光技術情報誌「ライトエッジ」No.23
特集 ウシオの露光装置
(2001年11月)
5. ウシオの「光」装置開発の歴史
5.1 はじめに
ウシオの露光装置の歴史は、お客様にランプをより効率よく使っていただくために、光のアウトプット開発から始まった。しかし現在では、ランプと並ぶ重要な柱として、ウシオを支える事業の一つに成長してきている。前章までに述べられてきた露光のさまざまな技術が、どのようにして築かれてきたのかを知っていただくことにより、ウシオのチャレンジ精神、開発にかける意気込み、そして露光技術がどのようにして育まれてきたかをご理解いただきたい。
ウシオの技術は、前身の牛尾工業株式会社電機事業部門で開発された、ジルコンランプやクセノンランプが登場する1955年(昭和30年)頃から急速に磨かれていく。それまで生産していた白熱電球の技術を生かせる部分はわずかで、焼結や陰極活性化等の陰極処理技術をはじめ、ほとんどの技術は未経験という状況の中で開発したのである。
しかし、新しい特殊なランプは用途が限られ、拡販に苦労したようである。そこで、ランプを売るための方策として、照射装置のようなランプ応用製品を開発することとなった。クセノンランプは当初顕微鏡用光源としての用途しかなかった。しかし垂直点灯方式により、映画館で使用されるようになったが、効率や作業性に問題があった。そこでランプハウスに組み込んだ水平点灯式の開発へと至った。また、ジルコンランプは学校の教材用として販売するため、照射装置に組み込んで販売した。小型のクセノンランプも同様に照射装置に組み込まれた。これがUI灯具である。一方、水銀ランプも複写機用として、ランプのみ生産していた。超高圧水銀ランプは1959年に完成し、電磁オシログラフや、蛍光顕微鏡用光源として使用された。また、ジルコンランプと同様に、照射装置にも組み込まれた。後にこの照射装置が半導体の研究をしていたメーカで使われるようになった。
ウシオ電機がウシオ工業(牛尾工業を社名変更)から分離独立した1964年には、集積回路の研究が盛んになっており、まもなく日本のメーカでも生産が始まった。それに伴い、世界初の投影方式のIC焼付装置を開発した。この開発も、数µの位置合わせや高性能レンズの知識などはほとんどなく、ゼロからの出発であった。それまで密着式で行われていた露光では、マスクやウエハに傷が付きやすいという欠点があったが、投影方式によってこれらの問題が解決した。
これら光学機器の開発においては、光測定器が欠かせない。最初は輸入販売も兼ね、輸入した測定器を使用していたが、もっと良いものが欲しいという思いから、自社で開発することになった。以来、数々の測定器を開発している。1965年にはクセノンランプを用いてソーラシミュレータを開発した。その後何件かの実績を経て、宇宙開発事業団の筑波宇宙センタに社運をかけたソーラシミュレータを完成させた。1974年には紫外線硬化型の印刷インク乾燥用のユニキュア装置を完成させた。その後、照射面積を小さくして、紫外線硬化型の接着剤への照射用としたスポットキュアも登場した。登場時は直接照射する方式だったが、現在ではファイバによって光を導くことができるようになっている。レーザ分野では、1962年にレーザ励起用のストロボランプが開発され、1969年に大阪大学よりレーザによる核融合の研究への協力要請を受け、翌年には科学技術庁から「核融合プラズマ生成用高出力レーザの研究開発」の委託研究を受けている。これら大型レーザの開発からレーザマーカへと発展していった。
ハードニング装置や、周辺露光装置は半導体製造工程の中で、歩留まり向上のために求められた装置で、その技術は現在の露光装置全般に生かされているといってよい。露光技術に限らず、搬送、制御など幅広く受け継がれている。
半導体ステッパ用照明ユニットは、ステッパに搭載される照明ユニットのことで、シリコンウエハの露光面に一定の光を照射する。現在でも弊社露光装置に搭載されている。この照明ユニットを、色々な目的に使用できるようにし、規格化することによって安価に提供できるようにしたものが、マルチライトである。そしてこのマルチライトがその性能のよさによって、他社の独占市場だったTAB露光装置の市場を、ウシオの独占市場に変えることとなったのである。その後も、露光装置に関連したユーザの相談を営業マンと技術者が検討し、蓄積した技術を背景に実現していくということが繰り返された結果、現在のウシオの露光装置のラインナップは、非常に幅広いものとなっている。
ウシオの歴史に刻まれた、露光装置の歴史を知っていただくことによって、ウシオの持つチャレンジ精神と技術力がどうやって育まれてきたかを、本章から感じ取っていただければ幸いである。
(志賀浩之)
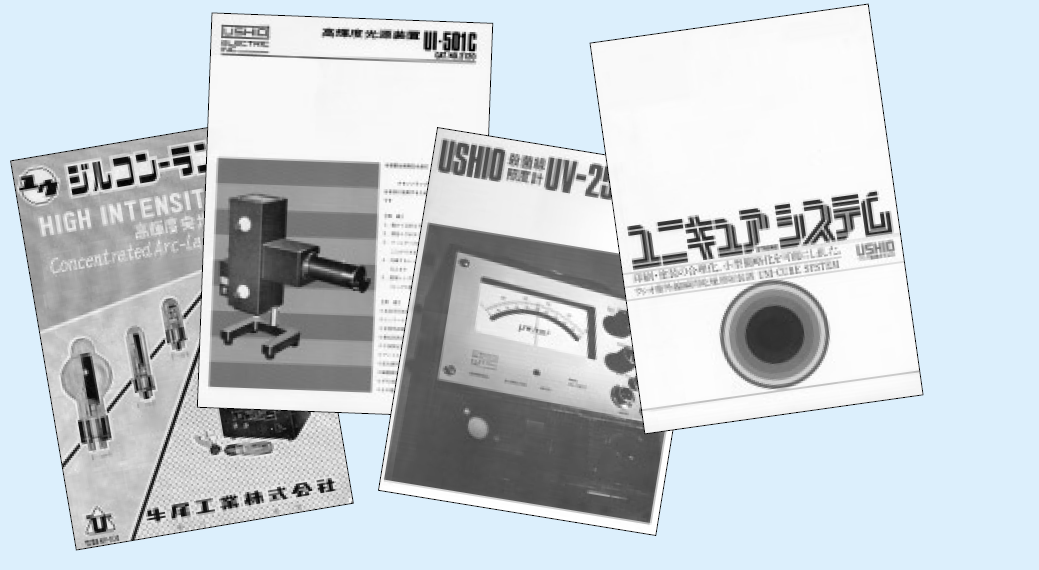
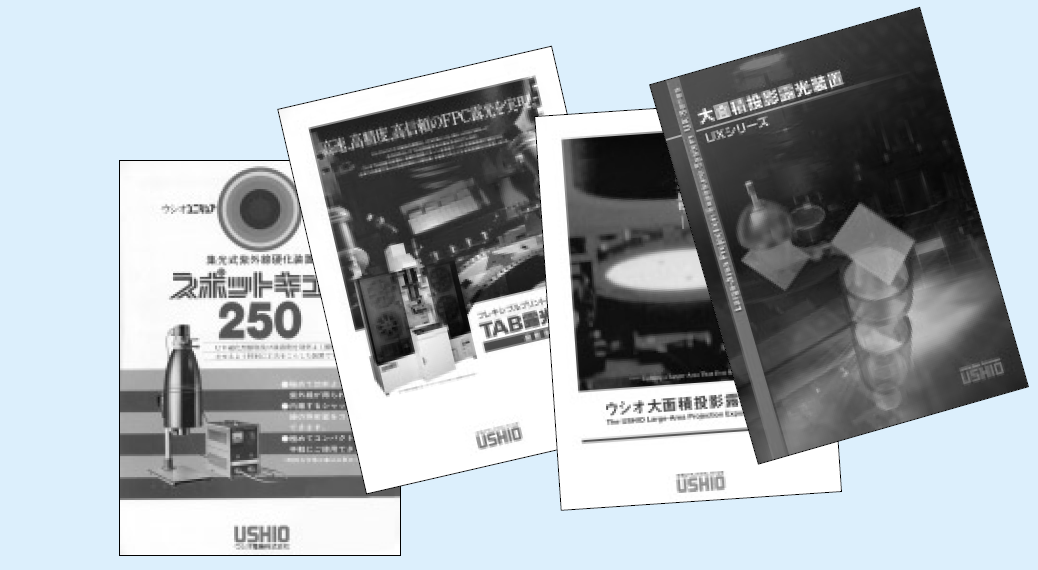
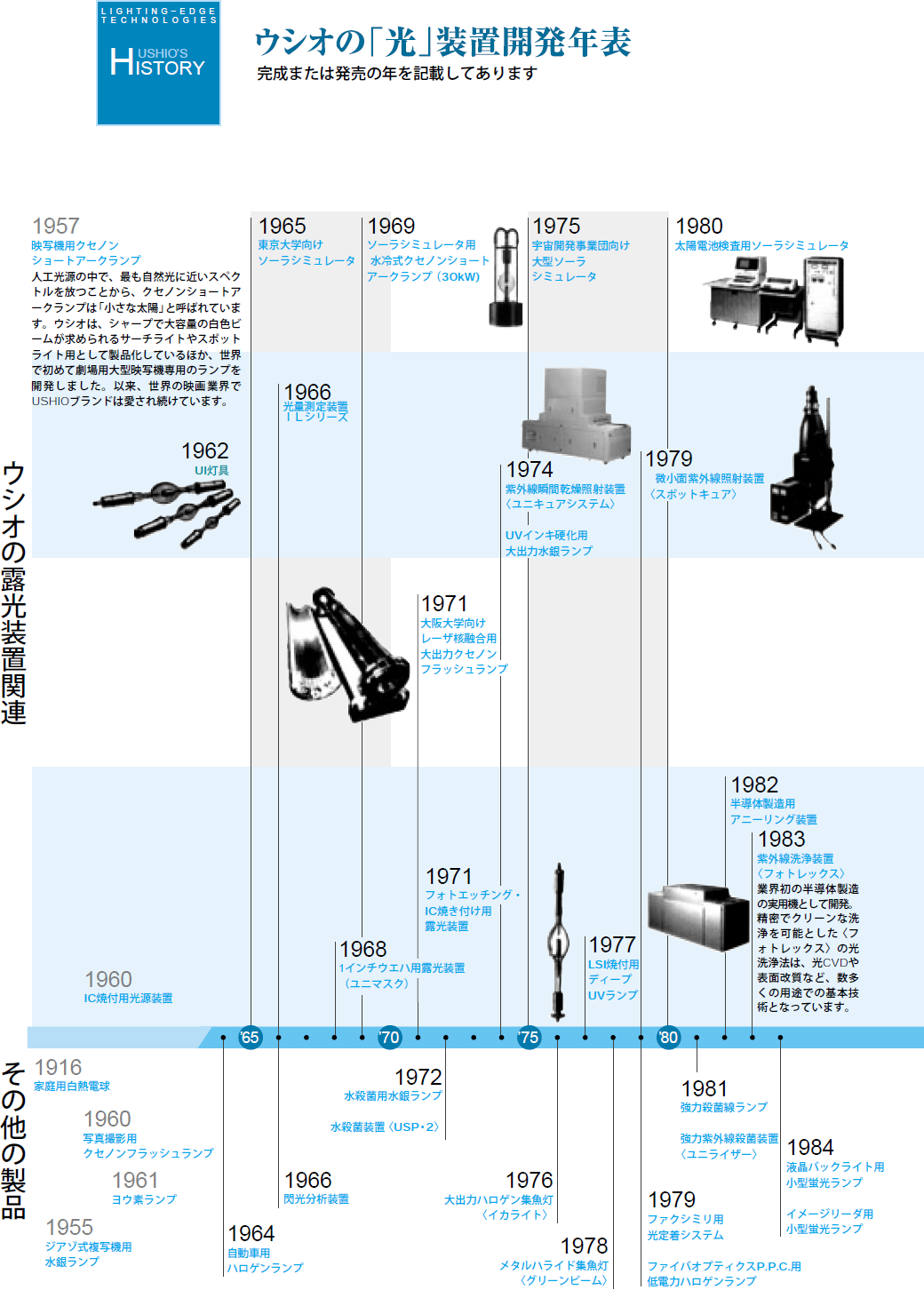
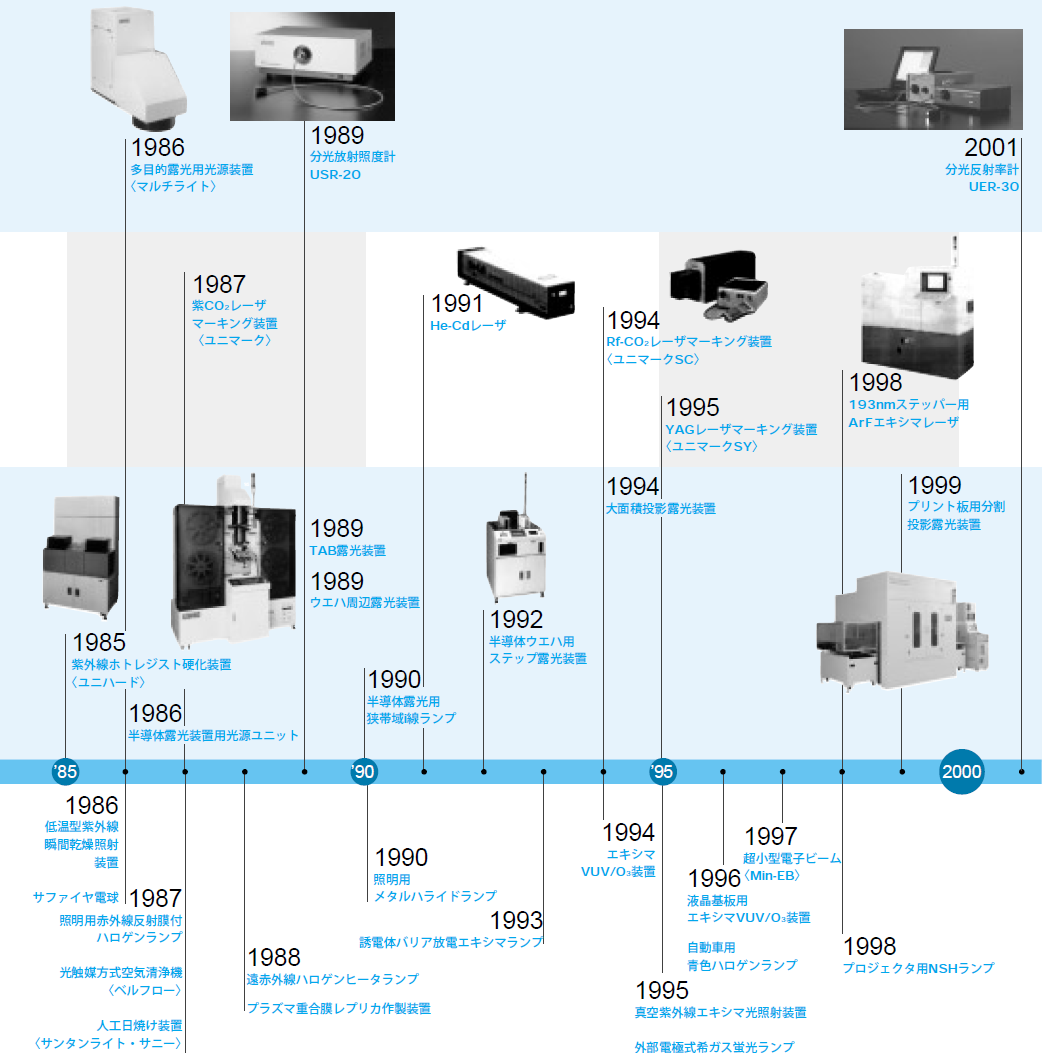
5.2 露光装置開発前史
5.2.1 映写機用ランプハウス
(1)クセノンランプハウス
1958年(昭和33年)10月23日、新宿のターミナルセンターに新しく建設された松竹会館の映画館で、クセノンランプを使用した映写テストが行われた。これは、ウシオが日本で初めてクセノンランプを開発し、映画用光源として利用するために、株式会社小糸製作所、株式会社三社電機製作所、日本音響精機株式会社(ジーベックスの前身)と合同で開発を進めていたものである。
この時代はカーボンアーク灯による上映が全盛期であった。しかしカーボンアーク灯は、常に人が付いてカーボンを交換したり、フィルムが止まって燃えたりしないように気を付けなければいけなかった。そこに取り扱いやすいクセノンランプが登場したのである。もちろん垂直点灯方式で、ランプハウスにセットするときは光軸がずれないよう注意しなければならなかった。
(2)水平点灯方式クセノンランプハウス開発のきっかけ
映画館用のクセノン光源は、1958年に商品化され、その後次々と大型クセノンランプが開発・実用化された。もともと照明用として開発されたもので、管球の角度が±15度の範囲とされており、全てが垂直点灯方式であった。このランプは、1966年には約1350~1400館まで普及した。当時のランプハウスの光学設計は、各社それぞれの特徴を活かし、垂直点灯(図5-1)方式、垂直点灯(図5-2)方式であった。そこに(3)で後述する、新しく開発された水平点灯(図5-3)方式が浸透していくこととなる。いずれもクセノン独自の輝度分布を活かした方法である。
垂直点灯の焦点・照度の調整は非常に難しく、普通の映写技士では100%の明るさを引き出すような調整が困難で、専門家の調整を必要とした。一方、使用者は経費削減等で100%の明るさにできないまま、使用しているのが実状であった。
1966年6月、ウシオ電機(株)の全額出資で日本ジーベックスが発足した。そして映画館の補充用ランプの販売、映写システム機器の技術メンテナンスを主体に営業を始めた。日本ジーベックスでは「クセノンランプの補充以外に商品がない。T社、V社に対抗するには、彼らより一歩も二歩も進んだ光源装置が必要である。技術で勝つしか道はない」と考え、最善の方法を模索した結果、次で述べるような技術的確信があることから、水平点灯ランプハウスを開発・商品化することになった。
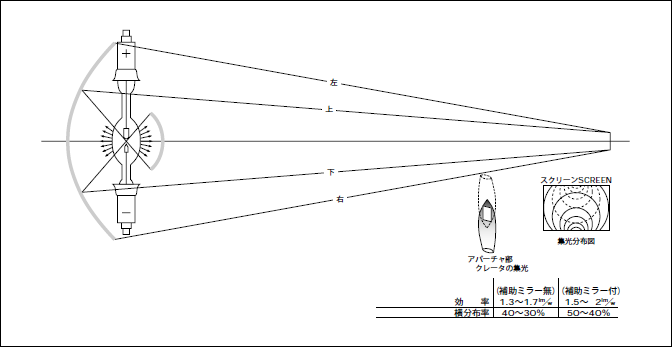
図5-1 垂直点灯(標準ミラー)方式
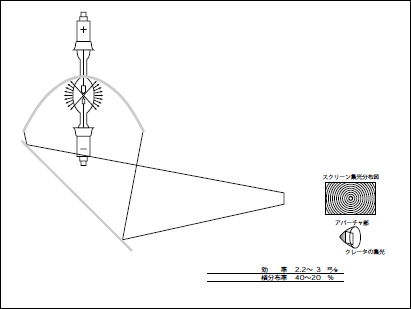
図5-2 垂直点灯(吊鐘ミラー)方式
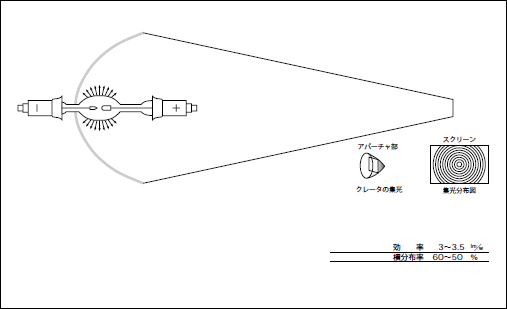
図5-3 水平点灯(深型ミラー)方式
(3)水平点灯ランプハウス開発にあたって
画期的な技術として、水平点灯ランプハウスの開発が以下のように検討された。
①ランプの封止部の温度について
白熱電球、放電ランプとも封止部の温度が一定の規定温度以下に保持されれば安全である。キセノンランプの管壁温度は、アークの輻射熱とキセノンガスの対流によって決まる。キセノンアークの温度は10,000°C近くもある。輻射熱は距離の2乗に反比例し、温度の4乗に比例するから、管壁温度の上昇は輻射熱によるものと考えてよい。しかし、水平点灯方式はアーク位置が中心の正常位置に保持されることが保証されない。その時管壁温度は安全温度に保証されないことがあった。従ってアークの位置をなんらかの方法でランプの中心位置に保持できれば、水平点灯も垂直点灯も何ら変わらない温度となるはずである。アークに磁石を近づけると、磁石の方にアークが引っ張られることもわかっていたので、水平点灯して磁石を適当な位置に調整して決めることによって、アークを正常位置に保持できるようにした。また封止部の温度は適当な冷却機構を考えれば、垂直点灯方式より、素晴らしく効率が上がることになった。
②輝度分布について
水平点灯の場合、深型の反射ミラーが使用できるので、集光効率は非常に良くなる。また、陰極を深型ミラー側に持ってくることにより、アークの最高輝度の点が有効に利用でき、垂直方式に比べて輝度分布が素晴らしく向上した。
③ミラーについて
垂直点灯方式で効率を上げようとすると、大きな直径の反射ミラーが必要となり、当然ミラー自体の価格も高くなる。(図5-1、図5-2)
以上の観点から水平点灯ランプハウスの開発は垂直点灯方式に比べて、大きなメリットがあり、技術的にも対応可能であるとの判断がくだされた。
(4)水平点灯方式クセノンランプハウスの誕生
このようにして35mm映画用水平ランプハウス1kWを開発・商品化することとなった。そしてついに1966年12月、試作1号をOS劇場株式会社の協力で、神戸スカイシネマに設置した。35mm映画として商業興行劇場での初めての実験を行い、性能検査では図6-4のような予想以上の結果を得ることができた。
横分布・隅分布を50と30程度にすると、中心照度は2000lxに上昇する。最大スクリーン光束3500lm、発光効率4.2l/Wとなり、従来の垂直2000型(2kW)ランプハウスの性能以上の効果が得られた。引き続き2kWの水平ランプハウスの開発に入り、1967年2月にはテアトル銀座に設置し、好評を博した。そしてクセノンランプの水平点灯について、寿命や安全性、スクリーン上での輝度照度分布も良好であることが、業界にも認識されるようになった。1967年のSMPTE journalには、新製品として弊社の水平点灯方式が紹介され、それ以降世界中にクセノンランプの水平点灯が広がっていった。
以上のようにクセノンランプの水平点灯に関しては、ウシオが世界のパイオニアとなったわけで、誇りを持っている。現在、映画スクリーン数は2600~2700と推定されるが、約80%が水平点灯方式と思われる。この、パイオイニア精神と、光学設計のノウハウがUI灯具やその後の露光装置への足がかりになったのではないだろうか。
(太田良雄 株式会社ジーベックス)
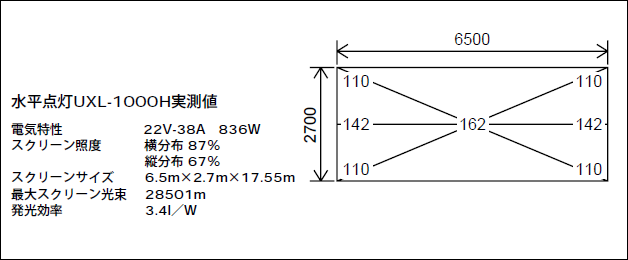
図5-4 水平点灯方式実験結果
5.2.2 UI 灯具
UI灯具とは、『ランプのウシオ』から、『ランプ・応用装置のウシオ』へと発展した歴史の上で、まさに分岐点に位置する製品で、露光装置の基礎ともなった。さらに、日本の初期の半導体研究には大きく貢献した装置である。
UI灯具の『UI』とは「Ushio Illumination」の略で、高輝度光源装置のことである。
その歴史は、ランプを販売するためのアイディアから始まった。1955年(昭和30年)、クセノンショートアークランプとジルコンランプが完成。ジルコンランプとは陰極タンタルパイプ中にジルコンを入れ、放電させることで点光源を得るランプであった。ただし、放電により生じたプラズマから放射される光を利用するランプではなく、放電によって白熱された金属ジルコニウムから放射される光を利用するランプである。輝度が6000~7000cd/cm2、色温度は3200Kで、主にシュリーレン装置用光源として利用された。レンズの検査用、ガラスの脈検査用としてそれらの分野の主立ったメーカで採用されていたが、それ以外の用途開拓は進まなかった。
そんな折り、ジルコンランプが高校の理科実験教材用として役立つことがわかった。しかし、学校で使うにはランプだけでは使い勝手が悪い。そこで、灯具を開発することになった。そして、1961年、ジルコンランプが理科教育設備基準品目に入った。これは、学校が設備基準品目から設備を購入した場合、政府から補助金がでるため、非常に導入しやすくなったということである。それまでにも、簡単な灯具はあったが、本格的に灯具に力を入れ始めたのは、これが最初だった。
翌年には、この時の灯具を設計し直して、クセノンランプや、超高圧水銀ランプを搭載した、高輝度光源装置UI灯具を発売した。これがUI灯具UIシリーズの始まりである。UI-100、UI-150、UI-500の3種類で、ランプはクセノンランプ75W、150W、500W、超高圧水銀ランプ100W、200Wであった。用途としては各種測定用光源が想定された。
この頃、日本でも半導体の研究が盛んになってきた。この半導体の研究・製造にはリソグラフィ技術が用いられた。しかし、露光装置のメーカは存在せず、それらは輸入品に頼っていた。光源としては1961年に開発された、超高圧水銀ランプ200Wが外国製露光装置の交換用ランプとして組み込まれる一方、UI灯具の高輝度平行光がリソグラフィ技術に最適であるため、研究室に浸透していった。
1964年3月にウシオ工業の電機部門からウシオ電機が独立。
1966年にUI-501シリーズが発売され、光を利用した物理・化学の基礎研究の必需品として重宝された。UI-501シリーズはクセノンランプや超高圧水銀ランプなどの点光源を用い、光学系はコンデンサレンズ、バックミラーで集光しコリメータレンズでΦ50mmの平行光線を得ていた。同年、半導体製造工程のフォトエッチング用ランプハウスを開発し、輸入露光装置の光源パワーアップ用として活用された。
更に翌1967年、ユニアーク250が、IC焼き付け用、光化学実験、ソーラシミュレータ、植物育成実験用として開発された。Φ60~120mm、照度100,000~400,000lx、照度均一度90%というスペックだった。これが翌年開発された、世界初の投影露光装置「ユニマスク」や、現在も活躍するスポットUV照射装置「スポットキュア」、露光装置用光源ユニット「マルチライト」へと発展していった。
一方、UI灯具も各種研究用として人気があり、類似品で1972年にフォトエッチングやIC焼き付け用の露光装置UIV-270が発売された。さらに、1977年にはウエーハ露光用ランプハウスとしてUIS-500Cが仲間入りした。
