光技術情報誌「ライトエッジ」No.23/特集 ウシオの露光装置(2001年11月発行)
2. アプリケーション例と使われる装置
2.1 アプリケーション例と使われる装置
2.1.1 はじめに
ウシオの露光装置のアプリケーションは、多種多様な分野にまたがっている。多種多様なアプリケーションがあるからこそ、ウシオが露光装置をひとつの事業として確立できたという見方もできる。
6章でウシオの露光装置の開発経緯が述べられているが、その成り立ちを簡単に触れることから本項を始めたい。
1984年当時、ウシオは、産業用特殊ランプの専門メーカとしての地位が築かれており、その一環として、半導体フォトリソグラフィ用ランプとして超高圧水銀ランプが、ステッパ、アライナメーカに供給され始め、大きな柱に育ちつつあった。
システム事業部は、その超高圧水銀ランプから出る紫外線をミキシングし、フォトリソグラフィに適した高効率かつ高精度な質の光を出すための照明系(ランプハウス)を製作する仕事を手掛けていた。
そのランプハウスがきっかけで、TAB露光装置が生まれたが、市場規模が(当時は)小さく、景気の波にかなり左右された。そこで、TAB露光装置で蓄積した露光技術を他の用途に展開することになり、生まれたのが、露光装置UXシリーズである。
ところが、当時露光装置は、数社あるステッパ、アライナメーカが先行しており、当然市場はとられており、後発のウシオが入り込む隙がない。そこで、先行メーカがフォローできない、かつ、する気もない隙間の市場をターゲットにせざるを得なかった。
当時、ステッパメーカ向けランプの営業担当者が、ランプハウス(商品名マルチライト)の販促を担当をすることもあり、先行露光装置メーカが行かない市場、また露光装置メーカが対応しないニーズをある程度知っていたため、まずはそれを攻略することから販売活動を始めた。
その環境のおかげで、客先との会話はある程度こなせ、ウシオに興味をもっていただくことができ、もちろん、技術の努力のおかげもあって、比較的好調なスタートを切ることができた。
上述の様な成り立ちを経た関係上、ウシオがターゲットとする市場は、大手ステッパメーカが手を出さない小さな市場で、ステッパほどの解像度(コスト含む)は要らないが、従来のアライナ(コンタクト、プロキシミティ露光)では不満足というニッチ市場である。そのような市場では、一用途だけでは需要が限られているため、他用途へ展開せざるを得ず、結果的に多種多様な用途、アプリケーションを対象とするようになった。
用途別販売実績を表2-1に記載する。
これら多様なアプリケーションの中から、ここでは、TAB・FPCとプリント基板について述べる。
(土屋 純一)
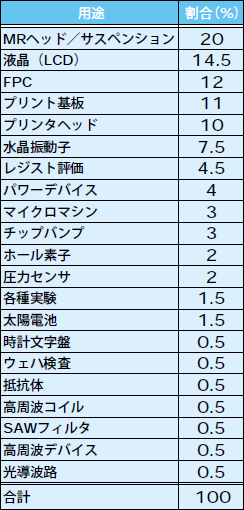
表2-1 用途別販売実積
2.1.2 TAB・FPC
(1)アプリケーションの変遷
フレキシブル性の強いポリイミドを基材とした配線基板であるTABは、ここ10年間で、アプリケーションが大幅に変ってきている。1988年以前は、時計、電卓といった比較的市場規模、成長性とも小さいマーケットに限定されていた。それが、1988年以降、LCDを駆動させるIC(ドライバIC)に採用され、ノートPCの成長に伴い、需要が拡大した。
