Customer Satisfaction and Product Safety
We strive to think from the perspective of our customers and provide products and services with appealing quality that goes above and beyond run-of-the-mill quality.
Enhancing Customer Satisfaction
Global Customer Support Center Initiatives
The Global Customer Support Center plays a pivotal role in supporting Ushio equipment operating worldwide, contributing to the advancement of a society that promotes digital transformation (DX). Striving to be a reliable presence for our customers, the Global Customer Support Center is engaged in ongoing initiatives, including the enhancement of remote maintenance support through cutting-edge technologies such as smart glasses and network devices. Additionally, we are intensifying customer support efforts to adapt to the evolving landscape of the "new normal."
Creation of Business Models with IT
Ushio has adopted a policy of strengthening cooperation among our group companies in our Medium-Term Management Plan announced in July 2020. Accordingly, we have begun to develop an IT infrastructure that enables us to collect information generated globally in a more timely and detailed manner than ever before and to make accurate management decisions.
In addition, we have introduced IoT to improve productivity and quality in manufacturing processes, and RPA (Robotic Process Automation) to improve the productivity of various back office works. Going forward, we will further expand the scope of application to our group companies
We believe it will be necessary to strengthen governance at the same time as we promote the development of a global IT system foundation. We have also begun developing global rules and establishing a security policy in response to policies for group-wide collaboration and cyber-attacks and information leaks.
The entire Ushio group will work toward the achievement of our goals by exerting a grip on governance and aligning the direction of our steps.
BCP Initiatives
In 2012, Ushio established the Company-wide BCP Committee and began efforts to comply with BCP. Ushio began its efforts in the Light Source business, which is its main business, and has been expanding into the Equipment business and the Medical business. In 2014, we established a company-wide integrated BCP response manual and distributed disaster stockpiles (food and beverages, toilets, bedding, daily necessities, and protective equipment) at each base, completing BCP compliance at all divisions.
We establish plans to anticipate and identify risks in advance and for preventing and mitigating risks as well as sustaining business activities, based on such scenarios as a recent large-scale disaster caused by flooding resulting from typhoons and heavy rains, a major outbreak of viral infectious disease, or major earthquake hitting Japan with a seismic intensity of upper 6 or higher.
In response to the outbreak of COVID-19 in 2020, we have formulated a manual for responding to COVID-19 BCP. We are also working to prevent the spread of infections on a company-wide level by reflecting timely and appropriate responses in accordance with the instructions of governments and local governments in each country from 2020 to 2021.
To maintain and improve our BCP, each division conducts BCP response drills and simulations, updates the emergency contact list as well as establishes, verifies, reviews the BCP.
At the Gotemba Division, we conducted drills using the scenario of an earthquake with a seismic intensity of upper 6 or higher as a Nankai Trough Earthquake and etc.
An earthquake with a seismic intensity of 6 higher may result in all fire doors unlocking and closing, even if there is no fire, and in the event of a fire, the fire shutters may close in addition to the fire doors.
In preparation for such a situation, we closed fire doors and shutters to create an extraordinary emergency situation where only one person could pass, and we conducted a drill to evacuate employees and notify the local fire department.
Similar initiatives are being pursued at domestic and overseas production bases, and BCP manuals tailored to the local conditions of each base are formulated and implemented.
We are continuing to develop BCP compliance for our suppliers and partner companies as well. In the evaluation and selection of suppliers for Ushio, the level of BCP compliance is one of the evaluation items. Regular CSR procurement questionnaires also confirm the status of suppliers' BCP responses and raise awareness, and work to further improve the BCP system.
In addition to advancing efforts to improve compliance with BCP as described above, we also revised the system for telecommuting and built a new mobile environment, considering the behavioral restrictions resulting from the spread of COVID-19 as an opportunity to reform work styles.
Initiatives for Quality Improvement
Ushio is dedicated to addressing societal challenges, firmly believing that the paramount importance lies in the safety and quality of the products and services we deliver. Our unwavering commitment is centered on continuous enhancements in safety and quality.
Quality Policy and Product Safety Policy
Aligned with our management philosophy, Ushio has instituted a comprehensive company-wide Quality Policy and Product Safety Policy. These policies serve as the foundation of our endeavors, emphasizing the ongoing commitment to elevate the safety and quality standards of our products and services.