このように、点光源と灯具の組合せであるUI灯具は、ウシオの露光装置参入のきっかけともなった製品である。
(取材協力:辻本浩司 ウシオ電機OB)
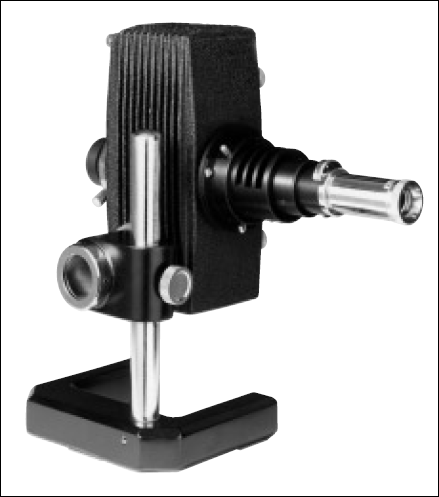
図5-5 UI-100
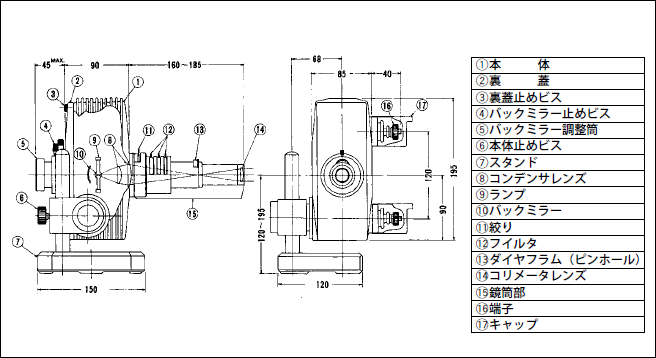
図5-6 UI-100の構成
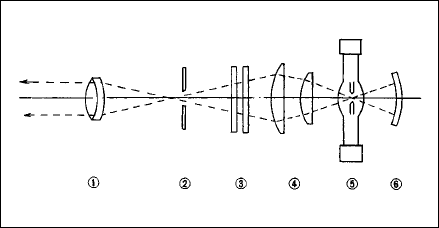
図5-7 UI-100の光学系
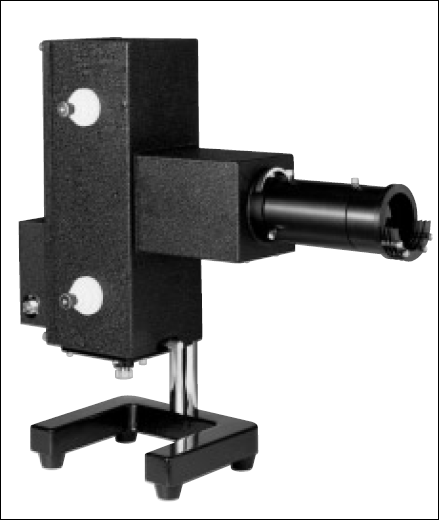
図5-8 UI-501C
5.2.3 投影レンズ式露光装置 ユニマスク
(1)はじめに
投影レンズ式露光装置とはICの製造工程の中のフォトエッチング工程で、フォトマスク(IC の図形)をシリコンウエハに投影レンズで焼き付ける装置である。
本装置が開発されたのは1968年だった。当時のウエハサイズは1~1.5inchで、IC図形の線幅は最小5~10µmであった。露光装置は密着式で、キャスパー、エレクトログラス、キュリック&ソファー社の密着式露光装置が主に使われていた。
密着式はフォトマスクとウエハの間隔を数十µm離してアライメントする。完了した時点で真空吸着で密着し、その後平行光で露光するシステムである。当然ながらマスクとウエハに傷が付きやすいので、マスクの消耗が激しく、またICの品質が低下する。
世界のすべての半導体メーカはこの問題を抱えていた。このようなことから非密着式が要望されていた。ウシオは露光装置の光源部を半導体メーカに納入していたので、非密着式の検討を依頼されたのである。
フォトマスクはIC原画をカメラで縮小撮影し製作されていたので、投影レンズ方式で実用できないかの検討をはじめ、1968年に世界で初めての投影式露光装置が完成した。
このことは岩井正和著「キヤノンスピリットの軌跡」(日本リクルートセンター出版部1981、p98)にも「この分野で先行していたのは、現実に商品化していた日本の中堅光学メーカーと光源メーカーのコンビだった。それとN 社と半導体のトップメーカーTI社、西独テレフンケン社とツアイス社の二つのコンビが開発中――と、これは実に豪華けんらんたる顔ぶれだった。」とある。
翌1969年2月にカリフォルニアで開催されたIC機器展示会「NEPCON SHOW」では関係業界から予想以上の注目を集め、テキサスインスツルメンツ社やウエスタンエレクトロニクス社などから注文をいただくことになった。
(2)装置の概要
図5-9に光学系を示す。光源部で楕円鏡を使用しているので、ランプは光軸上に置くことができるため、光源部、投影レンズ、顕微鏡などが同一ベンチ(柱)に取り付けてあり、芯出しのしやすい構造となっている。
①光源部
当時密着式の光源部は、超高圧水銀灯からの光束をバックミラーとコンデンサレンズで集光し、フィールドレンズで効率よくコリメータレンズに送り込み、コリメータレンズで平行光にするシステムであった。
投影レンズ方式にすると、レンズによる光の吸収、反射が大きく、特に紫外線の吸収が大きいため、より集光率の高い方式が必要になる。
ランプからの光束を楕円鏡で集光し、フィールドレンズで効率よくコンデンサレンズに送り込み、さらにコンデンサレンズはレンズ内で光束のロスが生じないように、投影レンズの入射瞳内に入射するように設計されている。これによって従来の倍の照度(30万lx)を得ることができたのである。
②投影レンズ
投影レンズは日本光学(現株式会社ニコンのリプロニッコールf=85mm、解像力は250本/mmであった。等倍レンズで一括投影方式だった。
我々はこのような高級レンズを扱ったことがなかったので、一抹の不安はあったが、光軸の芯出しを精度良く行い、ピントを合わすことができれば、うまくいくものと思っていた。
最初同じシリーズのリプロニッコールf=70mmを使ってみた。中心部の解像力は期待通りだったが、周辺部は落ちてしまった。調べてみると、これは収差の影響によるものとわかった。レンズの収差曲線がわからないとレンズを使いこなせないと考え、光学機関に測定を依頼したが断られた。物平面を非常に細かく分割し、そのすべての点からの光線の、レンズを通したときの像の状態を調べるのは非常に面倒で、難しいとのことだったのである。
f=70mmでいろいろやってみたが、周辺部の解像力を期待値まで上げることはできなかった。そこでf=85mmで試してみることにした。目視では収差が非常に少ないと思われ、周辺部も高解像力だった。そして実際に露光してみた。ところが現像してみると、フォトレジスト像はほとんど出てこなかった。
フォトレジストの処理(塗布、乾燥、現像、リンス)の悪さと思い、いろいろやってみたが、一向に良くならない。そのうちに露光波長(g線436nm)とアライメント光(可視光)の波長の違いによる色収差が原因であると気が付いた。アライメント光の結像面より100µm程度後側に結像していたのである。そこで丹念に調べていくうちに、g線と赤色光の結像位置が合致していることがわかった。実際に赤色光をアライメント光としてピントを合わせると、シャープなレジスト像を得ることができた。もちろんアライメントも可能となった。
さらにテストを繰り返し行い、レンズの最適絞り、芯出し精度、繰り返し位置合わせ等の検討を加え、最終的にΦ30mmのイメージフィールドで5µm、Φ40mmのイメージフィールドで8µm以内の解像力を得ることができたのである。
③アライメント部
粗アライメントはセンタースコープ(低倍率顕微鏡)を通して行い、精密なアライメントはサイドスコープ(高倍率顕微鏡)を通してマスク面に結像する像でアライメントを行う。サイドスコープはウエハ面両サイドの2点を分割視野で観察し、アライメントを行う。観察ポイントは移動できる構造となっている。
微調整テーブルはウエハを真空吸着し、X-YZ-θの可変が行えるようになっている。顕微鏡接眼部に赤色フィルタを貼りつけて、赤色光でアライメントを行う。露光フィルタ(g線)は光源部の出口に取り付け、紫外線カットフィルタ(シャッタ)はそのすぐ下に置かれ、タイマにより開閉できるようになっている。
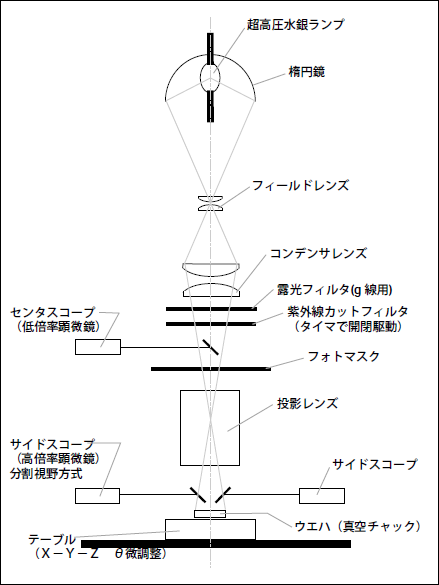
図5-9 光学系
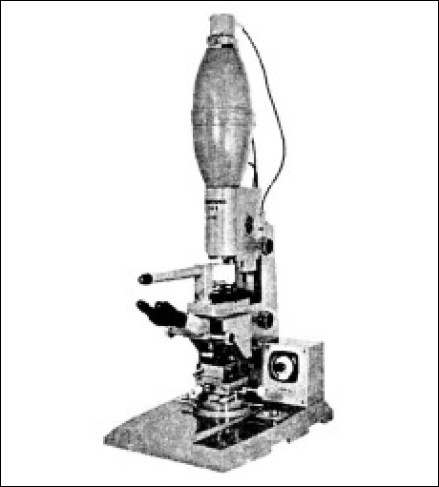
図5-10 ユニマスク101
(3)性能
解像力はΦ30mmイメージフィールドで5µm、Φ40mmイメージフィールドで8µm以内、焦点深度は±40µmであった。
位置合わせ精度は±3µm、露光時間は20~30秒であった。
(4)当時の課題
本装置の開発中はウエハサイズは1~1.5inchだったが、完成時には2inchのウエハが出始めており、2inch対応の投影式露光機が要求されるようになってきていた。しかしニコンのレンズでは露光エリアが大きくとれない。そんな折りキヤノンでは露光面積が大きく取れるレンズを開発し、2inchウエハに対応したのである。リプロニッコールf=170mmで試作的に検討してみたが、収差を少なくするためにレンズの枚数が多く、紫外線の吸収の点から実用的でないことがわかった。その上、今後ますますウエハのサイズが大きくなることが予想され、一括投影式での対応が難しく、今後どう対応していくかが課題となっていた。
またこの時の、投影レンズによって露光装置の性能が大きく左右されるという教訓から、最新の露光装置では自社開発した投影レンズを搭載することにつながっている。さらに高精度のテーブル移動、位置決め技術および顕微鏡の活用技術などのノウハウも蓄積され、微小寸法測定機やその後の露光装置へ活かされていった。
(守谷忠弘 ウシオ電機OB)
5.2.4 光測定器
(1)はじめに
産業界における紫外放射の利用は、露光(半導体1)、液晶、TAB、電子部品等)、印刷関係、UV硬化接着、光化学反応、紫外線殺菌といったように多種多様であり、各種の水銀ランプが使用されている。
紫外線放射照度の測定はこれらの産業で光をエネルギーとして利用する上で非常に重要である。
ウシオが最初に紫外線を測定するための光測定器を製品化したのは1970年のことであり、既に30年が経過している。ウシオが紫外放射を利用した装置を各種製品化していくうえで、光測定は非常に重要であり、それらの装置を活用するために、使いやすい測定装置がなかったのが光測定器開発のきっかけであった。現在ではウシオが露光装置を開発、製造、販売するうえで光測定器は非常に重要な役割を果たしている。
ここでは、光測定器の発展と現在の光測定器がどのようなものであるかを紹介する。
(2)当社における光測定器の開発
- 1966年・光量測定装置ILシリーズ(international light社製)販売
- 1970年・紫外線照度計UV- 365、UV- 400(シリコンフォトダイオード+色ガラスフィルタ、アナログ表示)開発
IC焼付装置、印刷用紫外線硬化システム等の放射照度管理用 - 1971年・殺菌線照度計UV- 2537(光電管式、アナログ表示)開発
殺菌灯の放射照度管理用 - 1976年・反射率計URE- 15(デジタル表示)開発
平面または曲面の反射率測定、平面鏡、楕円集光鏡、球面鏡用
・UIT- 100(アナログ表示)紫外線照度計、UVD- 365P、UVD- 405P(シリコンフォトダイオード+色ガラスフィルタ)受光器開発
UV- 365、UV- 400の後継機、表示部の共通化 - 1980年・UIT-110G(アナログ表示)殺菌線照度計、UVD- 254P受光器(光電管式)開発
UV-2537の後継機 - 1983年・UIT- 101(デジタル表示)紫外線照度計、UVD- 365PD、UVD- 405PD受光器開発
UIT- 100の後継機、表示部の小型化、デジタル表示、受光器感度入力により各種受光器で放射照度直読可能 - 1986年・UIT- 102(デジタル表示)紫外線積算光量計開発、受光器はUIT- 101用と共用
- 1989年・分光放射照度計(スペクトロラディオメータ)USR- 20販売
露光装置の分光分布測定、評価 - 1995年・UIT-150(デジタル式)紫外線照度計(積算光量測定可)およびUVD-S254、UVDC254、UVD-S365、UVD-C365、UVD-S405、UVD-C405の各受光器開発
機能のマルチ化:放射照度、積算光量、照度分布、温度測定に対応
各種受光器を取付けるだけで直読可、紫外線による感度劣化を従来品の1/10に改良
・分光放射照度計(スペクトロラディオメータ)USR-30開発
USR-20の後継機、小型、軽量化、Windows95対応 - 1997年・紫外線照度計用受光器の校正体系を変更
- 1999年・分光放射照度計(スペクトロラディオメータ)USR-40開発
USR-30の後継機、小型、軽量化、Windows98対応 - 2001年・分光反射率計UER-30開発
平面または曲面の分光反射率測定、分光透過率測定、楕円集光鏡、レンズの多層反射防止、大型フィルタ、大型ミラー用
(3)紫外線照度計
紫外線照度計UIT-150の外観図を図5-11に示す。受光器は水銀ランプの輝線波長に合わせて分光感度の違いによるものが3種類、さらに本体との一体型とセパレート型が有り、合わせて6種類ある。
一体型は印刷インキや塗料の乾燥用UVコンベアに流してピーク照度や照度分布を測定するのに適している。セパレート型は露光装置の放射照度を測定するのに適している。受光器の構造を図5-12に例として示す。受光素子にシリコンフォトダイオードを用い、色ガラスフィルタを組合せて水銀ランプの輝線波長が分光曲線のピーク付近になるようにしている。
図5-13に各種受光器の相対分光感度特性例を示す。受光器の校正は低圧水銀ランプの輝線、殺菌線(254nm)、または、超高圧水銀ランプの輝線、i線(365nm)、または、h線(405nm)の単色光で行っている。図5-14に一体型とセパレート型の入射角度特性を示す。理想状態はコサインカーブであるが、紫外線測定用受光器では完全に一致させることは難しい。しかし紫外用としてはかなり良い特性となっていることがわかる。同一タイプの受光器でも、分光感度特性の差が測定値バラツキの原因となる。校正時と同じ単色光を測定する場合は問題無いが、実際は校正時の光以外の波長も含む状態で測定することになるので、分光感度の広い受光器の場合、超高圧水銀ランプの光を測定すると±5%の測定値バラツキを生じる場合がある。
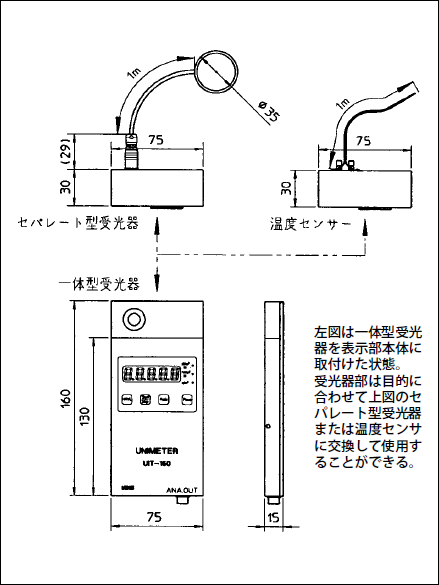
図5-11 紫外線照度計外観図(UIT-150)
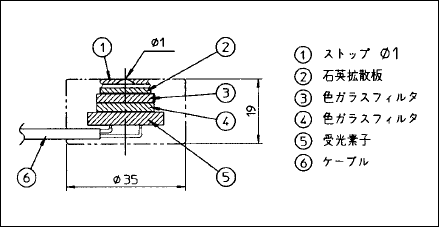
図5-12 受光器の構造(例)
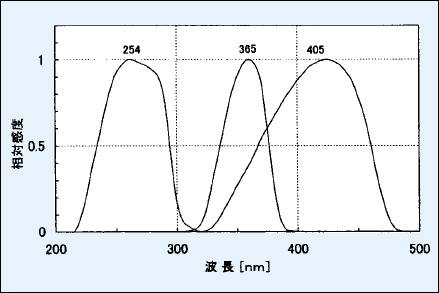
図5-13 各種受光器の相対分光感度
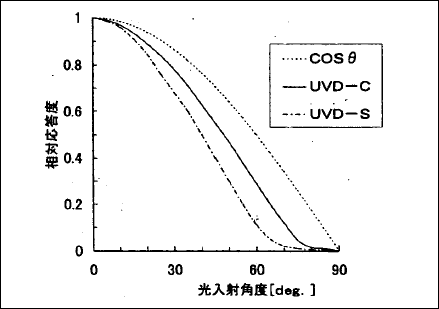
図5-14 受光器の入射角度特性
(4)分光放射照度計
前述の紫外線照度計が水銀ランプの輝線に合わせた分光感度特性を有するのに対し、波長毎に絶対放射照度の測定を実現したのが分光放射照度計である。従来の簡易的なものから、より高精度な光の測定、評価を可能としている。
測定原理の光学系を図5-15に示す。分光器に入るまでに、まず入射光学系が設けられている。入射光学系はミラーにより光路を折り曲げることもできるので、露光装置の露光面に設置した時に、上方より照射される紫外線を直接受けるのに都合がよい。また、減光フィルタを組込むことによって強い光に対しても測定が行なえるようになっている。光測定器として重要な特性である入射角度特性、受光位置、受光径は入射光学系により決まるため、絶対値測定を行なう上で重要な部分である。
次にライトガイドファイバが光を分光器のスリットに導く。ファイバは光学繊維束で構成され、短波長域まで透過性の優れた石英ガラス製である。これを用いると任意の位置、方向に入射光学系の受光位置をセットできるため、測定が容易に行える。分光器中のグレーティングは、スリットを通った光を分光しラインセンサ上に導く光学部品である。ラインセンサは入射した光の強さに比例した電気信号を出力する素子が1024個並んでいる。電気系を図5-16に示す。
ラインセンサはD1~D1024、C1~C1024、各々1024個のリセットスイッチと切換スイッチを持つ。D1~D1024は入射光の強さに比例した電流I1~I1024を発生する。C1~C1024の電圧をリセットより一定時間T msec後に読むよう、リセットスイッチと切換スイッチを駆動する。T msecの間C1~C1024はI1~I1024の電流で充電される。
1駆動は最小20msec、最大20000msecの間で選択可。読み出されたC1~C1024の電圧はプリアンプを経由しサンプルアンドホールド回路に電圧として記憶される。サンプルアンドホールド回路は高速で1024個の電圧値をアナログ的に記憶する。この電圧はIT/Cに比例し、入射光の強さに比例する。