主用途がLCDドライバICオンリーの時代から脱皮したのは、1998年のBGA/CSPと呼ばれるパッケージ基板の登場からである。このパッケージ基板とは、ICチップをプリント基板に実装するための中間板(インタポーザ)の役割をはたし、サイズがICチップとほぼ同じなため、CSP(チップ・サイズ・パッケージ)と呼ばれる。載せるICは、メモリ、DSP、ASICなどの比較的ピン数の少ないもの(多ピンICは、後述のリジッド板を使用)であり、携帯電話、DVCなどの携帯情報端末に採用されることで、一気にブレークし、更なる需要拡大へと繋がった。
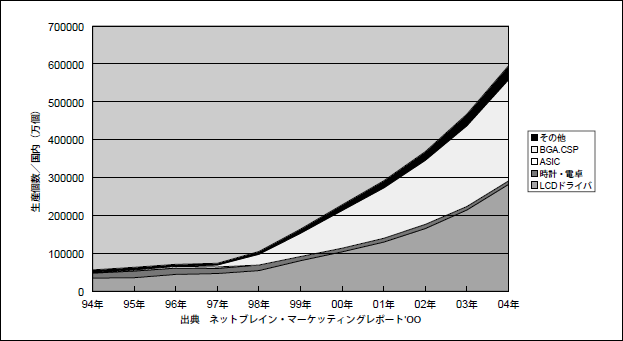
図2-1 TAB用途別生産個数推移
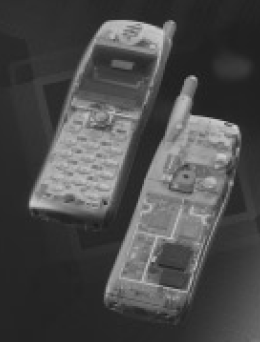
図2-2 TAB使用例
(2)アプリケーションの将来動向
LCDドライバは、COG(チップ・オン・グラス=ガラス基板上の電極端子に直接ICを接続する方式)などのTABを使わない実装方法が出てきているものの、限界があり、TABの延長線上のテクノロジーとして、COF(チップ・オン・フレキ)が主流となると考える。COFの大きな特徴は、従来ドライバICのみを基板上に実装していたものが、同一基板上にチップコンデンサ等も実装することであり、その結果としてテープの巾広化(105mm→150mm、250mm)、ファインピッチ化(40µmピッチ→20µmピッチ)が進むことである。
また、市場としては、LCDパネルがTV・CRTの代替として使用される様になれば、一気に市場が拡大(5倍位?)することになり、将来有望である。
BGA/CSP分野は、LCDドライバほどではないにしても似たようなトレンドを歩むと思われる。図2-3に、用途別のTABテープのサンプル写真を示す。
(3)露光装置のあるべき姿
上述の様な技術動向を示すアプリケーションに対し、装置のあるべき姿は以下と考える。
ひとつは、ファインピッチ化、巾広化に対応した大口径、高解像力PJレンズ(~Φ200、~5µmL/S)を搭載した従来装置のアップグレード機。もうひとつは、巾広テープ(250mm)ではあるが、ラフピッチで生産性重視のニーズに対応した一括プロキシミティ露光機である。
現在、上述2機種とも製作、開発に着手しているが、リーディングカンパニーという立場からも、早期に完成度高く立上げたい。
(土屋 純一)
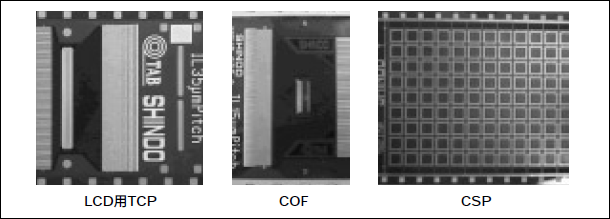
図2-3 TAB用途別サンプル写真
2.1.3 プリント基板
(1)市場動向
携帯電話、ノートPC等の電子機器の小型・軽量化、高速・高機能化に伴い、ICチップも高集積・高速化し、実装技術もQFP(リードがパッケージの4辺に設けられたタイプ)から、前述のBGA/CSP等の新実装形態へと移行してきている。それに伴い、ICチップを搭載する側のプリント基板も微細化、高密度化が要求され、ICチップと同様、配線を積層する方式であるビルトアップ基板の役割が重要になってきている。ビルトアップ基板のニーズとして一番大きいのは、微細化のため、高精度で位置決め(層間の重ね合せ)をして、ビアホール(層間を接続する目的であけられた穴)に対するランド(配線用パターンの先端に設けた丸型の導体パターン)の径を小さくし、ランド間の配線パターン本数を増やしたいというものである。このニーズは特に、ICチップが直接搭載されるパッケージ基板での要求が強い(ex.ランド径/ビア径=Φ60µm/Φ30µm)。(図2-4)
