmである。高電圧電極(SUS316)は内筒石英管に挿入し、接地電極(SUS316 パンチングメタル)は外筒周囲に巻き付けた。接地電極の長さは360mmであり、プラズマはこの間で発生する。
NH3/Arプラズマ内ではアンモニアラジカル(NHi)が生成し、これをモデルガスに吹き込むことにより、同時脱硫脱硝反応がおこる。印加電圧は3-15 kVに変化させた。周波数は10kHzで一定である。
ここでは、SO2の有無が脱硝率に及ぼす影響について報告する。
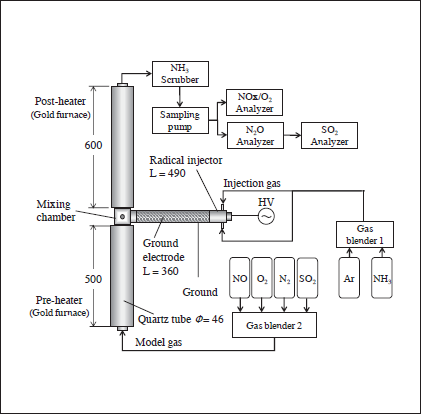
Fig.1: Schematic diagrams of experimental apparatus.
実験装置は、モデルガス(NO/SO2/N2/O2)供給系、脱硫脱硝ガス(NH3/Ar)供給系、ガス予熱部、インジェクター部、ガス混合室、反応部、高電圧パルス電源、NOx/O2、SO2、N2O分析装置よりなっている。
実験結果および考察
SO2なしでの脱硝特性
ここではNH3/NOモル比1.5、酸素濃度8.3%であり、SO2を含んでいない。温度500°Cでは脱硝は起こっていないが、600°C以上になると脱硝率の変化がみられる。脱硝率は、ある印加電圧で最大値をとった。例えば温度650°Cでは印加電圧8.0kVで、最大脱硝率39.5%であった。
温度が高くなるほど最大脱硝率は高くなり、その時の印加電圧は低くなった。焼却炉出口の排ガス温度は一般に750°C程度であるが、この温度領域では、極めて低電圧で80%以上の脱硝率を得ることができる。
ラジカルインジェクション脱硝法における反応メカニズムは未だ明らかではないが、印加電圧によって生成するラジカル種に影響されるものと考えている4)。すなわち、3kV程度の低電圧ではNH2ラジカルが多く生成し、高電圧になるにしたがってNH2ラジカルは減少し、変わってNHラジカル、Nラジカルが増加するものと考えている。NOx生成・消滅に関する素反応解析によると、NH2ラジカルは高温ほど脱硝反応が進行し、NHラジカルは低温域で脱硝反応が進行する。これより、600°Cでは高電圧で生成するNHラジカルが主に脱硝反応を進める役割を果たし、750°Cでは低電圧で生成するNH2ラジカルが脱硝に有効になるものと推定される。
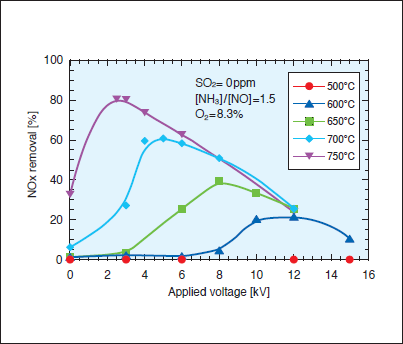
Fig.2 : Characteristics of NO removal by radical injection.
ラジカルインジェクション脱硝法での脱硝特性を、反応管設定温度(500-750°C)をパラメータとして示す。
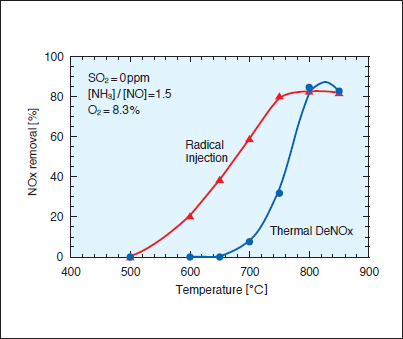
Fig.3 : Effect of temperature on NOx removal in radical injection and thermal de-NOx..