なお、I、Cのチャンネル毎の固体差は分光放射照度標準電球により補正(校正)される。サンプルアンドホールド回路に記憶された電圧はゆっくりと読み出され、A/Dコンバータを経由してコンピュータに取り込まれる。なお、更にS/N改善のためこのサイクルを何回も行い平均値を測定結果とするサンプリング数の指定が可能(1~99回)。0点補正を行うためシャッタ機構により被測定光をカットして測定する機能と、光学フィルタにより迷光を除去する機能を備えている。
ラインセンサを使用しているため、定常光、交流点灯光だけでなく、フラッシュ光の分光分布測定も可能。
測定結果はリアルタイムでノートパソコンの画面上に表示する。波長範囲を任意に設定するとその範囲の積算値を表示できるので、必要波長域での放射照度を求めることができる。露光装置等の分光放射照度の測定、管理に使用されているが、測定データはExcel上で処理、解析することができ、紫外放射を利用する広い用途で、どの波長が影響しているか調査、研究するのに適している。
ウシオの分光放射照度計USR-40の外観図を図5-17に、仕様を表5-1に、露光装置の光を測定した例を図5-18に示す。
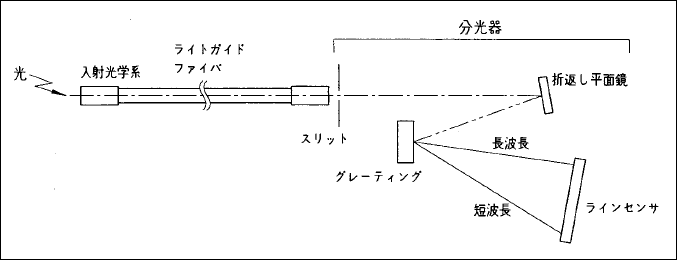
図5-15 分光放射照度計の光学系
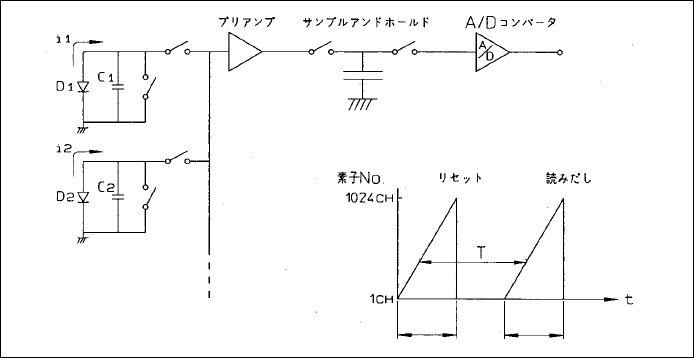
図5-16 分光放射照度計の電気系
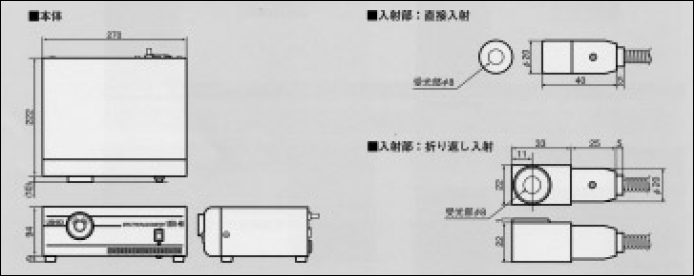
図5-17 分光放射照度計外観図
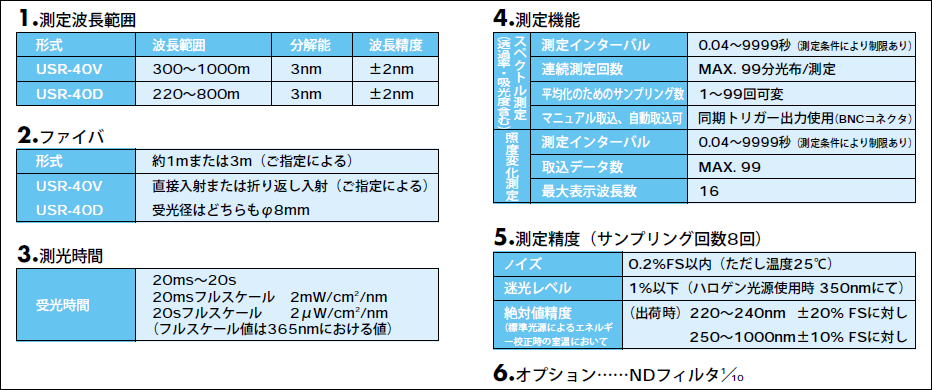
表5-1 分光放射照度計の仕様

図5-18 露光装置の分光分布
(5)まとめ
露光用途を中心に光測定器についてまとめた。露光装置には放射照度を管理するためのモニタ受光器が光学系の途中に設けられており、積算光量制御を行うセンサとして使用されている。モニタ受光器の出力値に応じてシャッタの駆動機構を制御し、設定した積算露光量を照射できるしくみになっている。また、1日1回程度、紫外線照度計により、露光面における放射照度、及び露光面内の放射照度分布が測定され、露光装置の放射照度管理に使用されている。また、定期的に積算光量制御用モニタ受光器を校正するのに用いられる。
露光装置の光学系では露光に必要のない波長の光は、光学系に配置される多層膜蒸着されたミラー、フィルタによりカットされる。短波長のDeep UVをカットしたり、バンドパスフィルタにより、単色光を露光に使ったりしている。これら波長毎の放射照度測定、解析に分光放射照度計は有効である。
(大澤理)
5.2.5 ソーラシミュレータ
(1)はじめに
ソーラシミュレータは、ウシオにとって歴史的かつ代表的な光源装置である。ウシオは古くからクセノンランプを開発し提供してきたが、当初の開発の理由は「分光分布が太陽光に似ているから」であったという。その目的に最もかなった光源装置がここで紹介するソーラシミュレータ(模擬太陽光発生装置)である。ソーラシミュレータは、人工衛星の熱真空試験において、疑似太陽光として用いるために開発された。人工衛星は、ロケット打ち上げ時の音響・振動に始まり、大気圏外での公転軌道上でも、さまざまな過酷な環境にさらされる。その環境試験のひとつが、宇宙における熱と真空環境についての信頼性試験を行う熱真空試験である。宇宙空間において人工衛星は、太陽光や、アルベド(地球等からの輻射)を受けて加熱される一方、その裏側の陰になった部分は、ほとんど輻射熱の入射がない。また、さらに宇宙空間は真空であるために、地上では常に発生しているガス対流による熱の移動がないという環境にさらされる。
このような、宇宙での熱真空環境を提供するのが、スペースチェンバと呼ばれる熱真空試験設備であり、ソーラシミュレータはその中で真空・極低温を提供する設備とともに、疑似太陽光を提供する設備として用いられている。また近年、ソーラシミュレータは、太陽光発電用の太陽電池評価用光源としても使用されるようになった。さらに、太陽光を模擬するために培われた照明光学技術は、今回のテーマである露光装置において、現在でも応用され、生きている。
(2)ソーラシミュレータの歴史
ソーラシミュレータは、1959年ごろからアメリカにおいてNASAを中心として開発が始まり、アメリカの宇宙関連機関に、各種のソーラシミュレータが建設された。なかでも最大規模のものはJPL(ジェット推進研究所、Pasadena,Calif.)に建設された直径4.5mのソーラビームを照射できるもので、光源として20kWクセノンランプを37灯使用しているものである。
日本では1965年頃から東京大学宇宙航空研究所(現文部科学省宇宙科学研究所)、郵政省電波研究所(宇宙開発事業団が業務継承)をはじめ、宇宙関連企業でもソーラシミュレータによる熱真空試験が行われていた。
当時は、最も大型のものでもソーラビーム直径が0.8mのものであり、6.5kWクセノンランプを3灯使用していた。当時ウシオ電機では、将来、大型化やハイパワー化を要求されるであろうソーラシミュレータやアークイメージング炉への応用を目的に、高輝度大出力光源を開発しており、1969年に、世界最大級の30kWクセノンショートアークランプを完成させた。1970年には、そのランプを光源とした、1灯式でソーラビーム直径1mのソーラシミュレータを、当時の東大宇宙航空研究所に納入した。
一方、宇宙開発事業団は、筑波研究学園都市に筑波宇宙センタを開設したのを機に、前述のアメリカJPLのものと同規模の大型スペースチェンバを建設する計画を立てた。
ウシオもこの計画に参加し、1975年に前記の30kWクセノンランプを19灯使用した、ビーム直径4mのソーラシミュレータを完成した。最大放射照度は2s.c.(Solar Constant:地球付近の放射照度を1とする単位)が得られた。(設備の概要を図5-19に示す。)
また、この14年後の1989年には人工衛星の大型化に対応して、1号機と同じ19灯式ではあるが新しく開発された水平点灯型の30kWクセノンショートアークランプを採用した、ビーム直径6mのソーラシミュレータが同宇宙センタ内に建設された。筑波宇宙センタでは現在、ウシオも参加して完成後26年を経た第1号機を2002年7月完成を目標に改修しており、完成すれば2機の大型スペースチェンバが人工衛星の熱真空試験に供されることになる。
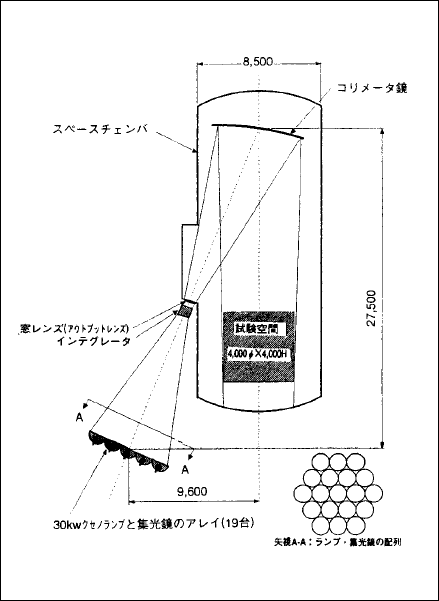
図5-19 宇宙開発事業団大型スペースチェンバー用大型ソーラシミュレータの概要
(3)ソーラシミュレータに要求される仕様
ソーラシミュレータに要求される性能は、太陽光とできるだけ同質の光を供給することである。地球を周回する人工衛星の試験を目的とする場合、模擬太陽光は地球付近の太陽光の特性を備えていなければならない。それらの特性には、下記のようなものがある。
- ①放射照度:1.4kW/m2
- ②放射照度均一度:均一
- ③サブテンス角(コリメーション角):±16min(全角32min)
- ④分光分布:Jonson Curve、Nicolet Curve等
- ⑤放射照度安定度:均一
- ⑥輻射による相互作用:なし
ソーラシミュレータは、これらの特性をなるべく忠実にシミュレーションする機能を備えれば良いのであるが、技術的な困難さや、試験体の形状、熱試験という目的などから、実用的な仕様は通常下記に示す通りである。
- ①放射照度:1.4kW/m2
- ②放射照度均一度:±5%以内
- ③サブテンス角:±1.5deg
- ④分光分布:クセノンランプ放電スペクトルまたは AM-0近似
- ⑤放射照度安定度:±1.5%/h
なお、スペースチェンバ内における輻射の相互作用の防止対策としては、
- ①コリメータ鏡⇔試験体間:コリメータ鏡を-100°C程度に冷却し、さらにBlack Space Condition(注1)を満足する範囲を試験空間とする。
- ②スペースチェンバ内壁⇔試験体間:内壁を極低温(約100K)に冷却した黒色のシュラウドで囲む。
等の手段を講じている。
(注1):試験体からの反射光や輻射が、コリメータ鏡で反射した後、試験体に再入射しないという条件。その条件を満足する空間は幾何光学的に決められる。(図5-20)
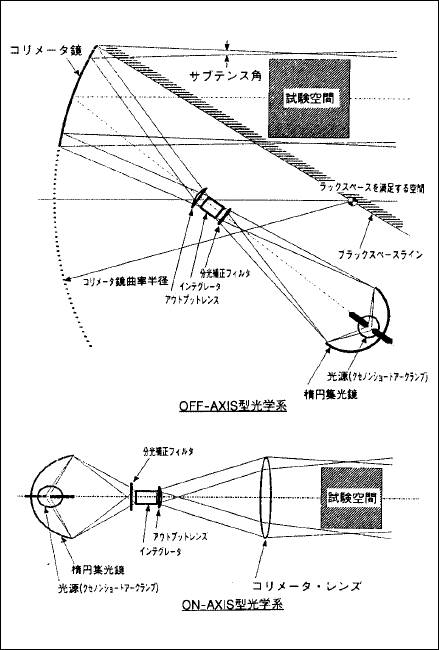
図5-20 ソーラシミュレータの基本光学系
(4)ソーラシミュレータの光学系
ソーラシミュレータの標準的な光学系を図5-20に示す。光学系の構成は基本的に
- ①光源
- ②集光鏡
- ③インテグレータ
- ④分光補正フィルタ
- ⑤コリメータ
である。
①光源
ソーラシミュレータの光源としては、ほとんどの場合、クセノンショートアークランプが使用されている。理由は、
- ・800nm付近の赤外部に大きなピークがある他は、太陽光の分光分布に近似
- ・高輝度
- ・アークが安定
- ・動作範囲が広い
- ・長寿命
などが挙げられる。
現在最も大型の光源は前述の30kWクセノンランプである。このランプの最大の特徴は、電極が大電流に耐えるように、電極の内部が冷却効率の良いフィン構造を形成しており、純水で水冷されている点である。おもな性能は下記のとおりである。
- 定格入力:30kW
- 定格電流:660A DC
- 定格電圧:45V DC
- 電極間隔:12.5mm
- 発光効率:50%
- 冷却水流量:900 l/h(純水)
②集光鏡
ランプの配光分布がランプ軸に対して対称であることから、その光を効率良く集光するために、回転楕円面のミラーを集光鏡として用いる。集光鏡とランプの軸を共有して配置し、ランプアークは集光鏡の第1焦点に置き、光を第2焦点に集光する。
③インテグレータ
太陽光の重要な特徴のひとつである均一な放射照度を得るために、このインテグレータが用いられる。インテグレータは石英ガラスで作られ、複眼レンズ構造をした、コンデンサレンズ素子群とプロジェクションレンズ素子群が対向して配置されている。インテグレータの機能は、集光鏡によってコンデンサレンズ素子群上に集光された光を、それぞれ対向するプロジェクションレンズ素子によってコリメータ上に投影するものである。投影された各々の光の放射照度分布は光軸に対称であるため、照射面(コリメータ鏡上)で積分された放射照度の分布は均一となる。(図5-21参照)
④分光補正フィルタ
クセノンランプの分光分布はその可視光部分では太陽光と良く一致しているが、波長800nm付近では非常に強いエネルギーがある。おもにこの部分を補正し、大気圏外の太陽光分光分布に近似させるのが、この分光補正フィルタである。
⑤コリメータ
コリメータはインテグレータから照射された発散光を太陽光のような平行光に変換するものであり、レンズを用いる場合と凹面鏡を用いる場合がある。OFF-AXIS型光学系は凹面鏡を用い、ON-AXIS型光学系はレンズを用いている。(図5-20参照)
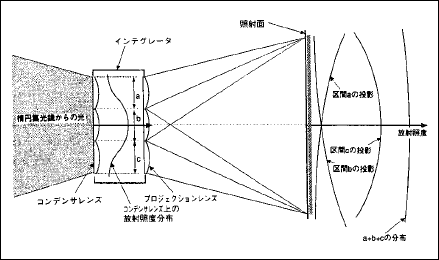
図5-21 インテグレータによる放射照度分布改善の原理図
(5)まとめ
ソーラシミュレータでは、点光源から発した光を、所定の面に均一照射する光に変換する照明光学技術や、放射照度を安定に保つ技術は不可欠なノウハウである。また同時に、ソーラシミュレータに使用される大出力ランプは、熱工学的には非常に大きな熱源であり、熱的、機械的にデリケートな光学部品を同じランプハウス内に共存させる熱設計上の技術もまた重要なノウハウである。露光装置に搭載されている照明系にも、過去から培ってきたこれらのノウハウが継承されている。
(堀口友四郎)
5.2.6 ユニキュア
(1)開発の背景
印刷インキの乾燥は主に溶剤の蒸発、印刷物へのしみ込みと酸化重合によっている。米国で有機溶剤の排出を規制する法律ができたことにより、溶剤を含んだ印刷インキに代わる速乾性のインキが必要となり、紫外線で硬化するインキが開発された。最も手頃な紫外線の発生源として、高圧水銀ランプが使用されることになったが、当時のランプは発光管に保護用の外管を取付した、二重管方式のいわゆるコピー用水銀ランプであった。ランプの放電長さ1cm当りの電気入力は精々15W(15W/cmと言う)程度しかなかったため、高出力のランプの開発が必要となり、世界各地で高出力の高圧水銀ランプの開発が行われた。
その結果、発光管のみの一重管方式でランプ入力80W/cmの高圧水銀ランプが印刷インキ硬化用として標準的に使用されることとなった。
(2)高出力水銀ランプの開発
紫外線硬化型のインキに紫外線が照射されると、インキに含まれている感光性樹脂が活性化され、分子量の小さい樹脂(粘性が低い)に架橋反応や重合反応などを起こさせて、高分子化することにより粘性が高くなって硬化が起こる。一連の反応は一般的に短時間で終了するため、硬化時間を左右するのは反応速度ではなく、反応の総量、すなわち紫外線のドーズ量である。
印刷の高速化に対応するため、硬化時間の一層の短縮が求められており、大量の紫外線が必要となっていた。出力の低いランプを多数並べてもドーズ量を確保することは可能であるが、印刷機への取付スペースの関係で、できる限りランプ本数を減らすことが必要であった。ウシオでは、ランプ発光管の直接強制空冷を行なうノウハウを使用した灯具を作り、他社の2倍の高入力(160W/cm)のランプを使ったユニキュアシステムを実用化した。これはランプと装置を別々のものとしないで、一体物として開発を進めた成果である。
高圧水銀ランプは発光管の内部に水銀を封入してアーク放電を起こし、放電の発熱により、水銀を蒸発させている。発光管内の水銀圧力により、出てくる紫外線の波長と量は大きく変化するので、発光管内部の水銀圧力をほぼ一定に保つことが必要である。
液体の水銀が存在する状態では、管内の最低温度(最冷点温度)の変化によって水銀の圧力は飽和蒸気圧曲線にしたがって大きく変化するので最冷点温度を一定に保つことが必要になるが、これは至難の業である。液体の水銀が存在しない状態では、圧力変化は、ガスの熱膨張が主体であるため、圧力変化は穏やかで許容される最冷点温度の範囲は格段に広くなる。
開発のポイントはランプの温度分布とその制御であった。自然対流による冷却では80W/cm入力の場合、発光管の高温部は約800°C、低温部は約400°Cとなり、高温部でも発光管の材質の使用限度内であり、低温部は水銀の完全蒸発に必要な温度になっている。しかし入力が80W/cmを超えるランプでは高温部が使用限界温度を超えてしまい、発光管の結晶化(白濁して失透する)や、発光管が軟化して変形する現象が発生するため、強制空冷が必要となる。