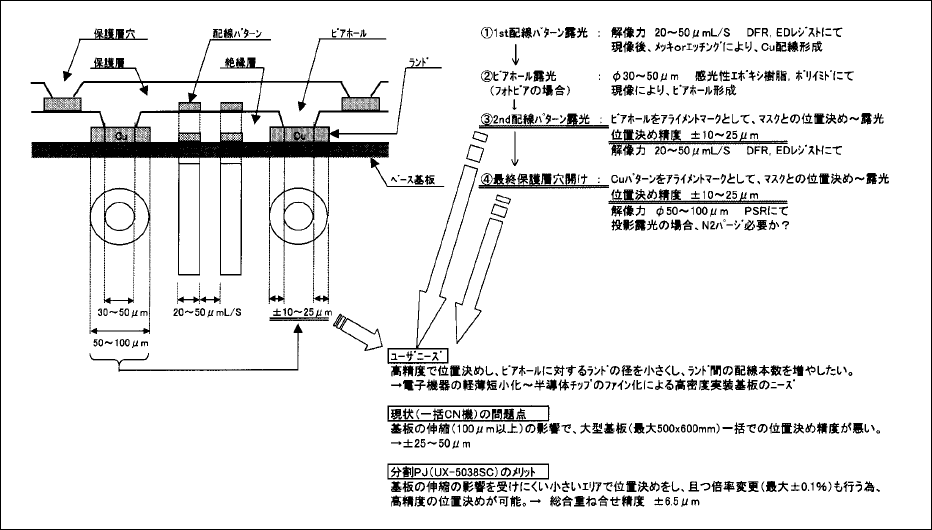
図2-4 パッケージ基盤市場ニーズとUX-5038SCの優位性
(2)露光装置に求められる機能
これらのニーズに対応するためには、基板全面の重ね合せ精度(前述ex.では±15µm)を向上させる必要があるが、従来の一括露光方式では、基板の伸縮(100µm以上)の影響で位置ズレが激しく、達成が困難である(歩留りが低下する)。
そのため、分割露光という手法がとられることになる。100µm以上伸縮するプリント基板でも、小さいエリアに限定すれば伸縮は大幅に軽減され、その分、重ね合せ精度が良くなる理屈である。ウシオは、この分割露光を、プロジェクション(投影露光)方式で世界に先駆け、1999年4月にリリースした(図2-5、図2-6)。
5038SCは、プロジェクションだからできるオートスケール機能(マスクの投影倍率を可変して基板に露光する機能)を持ち、分割露光でも吸収できない基板の伸縮バラツキに対応し、更なる重ね合せ精度の向上を達成している(±6.5µm)。
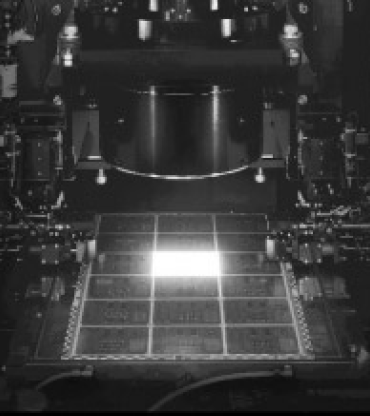
図2-5 UX-5038SC 露光部
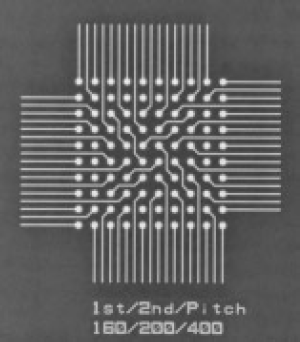
図2-6 重ね合わせサンプル
(3)アプリケーションの将来動向
プリント基板(ビルトアップ基板)を使用したパッケージ基板は、多ピン(700ピン以上)のIC(MPU、ASIC等)やMCMであり、最終製品は、PC等の情報機器である。多ピンのICでプリント基板を使う理由は、チップサイズが大きいための信頼性確保とコストであると思われる。
これは、今後もこの方向で進み、かつ携帯電話等の情報端末が高機能化(PC化)してくれば、搭載ICも多ピン化され、プリント基板を使うことになるだろう。
(4)露光装置のあるべき姿
現状、5038SCは、最先端のハイエンドパッケージやMCMの試作開発用途が主であるが、ここにきて量産のフェーズに移ってきた。量産対応の装置として今後、額縁露光、素数露光(マスキングブレード)、銅箔下パターンでのアライメント(X線アライメント)、ファインパターン(高解像力レンズ)に対応していきたい。
(土屋 純一)
2.2 TABの市場・技術動向
2.2.1 これまでの歴史
(1)TABの起源
1960年代のICの接続は、ワイヤボンディング(W/B)方式によりICのパッドとリードフレームをひとループずつ手作業により接続していた。当時、半導体メーカの製造工場の隣には女子寮があり、労働集約的な作業方法がとられていた。工場の壁には各作業者のボンディング不良率の比較成績表が貼り出され技能を競わせていた。
ICボンディングを自動化、省力化し品質を向上させるために2方向からアプローチが始まった。ひとつはW/Bの自動化であり、パターン認識とプログラム制御による全自動ボンダーの開発へとつながっていった。他方はワイヤレスボンディング方式により問題を解決しようとする方向であった。この方式では、ビームリード法、フリップチップ法、スパイダ法、ミニモッド法など種々の方法が提案された。