反応管設定温度に対する脱硝率の変化をラジカルインジェクション法とサーマル脱硝法について比較した。ラジカルインジェクション法は、サーマル脱硝に比較して低温域で脱硝反応が起こることがわかる。
SO2共存での脱硝特性
ラジカルインジェクションでは、500~700°Cの時、3kVを越えると脱硫率は減少する。特に700°Cでは3kV~6kVの間で急激に減少した。SO2とNHiラジカルの反応については、反応速度データが不足しているため、速度論的な考察は現在のところできないが、少なくとも3kVを越えるところで生成するNHiラジカルは、脱硫反応に有効でないことがわかる。したがって、ラジカルインジェクション法で同時脱硫脱硝を効率良く行うには、700°C程度の温度領域で低電圧で行う必要がある。
SO2が共存する場合、600~800°Cの領域で脱硝率が大幅に増加している。これはNHiラジカルがNOと選択的に反応している結果と考えられる。例えば600°C、12kVの時、脱硝率は21.5%から56.7%に大幅に増加している一方で、脱硫率は89.2%から59.0%に減少している(Fig.4)。これは、NHiラジカルが脱硝反応にある程度選択的に消費されたことで、脱硫率が低下したと考えられる。
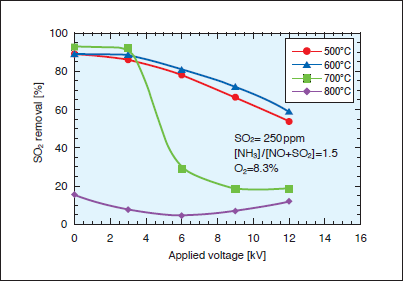
Fig.4 : Characteristics of SO2 removal by radical injection.
SO2=250ppm を加えた時の印加電圧に対する脱硫率の変化を示す。印加電圧=0kV、すなわちNH3による脱硫率は500~700°Cで90%前後であり、この温度領域では熱反応で高い脱硫率が得られる。
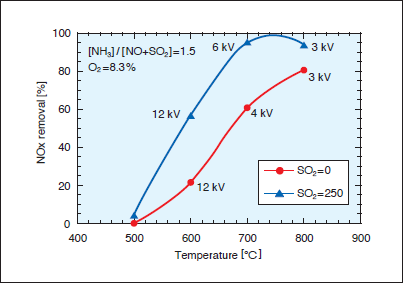
Fig.5 : Effect of temperature on NOx removal in radical injection and thermal de-NOx..
NOとSO2が共存する場合とSO2が無い場合の脱硝特性を温度に対してプロットした図である。
結言
ラジカルインジェクション法による同時脱硫脱硝実験を行い、SO2が共存する場合の脱硫率および脱硝率の変化を調べた。
SO2とNH3の熱的反応は、500~700°Cの範囲で容易に起こり、脱硫率は90%前後であった。ラジカルインジェクションでは、印加電圧3kVを越えると脱硫率は低下したが、変わって脱硝率が大幅に増加した。これはNHiラジカルがNOとある程度選択的に反応した結果であると考察した。
今後、SO2雰囲気でのラジカルインジェクション脱硫実験を行い、SO2の影響を明らかにする予定である。
微粉炭燃焼で生成するフライアッシュ
組成の特性化
遠藤倫子, 神原信志, 隈部和弘, 守富寛
緒言