開発の初期段階では、高温部を冷却するために発光管上部に空気を吹き付けしたが、ランプを冷却した空気が印刷機の周辺に充満することになるので、印刷機が高温となり、印刷オペレータの作業環境もひどい状態となって、結局本格的実用化にいたらなかった。
発光管の中心部で放電により高温になったガスは対流により上昇し、発光管の上部を加熱するので上部は高温になる。ランプの上方から強制排気を行って空冷すると、風下側となる発光管上部には渦が発生し、流線が剥がれてしまい、発光管の上部は冷却できなくなってしまう。
更に、低温になっている発光管の下部は冷たい空気により直接冷却され、管の上部と下部で自然空冷以上の大きな温度差ができてしまう。また、表面直近の流速が早ければ良く冷却されることが分かっている。
これらのことからランプ上部の流れの剥離を防ぎ、かつランプ上部の流速をあげるための冷却風のガイドを設置することで、上部を重点的に冷却する事に成功した。この原理を利用して、現在は280W/cm入力のランプも実用化されている。
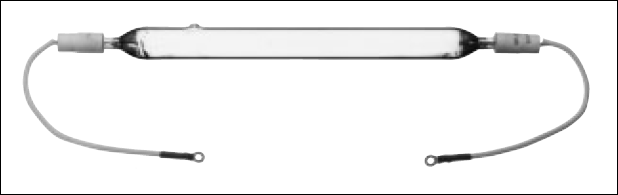
図5-22 ユニキュア用のランプ
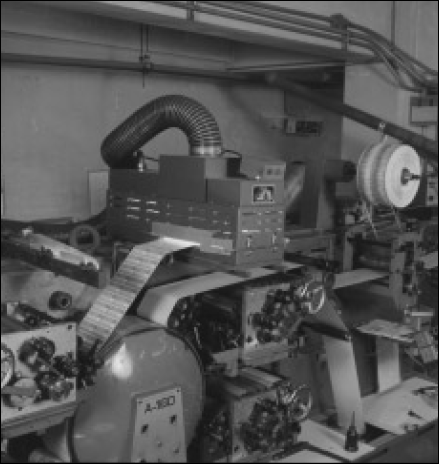
図5-23 シール印刷で活躍するユニキュア
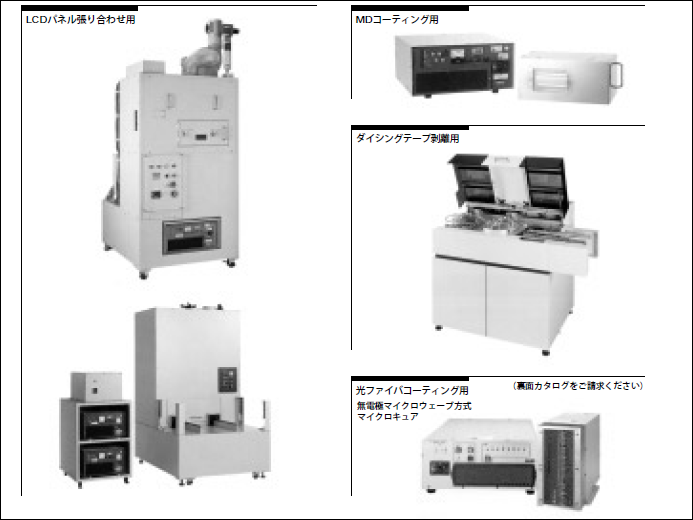
図5-24 ユニキュア応用例
(3)装置開発
ランプの温度が十分に高くなった状態では前述のような冷却が必要であるが、点灯初期の低温の時に冷却を行なうと、いつまでたってもランプのウオームアップが完了しないため、いわゆる過冷却の状態になってしまう。ランプのウオームアップに必要な時間は、夏と冬、朝と昼、など室温と装置の温度、ランプの形のバラツキ、電源電圧など種々の条件によって変動する。また、ランプの入力(W/cm)が大きくなるほど温度の上昇は急激になり、冷却開始のタイミングが重要となる。冷却を開始するタイミングを誤ると、ランプの温度が上がりすぎたり、過冷却になったりする。80W/cmを大幅に越える場合、タイマやサーモスタットによる冷却の起動ではバラツキを吸収できない。我々は、ランプ電圧が定められた値に達したことを検出して冷却を開始する方法を採用した。
停止した状態の紙や印刷機のドラムに、160W /cmのランプの光を当てると数秒間で焼け始める。焼損を防ぐためにランプの下にシャッタを設置し、印刷機の停止中とウオームアップ中はシャッタを閉めておくことが必要である。シャッタの熱負荷の低減と消費電力の削減のためシャッタを閉じているときは電力を下げておく。ユニキュアでは約65W/cmまで下げている。このときは当然、冷却風量も調整している。
ランプの冷却、ランプ電圧でウオームアップ完了を検出すること、シャッタ閉時のスタンバイ電力への切換と冷却風量を調整するという技術は、半導体業界向けのハードニング装置に応用されている。
(4)メタルハライドランプおよび瞬時点灯型ランプ
紫外線によって硬化開始するUV 硬化インキには顔料を入れて、各種の色を出している。顔料は紫外線を吸収したり、反射したりして、紫外線が塗膜の内部に深く入り込むのを阻害している。そのため特に黒色と白色の硬化速度が遅く、塗膜への浸透力の強い紫外線を多く出すことのできるランプの開発が必要となった。
金属を封入したランプによるインキの硬化実験の結果、数十種類の金属の中から鉄を入れることに決定したが、すでに競合他社が鉄を封入したランプを開発完了しており、特許も持っていたため、ランプと電源のセットで競合他社からOEMで供給を受けることにした。ランプは非常に安定しており、ランプ不良は0.1~0.2%程度で問題はほとんどなかった。同じランプを競合他社の装置用として市場に出したものは不良率が数十倍から百倍近い10%前後ということであった。これはランプを正しく使用することがきわめて重要であることを示している。
その後、自社小型の印刷、小物のUV硬化用として小型で安価なUVランプの要求が強くなってきた。そこでウオームアップ時間は160W/cmのランプで1分半程度必要であるが、製版用ユニパルスの技術を応用して数秒にまで短縮したランプを開発し、シャッタを使わなくてもすむラピッドキュアとして製品化した。
シャッタがないため灯具は小型化でき、制御も簡略化できたため装置価格が安くなり、紫外線を照射しない時は消灯するために、ランニングコストも安くなるなどのため好評で、主にシール印刷等に多数導入された。
(5)市場の状況
ユニキュアの販売を開始するまでは、ウシオの主要製品は、1本数百円~数千円程度のランプが中心であった。だから1台数百万円以上もするユニキュアの販売を行うには、販売戦略の根本的な見直しが必要であった。つまり、ユーザの開拓から始め、購入を決定できるキーマンへのアプローチ、予算取りへとつなげる。印刷業界は中小企業が多く、新しい技術を自社評価できないので、大手での実績がないと購入に踏み切れない。そのため、業界のトップユーザに製品を持ち込み、性能評価を受けなければならない。これがシステム事業部の装置販売展開への基礎となった。更に、エンドユーザ向けに保守部品の販売とアフターサービスが不可欠であったので、サービス部門を設置した。これらは以後の半導体業界向けの製品販売に向けての土台を作ることととなった。
小型のユニキュアは電子部品の接着やディスクの貼り合せ用にも導入されはじめ、印刷業界を中心とした販売から電子部品業界へのシフトが始まってきた。
(長谷川武彦 株式会社ユーアイエス)
5.2.7 スポットキュア
(1)はじめに
磁気ヘッドのフェライトを接着する目的で、ショートアークランプを使用したスポット照射装置を開発したのは1979年で、商品名スポットキュア(「スポットキュア、SPOTCURE」は当社の登録商標、1979年出願1983年登録)として販売している。それまでこのような商品は存在していなかったから、商品化したのはウシオが最初である。
初期のスポットキュア(以下、SPキュア)は、ショートアークの250W超高圧水銀ランプと楕円集光鏡を組合わせた簡単な光学系で、集光位置にワークを置き、紫外線硬化型接着剤で瞬間接着するものであった。今日のように光ファイバをライトガイドとして使ったものでは無かったが、当初より光ファイバで使いたいという要求も極めて少数ながらあり、光ファイバを取付けて使えるようにした特注タイプも存在していた。光ファイバがライトガイドとして本格的に使われだした1985年頃からは、光源部と電源部を一体化し、光ファイバで使うことを第一優先に設計した新機種(SP1)を開発、販売している。紫外線硬化型接着剤は生産工程を自動化する上で都合がよく、光ファイバで使い勝手が大幅に向上したことにより年々、需要が増加し今日に至っている。
(2)SP キュアの開発
- 1979年・スポットキュア250(250W超高圧水銀ランプ使用)開発
- 1986年・SP1(UIS-25102、主波長365nm)開発、光源部と電源部を一体化、光ファイバをライトガイドとして使うタイプ
- 1988年・SP1に、365nmタイプに加えて短波長(Deep UV)も照射するタイプを追加。紫外線硬化型接着剤の表面硬化性を改良
- 1990年・SP3開発、ランププリセット化(ランプ交換時の位置調整を不要とした)
- 1997年・高照度型石英ガラスファイバ採用
- 1998年・SP5開発、長寿命250WDeep UVランプの開発、メカ絞りによる0~100%の調光機能追加
- 1999年・光ファイバ用極細タイプレンズの開発
SPキュア関係の主な開発項目のみを上げた。ランプWの違うタイプや光源装置に対する光ファイバの取付け方向を変えたタイプ等、ユーザの使い勝手に合わせて実際はかなりのタイプが存在するが省略した。
(3)原理・構成
SPキュアの光学系を図5-25に示す。①250W Deep UVランプ(ランプの外観図を図5-26(a)に示す)のアークが②集光鏡(反射面が回転楕円面の一部より構成される)の第1焦点位置となるように配置され、アークより射出した光(配光特性を図5-26(b)に示す)は集光鏡によって効率よく捕捉、反射される。反射した光は第2焦点位置に配置されている⑤光ファイバの入射端面に集光する。光ファイバを透過、射出した光は⑥レンズユニットにより照射面に効率よく照射される。③はシャッタ、④はコールドフィルタでワークの温度を低くしたい時に用いられる。
ライトガイドとして使用する光ファイバは石英ガラスファイバで紫外線の透過にすぐれ耐熱性もよい。石英ガラスファイバは直径0.2mm位の素線を数百~数千本高密度に束ねたバンドル(光学繊維束)である。素線はコア、クラッド共に石英ガラスであるが、コア材は遠紫外域まで透過する高純度な石英ガラス、クラッド材はコア材と屈折率の差を設けるためにフッ素を添加した石英ガラスとなっている。ライトガイドとして使用する光ファイバはバンドルで透過効率が高いことが望ましい。
ウシオのSPキュア、SP5の外観図を図5-27に示す。
SPキュアは外部からの信号により、ランプの点灯、シャッタの開閉といったコントロールが可能である。また、ランプの点灯、安定、シャッタの開閉状態がわかるように信号検出の端子が設けてあり、生産ラインでの使用に適している。
光ファイバは、照射形状、長さ、分岐数、等各種揃えてあり使用目的に合った物を取付け使用できる。
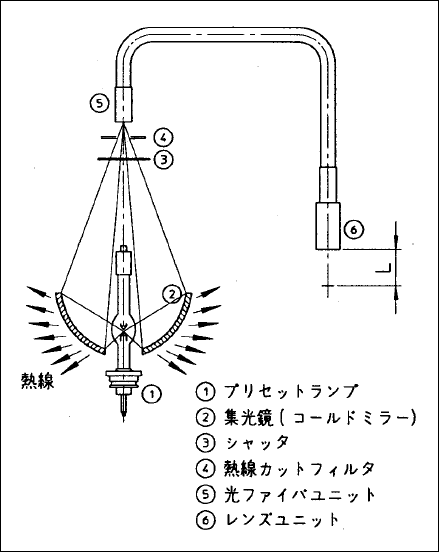
図5-25 光学系(SP-250)
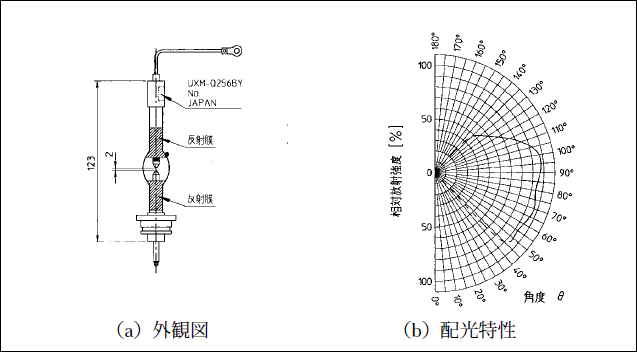
図5-26 Deep UVランプ(UXM-Q256BY)
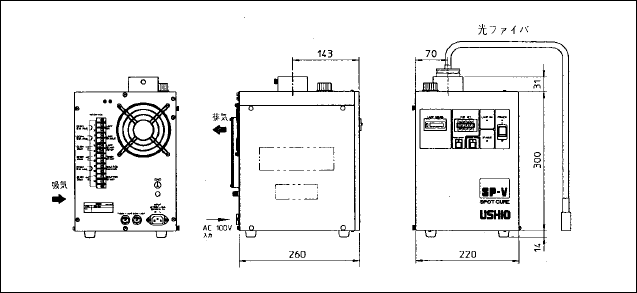
図5-27 SPキュア(SP5-250)外観図
(4)光学性能
ショートアークランプと楕円集光鏡により光ファイバに効率良く光を集めることができ微小面積に高放射照度の紫外線を照射することができる。なお、SP5に使用している250WDeepUVランプは極間2mmの高輝度光源で、直径Φ5mm、長さ1mの石英ガラスファイバとレンズユニットの組合わせにより、照射径Φ5mmの範囲で高い紫外線(365nm)照度を得ることができる。受光径Φ4mmの受光器で測定すると2 5 0 0 ~3000mW/cm2となる。
図5-28にΦ5mm、1m石英ガラスファイバ使用時の照射距離と放射照度の関係をレンズユニット有、無の場合について示す。照射距離は各々レンズユニット先端、ファイバ端面からの距離である。光ファイバの射出部から照射される光線は、光ファイバに入射した角度と同じ角度で広がるので、ファイバ端面より遠くなるほど放射照度は低下してしまう。レンズユニットによりファイバ端面を照射面に投影すると十分な照射距離をとり必要範囲に高放射照度で照射することができる。
楕円集光鏡は特定の波長域を優先的に反射させる多層膜蒸着を行ったコールドミラーである。SPキュアでは主波長がi線(365nm)のものとDeep UV(240nm)~i線のものの2種類のタイプを揃えている。ほとんどの紫外線硬化型接着剤はi線の照射で硬化するが、中には接着強度は十分であるが接着剤の表面部分が硬化しないものがある。これは硬化した接着剤の表面にベタツキが残るために嫌われている。このような場合、接着剤表面も硬化する主波長Deep UV~i線のSPキュアが適している。図5-29に主波長i線SPキュア(SP5-250UB)の分光分布と、主波長Deep UV~i線SPキュア(SP5-250DB)の分光分布を示す。
図5-30にSPキュアのランプを2000時間点灯した場合の放射照度の経時変化を示す。減衰特性はランプの減衰であり光学系の劣化はほとんど無い。放射照度が減衰する理由は主としてランプのスパッタリング、及び電極の消耗による輝度の低下である。新開発のDeep UVランプ(UXM-Q256BY)は従来より使われている超高圧水銀ランプ(USH-250BY)に比べ電極の消耗による輝度の低下を改良している。
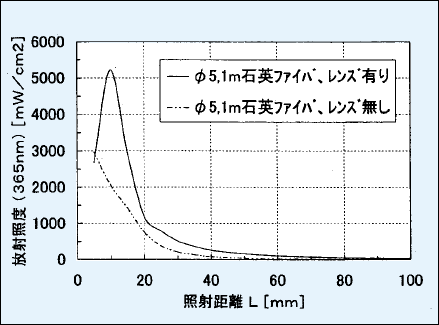
図5-28 放射照度と照射距離の関係
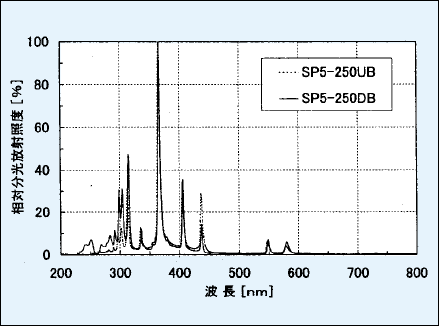
図5-29 分光分布(SP5-250)
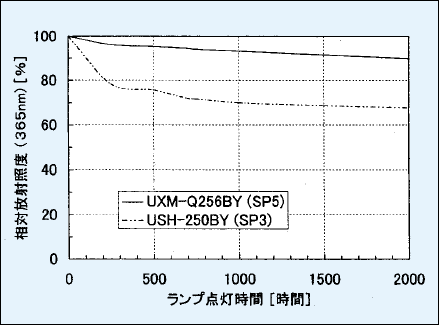
図5-30 放射照度の経時変化
(5)まとめ
SPキュアはショートアークランプ、集光光学系、光ファイバの組合わせにより多彩なUV照射が可能で接着工程の自動化とともに広く普及してきた。また、SPキュアの応用製品として同じファイバ光源装置1)である、半導体の周辺露光装置、TABの周辺露光装置、検査用光源等に発展している。紫外線接着用途、及び、それ以外の微小面積に強い光を当てたい用途に対し、今後もユーザのニーズに対応した新しいファイバ光源装置の商品化が望まれている。
(大澤理)
5.2.8 レーザマーカ
ウシオにおけるレーザは主に研究用の比較的大型のレーザ開発から始まったものと、これとは独立に情報機器用のヘリウムネオンレーザ開発がなされた。大型レーザは電子ビーム制御型ガスレーザ(核融合)、紫外線制御型、マーキングレーザというように発展していった。ここではヘリウムネオンを除く比較的大型のレーザの概要について述べる。
(1)電子ビーム制御型放電レーザの開発
1975年に大阪大学レーザ核融合研究センタ用の大型炭酸ガスレーザ増幅器の開発(図5-31)を行ったのが始まりである。
放電体積が27×27×200cm3と巨大でレーザ出力エネルギーは1nsのパルス幅で1kJを取り出す事ができた。均一なグロー放電を実現するために、加速電圧300kVの大面積の冷陰極型電子ビーム発生器を開発し、発生させた電子ビームをチタン薄膜を通して2kg/cm2に加圧された炭酸ガスの混合気体に打ち込み、この混合気体を均一に予備電離させ、タイミングを見計らい主励起用の380kVのサステイナ電源より、放電エネルギー380kV×80kA×2.5µsの均一なグロー放電を起し、レーザガスを励起させる方式である。
開発の課題は、均一な大電流電子ビーム発生器と、発生用の低インダクタンス高圧電源、高真空と高気圧気体とを隔て効率よく電子ビームを透過させるチタン薄膜機構、高気圧で均一グロー放電を発生させる大面積電極機構と大容量の加圧放電容器及び低インダクタンスな大容量高圧電源、そして各種高圧電源のタイミングやレーザ発振器との微細なタイミング制御、真空容器、加圧放電容器の制御方法などであった。
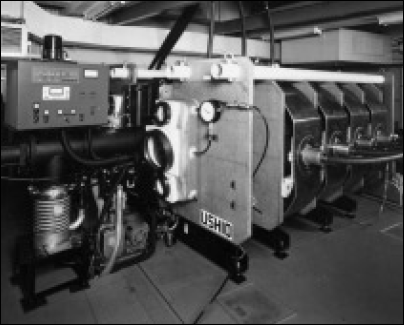
図5-31 大形炭酸ガスレーザ増幅器
(2)紫外線制御型放電レーザの開発
1979年に電子ビーム制御型に比べ取り扱いが容易で大きなエネルギーを発生させる事が可能な、紫外線予備電離制御型の炭酸ガスレーザの開発(図5-32)を行ったのが始まりである。放電体積が20×23×70cm3と大きく、出力エネルギーは250Jを取り出す事ができた。20×70cm2の大面積の紫外線を発生させ、必要な放電空間を均一に予備電離し、タイミングを計って励起用主放電にて、炭酸ガスを励起させる機構である。