TAB(Tape Automated Bonding)はGE社から1971年に発表されたミニモッド(Mini Mod)方式1)(図2-7)が起源である。
各種の方式の中でGEのミニモッドはテープ・アッセンブリ方式を採用している点に大きな特徴があり、工程の合理化に著しい効果があり現在の発展へとつながっていった。TABはICのパッドとテープのリードを全ピン同時に接続(ギャングボンディング)するので多ピンICの接続効率が著しく高い。TABパッケージはTCP(Tape Carrier Package)と呼ばれ、小型、薄型、軽量を特徴としており、これらの特性を生かした各時代の商品が作られてきた。
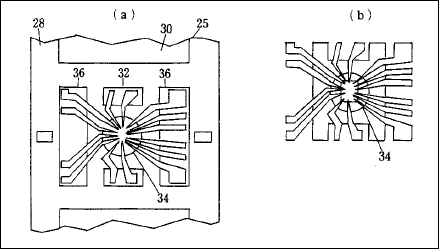
図2-7 GEのミニモッドのパテント図
(2)TABの製造
TABに使用されているテープをテープキャリア(フィルムキャリア)と呼んでいる。開発当初テープキャリアは米国では8、11、16、35mm幅などのテープが使用されていた。日本では35mm幅から始まり70mm、次に48mmのテープ幅の順序で実用化された。テープのスプロケット孔および付随する規格は米国映画規格が元になっている。
ICパッケージとしてのTCPの規格は日本のEIAJと米国のJEDECとの共同作業により1993年に制定された。
テープをその構造から分類すると1層、2層と3層テープに分類される。日本では3層テープから始まり2層テープも途中から生産が始まったが、3層テープが主流を歩み今日の世界のデファクト・スタンダードとなった。TABの開発の歴史は日本でつくられたと言っても過言ではなく、TAB製造の材料、機械、製造方法は日本が発信基地となった。3層テープの製造工程を図2-86)7)示す。長尺状の加工はファイン・パターンの製造に適しており、今日の隆盛を招く源となった。ファイン・ピッチ化のキー工程は露光工程であり、最初はマスク密着方式で露光していたが事故が多く投影式の開発へと進んだ。初期の投影レンズは市販品を改良したタイプを使用していたのでテープのファイン・ピッチ化が進むと解像力不足が問題となり、ファイン・ピッチの加工を可能とする優れた専用投影レンズ付きの露光機が開発され、現在のファインテープ加工を可能とする基礎となった。TCPのインナー・リード・ピッチのファイン化を図2-9に示す。最初、350µピッチ40ピン(電卓)から始まったテープは年々ファイン化が進み、1983年にはサーマル・ヘッドが登場し急激なファイン・ピッチ化が進んだ。今日ではファイン化はLCDドライバが先導している。
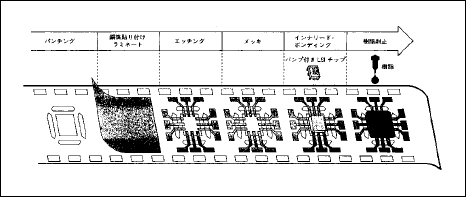
図2-8 TABの組立行程
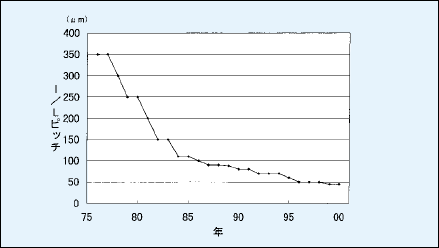
図2-9 インナー・リードピッチのファイン化
(3)テープ材料の開発