石炭は微量ながらAs,Se,Bなどの有害元素を含有し、石炭利用プロセスにおいては、気相(排ガス),固相(フライアッシュや石膏),液相(脱硫排水)に分配され、その一部は環境中に排出される。石炭火力発電プロセスで発生するフライアッシュは、その大部分が電気集塵機で集塵され、セメント製造などへの有効利用または管理型埋立処理が行われる。管理型埋立処理場においては、フライアッシュ(FA)から溶出する様々な化学成分の流出を抑制するため、今後なんらかの積極的な対策が求められるようになってくるものと予想される。
我々はこれまで、微粉炭燃焼フライアッシュから溶出する微量元素の特性を調べてきた1-2)。その結果、微量元素の溶出量は溶媒pHによって大きく変化し、溶媒pHの増加によって溶出量が増加するタイプと、溶媒pHの減少によって溶出量が増加するタイプの2タイプに分類できることを明らかにした。周知のとおり、微粉炭火力発電プラントでは多種類の炭種が使用されており、それらのフライアッシュがどのような微量元素溶出特性をもつのか、事前に判断することは環境管理上、重要である。
本研究では、様々な炭種のフライアッシュの溶出液pHを調べ、微量元素溶出特性との関連を定量的に明らかにすることを目的としている。ここでは、微粉炭火力発電プラントの低低温電気集塵器で収集された14炭種のフライアッシュについて、環告13号試験に準拠した溶出試験を行った。炭種別および集塵室別の溶出液のpHおよび溶出試験前後の灰組成を調べ、溶出液pHを決定する因子について検討した。
実験方法
微粉炭燃焼プラントからのフライアッシュサンプリング
プラントはボイラ、脱硝装置、低低温EP、湿式脱硫装置(石灰-石膏法)、煙突から成り、途中にエアヒータ(AH)とガス-ガスヒータ(GGH)の2つの熱交換器が設置されている。低低温EPは排ガスの流れ方向に対し3つの室から構成されており、それぞれ1S、2S、3S と呼ぶことにする。1Sでは流入したフライアッシュの約85wt%が、2Sでは約10wt%が、3Sでは約5wt%が集塵される。微粉炭燃焼で発生する粒子は、低低温EPで集塵されるフライアッシュのほか、ボイラ底部から排出されるボトムアッシュ、ボイラ出口ホッパーから排出されるフライアッシュ、排ガス再循環ラインに設置されたマルチサイクロンで収集されるフライアッシュがある。
サンプリングは定常状態とコンタミネーションの防止に留意し、これらすべての粒子について行った。すなわち、100%負荷のもと、給炭量やNOx濃度、SO2濃度がほぼ一定となったところを燃焼の定常状態とみなし、その48時間後、コンタミネーションのない粒子とみなしてサンプリングを行った。
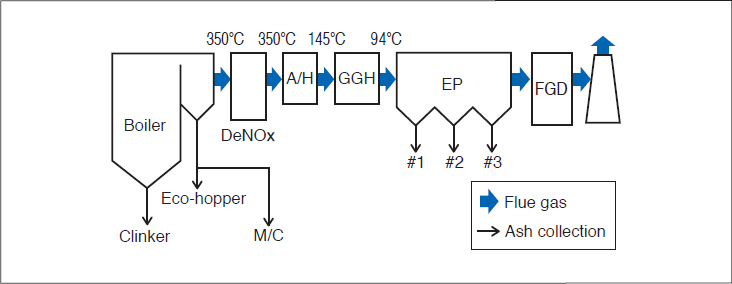
Fig.1 : Configuration of the plant and ash collection points
試料のサンプリングを行った微粉炭火力プラントの構成と100%負荷での平均的な排ガス温度を示す。
試料の分析
Table 1に試料分析の一例を示す。原炭および1S-3Sのフライアッシュについて、Table 1に示す項目について分析を行った。フライアッシュの平均粒径は、1Sから3Sに向かって小さくなることが特徴的である。また、灰組成変化の観点では、CaOは1Sから3Sに向かって少なくなる傾向およびSO3は逆に多くなる傾向が見られる。
