- 光技術情報誌「ライトエッジ」No.39(2013年6月発行)
インターポーザ基板向け露光装置、
ニーズと課題
中澤 芙美
1. スマートフォンの高画質•高性能化とバッテリー持ち時間
ここ数年、需要が急速に伸びてきているiPhoneに代表されるスマートフォンは、当初はディスプレーの解像度が480×320であったが、2011年には960×640、2012年の最新モデルでは1920×1080となり、Full HDの解像力が実現されるようになった。タブレットPCにおいても、iPadに代表されるように、FullHDを超える2048×1536など、非常に高い解像度のディスプレーが実現されている。
このためにデバイスの消費電力が増大し、消費者は、スマートフォンに対して高性能と同時に、より長いバッテリー時間を求め始め、メーカー業界では、消費電力の低減が新たな課題となっている。
2. データセンタの高処理能力化と消費電力増大
急進するスマートフォン•タブレットとともに、そのデータを処理するデータセンタも、非常に巨大化してきている。そのため、その消費電力の低減が強く求められ、バッテリーの制約がないデータセンタであっても、高い処理能力と低消費電力の両立が課題になってきている。
高性能と低消費電力の実現といえば、ウエーハプロセスの微細化に焦点が当たり勝ちだが、最近の最先端のチップでは、チップとデバイスを接続する際の配線での電力損失が、無視できないほどに大きくなっていると言われている。そこで、いかにパッケージングでの電力損失を抑えるかが、パッケージ技術に対する新たな課題としてクローズアップされ始めている。
3. 複数チップ1パッケージ化による課題解決の提案
上述の高性能と消費電力低減の両立という課題を解決するため、新しいパッケージング方式が提案されている。それはLogicチップとメモリを最短距離で配置し、今までの接続方式に比べ、1チップ当り多くの接続端子で接続することにより、高速な信号伝達を低い消費電力で実現しようとするアプローチである。
このメモリと、Logicチップを接続する新しいアプローチには、2種類のアプローチがある。ひとつは3Dと呼ばれるシリコンチップを3次元に積層する方法、もうひとつは2.5Dと呼ばれるメモリとLogicチップを1パッケージ上で隣り合わせに並べ、最短距離で接続する方法である。
3Dについては、実装面積低減の観点から理想的であると言われているが、TSV(Through Silicon Via)と呼ばれるシリコン貫通穴が必要となる。TSVはプロセス技術的には確立されつつあるが、Logicデバイスへの適用となると、信頼性の検証など課題が多く、直近の量産にはTSVの必要がない、2.5Dから量産採用されるというのが業界の共通認識になっている。
4. 2.5D技術、パッケージサイズ大型化と高密度化
メモリとLogicチップを1パッケージ上で隣り合わせに並べ、最短距離で接続するためには、1チップのサイズを超える(2チップより大きな)パッケージが必要となる。そのため、半導体業界のステッパおよびスキャナのフィールドサイズを越える、超面積の大型フィールドサイズが必要とされる。
また、新型のメモリは、今までよりも多くの接続端子を限られた面積の中で作りこみ、高密度でLogicチップと接続する方式である。そのため、現在の最先端パッケージ基板のバンプピッチである100µmピッチの1/2以下の、40µmピッチの接続端子が必要となる。また、高密度な接続端子への配線としては、最先端パッケージ基板の1/2~1/5以下である2~5µmL/Sの微細配線が必要とされている。
つまり、大面積で高解像を両立した、今までにないパッケージ基板が求められている。
5. 高機能化とコスト低減
この新しい2.5Dパッケージング技術として、現在実現されている技術に、2.5Dシリコンインターポーザを用いる方法がある。高価なシリコンウエーハと半導体プロセスを使い、高密度化を実現するというアプローチであり、超高性能なFPGAなどに採用され始めている。
データセンタや高速なインターネットルータなど、設備投資型産業向けのプロセッサならば、超高性能なFPGAなどの高いパフォーマンスに対して、ある程度のコスト増加は許容の範囲とされる。しかし、一般消費者が対象となるスマートフォン•タブレットなどにおいては、高性能を実現し、かつ価格も手ごろな価格に抑えることにより、初めて大きく普及することができる。