TABの主材料は、ポリイミド・ポリイミド基材、銅箔そして接着剤である。TAB方式は高耐熱性のフイルム基材が無ければなりたたなかったといえる。1960年代は米ソの宇宙開発の競争時代の真っ只中にあり、高耐熱性のポリイミド・フィルムはその中で生まれた。ポリイミド・フィルムのカプトンは1965年にデュポン社から上市された。カプトンは優れた耐熱性(図2-10)に加えて、熱収縮率が小さく寸法安定性に優れ、強度が強く、電気特性が良いなど今までの樹脂に無い優れた特性をもっている。更にポリイミド・フィルムの特筆すべき性質は線膨張係数の値が銅と近いことである。これはテープの反りを防ぐ意味で重要なポイントであり、他の高耐熱性樹脂は全てその値が高く(図2-11)テープとして使用できない。1984年に開発された宇部興産のユーピレックスSは引っ張り弾性率が高く剛性を必要とするTABテープにむいており現在の主材料となった。テープの歴史の中でガラス・エポキシ基材が多量に使用された時期があった。ガラエポ基材はガラスクロスにエポキシ樹脂を含浸させた構造になっており、剛性が非常に高く、価格もポリイミド・フィルムと比較して安く一時期電卓用材料(図2-12)として多用された。しかし、電卓用としてのテープの衰退、ファイン化に伴うクリーン化の必要性から特殊目的以外は使用されなくなった。表2-2に各テープ材料の特性を示す。
回路を形成する銅箔には、接着剤とのピール力が強く、裏面粗さが小さい特性が要求される。裏面粗さはエッチングの切れに影響するので、ファイン・ピッチ化が進むほど裏面粗さの小さい銅箔が必要となり各種の新しい銅箔が開発がされた。TAB用の銅箔には電解銅箔が使用されているが一部の製品には圧延箔、合金箔が使用された。当初の銅箔厚は35µmであったがファイン化が進むにつれて、25、18、15µmと薄くなっていった。
基材と銅箔を接着する接着剤は、当初はフレキ用接着剤を使用していたがテープへの要求特性がきびしくなり専用接着剤が開発された。接着剤にはエポキシ、ポリアミド樹脂などが用いられており、接着力、耐熱性、パンチング性、ラミネート性、電気特性などさまざまな要求項目を満足させる必要がある。テープのファイン化に伴い電気特性を向上させる必要があり、この面でも接着剤の改良が行われ、3層テープの高性能化に寄与した(図2-13)。
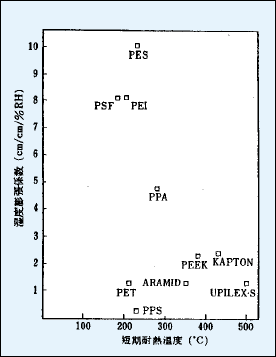
図2-10 フィルムの短期耐熱性と湿度膨張係数
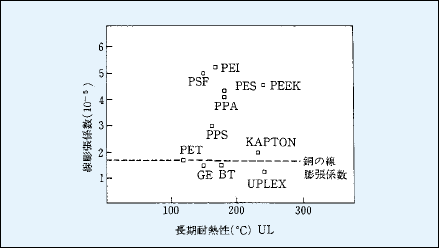
図2-11 フィルムの長期耐熱性と線膨張係
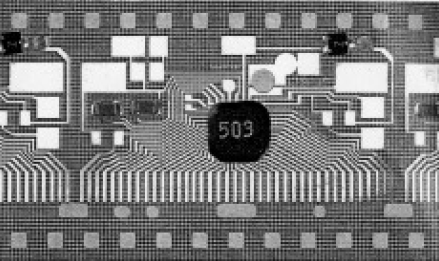
図2-12 ガラスエキポシテープ(電卓)
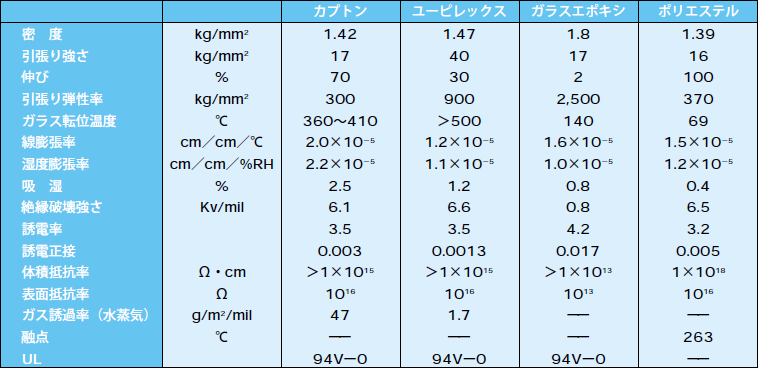
表2-2 テ-プ材料の特性
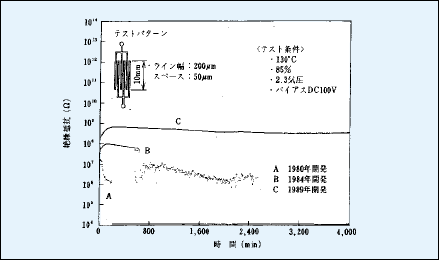
図2-13 接着剤の開発と絶縁特性
(4)テープ使用製品の歴史
GEのミニモッドが発表されてから3年後の1973年にTABを使用した製品として始めてポラロイド社からインスタントカメラSX7010)が発表された。SX70に使用されたTABはフェアチャイルド社が製作した。
米国ではその後TABは主としてリードフレームの内部接続用として使用され、1980年代のなかばにその使命を終え、以後、1980年代の後半に多ピン時代を迎え日本のテープを使用してTABアッセンブリが再開された。