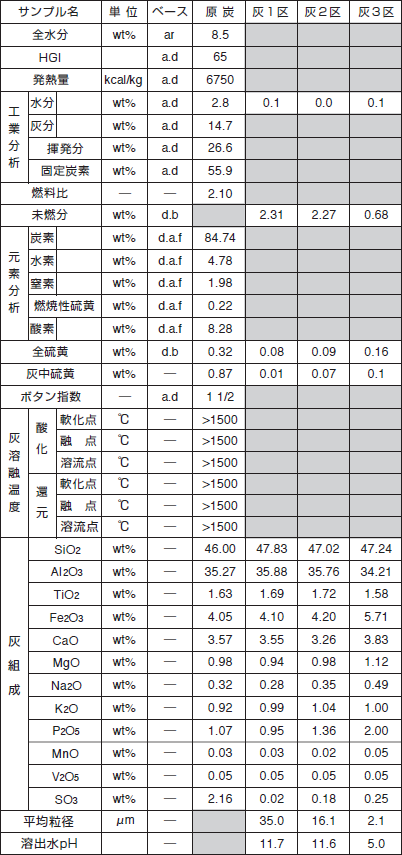
Table1 : 原炭性状とフライアッシュの性状
溶出試験
試料1.0g前後を入れた栓付き試験管に蒸留水10mℓを加え、200rpm、30分間、振とう機にかけた。溶出試験後の試料は減圧ろ過器で回収し、組成分析のために107 °Cで乾燥した。
14炭種の1S、2S、3Sのフライアッシュについて溶出試験を行ない、溶出液のpHを測定した。また溶出前後の灰組成をXRFにより分析した。
結果および考察
集塵室別B/A 比の変化
B/A比は、灰成分のうち塩基性成分と酸性成分の比を意味し(次式)、Table 1に示した灰組成分析結果を用いて計算した。
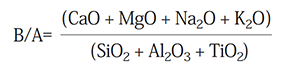
多くの炭種で1Sから3Sに向かってB/A比は小さくなった。これは主にCaOの含有率減少の影響によるものである。このようなB/A比の変化は、溶出液pHに直接影響を及ぼすものと考えられる。
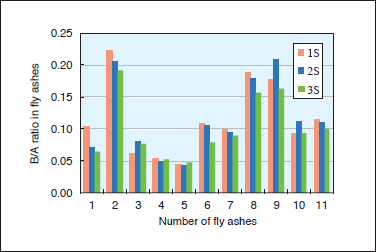
Fig.2 : Variation in B/A ratio for different fly ashes collected at 1S, 2S, and 3S.
11炭種のフライアッシュについて1S、2S、3S のB/A比の変化を示す。
炭種および集塵室別のpH変化
溶出液のpHは炭種により大きく異なり、1Sの溶出液pHは7.32~13.02の範囲にあった。全体的な傾向として、1Sから3Sに向かって溶出液pHは低くなる傾向にあるが、1Sの溶出液pHが12以上の場合、2S、3SのpH変化は小さくなる。
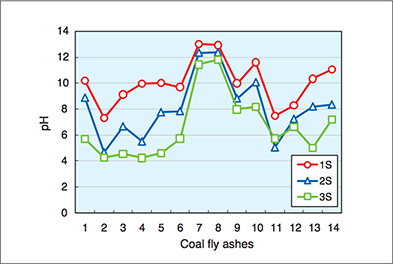
Fig.3 : Variation in pH for different fly ashes collected at 1S, 2S, and 3S
14炭種のフライアッシュ(1S~3S)について溶出試験を行い、その溶出液pHを調べた結果である。
溶出前後の灰組成変化とpH
溶出液pHを支配する灰組成を特性化するために、溶出前後の灰組成変化(Table 1に示した組成)を比較した。
明らかにCaOは溶出試験後多くの炭種で減少しており、CaOが溶出液pHに大きく影響していることがわかる。この他、アルカリ土類金属(Mg,Na)の溶出も少し認められたが、CaOの溶出に比較するとごくわずかなレベルであった。一方、酸性成分ではSO3の溶出が顕著であった。
以上の結果から、溶出液pHはB/A比あるいはCa+Sが影響するものと考えられる。
B/A比が低い炭種ほどpHが低くなる傾向が見られるが、各室で比較すると同じB/A比でもpHは大きく異なり、一般的な整理は困難である。
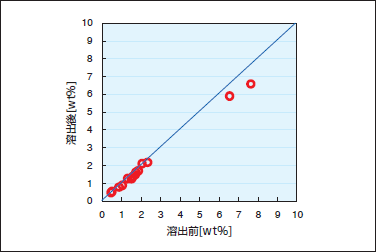
Fig.4 : Comparison of CaO content before and after leaching.