開発の課題は、大面積で均一な面発光の紫外線発生機構と、発生した紫外線を用いて大面積を均一に予備電離させる放電機構、タイミングを見計って均一な300kVの高電圧放電をさせる低インダクタンス高電圧電源とアーク放電を発生させない電極形状および放電容器などであった。また、放電体積2.5×2.5×60cm3で出力エネルギー5J、放電体積1.5×1.5×60cm3で出力エネルギー2Jでそれぞれ繰り返しが1Hzのレーザ発振器も同時に開発した。
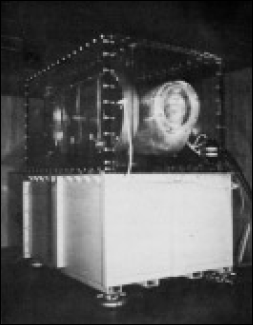
図5-32 大形紫外線予備電離型炭酸ガスレーザ
(3)産業用レーザの開発
各種実験用の大型炭酸ガスレーザの開発から産業用への応用展開として以下の装置が開発された。
①マスクタイプレーザマーカの開発
1987年にコンパクトで比較的出力エネルギーが大きく、繰り返しが速い3軸直交型(ガスフロー方向、放電方向、レーザ出射方向が互いに直行した)放電容器からなる紫外線予備電離型炭酸ガスレーザ(波長10.6µm)の開発を行い、ユニマーク400レーザマーキング装置として販売を開始した。放電体積3×3×70cm3、出力エネルギー3~6J、繰り返し13Hzで放電スイッチとしては乾燥空気による加圧スパークギャップを使用した。1990年にスパークギャップに代わって高信頼型のサイラトロンスイッチを用いたユニマークマーク2を開発した。外観を図5-33に示す。
マスク方式のレーザマーキングの特長とマーキング例は以下の通り。
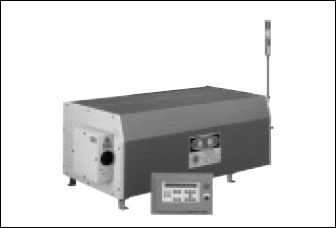
図5-33 ユニマークII外観
a. マーキング方法
長方形のレーザビームが発振されシリンドリカルレンズにてビーム整形された後、マーキング字体が切り抜かれた金属製のマスクを通過したレーザ光を凸レンズにより結像し、ワークに永久刻印をする方法である。図5-34に概念図を示す。マスクを円盤状に配置して高速に回転させる事により刻印内容を任意に選択できるようにした装置もある。
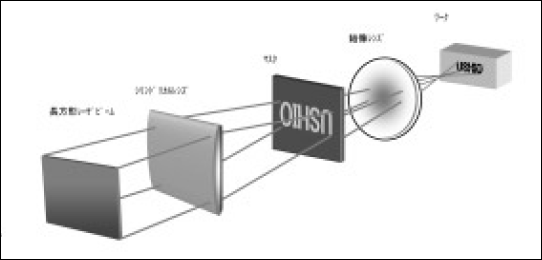
図5-34 TEAレーザマスキング概念図
b. 特長
非接触でロゴマークなどを一秒間に最大13マークを永久に印字できる。
c. マーキング例
- ・半導体パッケージ(集積回路、トランジスタ、ダイオード等)や電子部品(コンデンサ等)への型式の表示がほとんどである。
- ・フイルムやテープのパッケージへの有効期限の表示にも多く利用されている。図5-35にマーキング例を示す。
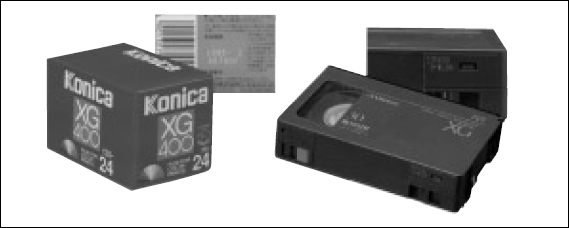
図5-35 パッケージへのTEA レーザマーキング例
② ガルバノスキャン型一筆書きレーザマーカの開発
TEA-CO2レーザマーカに続き、ガルバノスキャンミラーを利用した各種波長のレーザマーカの開発を行い販売した。
- 1994年RF励起方式炭酸ガスレーザマーカ(波長10.6µm)、「ユニマークSC」の販売
- 1995年YAGレーザマーカ、「ユニマークSY」の販売(波長1.06µm)
- 1996年紫外線レーザマーカ、「ユニマークSU」の販売(波長0.266µm)
YAGレーザや第4高調波を発生(CLBO結晶使用)させたガルバノスキャン一筆書き方法の特長とマーキング例は以下の通り。
a. マーキング方法
放出されたレーザ光をX軸、Y軸に配置されたガルバノスキャナと呼ばれる高速回転のモータに取り付けたミラーをパソコンにより文字の字体に沿ってスキャンし、微細な文字用に設計したfθレンズと呼ばれる特殊な凸レンズにより、ワーク表面に集光して刻印する方式である。図5-36に概念図を示す。
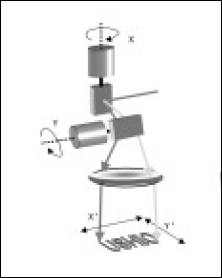
図5-36 スキャンマーキング概念図
b. 特長
波長1.06µmと0.266µmの波長にてワークの特性に合わせた最適なマーキングができるようになった。
c. マーキング例
図5-37に装置外観図を、図5-38に紫外線レーザによる2次元コードをガラス板にマーキングした例を示す。
(横田利夫)
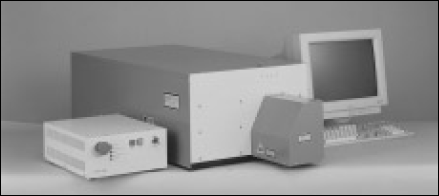
図5-37 UVレーザーマーキング装置外観
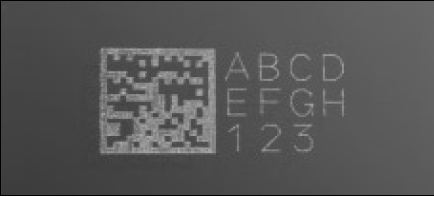
図5-38 硝子板への紫外線レーザーマーキング例
5.2.9 ハードニング装置
(1)はじめに
ハードニング装置は、半導体製造のリソグラフィ工程で、ウエハ上に形成されたレジストパターンの耐熱性や耐エッチング性を高めるための装置である。現像後のレジストは、そのままでは、エッチング時にプラズマと直接反応、あるいはプラズマ中のイオン衝突による反応で昇温し、レジストフローを起こし、パターンが乱される。場合によってはレジストが炭化し、除去が困難になる。本装置はこの問題を解決するために登場した。
ウエハの温度を徐々に上げながら紫外線を照射するので、装置の中心部分は、ウエハの載置台と昇温機能とを兼ね備えた「ホットプレート」と、紫外線照射のための「ランプハウス」とから構成されている。さらに装置に投入されるウエハは通常カセット(キャリア)でまとめて(25枚など)供給されるので、これを1枚ずつ取り出してホットプレート上に置き、処理後に元のカセット、または別のカセットに回収する「ウエハ搬送系」が付加されている。
ハードニング装置の姉妹製品として、ウエハ上に形成された回路に溜まる電荷を紫外線照射することにより消去する、チャージイレーザがある。これはハードニング装置から温度制御機能を抜いたものあり、同様の変遷をたどっている。
これらの装置の開発経緯を、半導体業界ニーズに対応した装置化技術の変遷として、以下に一瞥してみる。表5-1に、この状況を「開発年表」として示す。
(2)開発経緯
当初、ハードニング機能を装置化するに当たり、性能発揮の重要要素である「ホットプレート」、「ランプハウス」、「ウエハ搬送系」が自社内にて開発設計された。「ホットプレート」は1分程度の短時間に室温から250度付近までの急激な昇降温が必要なため、ヒータと水冷のためのパイプを埋め込んだ銅製のプレートが製作された。「ランプハウス」は直管型特殊水銀ランプ2本が実装され、ウエハを高照度で均一に照射できるように反射鏡の形状が工夫された。ただし、ランプは、1本1本交換する形を採っていた。「ウエハ搬送系」はカセット内の下方のウエハからベルトに載せて取り出し、ウォーキングビームと呼ばれるクランク動作をする機構にてホットプレート上に載置し、処理後、ウォーキングビーム→ベルトの順で、別のカセットに回収する方式が採られた。
一方、装置の制御については、当時普及してきた8ビットマイコンを1個使った集中的な制御形態が採られ、電気系・ソフト系は外部業者に製作委託した。こうして1985年に完成したのが、プロトタイプH型ハードニング装置である。これに続き量産対応として開発されたH3型(図5-39)では、マンマシンインタフェース向上のために、操作部分に液晶表示・タッチパネルが採用され、ランプの部分をユニット化したため、ワンタッチ交換、照度・均一度保証が実現された。24時間稼動対応装置の誕生である。
その後、信頼性向上・量産対応・メンテナンス対応のために制御・電気系の内製化が施され、マイコンを何個か使用して機能別に分散制御する方式に改良された。また、回路パターンの微細化に伴う、いわゆるパーティクルの減少要求に対応するために、当時としては先駆的な開発を行っていたロボットメーカの協力を得て、「ウエハ搬送系」をロボット化した。(図5-40)この形をベースにして、客先要求に対して、H4型、H5型(図5-41)、さらにそれら6inchまでのウエハ対応から8inchウエハを処理できるH8型へと展開された。また、厚膜レジストに対応するために減圧下でもハードニング処理できる真空対応HV5型も製作された。
1994年に、制御・電気系を一新し、シングルロボット・ダブルアーム採用のHC93型(図5-42)が開発され、現在の主流となっている。
1998年には、スループットを改善するためにダブルチャンバ(処理部2つ)を持ったHD98型が投入されたが、この際、制御・電気系を市販PC(パソコン)に切り替え、制御系部品の入手性を確保すると共に、マンマシンインタフェースの改良を行った。最近では、12inchウエハ対応のチャージイレーザCE-120型を、HD98型ベースの制御・電気系にて開発し、さらにハードニング装置H120型(図5-43)に展開中である。
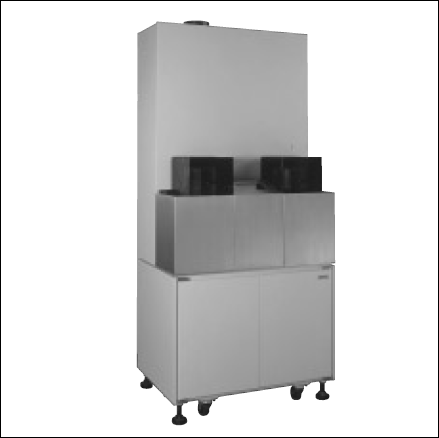
図5-39 量産タイプH3型
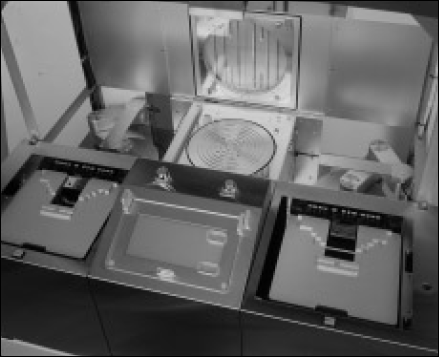
図5-40 ロボット
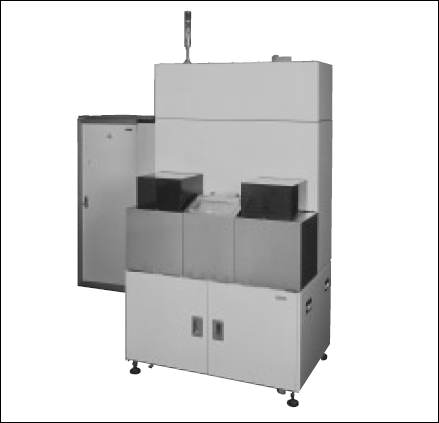
図5-41 量産ロボット搬送H5
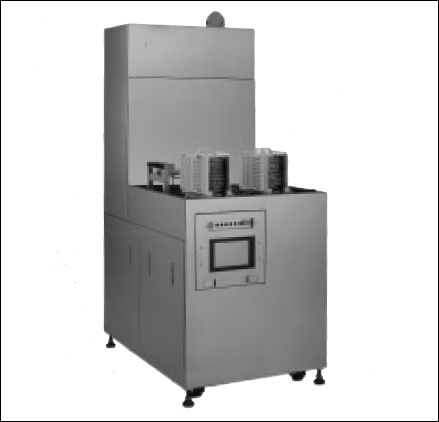
図5-42 シングルロボット・ダブルアーム搬送HC93型
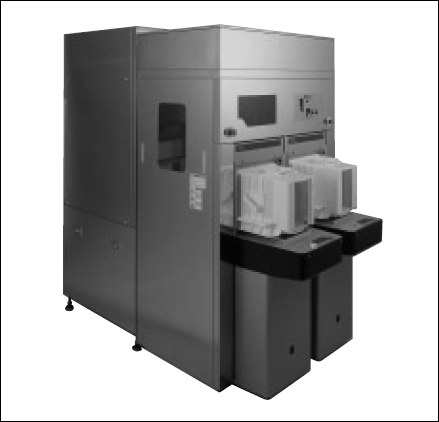
図5-43 12inch対応H120型
(3)おわりに
このように、半導体製造ラインで稼動する装置としての装置化技術がハードニング装置を中心に培われてきた。この中の多くのものが露光装置開発のベースになっている。中でも「ウエハ搬送」、「制御・電気系」などは、ほとんどそのままの形でいくつかの露光装置に採用され、開発期間の短縮、信頼性確保に大きく貢献している。
(三村芳樹、栃原一元)
5.2.10 周辺露光装置
(1)はじめに
周辺露光装置は、半導体製造のリソグラフィ工程などで、パターン形成のためにウエハ上に塗布されたレジストの内、不要であり、しかも残しておくとパーティクルの原因になる恐れのある周辺の部分を、パターン転写に使用する露光光と同等の紫外線で照射し、その後の現像工程で除去する装置である。ウエハを回転ステージ上で一定回転させながら、ウエハ端面を光センサでリアルタイムに検出し(ならい制御)、その位置に基づいて周辺部からの一定幅を帯状に紫外線露光する。したがって、「回転ステージ」、「ならい制御」「露光幅設定」がこの装置の主要部分である。加えて、ハードニング装置と同様にカセットで供給されるウエハを回転ステージに運び、処理後に元のカセット、または別のカセットに回収する「ウエハ搬送系」が用意される。これをスタンドアロンタイプと呼ぶ。一方、コータ・デベロッパ(C/D)に1つのモジュールとして搭載され、C/Dの搬送系によってウエハを1枚ずつ供給される形態があり、これをユニットタイプと呼んでいる。
周辺露光装置の姉妹製品として、ウエハ周辺部を環状に露光するのではなく、ICチップパターンの外形に沿って階段状に露光するステップ露光装置がある。
これらの装置の開発経緯の概略は以下の通りであり、その状況を表5-1に前項にて述べたハードニング装置の開発経緯と並列に示す。
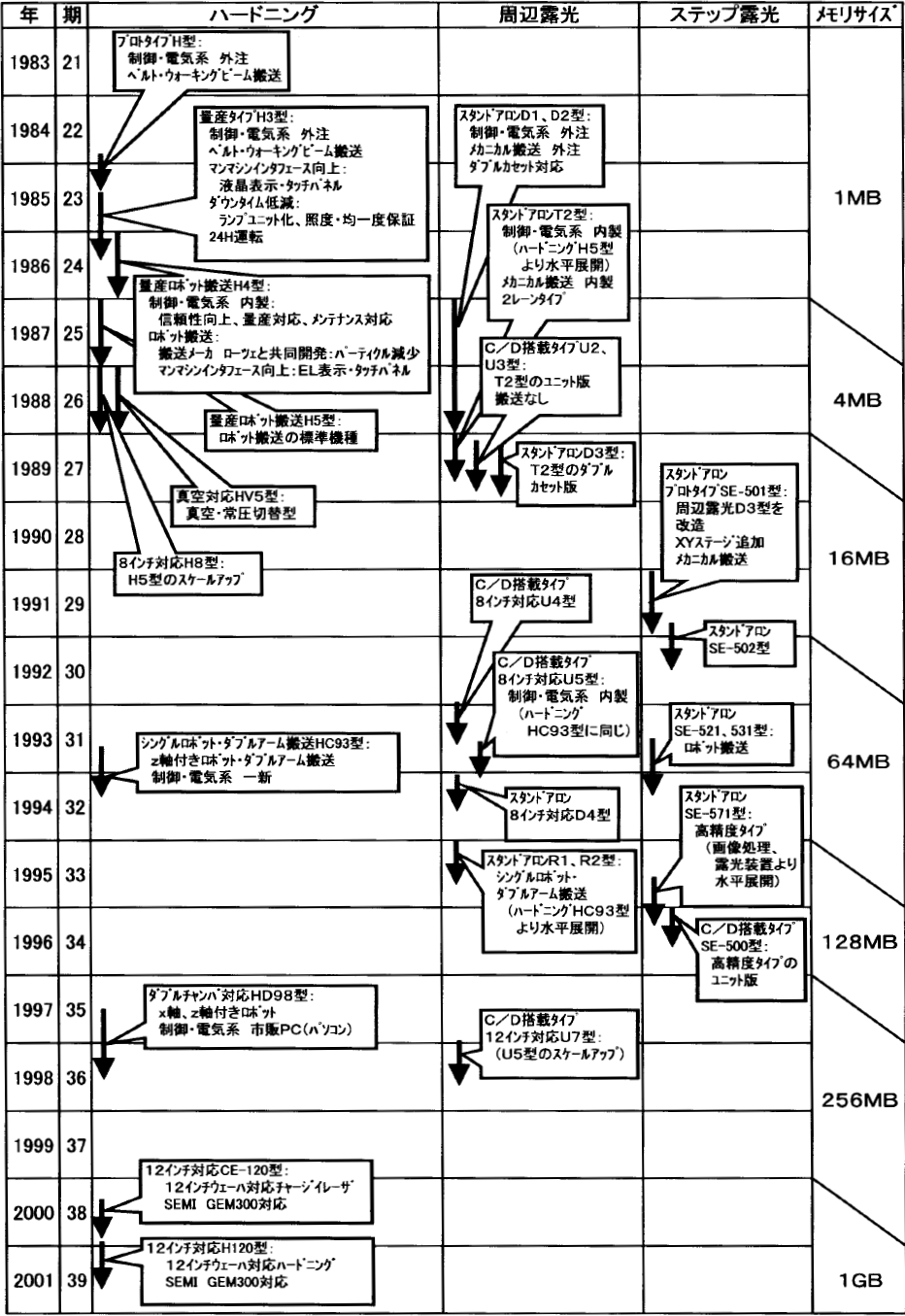
表5 - 1 ハードニング装置・周辺露光装置・ステップ露光装置 開発年表
(2)開発経緯
1987年から1988年にかけて、D1型、D2型が開発された。ウエハを供給する作業者の作業量を軽減するために、カセットを2個まとめて投入できるダブルカセットタイプである。圧縮空気で前後及び90度回転動作するアームでウエハを運ぶメカニカル搬送方式で、シーケンサを使用した制御・電気系を含めて、装置の製作を外部委託した。
引き続いて、それらを内製化した3種類の量産タイプが完成を見た。D2型の2台分を1つの装置のまとめた2レーンタイプのT2型、D2型の内製版でユニットタイプのU3型、U3型のダブルカセット版であるD3型がそれである。制御・電気系の内製化に際しては、その技術をハードニング装置のH5型より水平展開した。外形や処理機能は異なっているが、その異なる点を司るマイコンの制御部分を置き換えれば、装置としての全体制御はハードニング装置も周辺露光装置もほとんど同じと考えられ、統合的な管理が可能となった。
周辺露光装置を装置化する上でもっとも注目すべき機能は「ならい制御」である。光センサによってウエハ端面をリアルタイムに捕らえ、その位置に露光光を当てるため、中心のずれた状態でウエハが回転ステージに置かれた場合でも、また、オリエンテーションフラットのように円からずれた形状が任意のタイミングで現れても、間髪を置かずに正しく露光することができる。
6inchウエハまで対応する上記のタイプのうち、U3型、D3型については、8インチまで処理可能なU4型、D4型が投入されているが、これは単に、スケールアップによる対応である。ハードニング装置のHC93型で制御・電気系を一新したのに合わせて、周辺露光装置も、U4型に対してU5型、D4型に対してR2型と呼応した。なお、R2型では、搬送系もハードニング装置と同じシングルロボットダブルアームに変更し、処理したウエハを同じカセットに戻すことを可能にしている。(図5-44)12inch対応のU7型は、U5型のスケールアップとして、業界の立ち上がりに先駆けて1998年に完成している。
一方、ステップ露光装置の開発は、周辺露光装置のD3型を改造して、「ならい制御」「露光幅設定」をはずした露光ヘッドをxyステージに載せて動かす形で始まった。D3型と同じメカニカル搬送を用い、SE-501型、SE-502型が装置化された。露光位置はオリエンテーションフラットを基準に指定されるので、リニアセンサと回転ステージの組合わせでオリエンテーションフラットの概ねの方向を測定し、さらにy軸(ウエハの動径方向)に抱えた光センサを使って、より正確な値を求め、それに基づいて露光を行っている。この時、回転ステージの高い制御精度が必要なので、回転ステージ用のモータをその仕様に合うものに変更している。他の装置と同じく、SE-521型、SE-531型として、ロボット搬送化がなされた。その後、ICチップパターンの境界であるスクライブラインの真ん中に沿って露光せよという要求が出され、それまでの露光精度±200µmでは対応できなくなった。そこで、露光光の形状をよりシャープにするために露光ヘッドに使用するレンズを高解像タイプに変更し、このための露光ヘッドの重量化とユニットタイプをにらんでの装置の省スペースに対応するよう、露光ヘッドではなく回転ステージをxyに動かす方式に変え、リニアモータを採用した。更にウエハの姿勢を正確に測定するために、露光装置に使われていた画像処理機能を導入して、露光精度±30µmを実現している。この仕様のスタンドアロンタイプがSE-571型(図5-45)であり、ユニットタイプがSE-500型である。