図2-14にTABを使用した商品の歴史を示す。日本ではTABが1974年にアナログ(図2-15)およびデジタル腕時計に最初に使用されたのが始まりである。クオーツ化された腕時計はそれまでの機械式と比較して精度は格段に向上した。デジタル腕時計用のTAB(図2-16)はデジタルの流行の終了と共に終わったが、アナログ時計には現在に至るまで使用されている。1976年に液晶表示の薄型電卓に使用され、ポケット電卓の開発競争の始まりとなった。TABを使用した電卓は多量に生産されたが台湾への生産移管に伴い生産は終了した。0.8mm厚の超薄型カード電卓は究極の軽薄短小のTAB実装を実現した。
1977年にはコンピューターのメインフレームに採用された。メインフレーム用のTABは数社に採用され1990年代のなかば近くまで使用されていた。サーマル・ヘッド(図2-17)には1983年から使用され多ピン、狭ピッチ接続の牽引役となった。IL(インサーリード)ピッチは110µmから始まり最終には55µmピッチとなった。
1980年代のなかばになるとTCPはASIC用の多ピン時代を迎えた。当初は200~300ピン、次いで300~500ピンそして近年には500~900ピンまで多ピン化されている。ASICの多ピン製品はスライドキャリア(図2-18)にいれて個別にアッセンブリ工程を流す方式も採用された。
1980年代後半になると液晶表示(LCD)向けのLCDドライバ(図2-19)が立ち上がり、1990年代になると液晶パネルの大型化が進みCRTの代わりとなるモニタが出現し、現在のLCDドライバの全盛時代となる。
1993年にはノートブックPCのCPUに採用され、狭ピッチのアウターリードボンディング技術12)の普及に貢献した。1990年代のなかば近くになると多ピン実装をより容易にする目的でボール・グリッド・アレーが登場してきた。TBGAにはTCPタイプ(図2-20)とW/Bタイプとがある。TBGAの小型版であるCSP(チップ・サイズ・パッケージ)(図2-21)も同時期に生産が始まり携帯電話に多数使用されるようになった。
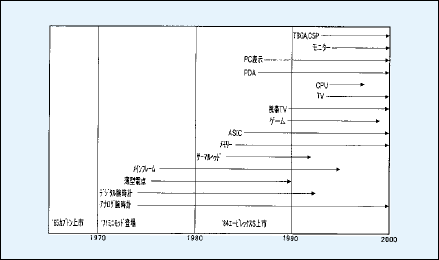
図2-14 TAB商品化の歴史
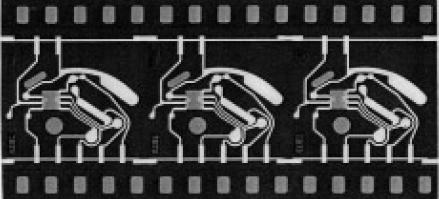
図2-15 アナログ腕時計(日本最初のTAB)
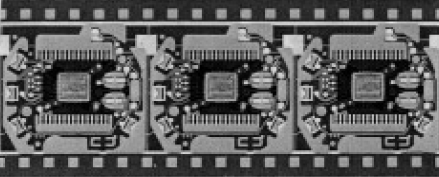
図2-16 デジタル時計
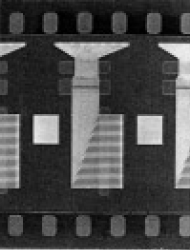
図2-17 初期のサーマルヘッド
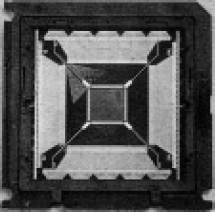
図2-18 スライドキャリア入りASIC
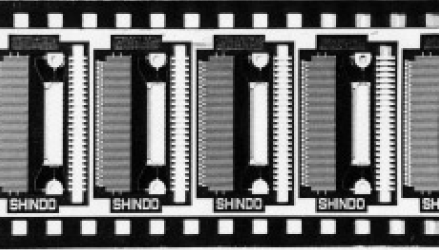
図2-19 LCDドライバー
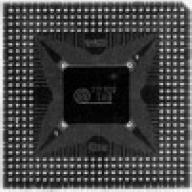
図2-20 TBGA
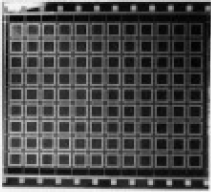
図2-21 CSP
(齋藤 公彦 新藤電子工業株式会社)
2.2.2 将来展望
(1)はじめに