フライアッシュ中CaOの含有量を溶出前と溶出後で比較した図である。
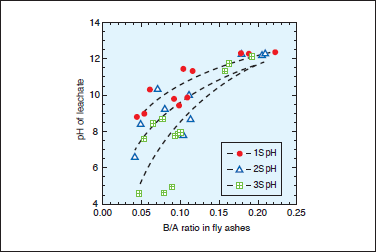
Fig.5 : Effect of B/A ratio on pH of leachate for 1S, 2S, and 3S.
14炭種について、B/A比と溶出液pHの関係を1S、2S、3S各々についてプロットした図である。
溶出液pHの支配因子
溶出前後の灰組成成分の測定と比較から、主要な溶出成分は、どの炭種についてもCa2+とSO42-であることがわかった。そこで、溶出液はCa(OH)2とH2SO4の混合液であると仮定してpHを計算した。
計算値と測定値は概ね傾向が一致し、Ca/SO4モル比が溶出液pHの主な支配因子であることが明らかとなった。
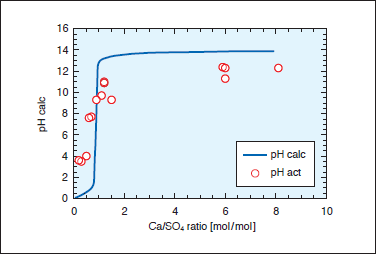
Fig.6 : Comparison between actual pH and calculated pH.
溶出前フライアッシュのCa/SO4モル比から計算したpH(実線)と実測値を比較した図である。
結言
微粉炭燃焼火力発電プラントから採取されたフライアッシュの溶出液pHを決定する因子を探索した。溶出液pHは炭種によって大きく異なり、1Sから3Sにかけて溶出液pHは小さくなった。溶出前後の灰組成成分の測定との比較から、主要な溶出成分はCa2+とSO42-であることがわかった。Ca/SO4モル比が溶出液pHの主な支配因子であることが明らかとなった。
微粉炭火力発電
プロセスシミュレーターの開発
針金祐一, 神原信志, 守富寛
緒言
我が国においては、種々のエネルギー源の確保は重要な課題であり、今後も石炭火力の担う役割は重要である。昨今、原油のみならず石炭も需給が逼迫しており、将来は炭種を問わず、高効率かつクリーンに利用できる技術が求められる。石炭は炭種によって含有成分が異なるため、経済性と環境保全を両立するには、それぞれの炭種に適した運転条件を的確に設定する必要がある。さらには、過去に使用実績のない炭種を検討していくことも予想される。そこで、炭種の影響、経済性および環境性能を考慮した石炭火力発電プロセスシミュレーターの開発が望まれている。
本研究では、汎用のプロセスシミュレーター「Aspen Plus」をベースとして微粉炭燃焼システムを構築し、石炭の性状から、その影響を予測する微粉炭火力発電プロセスシミュレーターを開発したので報告する。
プロセスの構築
石炭は1~5cmの粒径で微粉炭機に供給され、平均粒径60µm程度の微粉炭に粉砕される。この後、予熱された空気とともにボイラーに供給され燃焼する。燃焼熱は表1に示す蒸気に変換され、3機の蒸気タービンにより再熱再生方式で発電される。
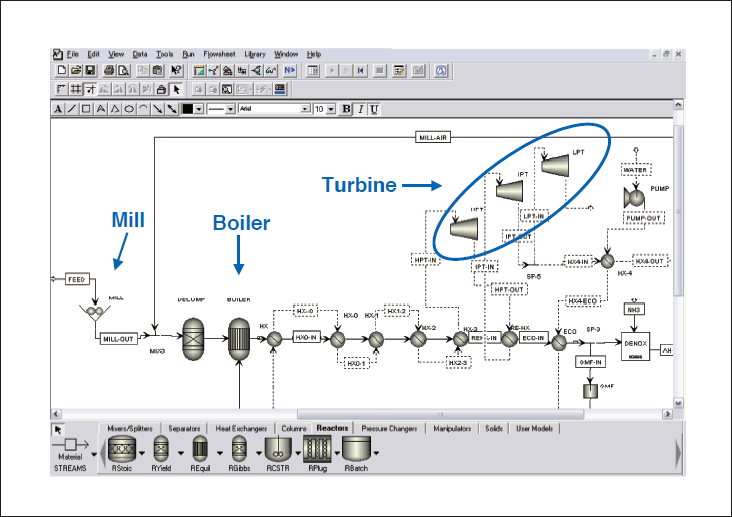
図1. 微粉炭火力プロセス構築画面