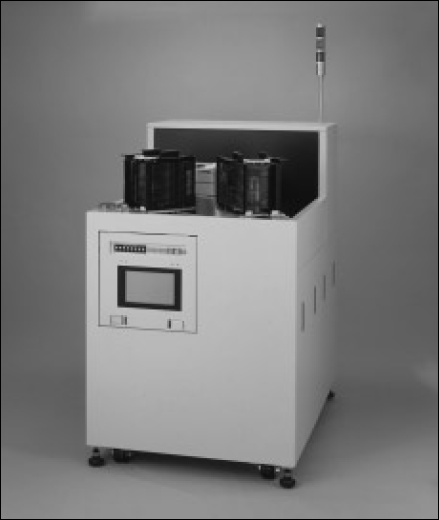
図5-44 スタンドアロンR2型
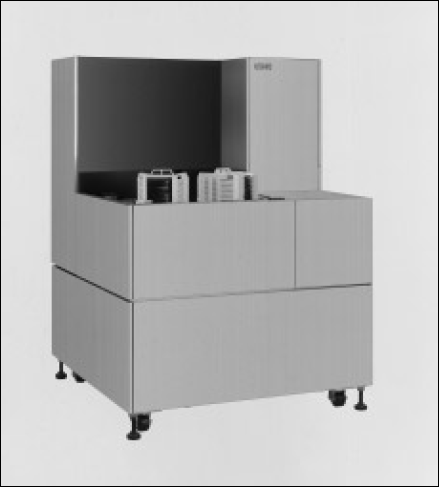
図5-45 スタンドアロンSE-571
(3)おわりに
周辺露光装置にて開発された「ならい方式」は、TABテープの両端(耳の部分)の不要レジストを除去するテープエッジ露光装置に展開されて、新製品として脚光を浴びつつある。
(三村芳樹、栃原一元)
5.3 高性能照明ユニットの開発
5.3.1 半導体ステッパ用照明ユニット
(1)概要
半導体ステッパ用照明ユニットとは、シリコンウエハ上にICを製作するためのステップ&リピート(S&R)投影露光装置に搭載される、照明ユニットのことである。S&R投影露光はICを微細加工する際の露光方式のうちの一つであり現在支配的な方式である。照明ユニットの構成はランプ及びランプ電源、シャッタ及びシャッタコントローラ、光学系からなる。図5-46に照明ユニットの光学系統を示す。本照明ユニットの目的は投影レンズを介して、ウエハ上の露光面に効率よく、均一に、決められた量の光を照射することにある。ランプは超高圧水銀ランプであり、その輝線であるg線(436nm)またはi線、(365nm)が使用される。また均一に照明するためにインテグレータ(フライアイ、ミキサとも言う)が使用され、光が投影レンズを効率良く通過するためにコンデンサレンズが使用されている。
この光学系にマスキングブレード光学系が追加されたものを図5-47に示す。この光学系を付加することにより、マスクの一部分のみを照明することができる。即ち一部分のパターンのみを露光することができる。近年ICの線巾微細化に伴い、光源としてKrF(249nm)、ArF(193nm)レーザが使われているが、インテグレータ以降の基本の光学系は同じものが使われている。ただし、レーザ特有の可干渉性によるスペックル(露光面に多数の傷のような明暗ができる)を消すために、光を振動させる等の工夫をしている。
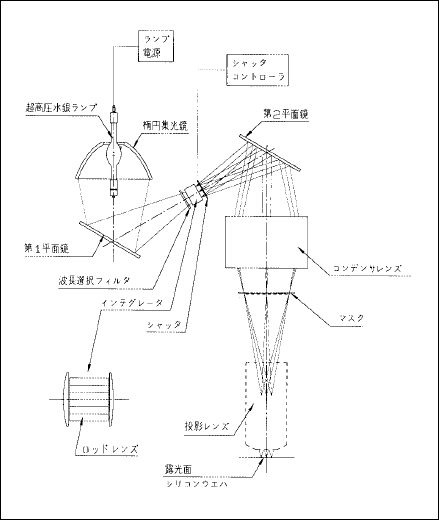
図5-46 照明ユニット光学系統図
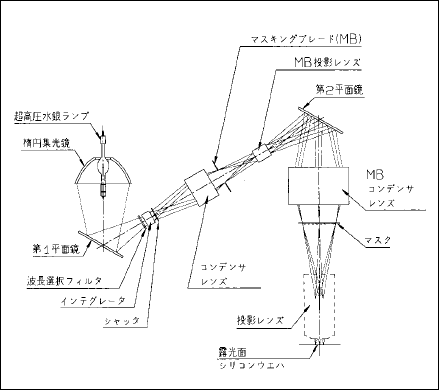
図5-47 マスキングブレード付照明ユニット光学系統図図
(2)歴史
ウシオのステッパ用照明ユニットは1979年A社の研究所への納入で始まり、A社製ステッパに100%搭載され、1993年まで続いた。本照明ユニットは、この間、あるいはその後の、TAB露光装置、プリント基板用ステッパ等の投影露光装置の開発、受注に大きく貢献し、投影露光装置用照明ユニットと名前を変えて、自社の露光装置に搭載され現在に至っている。ウシオは1960年代後半から1970年代前半にかけて、前述の5.2.5ソーラシミュレータを開発している。当時既に、米国NASA・JPL(ジェット推進研究所)がソーラシミュレータを開発しており、これらの文献等を参考にしながら独自に開発を行った。この時の光学設計の技術が半導体プロキシミティ露光用照明ユニット、ステッパ用照明ユニットの開発につながっている。
これらの光学系の最大の特徴はインテグレータと言う、独特の光学要素を使用している点にある。この光学要素は1930年代にイーストマンコダック社、あるいはツァイス社により映写機用として発明され米国特許登録されている。その後、ソーラシミュレータ、半導体・液晶・プリント基板露光装置や、最近ではデータプロジェクタに使用されている。
通常の光学系では、均一な照度を得ようとすると効率が悪くなる(照度が低くなる)が、一方、効率を上げよう(高い照度を得よう)とすると均一性が悪くなる。このジレンマを解決したのがインテグレータである。1979年当時世界で唯一であったGCA社のステッパは、その照明ユニットにインテグレータではなく光ファイバを使用した光学系を採用していた。光ファイバの光学系を図5-48に示す。我々はステッパ用照明ユニットの開発にあたり、光の利用効率、光学部品の組立て易さ、ソーラシミュレータやプロキシミティ用照明ユニットでインテグレータ光学系の経験があった等の理由で、インテグレータ光学系を採用した。この照明ユニット開発に必要な基本的技術は既に持っていたので、開発は通常製作期間で大きな苦労なしに完了したと記憶している。多少苦労したのは、436nmの波長を通し、405nm以下の波長をシャープカットするための色ガラスフィルタが光が強すぎて割れてしまい、多層膜蒸着と組み合わせて割れないようにしたこと、高い照度を得るために、高出力(電力の大きいランプ)のみでは駄目で、高輝度(電極間の短いランプ)が原理的に必要であることを理解してもらうのに苦労したこと位である。しかしその後の商品展開において、問題は山のように発生し、色々と勉強をさせてもらった。この勉強の中で我々にとって最も重要であったのは、マスキングブレード光学系であった。当時ウシオは投影レンズ設計・製作ができなかったので、やむを得ず他社に設計・製作をお願いした。これが契機となり、照明光学系のみではなく、投影レンズの設計製作ができるようになればもっとユーザの役に立てる、仕事が増えると考えて、この時に投影レンズ設計製作に着手した。これが実ったのは、TAB露光装置である。他社が独占していた所へ参入し、数年でシェア100%にできたこと、その後、10年間以上現在にいたるまでシェア100%を維持できていることの大きな理由の一つは投影レンズの設計製作が自社でできることにある。更に、プリント基板用分割投影露光装置等の露光装置において、光源、照明系、投影レンズ、装置(機械、電気、ソフト)が自社で設計製作ができることがウシオの強みになっている。
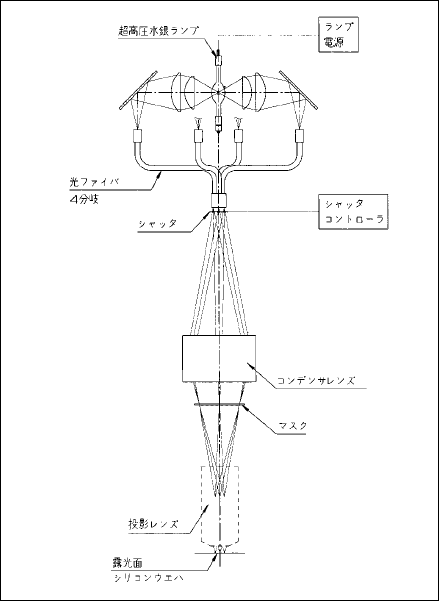
図5-48 光ファイバを使用した照明ユニット光学系統図
(3)要求仕様とその実現のポイント
①要求仕様例
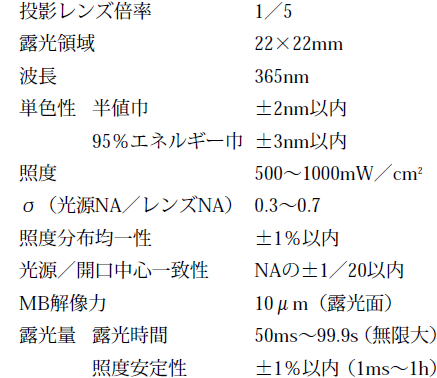
②波長・単色性
超高圧水銀ランプの分光分布は大略図6-49のとおり。この中の436nmまたは365nmの輝線を多層膜波長選択フィルタ等でとりだして単色光にして使用する。半値巾はランプの特性で、95%エネルギー巾はランプの特性に加え波長選択フィルタの特性で得る。単色性が要求されるのは投影レンズの色収差をなくすのが難しいためである。投影レンズの解像力の限界は露光波長と同程度までであり、ICの微細化動向に従い短波長化が進んだ。最近では、KrFエキシマレーザの249nm、ArFの193nmが使用されている。波長300nm以下では通常の光学ガラスは使用できない。レンズの材料として石英ガラス及び、螢石(CaF2)が使用されているが、これだけでは投影レンズの色収差をなくすことができない。このため要求される単色性は1pm程度になり、波長365nmの場合の数nmに比べ1000倍以上厳しい要求になっている。これが光源としてレーザが選ばれた大きな理由であり、エキシマレーザ自身を狭帯域化することによってこの単色性を得ている。
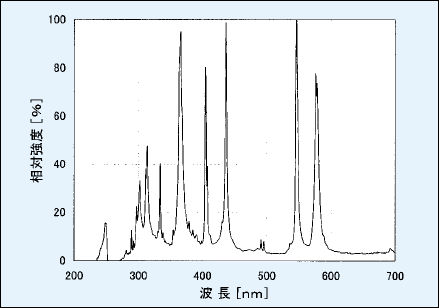
図5-49 超高圧水銀ランプの分光分布
③照度とσ
照度はランプの光出力量、光学系の効率、露光面積で決まる。別の見方をすると、露光面より見た光源のNAと露光面より見た光源の輝度Bで決まり、露光面照度はΠBSIN2βと書ける。図5-50に光源のNAとレンズのNA及びその比σを示す。また、輝度は光学系では高くすることはできない。光源のNAはレンズのNAとσで決められるので、高い照度を得るためには輝度の高い光源が必要になる、即ち電極間の短いランプが必要になる。先頭の論理で言うと、ランプの輝度が低いと光学系の効率が下がり、高い照度を得ることができない。この理由により光源として超高圧水銀ランプが使用され、より電極間の短いランプが要求される。通常σを小さくすると、像のコントラストが上がる(解像力が良くなる)。しかし上記の理由で照度が落ちるため、解像力と生産性とのバランスでσは決められる。σを変更するのはインテグレタ出口に設けられたアパーチャ径を変えれば良い。このアパーチャは投影レンズ開口と結像関係にあり、アパーチャ径が変わると、光源のNAが変わり、σが変わる。
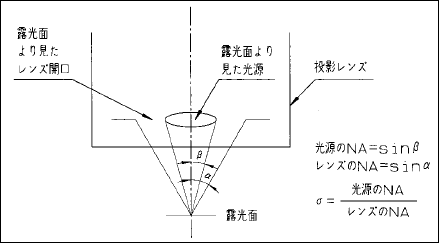
図5-50 光源のNA 、レンズのNA とσ
④照度分布均一性
均一性は基本的にはインテグレータによって得られ、コンデンサレンズの設計により露光面中心と周辺の照度比が調整される。インテグレータの構造は単に、両側に凸面のあるロッドレンズを束ねたものであり、インテグレータ入射側の光軸対称な照度分布が露光面において均一にされる。各ロッドレンズの入射部に入った各々の像が露光面全面に投影され、各々の像が重ね合わされている。これが照度分布が均一になる理由である。露光面と結像関係にあるのはマスク面、インテグレータ入射側、MB面であり、これらの近傍に物を置く時はゴミ、傷等に細心の注意が必要である。ゴミ、傷等が露光面に結像し照度が不均一になる。また光学部品の透過率、反射率のばらつき、特に投影レンズの反射防止膜の透過率ばらつき(主としてレンズ中心と周辺の透過率差)が均一性に大きく影響する。
⑤光源/開口中心一致性
光源/開口中心一致性とは、露光面のどの場所より見ても光源の中心が投影レンズ開口の中心と一致しているか否かの度合いである。これが悪いと期待通りの解像力がでない。図5-46あるいは図5-47において、コンデンサレンズでインテグレータ出射側中心を投影レンズ開口中心に結像させれば良いが、投影レンズの入射側から開口まで、MBがある場合は更に、MB投影レンズ、MBコンデンサレンズで収差が発生しているので、これの補正をコンデンサレンズで行う。コンデンサレンズの設計は主としてこれと上述の均一性を両立させることにある。
⑥MB解像力
MBはMB投影レンズMBコンデンサレンズにより、その像がマスク上に結ばれる(図5-47)。MBは直角2方向に各2枚配置され、各MBは一方向に動く。これにより任意のサイズの長方形の露光エリアが得られる。マスク近傍にMBを配置すればMB投影系は不要となるが、解像力、ゴミ、MB配置の機械的困難さよりMB投影系が使用される。例えば、露光面で10µmの解像力を得るためには、マスクパターン面(下面)とのギャップ350µm以内に、MBを4枚、一部重ねて配置しないといけないが、実際には困難である。
⑦露光量
露光量を安定させるためには、照度の安定性と露光時間の安定性が必要である。通常は照度モニタが取り付けられ、照度×時間でシャッタの制御を行う。従って照度の安定性は厳しく要求はされない。しかし近年、少しづつ多くなっているステップ&スキャン方式では、スキャンしている間の照度変化は即露光量変化となるので、上述の±1%より厳しい要求をされる。露光時間は50msの要求により回転板をサーボモータで回転させる方式のシャッタが使用される。図5-51にシャッタ板を示す。もっとも問題となるのはシャッタ板が局部的に温度上昇し、板が反ることである。これを防止するために、シャッタ板の材質は比重が小さく熱伝導率の良いものを使用する、サーボモータパワーアップの弊害はあるが板厚を厚くして温度を均一にする、光の入射面の反射率上げる、エアー冷却、もう一つ低速シャッタを設け長時間シャッタ閉の時はこれを使う等の対策が必要である。照度安定性のためランプ電源は定電力制御方式が使われる。定電力でランプは1000時間で約30%照度が低下するが、照度モニタで露光量制御するのであまり問題は無い。問題となる照度変化はステップ&スキャンの方式のスキャン中の時のみである。ランプ電源は1msオーダの電力変化(リップル)を±0.2%程度まで押さえられるので、この場合でも問題となることは無い。超高圧水銀ランプは放電ランプであり、そのアークの位置がゆらぐことがある。定電力であっても、アーク位置がゆらぐと、通常の光学系では照度が変化する。このアーク位置の揺らぎ(特に1ms~1s間)を小さくするのがポイントである。
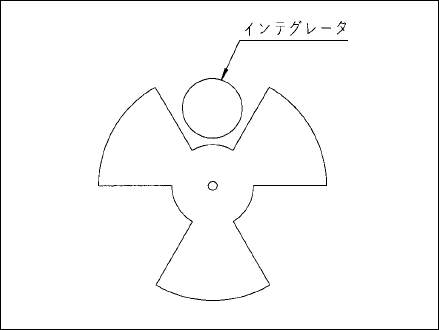
図5-51 シャッタ板
(後藤学)
5.3.2 マルチライト
マルチライトは、制御された光をいろいろな目的に、しかも比較的安価にお客様に使っていただくための製品として作られた。このためにランプとランプハウスのバリエーションを数種類用意し、100%要求を満足できないまでも、その中から近い物を選んで頂けるよう、ラインナップしている。
(1)マルチライトのできたわけ
1986年頃かそれ以前の事だが、自社で大面積のパターンを露光できる露光装置を作りたいと言う構想があった。しかし、使ってもらえる市場、あるいは市場で育ちそうな技術の芽が無ければ、何の意味もない。そこで、まずはそのような市場を見つけるために、まずカタログ商品を作り、宣伝や訪問し使ってもらうことで糸口をつかもうと言うことになった。その頃はアライナやステッパの照明光学系(ランプハウス)を数社にOEM供給しており、露光機の最先端に常に接していたので、当然の事ながら得意分野であるランプハウスがこの製品群に選ばれることとなった。また、OEMでなく光源部を標準化すれば同じ物が何台も生産できるので、当然値段が下がり、値段が下がることで性能の良い製品を安く供給でき、そうすることでお客様に使っていただく機会が増え、更には新しい用途が拓けると言うストーリーが考えられた。
(2)マルチライトの構成
①ランプの選択
ウシオはランプのメーカでもあり、使うことのできるランプは何十種類にもおよぶ。その中で、露光には超高圧水銀ランプが今も良く使われている。その当時、実際に露光(パターニング)に使われているランプは、250Wから3.5kWと様々なランプが使用されていた。同じワット数でも何種類もランプが存在していた。もともとはお客様にまずは使ってみていただくためのものであるから、大きな装置では敬遠されてしまう。そこでカタログのラインナップは250Wと500Wの2種類に決め、仕様は実績と安定性、及びできるだけ電極間の距離が短い物を選定した。電極間が短いと良い理由は、点に近いほど光学系の自由度が上がるためである。
②ランプハウスの構造(図5-52)
ランプの発光部は点光源に近いので、楕円集光鏡で光を集めて次の光学部品(ファイバやインテグレータ)に渡す。光路を短くするために、途中で一度折り返すための平面鏡を入れる。また、集光鏡と平面鏡は多層膜蒸着をして、露光に関係のない光をできるだけ少なくしている。これは短波長の光がレンズなどを劣化し、長波長の光は露光しようとする対象物の温度を上昇させていろいろな不具合を生じさせるためである。(図5-53)超高圧水銀ランプはその名のごとく、放電が安定したときの水銀の蒸気圧が十数気圧になる。この蒸気圧を保つために放電ランプの管壁温度が約600°Cにもなる。だからランプハウスの構造には火傷などの危険のない、例えばハウスを触っても暖かい程度にしなければならない。また、ランプの放電部分は1~2mm程度であるので、温度が上がって光軸がずれてしまうと、照度が落ちるだけではなく、照度均一度も悪くなってしまう。そこで、主な光学部品(ランプ、集光鏡等)は一つの鋳物部品に貼り付け、光路が歪まない様にし、それ全体を更に2重の板金で覆い、温度の対策をする構造にした。