スマートフォン•タブレット向けのCPUメーカーからは、普及可能なインターポーザ価格として、1平方ミリあたり1セント以下というコストターゲットが提唱されている。このコストは、300mmウエーハで、約70ドルする半導体用のシリコンウエーハを材料として使用する場合、非常に厳しいターゲットであり、シリコン以外の材料を使う必要があると言われている。
この要求されている低コストを実現するため、代替材料として提案されているのが、有機インターポーザ、ガラスインターポーザである。
6. インターポーザ基板技術へのウシオの今までの実績
ウシオ電機は、1999年に発表したステッパ「UX5」を進化させて、自社開発の大面積投影レンズを使用し、高解像かつ高生産性を両立させた。現在では、最先端有機パッケージ基板の量産用露光装置のリーディングサプライヤとなり、パッケージ基板の先端ロードマップを常にリードしてきた。
その経験の中で、基板特有の変形、反り、厚みムラなどに対応する変倍機能、反り基板/ウエーハ対応機能、適切な焦点深度を持つ超大型高性能レンズ設計のノウハウを磨いてきており、それを、この次世代のインターポーザ向け露光装置に生かすべく、新型露光装置の開発を行ってきた。
7. 新しいインターポーザ技術と、露光装置へのニーズ
これらの新しいパッケージ技術の実現のために、露光装置に要求されることは、
- • 従来のスキャナサイズを大きく超える超面積のフィールドサイズを有すること
- • 2~5µmL/Sを量産できる解像性能と、適切な焦点深度を持つこと
- • 生産性が高く、CoO(装置所有コスト)が低いこと
- • TSVウエーハへの高精度な裏面アライメント機能を有すること
- • シリコンウエーハだけでなく、有機、ガラスなどの様々な基板材料に対応できること
- • 基板の変形に対応できる変倍機能をもつこと
- • 基板反り、厚みムラなどに対応できる、適切な焦点深度を有すること
などである。
8. 新型ステッパ「UX7-3Di LIS350」
このニーズに対応すべく、ウシオ電機は、セミコンジャパン2012において、2.5D/3Dパッケージング向け大 面 積 イン タ ー ポ ー ザ 製 造 用 の 新 型 ス テ ッ パ「UX7-3Di LIS350」(図1)を発表した。
「UX7-3DLIS350」は以下の機能を搭載し、2.5D/3Dパッケージング向けのニーズを満たすものになっている。
- • 78×66mmの超大型ショットサイズ(Field size)の投影レンズ(図2)を搭載
- • 2µmL/Sの解像性能と±10µmの焦点深度
- • 120wphの高スループット
- • <0.5µmのIRアライメント精度
- • 300mmのシリコンウエーハおよび405×350mmまでのシリコン以外の基板にも対応
- • 変倍機能、反り基板対応機能の搭載
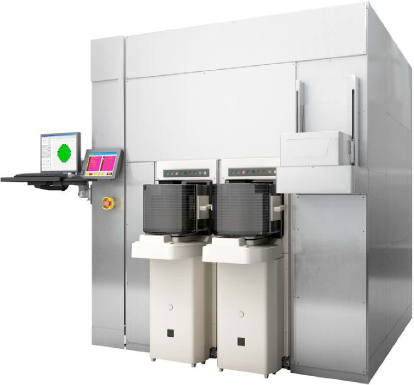
図1. 大面積インターポーザ製造用新型ステッパ「UX7-3Di LIS350」
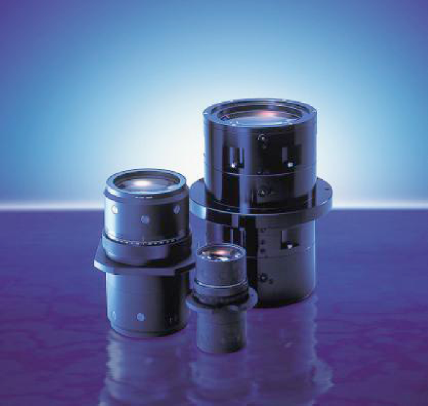
図2. ウシオの独自開発による超大型投影レンズ「UX7-3Di LIS350」シリーズは、最大300mm口径の超大型投影レンズを搭載し、78×66mmの大面積フィールドを可能にしている。
9. まとめ
スマートフォン•タブレットの高性能化と、データセンタの大型化に伴う、半導体の高性能化と消費電力の低減という課題を解決するため、「UX7-3DiLIS350」によって、半導体バックエンドレベルの技術を先端プリント基板レベルのコストで実現した。
今後も、先端パッケージ基板分野での経験とノウハウを生かし、実装業界に新しい価値を提供していきたいと考えている。
論文を探す
今号では、各種の光源(半導体露光用EUV、複写機用LED、高輝度・長寿命・高安定のLDLS、光加熱用ハロゲンヒータなど)や、光の装置・システム(インターポーザ基板用露光装置、スマートフォン・タブレット端末用UVキュア、新規蛍光免疫素子Q-bodyによる薬物検出システムなど)など、2012年春から2013年春にかけて発表した技術や市場動向の論文15件を掲載しました。
シリーズ「大学研究室を訪ねて」では、新しい機能性タンパク質と有機メソッドの創製に挑む、東京工業大学資源化学研究所の上田先生をお訪ねし、開発に成功され、今、話題を集めているQ-bodyを用いた免疫測定法をご紹介しております。
(2013年06月)