TAB(Tape Automated Bonding)は近年のLCD(Liquid Cristal Display)市場の急成長を追い風にして順調に普及を続け、多ピンLSI(Large Scale Integratedcircuit)の実装技術の一つとして拡大してきた。TABテープはその特徴を、ファインピッチ対応、プリント基板や液晶パネル実装の際のフレキシビリティ、リールtoリールによる高い生産性などを特徴とし、LSI一次実装基板(インターポーザ)として定着してきている。一方で、BGA(Ball Grid Array)やCSP(Chip Size Package)、COF(Chip on FilmまたはChips on Flexible)等のあらたなパッケージの登場によりTABは絶え間なく進化し続けている。
本稿では「TABの将来展望」とのタイトルで今後の市場動向や技術動向を探ってみた。
(2)TAB市場の将来展望
これまでのTABのアプリケーションは、量的にはLCD市場がメインであり、今後暫くはそうありつづけよう。ボリュームゾーンとしては、ここ数年はLCDの時代が続くと言えそうだ。パネルの種類は色々あるものの、アモルファスシリコンは大型パネルに、LTPS(Low Temperature PolySilicon)は中小型にと棲み分けが進むとみている。中小型パネルのセグメントは携帯電話やPDA(Personal Digital Asistance)などの情報端末向けで、今後も急成長が見込まれている。この分野は、次々と新製品が登場し、セットメーカ間の開発競争も激しく、ハイテクノロジ-の結集でありながら陳腐化に至る期間が短い、いわばハイテク・コモディティ市場とも言えよう。この傾向は、ますます半導体に力を入れつつあるセットメーカのデジタル家電化の流れの中で強調されるであろう。パッケージ基材の供給者の立場からは、家電として大量に販売される商品への低コスト化に加え信頼性保証に対する要求は一層厳しくなるであろうと考えている。
BGAやCSP、WLP(Wafer Level Package)等のパッケージにもテープ基材が利用されている。これはLSIの微細化と稠密化のトレンドにのった動きであり今後も拡大するであろう。図2-22は1999年のITRS(International Technology Roadmap for Semiconductors)によるテクノロジートレンドを示している。
LSIの速度、容量、多機能化の付加価値追求、半導体メーカの生産性向上、セットメーカの「軽薄短小」に対する要求等々がドライビングフォースとなり技術を進歩させ、一定期間(概略4年毎)にデザインルールの変更がなされ、メモリ容量は一桁アップしてきている。
今後もこのトレンドは続くとするのが大方の見方である。
TAB市場全体としては、LCD、BGAやCSP、その他各種ICカード、プリンタ印字部、PDPドライバ等のアプリケーション毎に調査機関などが予測している。(図2-23)00-04年の平均成長は35mmテープ換算パーフォレーションベースで約30%/年の成長が見込まれている。これまでは、急成長する需要の中で供給面の課題が指摘され続けることが多かったが、これからは伸びる市場への対応力に加え、さらに高信頼性や低コスト化の提案をTABメーカの課題として受け止め、真摯に取り組む必要があろう。