Aspen Plusを用いて構築したプロセスを示す。
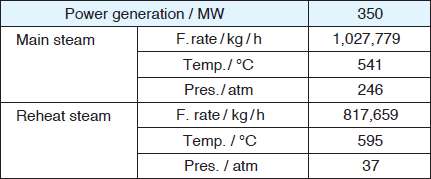
表1 運転条件
計算方法
入力条件
今回想定したプラントは発電量350MWの発電プラントである。入力値は主に石炭の性状から工業分析値、元素分析値、灰組成、HGIおよび発熱量、実機データから石炭給炭量、燃焼用空気流量、外気温度、蒸気条件等とし、A~Cの3炭種(表2)について計算を行った。
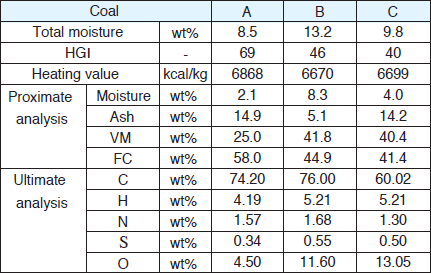
表2 石炭性状分析値
予測式の導入
プロセスに及ぼす種々の影響を予測するため、シミュレーター内に石炭の性状からの予測式を組み込んだ。これにより微粉炭機動力、未燃分、NOx 濃度、電気集塵機動力の簡易予測が可能となる。
評価方法
実際の微粉炭火力において、微粉炭機と送風機(PAF、FDF、IDF、GMF)および電気集塵機の所要動力はプラント所内動力の約9割を占める。ここでは、これらの合計を所内動力として定義した。本研究では、炭種別の発電効率を計算し、実機データとの比較することで計算精度の評価を行う。発電効率は以下の式で求めた。

結果と考察
NOx濃度
シミュレーター内に組み込んだNOx濃度予測式より、3炭種それぞれを燃焼させたときに生じるNOx量が計算された。NOx濃度の計算値は実測値よりも低い値となるが、概ね予測できていることが確認された(図2)。
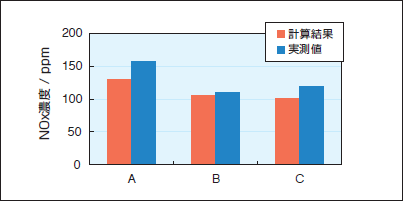
図2. 節炭器出口NOx濃度比較
所内動力計算結果
微粉炭機、送風機、電気集塵機の所要動力を計算した。
図3より、PAFの所要動力は予測できていることがわかる。その他の送風機や微粉炭機、電気集塵機についても同様の結果を示した。
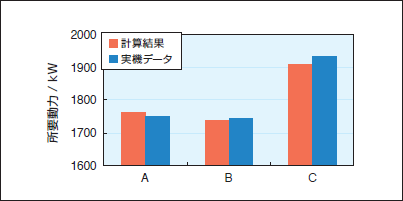
図3. PAF 所要動力比較
動力計算結果の例として、一次空気を送るPAFの所要動力計算値と実機データとを比較したものを示す。
発電効率
図4から計算結果は3炭種とも発電効率がやや高くなる傾向があるが、炭種の傾向を含めて精度良く計算できていることがわかる。計算結果の発電効率が高い値を示す理由としては、水系統のポンプ設備などの所要動力が考慮されていない部分があるためであり、今後の課題である。
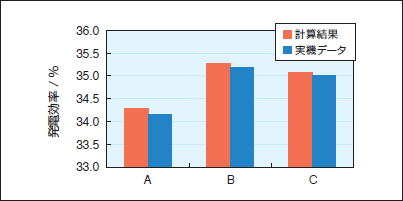
図4. 発電効率比較
3炭種についての発電効率の計算結果と実機データとの比較を示す。
結言
石炭の性状からそれらの影響を予測することは、既存の予測式をシミュレーター内に組み込むことにより可能となった。また、プラントの運転に要する所内動力の計算を含め、炭種ごとの発電効率を求めることも可能となった。
大気圧プラズマよりも優れた脱硝法の開発
ウシオのエキシマランプを用いて