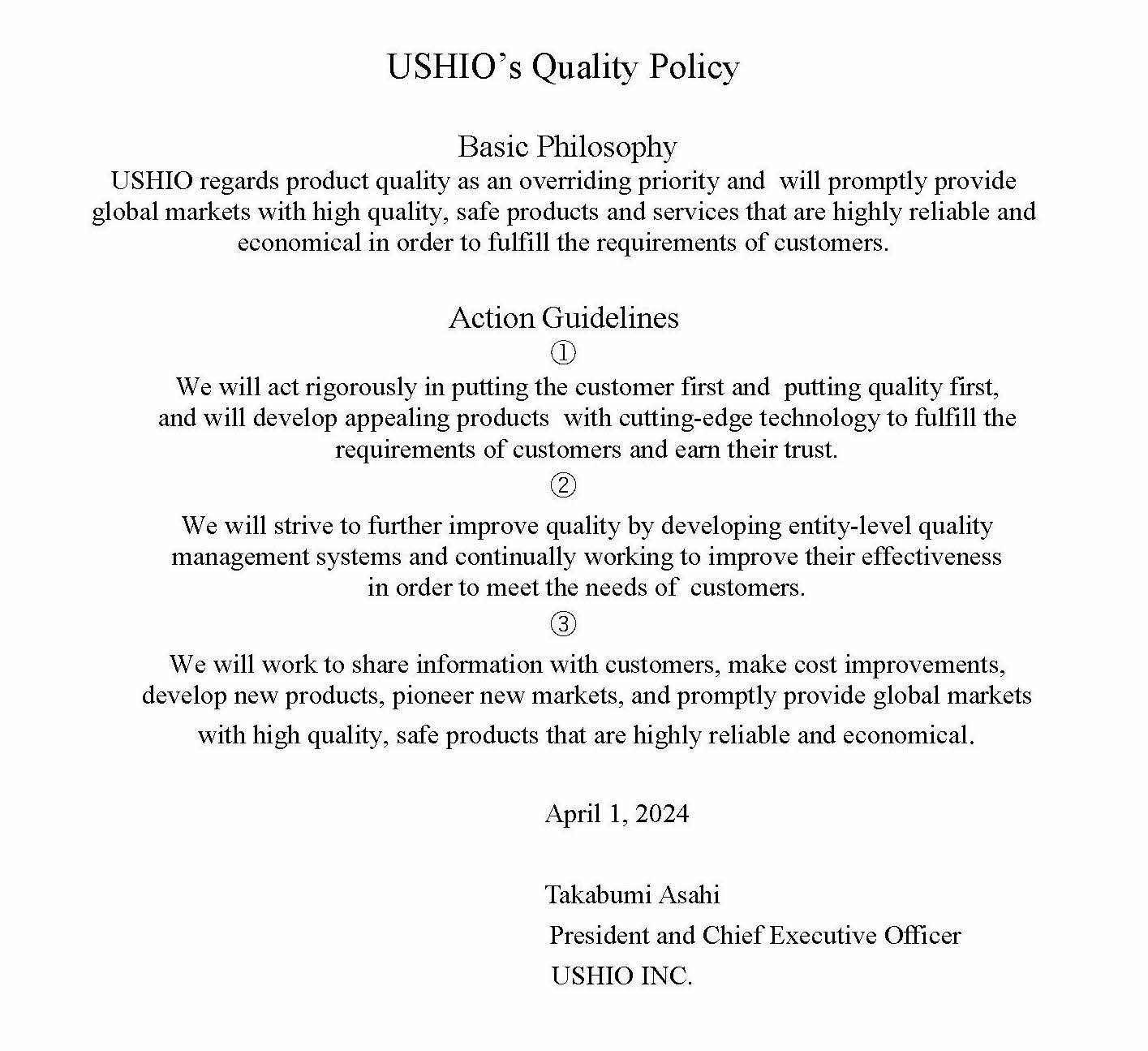
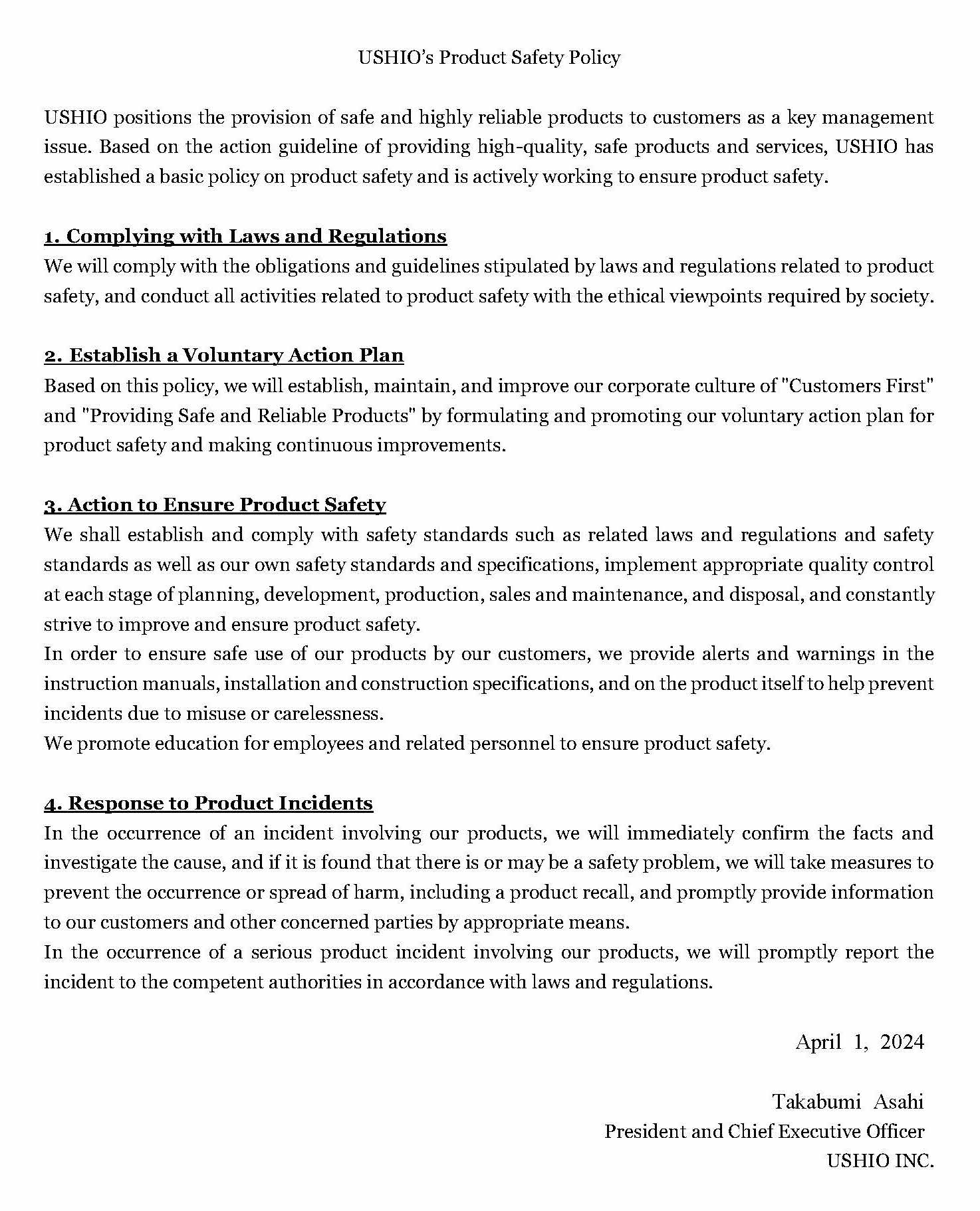
Quality Management System and Framework
Ushio has implemented a robust Quality Policy and Product Safety Policy in alignment with its management philosophy. The company is dedicated to the ongoing enhancement of quality and product safety, facilitated through the implementation of the ISO 9001 quality management system, with the President and Chief Executive Officer holding ultimate responsibility.
Moreover, the Quality Assurance Department actively spearheads initiatives to foster comprehensive quality and environmental management throughout the organization. This includes reinforcing collaboration and development with group companies and overseeing adherence to product safety regulations. The department’s activities are geared towards achieving an optimized management system that contributes to the overall effectiveness of the company.
Quality Enhancement Initiatives
ISO and Product Regulatory Management Department
We are working to improve the efficiency and speed of our quality and environmental management systems. With satisfying ISO requirements, we are able to respond swiftly to customer demands, maintain and improve systems for solving social issues and contributing to the development of our business, and carry out fundamental reforms at the workplaces so that they do not become activities for rules. This activity leads to the provision of safety and reliable products and services and higher customer satisfaction.
Every division, department, and group company, with the Quality Assurance Department at its core, collaborates to streamline the overall quality management system. The aim is to transfer best practices in quality maintenance seamlessly across different business units and enhance quality standards within the framework of ESG management. In addition, there are "Sustainably Reducing Environmental Impact" and "Building a Robust Management Base" in the "Five Management Focuses" that accompany the shift to ESG management. We are promoting the development of environmentally conscious products utilizing ISO tools and strengthening product safety management in line with business expansion aimed at solving social issues.
We keep working to improve the level of quality assurance so that the Ushio Group as a whole can continue to provide high-quality, safe products and services by promoting collaboration with overseas production affiliates and Group companies.