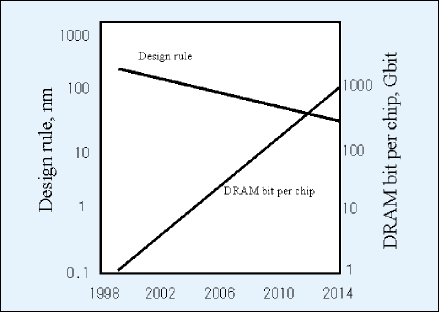
図2-22 Semiconductor Technorogy Trend. ITRS(1999)3)
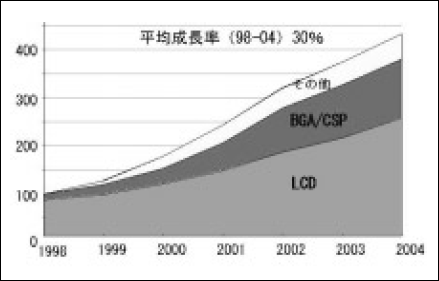
図2-23 世界のTAB市場の予測35mm幅換算のパーフォレーション数を
98年を100とした指数表示日経マーケットアクセス、
テクノシステムリサーチのデータ、一部推定
(3)TAB技術の将来展望
技術面の将来展望を一口に言うと「軽薄短小」に加えて、「3次元」がキーワードになる。ファイン化の進展に加えて、2層や3層以上の多層構造がテープ基材にも要求されてくる。
「軽薄短小」の流れを図2-24に示す。このロードマップは大型LCDの表示の微細化、ドライバICの多ピン化の計画から作成されている。従来のファイン化のトレンドを踏襲しており、2005年にLine/Space15µmをベンチマークとしている。COF(Chip on Film)対応領域はL/S 35µm以下が中心になると考えられている。また、いわゆる「スーパーコネクト」に代表されるL/S 10µm以下超ファインピッチの領域については、TABは大きな期待が掛けられてはいるが(図2-25)、材料面など解決すべき課題も多い。また、プロセス面でもベーステープが50µm、25µmと薄くなるにつれテープ搬送に課題があり、装置メーカの対応が待たれる。
一方のキーワード「3次元」は、フレキシブル加工を施したTABに抵抗・コンデンサなど複数受動部品を実装する、特に携帯電話向けで要求がある。さらに実装の高密度化が見込まれ配線引き回しの関係から2メタル配線の動きがある。
BGAやCSPにも2次元方向での集積度向上に加え、チップを重ね合わせて縦方向へ積層する技術が近年使用されている。図2-26のようにチップをフエイスアップに積層し、いずれのチップへも基板からワイヤーボンドするスタックドCSPや一次実装基板側でImplant法によりバンプを形成し積み重ねる(スタッキング)方法(図2-27)などがあり、3次元化の動きは今後ますます活発になってこよう。
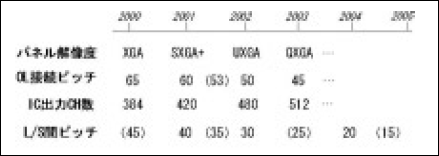
図2-24 TABテクノロジーロードマップ
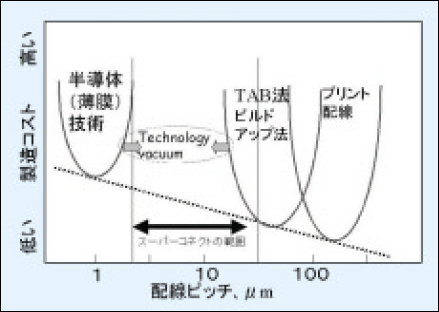
図2-25 各種配線形成技術の配線ピッチとコストの関係
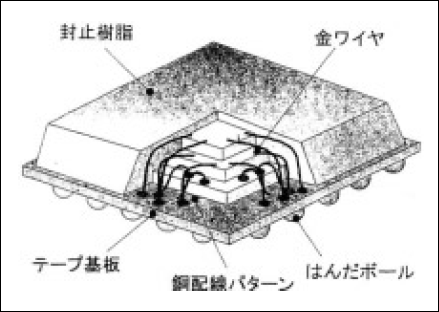
図2-26 スタックドCSP
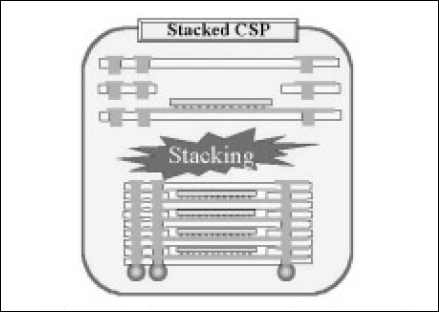
図2-27 Implant法によるスタッキングの概念図
(4)おわりに
TABの市場・技術展望と題して、TABはファインピッチを軸に今後も成長を続けるが、ハイテク・コモディティ化、3次元化対応への課題をキーワードとして導出した。三井金属/エム・シー・エスはファインピッチ化対応と各種IC実装へのフレキシビリティな対応でTABの裾野を広げつつ、量産対応能力と高信頼性を基本に顧客にとってのパッケージ・ベストソルーションを今後も提案し続けていく所存である。
(茂住 洋史 三井金属鉱業株式会社/株式会社エム・シー・エス)