中小規模の燃焼設備では、これまで、窒素酸化物(NOx)の排出濃度の規制はなかったが、昨今の環境問題に対する意識の高まりから、地域協定等によって規制されはじめている。
事業用や産業用の大規模燃焼設備では、燃焼制御や排煙脱硝装置(SCR)でNOxを除去する方法が一般に採用されている。しかし、中小規模の焼却設備では、設置スペースや設備コストの面から、この方法は実用的ではなく、小型で安価な脱硝装置の開発が強く望まれているのが実情である。
守富・神原・隈部研究室の神原先生は、これまでラジカル連鎖反応を利用したラジカルインジェクション脱硝法の開発を行ってきた。ラジカルインジェクション脱硝法とは、NH3ガスを大気圧アルゴンプラズマに通過させることでNOxの除去に効果的なアンモニアラジカル(NHi)を生成させ、それを燃焼排ガスに吹き込むことにより、無触媒で高効率に脱硝を行う方法である。従来のプラズマ利用脱硝装置のように排ガス全体を励起するのではなく、脱硝剤のみを励起するため、電力消費量が極めて少なくなる。加えて、装置が小型で単純なこと、冷却水を必要としないことなどの利点を有する。
この開発過程で、先生は、大気圧アルゴンプラズマにアンモニアを通過させると、NH、NH2、Nといった活性化学種以外にもN2H2、N2H4といった準安定化学種が生成することを確認した。そこで、それらが温度場でNHiラジカルを生成し、脱硝反応に少なからず寄与しているという推論に立ち、何らかの手段でN2 H2、N2H4といった準安定化学種を生成できれば、大気圧プラズマを用いるよりも安価でエネルギー効率の高い脱硝法が開発できると考えた。
「アンモニアガスの光吸収係数は160-210nmの間で大きく変化します。従って、この波長域をもつ光をアンモニアガスに照射すれば、アンモニアは励起、改質され、N2H2、N2H4を生成する可能性があります。160-210nmの光源としては、エキシマランプ(172nm:真空紫外光)や低圧水銀ランプ(185、254nm:遠紫外光)がありますが、この研究※では、ウシオ電機さんが提案された出力の大きいエキシマランプを用いました。エキシマランプが放つ172nm真空紫外光でアンモニアガスを励起、改質し、それを模擬排ガスに吹き込んだ時の脱硝特性を調べました。その結果、励起、改質したアンモニアガスは、熱的脱硝法よりも低温で脱硝効果があり、かつ脱硝率は非常に高くなることが判明しました。また、大気圧プラズマを用いたラジカルインジェクション法の脱硝率と比較しても、700°C以上ではほぼ同等の特性を示しました」(神原先生)
ラジカルインジェクション脱硝法は固定排出源のNO除去に実用性はあるが、低電圧(低消費電力)でプラズマを生成させるために、アンモニア希釈ガスとしてアルゴンを使用する。このことから、車両や船舶等の移動体の脱硝装置として適用するには難しいとされている。神原先生は、アンモニアラジカル生成方法を大気圧プラズマから真空紫外光(VUV)に変えることで、希釈ガスを窒素とすることを検討した。