UPS Activities; Enhancing Factory Automation and Digital Transformation
Since 2011, the Harima Division has been implementing activities called UPS (Ushio Production System) from a diversified perspective by integrating the improvement activities (TQC and TPM). It has been cultivated over the years in order to respond flexibly to rapid changes in the business environment and transform it into a high-quality and highly efficient division. We have the three pillars; "Small Group Activities," "Talent Training," and "Loss Reduction,"; in order to acquire the ability to identify problems and share problems with colleagues and improve them strongly. In particular, since 2018, we have been striving to raise the level of these indicators, which are visible in terms of the figures for each of the three pillars. The results of these efforts have been disseminated outside the company through presentations, exhibitions, and lectures, which has also contributed to local communities.Based on this UPS improvement activity, we continue to promote activities aimed at reducing all types of losses in lamps and module products. At the same time, we strive to create a bright working environment, mutually acknowledge each other, work in friendly competition, and aim to be our aspiration. We continue our efforts to recognize, learn, and enhance each other for growth to tomorrow.
In the future, we will expand the scope of our activities to include not only the Harima Division, which is the mother plant of Ushio, but also domestic and overseas production bases and our group companies.
Promoting Digital Transformation in Manufacturing Lines
Until now, we have achieved to reduce variations and strengthen process management by introducing a process management support system (Eagle Eye・Yellowfin) that visualizes each process in on-time for lamps and module manufacturing, and by introducing robotics. Furthermore, we are building a system to reduce costs and shorten lead times by analyzing data using a process management support system to analyze defects and improve factory productivity.
Organizational Reform
To bolster production activities that align with societal and market demands, Ushio Inc. has consolidated five production-related functions—production planning, procurement, manufacturing, logistics, and quality assurance—into the unified Production Division. This is through our SVC (Sustainable Value Creation) activities, which lead to the reduction of environmental impact and the creation of digital and other sustainable values, while also leading to improvements in our workplaces, comfortable working environments and productivity improvements. Ultimately, this will enable us to realize our vision of becoming a "light" solutions company.
Quality Initiatives in Power Supply Production for Sustained Stability
Ushio’s power supply products, being fabless, are manufactured by contractors in Japan and overseas. Facing challenges like the discontinuation of semiconductor and electronic component production, along with difficulties in parts acquisition, Ushio is actively ensuring stable production and elevating quality. This involves reinforcing ties with suppliers and systematizing parts information for effective management and operation. Particular emphasis is placed on achieving long-term stability in the production of power supplies for industrial applications. Collaborating closely with contractors, Ushio addresses issues related to succession training and business continuity at production sites. Efforts are underway to establish a long-term stable production system by systematically structuring the production process and expanding collaboration with new suppliers. Moreover, Ushio is dedicated to ESG-oriented initiatives, emphasizing the development of products with reduced environmental impact and the establishment of sustainable production systems.
Product Safety Management System
The Product Liability Committee oversees the management of product safety and provides biannual reports to the President, detailing the status of company-wide product safety activities, issues, and reviewing policies and improvement targets. Following these reviews, the Quality Assurance Department, along with the Subcommittee on Product Regulatory and Design and Engineering Department, spearheads initiatives to ensure high levels of product safety and quality throughout the entire company.
Specifically, to mitigate product safety risks, the Quality Assurance Department evaluates the need for designating products subject to product safety management at the initial stage of product development. For newly designated products, a comprehensive product safety risk assessment is conducted at each stage of the design review process.
Product Safety Management System Chart
Response to Product Incidents
In the event of a product incident, Ushio prioritizes the safety of our customers by diligently gathering information, verifying the cause of the incident, and confirming the facts. If deemed a serious product incident, Ushio collaborates as a unified entity to implement appropriate measures ensuring customer safety. As part of this response, Ushio assembles an Emergency Product Liability Committee, reports to the pertinent authorities, the President, Group CEO, and senior management, and engages in discussions to formulate effective countermeasure policies.
Information on Serious Product Incidents
In adherence to the Consumer Product Safety Act and product safety management regulations in Japan, Ushio discloses information concerning serious product incidents suspected to be caused by a product. This includes incidents where the cause is uncertain, yet there is suspicion of product involvement.
Serious Incident Response Chart
Safety of Lamp Products
The categories of chemical substance contained in the lamps are listed on the material safety data sheet (SDS). To ensure safe and proper product handling, the names of substances contained in products as well as information on the hazards and toxicity of these substances, precautions in handling, and information on environmental impact are contained on the SDS. For inquiries regarding SDS, please contact Ushio's sales representatives.