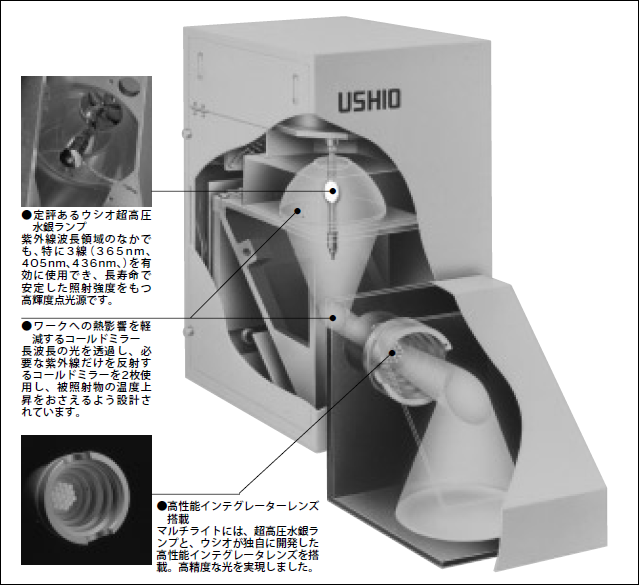
図5-52 ランプハウスの透視図
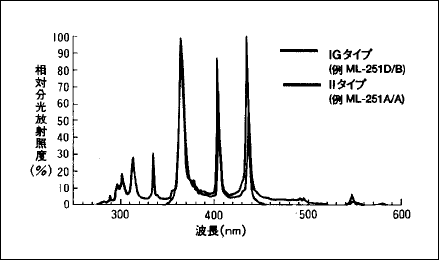
図5-53 分光分布
③照射部のバリエーション
照射面積の要求は、お客様に依ってまちまちであるが、要求のあるたびに作っていたのではコストも掛かってしまう。そこでΦ200mmまでの照射径のユニットを数種類用意し、要求に一番近い径の物を選んもらえるようした。Φ200mmというのは半導体ウエハの8inchを想定したものである。また、平行光だけでなく、ファイバでの使用も選択できるようにした。また、平行光でも視角(照射面のある一点に入る光の角度)も色々な実験を想定して変更できるようにした。
④照射量のコントロール
照射量をコントロールするのに、手動でシャッタ開閉していたのでは正確さにも欠けるし、また、生産に使おうとしたときにいちいちその機能を設計するのは効率が悪い。そこで、2種類のシャッタコントローラを用意した。一つはシャッタの開時間を、もう一つは照射量そのものをコントロールするものである。共に外部(お客様の)信号で制御を開始する機能も附加した。
(3)光源部のバリエーション
以上のように、実験やある程度の生産装置を想定した品揃えは整ったが、対応できるのは半導体のウエハまでで、他の市場、例えばプリント基板などでは□数百mmの面積が必要であった。しかし、規格も一定しておらず、予め照射面積を想定して用意するわけにもいかない。とは言っても、何らかのラインナップが用意されていなければ話が進まない。そこで用意したのは光源部と、広い面積にも対応できるレンズであった。当時、広い面積の平行光を作るには、コリメータミラーが使用されていたが、ガラスのレンズで同じ事をしようとすると、重たくなりすぎて実用的ではなかった。そこでレンズをガラスではなくアクリルに変えてみた。現在では更に照射面積が広くなり、コリメータミラーが多用されている。(図5-54)光源部は2kWと、当時保有していた超高圧水銀ランプで一番大きかった3.5kWを用意した。2kWは当初、想定していたが、3.5kWは別の事情からシリーズに加わったものである。アメリカのベンチャー企業から、液晶ステッパ用ランプハウスの依頼があったのがきっかけであった。余談ではあるが、このランプハウスの打ち合わせのために、筆者は初めて海外に行った。それまで渡航の経験は無く、行くときも一人であった。今考えると実に無謀だったと思う。お客様はボストンの郊外に位置しており、ボストン空港に着いて迎えの方と会ったとき、先方の方の言葉が「良くたどり着けましたね」であった。
その他にシリーズには加えなかったが、当時1kWのランプハウスがG社ステッパのレトロフィット用として存在していた。現在は自社製品にのみ使用されている。
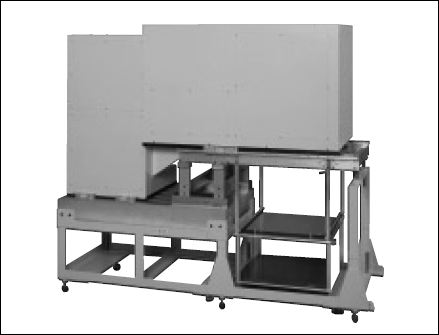
図5-54 2kW、3.5kWシリーズ
(4)マルチライトの広がり
以上のように、光源部は標準化され、ある程度の要求までは照射部が対応でき、照射部を変えれば色々な要求に対応できる状態になった。そこから先は、さて、何に使えるかと言うことになる。現在ではお客様のみならず、自社内でも手軽に使える光源ユニットと言う位置づけが定着している。以下に当時使われた例を述べる。
①□800mmプリント基板用
ランプハウスの照射面積は□400mmであった。購入したお客様がランプハウスを平行移動させて□800mmの照射面積をカバーすると言うユニークな使い方であった。
②液晶ステッパ用
前記で述べたボストンの会社へ納入したものである。3.5kWのランプハウスで照射面積はΦ160mm。ステッパのレンズは1/2の縮小投影なので、一回の露光面積は□56mmである。このステッパのユニークなところは、一つの装置に二つの光学系を搭載していて、一度に2パッターンを露光できるというところであった。(図5-55)
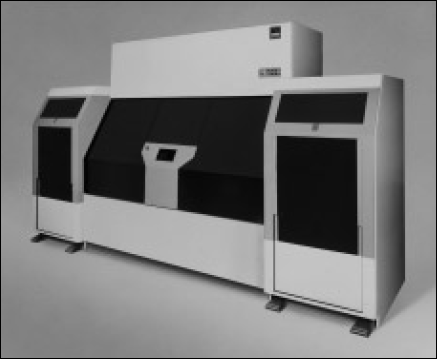
図5-55 液晶ステッパ
③他社露光装置の光源部のレトロフィット
現在、TABテープは液晶ドライバ、T-BGA、CSPなどいろいろなところで使われているが、当時は存在があまり知られていなかった。仕様書を持って営業と技術が一緒にお客様を回っているうちに、面積は小さいが投影露光でテープ上にパターンを作っている会社があることを知った。それが現在のTABテープだったのである。当時は5~6社であったと思う。それらの会社はB社の露光装置を使っており、ランプハウスの仕様から、ウシオのランプハウスを載せ変えること(レトロフィット)で生産性を上げる可能性が十分にあった。実際、載せ変えてみると照度は上がり、パターンの切れも良くなり、実質的に生産性が2~3倍になったのではないかと思う。これがお客様の信頼を得るきっかけになり、TAB露光装置を作ることに繋がっていった。(図5-56)これら以外にも150mm幅テープのコンタクト露光用、液晶カラーフィルタ用などに実際に使用した例もあるが、いずれにしても光源部を標準化したことが、お客様にとってもウシオにとっても良い方向に働いたのではないかと思う。
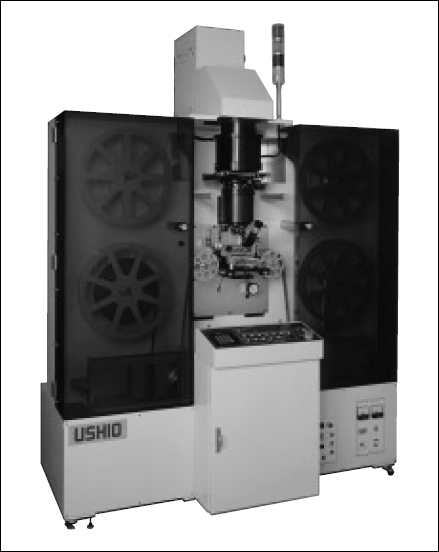
図5-56 TAB露光装置
④自社製品への展開
マルチライトの出発点は自社で露光装置を作ることであった。現在はプリント基板の投影露光(ステップ&リピート方式)を手がけるところまできており、当初の思惑通り運んだと思う。その他にもハードディスクのサスペンション、水晶振動子などの製造用の露光装置も作られてきたが、光源部は標準品かそのマイナーチェンジするだけで利用することが可能となっている。マルチライトの初期の目的は一応達成したが、まだ未知の応用分野が残されているかも知れない。これからも新しい使われ方や応用が考案され、使われる方々の役に立つに違いない。
(田中一也)
【コーヒーブレイク】
照明ユニットのレトロフィット化
ウシオのTAB露光装置は今でこそシェア100%を誇るが、その誕生には語り草になっている、ある作戦があった。長期にわたる信頼関係とほぼ100%のシェア。このようなところへ挑むことなど無謀としか思えない。しかし、我々は持ち前の意欲と発想で0から100%へという奇跡を起こしたのである。
●露光装置メーカB社の牙城
当時、A社の「TABテープ」のことを、ウシオでは誰も知らなかった。しかもTABテープの露光装置はほぼ100%B社が供給しており、A社と同様のTABテープを作っている各社とは長期にわたる取引関係にあり、ウシオから見れば「牙城」に思われ、どうやって参入するか困り果てていた。「“ランプのウシオ”は知っているが“ランプハウス(マルチライト)のウシオ”とは聞いたこともない」と認めてもらえなかったのである。いくら実績データを提示しても、なるほどとうなずくものの実機で未確認のため、具体的な購入行動には移していただけなかった。
●マルチライト
実はその数年前に多目的露光ユニット「マルチライト」が開発された。マルチライトは照明系だけ、つまりランプの光をインテグレータを経由して平行光にするコリメータレンズまでで、いわゆるランプハウスといわれるものである。(詳細は5.3.2参照)そもそもマルチライトは露光装置メーカに数多く販売することを目的に開発した製品で、標準化・シリーズ化を図ることにより、ウシオの従来比で価格が1/3、納期が1/2というレベルを達成していた。だからそれなりに販売は伸びたのだが、計画にはとても及ばないという状態が2年間も続いた。半導体生産用プロキシミティ露光装置用レトロフィットとして半導体メーカにもアプローチしたが、取り合い部分で露光装置メーカとの協力が不可欠であった。しかし、そのようなことへの協力など、露光装置メーカが受け入れるはずもなく断念せざるを得なかった。「もうだめなのか…」そんな思いをいだき始めたあるとき、A社に納めたマルチライトが大変好評で、1号機評価の結果次第では複数台まとまるとの引き合いがあった。結果は「ウシオ製は照度が強く生産性向上に役立つ」ということだった。「やはりウシオのランプハウスは優れているんだ」と再認識させられた。
●スフィンクス作戦
打開策として「ランプハウスを試してもらい、気に入ったらご購入いただく」という方針を打ち出し、社内では「スフィンクス作戦(露光装置のヘッド部をB社製からウシオ製にすげ替える)」と名付け展開を開始した。エジプトのスフィンクスは頭部が人で胴体は動物ということで、胴体にもっともマッチした違和感のない頭部(当社ランプハウス)にすげ替えるという意味でスフィンクス作戦と名付けたわけである。作戦は貸出しという、お客様のリスクを最小限に押さえた方法だっため、検討開始スピードが早くなった。更にそのスピードが計画的にP-D-C-Aを回転させるという、好循環パターンを継続することができ、満足できる結果となった。作戦が的中したのである。
●業界貢献
スフィンクス作戦の好循環パターンを維持できた最大要因は、「貸出し→評価→好評」となること。つまり、必要な波長帯域での照度エネルギーが従来比2~3倍にアップしたことにより、お客様の生産能力が大幅に向上したのである。お客様にとってもレトロフィットにより既設機改造のみで新規設備投資が不要となった価値は大きく、「ウシオはTAB業界に多大なる貢献をした。表彰したいくらいだ」と絶賛され、ウシオ認知から信頼を勝ち取るという域まで一気に到達することができた。
●TAB露光装置への発展
信頼を勝ち取ることにより幸運は程なく訪れることとなった。その幸運とは、お客様より「頭部だけでなく胴体もチャレンジしてはどうか」とのお話しをいただいたことである。常に新しいものへの挑戦を考えていたウシオでは、即座にその話しに飛びついた。これが「ウシオTAB露光装置」の始まりである。しかし装置化となるとそう簡単ではなく、完成度を向上させることは非常に困難なことで、試作1号機から量産機まで挑戦と失敗を繰り返し、なんと3年もの年月を要してしまったのである。途中で何度も挫折しそうになったが、このときの我慢が今日に至った事を思うと、ビジネスとは成功、失敗が紙一重の部分があり恐ろしくさえなる。
(衛藤潤生)
5.4 露光装置への展開
5.4.1 投影レンズの開発
1988年、ウシオは露光装置の開発をスタート。この時、マスクダメージのない投影方式に着目し、開発のターゲットに投影露光装置を選択した。この選択が投影レンズ開発の第一歩である。以下にその投影レンズ開発の歴史を紹介する。
(1)スタートのきっかけ、TAB露光装置
ウシオで最初の投影レンズ搭載露光装置は、1989年に商品化されたTAB露光装置である。既に10年余の歴史を経て、現在ウシオの主力商品の1つに成長したTAB露光装置であるが、そのスタートはウシオにとって初めての投影露光装置開発であった。当時、光源メーカとしてフォトリソグラフィ用紫外線光源をさまざまな露光装置用に供給、更には半導体ステッパ用に照明ユニットをOEM供給する状況にあったウシオは、効率よく均一に光を照射する、いわゆる照明光学系についてはその基盤ができあがっていた。また、この当時からランプを使った装置開発をも進めており、紫外線レジスト硬化装置が半導体装置として認知され始めた時代でもあった。ここでウシオでは、これら「光源」「照明ユニット」「装置技術」をベースに新たな装置開発に着手。TAB露光装置、そして投影レンズ開発のスタートである。
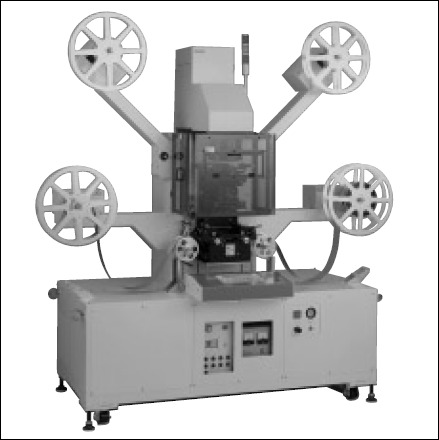
図5-57 TAB露光装置
(2)露光装置の分類
ここで少し露光装置について見てみたい。露光装置とは、照明ユニットから照射される紫外線によって、マスク上のパターンをレジストの塗布されたウエハ等のワーク上に転写する装置である。一言で露光装置といってもその露光の方式によっていくつかに分類される。図5-58に示すように露光方式の分類は、まず「マスクとワークとを密着(コンタクト)して露光するもの」と「マスクとワークとを離して露光するもの」に大別される。前者のコンタクト露光法は日光写真そのものであり、最も基本的な方式である。装置として構造が単純で安価であるというメリットに対して、マスクとワークが密着するためにマスクの消耗(ダメージ)が生ずるというデメリットを持っている。
後者の「マスクとワークとを離して露光するもの」は、更に「わずかな隙間をあけて露光するもの」と「投影レンズを使用しマスクとワークを完全に分離して露光するもの」に分類される。わずかな隙間をあけて露光する方法はプロキシミティ露光法と呼ばれ、日光写真の通用する範囲内でマスクとワークに隙間をあけ、マスクダメージを軽減させる工夫がしてある。それに対し投影露光法は投影レンズによってマスクとワークが完全に分離可能な方式である。このためマスクダメージがない。しかしながら装置の性能を投影レンズが左右することになる。露光装置開発にあたりウシオでは、上述のとおりマスクにダメージがなく、また焦点深度の確保に有利な「投影露光方式」に着目した。そして「投影露光装置」を開発のターゲットとしたのである。
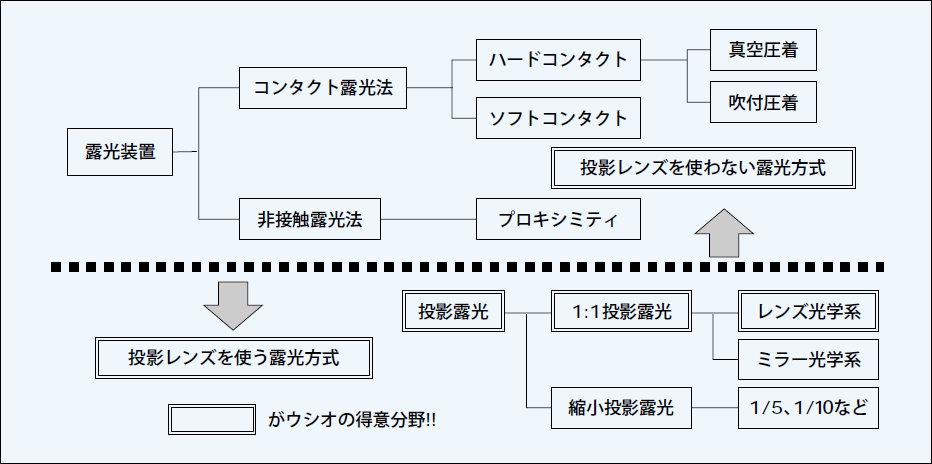
図5-58 露光方式
(3)照明光学系+市販レンズ時代
話を戻そう。紫外線光源を持ち、また照明光学系技術のを確立していたウシオが、露光装置を手がけるのはある意味で自然な流れであった。その流れのなかでTAB露光装置開発がスタートした。しかしながら当時のウシオには「投影レンズ」の設計/製造経験はなく、更には使用経験もほとんどなかった。投影露光方式を選択した以上、たとえ良質の照明光があっても投影レンズがなければ始まらない。投影レンズの開発が必要であった。しかし投影レンズは露光装置の心臓部である。素人集団にすぐに開発できるほど簡単ではない。そこでウシオでは、まず市販の写真製版用レンズを入手し装置に搭載した。この時点ではとても投影レンズ開発とは言えないかもしれない。しかしながらこの市販レンズを使うことによって投影レンズ、そして投影露光法というものの感触をつかみ、解像力・ディストーション・性能ばらつき・耐久性などのポイントを知ることができた。
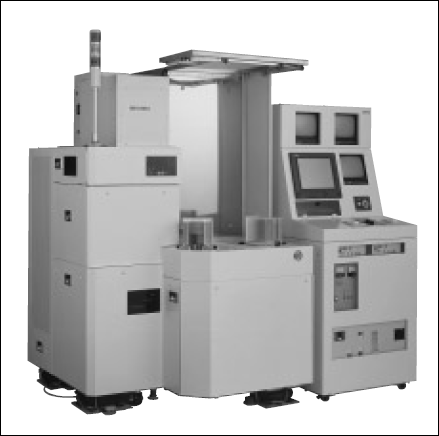
図5-59 片面一括投影露光装置
(4)自社開発レンズの誕生