「希釈ガスを窒素にできれば、移動体の脱硝装置として適用できるうえ、より安価に脱硝を行うことが可能となります。この研究※3では、エキシマランプの真空紫外光でアンモニアガスを励起し、それを模擬排ガスに混合した時の脱硝率に及ぼす反応温度、酸素濃度、NH3/NOモル比、ガス滞留時間の影響を実験的に調べました。その実験過程でVUV励起アンモニア脱硝法を開発し、結果、脱硝性能はラジカルインジェクション法よりわずかに劣る程度でした。この方法は、希釈ガスに窒素を用いることが可能であり、より低コストの脱硝法である、と言えるのではないでしょうか」(神原先生)

▲エキシマランプで励起したアンモニアによる同時脱硫脱硝法の開発
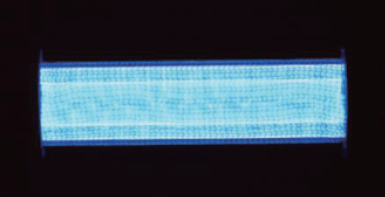
▲172nm 真空紫外光を放つ誘電体バリア放電のエキシマランプ(ウシオ電機製)
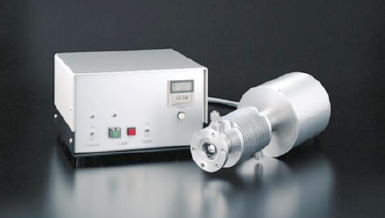
▲ ヘッドオン型の実験用エキシマ光照射ユニット(ウシオ電機製)
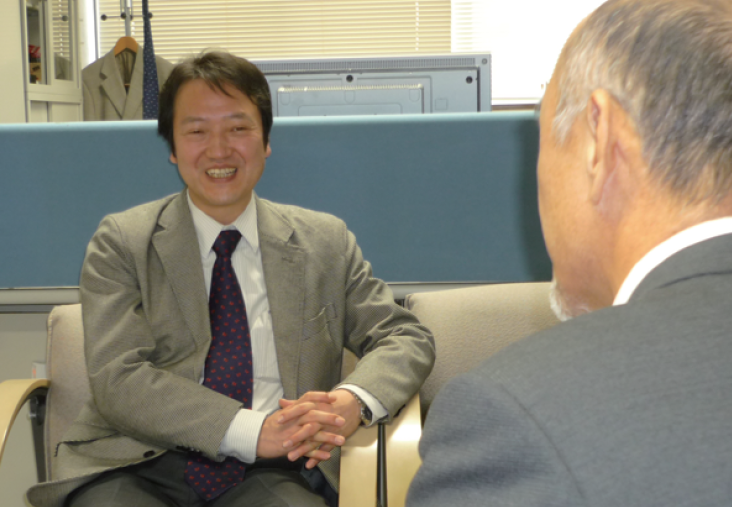
▲エキシマランプを用いた研究成果を説明する神原先生(手前は弊社の菱沼上席研究員)
プロフィール
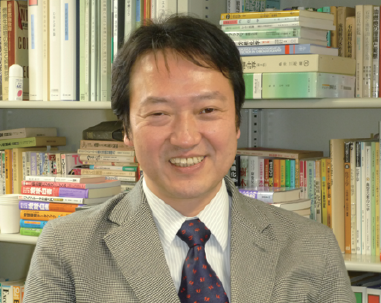
神原 信志 ( かんばら しんじ)
岐阜大学 准教授
大学院工学研究科
環境エネルギーシステム専攻(独立専攻)
兼 工学部 応用化学科
- ■学位
- 1986年 工学修士(群馬大学) 「流動層からの粒子の飛び出しに関する研究」
1993年 博士(工学) 群馬大学 「石炭燃焼におけるNOx 生成機構とその抑制技術に関する研究」 - ■職歴
- 1986年 出光興産(株) 新燃料部新燃料研究室
1988年 同 新燃料部石炭研究所
1990年 群馬大学 大学院生産工学専攻博士後期課程入学
1993年 同課程修了 博士(工学)
2002年 弘前大学 理学部知能機械システム工学科非常勤講師
2003年 出光興産(株)退職 岐阜大学 助教授 現在に至る - ■受賞学術賞
- 1993年 日本燃焼学会研究奨励賞
1996年 日刊工業新聞社・環境庁環境優良賞
1998年 日本エネルギー学会進歩賞(技術)
2002年 日本燃焼学会技術賞
2005年 The Best Paper Award of Advanced Gas Cleaning (Hosokawa Award)
2008年 小野木科学技術振興財団最優秀賞 - ■所属学会
- 化学工学会
日本エネルギー学会
日本燃焼学会
日本分析化学会
電気学会
火力原子力発電技術協会
日本機械学会 - ■勤務先住所
- 岐阜大学大学院工学研究科 環境エネルギーシステム専攻
〒501-1193 岐阜県岐阜市柳戸1番1(居室:工学部C棟7階716-3号室)