市販レンズを搭載したTAB露光装置は、そこそこの実績を残した。しかしながら決められた仕様しか選択できない市販レンズでは、限界は見えていた。ユーザニーズに対して的確にかつタイムリーな製品を出荷するには、やはり投影レンズの自社開発が必要であった。1990年、ウシオでは光学設計ソフトウエアを導入。自社投影レンズ設計を開始した。と言っても光学設計ソフトウエアはただのTOOLに過ぎない。肝心の投影レンズ設計経験者はゼロ。現役の光学設計者の方が聞くと驚くかもしれないが、「横収差図って何?」といった状況であった。まさにゼロからのスタートである。このような状況で、ウシオは幸いにも強力な指導者にめぐり合う。大手光学メーカを経て大学の教授をされていた先生から、月1~2回のご指導を受ける機会を得たのである。これはウシオにとってまさに救いの舟であった。本当にゼロからのスタートではあったが、この指導会のおかげもあってウシオでの投影レンズ自社開発は急ピッチで進むこととなる。そして1990年、記念すべきウシオ初の自社開発投影レンズ「UPL-04」が完成した。現在のウシオの投影レンズの仕様と比べるとかなり未熟な仕様ではあるが、この投影レンズが光学設計ソフトウエアの導入と同じ年に完成できたのは、指導会の成果以外の何ものでもないと思う。この1990年はウシオの投影レンズ開発にとって大きな1年であった。TAB露光装置用に開発された「UPL-04」レンズは、市販レンズを搭載し出荷されたTAB露光装置に対して、投影レンズのみをグレードUPできるようコンセプトされた。すなわち従来使用していた市販レンズとの取付けの互換性を考慮し、かつ光学性能をUPすべく設計されたものであった。翌年の1991年だったと思うが、この投影レンズがユーザにて評価された。結果は良好。従来の市販レンズの性能を超え、このレンズへの交換のみで装置性能が向上した。
(5)高性能レンズへのチャレンジ
その後ウシオではコストと品質を配慮の上で「自社設計+協力工場にて加工・組立」という形で投影レンズ開発・生産を進めていった。露光装置開発もTAB露光装置のみにとどまらず、チップバンプやパワーデバイス用途でウエハを露光するタイプの開発も行われた。更にマイクロマシン用途、ハードディスクのサスペンション露光用途など、バリエーションが広がっていった。また投影レンズ開発当初から行われた指導会はその後も数を重ね、設計技術向上ばかりでなく光学知識習得のためにも大きな成果をもたらした。そのかいあって投影レンズ開発もまた、露光装置のバリエーション拡大に対応し順調に進んでいった。1995年、この年は弊社投影レンズ開発にとって次なるチャレンジの1年となった。世の中の軽薄短小の流れに乗って、露光装置の解像性能要求も微細化、高精度化が進んだ。投影レンズの基本性能である解像力とディストーションも、従来に増して高解像・低ディストーションが求められていった。更にウシオでは生産性向上のための大面積露光エリアも重要なファクタであると考えていた。「大面積かつ高解像・低ディストーション」要求。これに応えるには当時の「自社設計+協力工場にて加工・組立」では限界にきていた。設計も当然重要だが、それにも増して組立技術が重要となっていたためである。従来に増して高精度に組立が可能な投影レンズ構造と組立技術が必要となった。1995年、ウシオでは自社組立の大面積・高解像・低ディストーション投影レンズ開発をスタートした。この時点で投影レンズの光学設計に関しては5年近い経験となっていた。しかしながら構造設計、更に組立方法に関する知識・技能はまだまだ未熟であった。この年、従来の投影レンズ構造を見直し、その組立精度・方法も考慮した構造設計が行われた。更には組立設備の開発も同時に進められた。ちなみにこの時に開発された投影レンズは光学設計的にも過去最高の解像力を誇るものであった。この開発が完成するまでに約1年半が費やされた。1990年のUPL-04開発はある意味ビギナーズラックであったかもしれないが、1995年はそうはいかなかった。やはり高精度組立が困難であり、試行錯誤が繰り返された。1996年末、苦難の末に投影レンズは完成した。Φ150mmの露光エリアを持ちながら従来比で3~5倍の高解像・低ディストーションが実現された。図5-60はそのイメージ図である。投影レンズの全長は1mを超えるものである。この開発は、現在に至る大きな基礎を築いた。この時開発された投影レンズ構造および組立技術は、改良を加えながらも基本的には現在も踏襲されている。このレンズ開発は当時のウシオにとってかなり高いハードルと思われる開発仕様であった。しかしあえてその難しい仕様にチャレンジできた当時の環境は幸せであった。
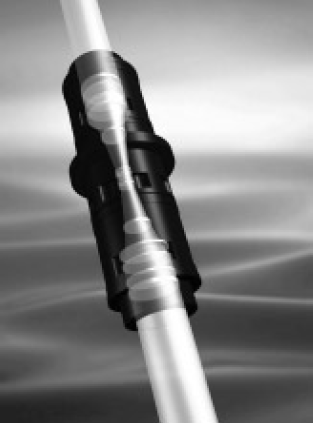
図5-60 投影レンズ
(6)オートスケール機能への対応
1999年、現在のウシオの投影レンズの特徴のひとつとなった仕様が追加された。オートスケール機能への対応である。オートスケール機能とは露光時の重ね合わせ精度向上のため、投影レンズの倍率を±0.1%程度変化させ露光する機能である。この年、このオートスケール機能に対応するため投影レンズに自動変倍構造を追加した。いわゆる写真用カメラのズーム機構である。±0.1%というとほんのわずかに聞こえるが、この種の露光用レンズで同様の機能を有するものは極わずかである。解像力他に極力影響を与えず倍率を変化させるには非常に高精度な移動機構が必要であり、決して容易ではない。ウシオでは投影レンズ内部の構造を工夫し、組立やすさ等も配慮しながらその機能を実現した。現在このオートスケール機能はウシオの投影露光装置の大きな特徴となっている。
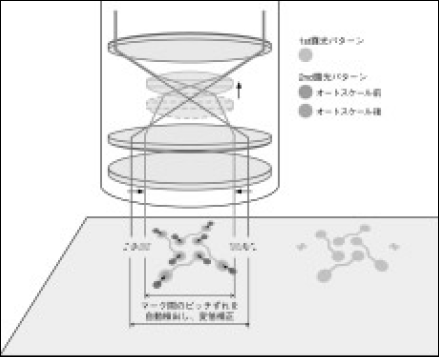
図5-61 オートスケール機能
(7)今後の開発計画
上述のように、1990年以来ウシオはある意味で「怖い物知らず」で投影レンズ開発を行ってきた。最初の開発以来、市場のニーズに応えるべく「高解像力化」「低ディストーション化」を進め、更に露光装置としての生産性にこだわり「露光エリアの大面積化」も進めてきた。最近では「オートスケール対応」も実施した。これらの投影レンズ開発はウシオの露光装置の成長に貢献し、更には多少なりともユーザのニーズに応えられたものと自負している。今回、非常に簡単ではあるが、それらの投影レンズ開発の歴史を紹介させていただいた。最後に今後の開発計画であるが、やはり「高解像力化」「低ディストーション化」あるいは「露光エリアの大面積化」を進めることとなる。市場のニーズを的確につかみ、そのニーズに応えられる投影レンズ開発が今後のテーマである。
(住谷正人)
5.4.2 アライメント、搬送、制御
1990年代初め、すでにウシオは半導体生産装置としてレジストハードニング装置およびウエハ周辺露光装置(以降先行製品と呼ぶ)を生産していた。露光装置の開発はこれらの先行製品を基礎に性能や機能の仕様検討を行う事から始めた。
露光装置はフォトリソグラフィと呼ばれる光を使った印刷技術の一種に使われる装置で、その応用範囲は非常に多岐に渡る。特に今までウシオ電機が経験している半導体用ウエハのみならずガラス、金属片、セラミックス、有機材料など広範囲な産業分野で使用される、微細加工を行う材料全般に渡っている。このように材料が広範囲であることは材料のハンドリング(搬送や位置決め)は各種材料に対して個別に検討する必要があることを意味する。また、このことはアライメントを行うためのターゲットマークも多種であることを意味している。このような個別材料に対応するための作業は、露光装置開発そのものにつながっている。このような個別対応の設計作業以外にも制御システムの基本設計は装置開発において非常に重要な部分である。
先行製品は高い信頼性が要求される半導体業界向けで実績があったため、各種の制御システムはそのまま導入することができた。また、装置が基本的に備えておかなければならないメンテナンス性や信頼性確保のための検討等はこれら先行製品の経験を参考に進めた。通常新しく装置を作る場合、このような検討は十分に行われるべき項目であるが、それをかなり省略することができた。そのことを具体的な効果として表すことは難しいが、先行製品での成果を使うことによって開発期間の大幅な短縮ができたと考えられる。また、これらの検討とは別に露光装置の固有技術アイテムの以下項目について紹介する。
(1)アライメント
光照射装置(照射装置と露光装置に区分される)の場合は、アライメントが単独で存在することは無く、光照射機能と合わせて有意になる。「アライメント」の語意は「整列・整頓」の意味である。しかし、光照射装置の場合は、処理される対象ワーク(以降ワークと呼ぶ)の位置と照射される光の相対位置を合わせることを意味している。また「露光」は化学反応を進めることができる波長の光(露光光)を、処理対象ワークに照射させて、光化学反応を促進させる工程の一般的総称として使われる。アライメントとは照射するべき光の有効領域の中に、処理対象ワークを位置決め設置することである。これらの工程の中でもワークの特定の部分にのみ、光を照射する場合がある。特定の部分にのみ光を照射する目的で金属薄膜の遮光板(マスク)が使われる。この場合はマスクとワークの相対的な位置を決めることが重要な要素となる。このような光の照射を行うことを露光工程、露光装置と呼び光照射装置と区別している。先行製品は光照射装置で上述したマスクを使うような露光は行っていない。従ってアライメント性能はラフで、おおよそ±数百µmであった。これに対して露光装置で要求される精度は±数十µmから±数百nmである。従って先行製品で培われた技術をベースに更に高精度化するためのブレークスルーが技術開発要素となった。具体的な詳細説明は4.4アライメント系に記載されている。
(2)搬送
露光装置で処理するワークは多種多様でサイズ、形状も広範囲にわたる。これらのワークを形状の特長から大きく分けると以下の2種類になる。第一はロール材と呼ばれる形態で、フレキシブルプリント配線板(FPC)が代表的である。第二は枚葉ワークと呼ばれる形態で、シリコンウエハが代表的である。これらの材料に対する搬送方式をウシオでの実施実績に合わせて分類すると、さらに表5-2、5-3のように8分類に区分できる。
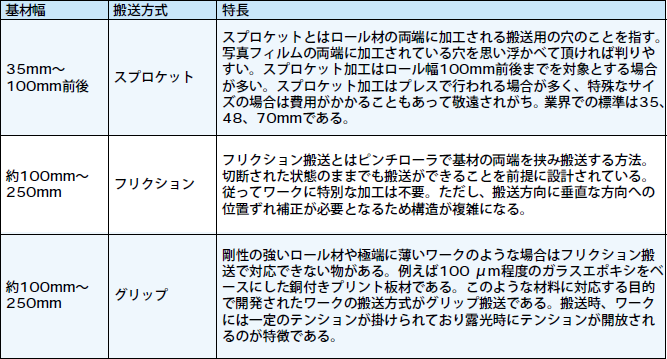
表5-2 ロール材の搬送方式と特徴
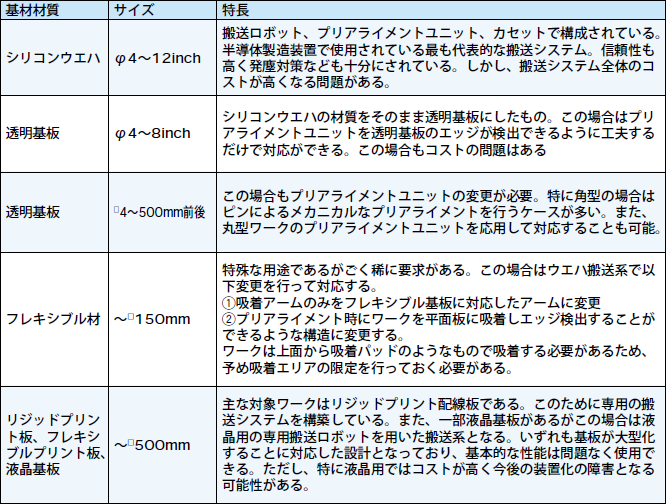
表5-3 枚葉材の搬送方式と特徴
(3)制御
先行製品の技術転用として、最も効果が大きかった項目が制御系である。制御系はソフトウエアおよびハードウエアから構成されているが、いずれも先行装置での成果を利用することができ、開発機関の短縮に貢献した。具体的な例として以下を紹介する。露光装置の開発に際して、その制御対象となるハードウエア(アクチュエータ)はサーボモータ系、デジタルI/O系、アナログI/O系等がある。これらの制御システムはすでに先行製品でシステム開発が完了していた。従ってハードウエアの構成は、ほとんど変更することなく露光装置の開発が可能であった。また、露光量制御など露光機固有の機能を達成するために必要な基板のみ新規開発とした。さらに、ソフトウエアも基本OSの選択やソフトウエア開発ツールなど装置を作る上で必須項目については先行装置で開発が完了していたので、そのまま利用することができた。また、「マンマシンインターフェース系をどのような構成にするべきか」、「メンテナンス時のオペレータ操作をどのように考え、どのように行わせるべきか?」と言ったコンセプトも先行製品でのシステムをそのまま利用した。
(4)システム開発
これまで紹介してきた内容は先行製品での技術要素を、いかに利用して露光装置の開発を行ってきたかであった。しかし、実際の開発では新しく開発すべき課題も多く発生した。本章の最後に露光装置固有の要素技術として、どのような開発要素があったか紹介する。これらの要素技術は多くの開発要素の中でも重要なキー技術で、ウシオの技術の差別化を可能にする要素である。
①投影レンズ開発
投影レンズの開発仕様は対象となる製品のサイズ、感光材の種類、材料の特長を元にしてシステム設計時に決定される。その一例として、例えばオートスケール機能等がある。プリント板はその製造プロセスの工程途中でプリント板自体が伸縮を起こしてしまう。これは素材そのもの、もしくは工程そのものの持っている挙動でなくすることは不可能と考えられている。このためにウシオではプリント板用露光装置のシステム設計時に、これらの伸縮を自動計測して投影倍率を自動で変更できるオートスケール機能を仕様に盛り込むこととした。また、対象となる感光材料に対応して露光波長を確定することなども必要である。技術的な詳細は前項章に記載されている。
②プロキシミティギャップ設定機構の開発
マスクとワークを近接させて露光(影絵方式)する方式をプロキシミティ露光と呼ぶ。簡単にパターンを焼き付ける方式としては最もポピュラーな方法である。業界での認知度も高く、露光装置メーカとしてビジネスを行ううえでは必須の技術と考えた。具体的な課題はマスクとワークをいかに平行に保持するかである。平行度の要求精度は±数µm。設定された平行度の精度で、露光されるパターン精度(線幅忠実度とバラツキ)が決まってしまう。従来、この機能は球面座と呼ばれる特殊な機構が採用されていた。しかし、球面座構造では大きいサイズのワークに対応しづらいといった問題もあった。このためウシオでは独自の3軸ジンバル構造の平行度調整機構を開発した。詳細は3.1.3露光方式に記載されている。また、近年ではマスク下面とワーク表面の距離を直接計測してプロキシミティギャップを設定する方式も開発した。いずれにしてもプロキシミティギャップは同方式での露光性能を支配しているパラメータで、各社の技術力の差が出るキー技術である。
③TTLオンアクシス非露光波長
アライメントの開発投影レンズは一般的に露光波長で収差が出ないような設計を行っている。高い解像力が要求されないような場合は、感光材に反応しない546nm(e線)と露光波長の2線で収差補正を行う。しかし、近年のように高い解像力と広い有効露光領域で露光を行うような場合は、前述の方法による設計が困難となる。従って、高解像力化と有効領域の拡大に対応するには、投影レンズを通った露光波長でマスクマークとワークマークを観察し、相対位置をアライメントする必要がある。しかし、アライメント時に露光光を照射すると、アライメントを行わないマスクとワークの相対位置は当然の事ながら合っていない状態なので、位置が合っていない状態のまま露光されてしまう結果となる。また、ドライフィルムレジスト等の感光材では露光時に着色するのが一般的で、ワークのマークの視認性がアライメント途中に変化する事にもなる。このような問題点を解決するための方法として、TTLオンアクシス非露光波長アライメント(ミラーアライメント方式)を開発した。詳細は4.4アライメント系に記載してある。
(田中米太)