光技術情報誌「ライトエッジ」No.24(2002年4月発行)
JPFA技術セミナーウシオ電機講演
(2002年2月)
「露光装置に求められる課題と
新露光装置の開発コンセプト」
日時:2002年2月19日
場所:中野サンプラザ
講師:プロジェクト推進室 田中米太
電子部品業界の状況を見ると、市販の電子機器は小型軽量化、軽薄短小の言葉に代表されるようにどんどん小さくなっています。これらの変化のポイントは実装密度が飛躍的に向上してきていることだと考えられています。また、実装密度を上げるためのキーワードの一つは実装する電子部品自体の小型化ではないかと思います。要するに電子機器の進化に伴って、実装される部品自体もCSP実装等で代表されるように小さくなってきているのです。
BGA、CSPという実装形態が新しく加わってきたことにおいて、特徴的なことは、特にTCPと呼ばれる実装部品が台頭してきたことではないかと思います。BGA、CSPにはリジッド基板を使ったものもありますがTABテープ技術を使って製作することもあります。数年間のTAB露光装置出荷台数の推移などを見ていますと、詳細な数字はお話できませんがBGA、CSP用途の出荷大半を占めるような時期もありました。TABはLCDのドライバー用の配線部材として知られていますが、その他の用途への展開も最近は具体化てきています。これらの部品を作る装置として、ウシオの露光装置はかなり高いシェアでお客様に使用して頂いています。一方、FPCと呼ばれる形態のワークを処理する場合はプロキシミティ、コンタクト、プロジェクションの色々な方式の装置を使うことがあります。
上記に申し上げましたとおり小型軽量化、軽薄短小の流れのキーワードとして電子部品の実装密度が向上している、実装密度を上げるために部品自体の形態が変わってきているということがポイントではないかと我々は位置付けております。
ではウシオ電機はこのような状況に対してどのような取組をしてきているのかをお話します。ウシオ電機には大きく分けて2つの事業部があります。ウシオ電機に対するお客様の認識はランプを作っている事業(ランプ事業部と言っています)です。こちらは工業用の特殊光源を作っている部門でワールドワイドであることでも有名だと思います。これとは別の、もう一つの事業部が私たちの所属しているシステム事業部です。システム事業部では各種の特殊光源を使った製造装置の開発製造の対応を行っています。どのようなものを作っているかというと、紫外線UVを使った乾燥装置や硬化装置などが4種類位と露光装置があります。露光装置は大きく3つに分類されています。一つは、高密度プリント基板用のステッパです。2つ目がTAB・FPC用途ということで、テープ材を取り扱う露光装置です。テープ材というのはロール状に巻かれているものをロールのまま搬送して、逐次1ショット、1ショット打っていくというタイプです。この中に2機種、3機種あります。一番新しいタイプのTABテープ用の露光装置をご紹介します。これはテープ自体の幅が96mmのものを使用して、48mm幅のものを2条で取り、Φ150mmくらいのエリアで露光していきます。投影露光という方式を使っているのでマスクとワークが離れているというのが特長です。ちなみに最も大きいレンズではマスクとワークの距離は1.3m位です。3番目が、半導体の後工程用途ということでの装置を作っています。こちらのものは、UX-4031SCという8インチのウエハを一括で投影露光するというタイプのものやUX-3000シリーズというものがあります。こちらは、プロキシミティコンタクト露光装置です。いずれも半導体の後工程に導入するわけですが、なるべく一括で生産効率が良くて安い装置を供給する目的でこのような装置を開発しました。半導体用のステッパを使うと、非常に生産のコストがかかります。生産コストをなるべく押さえたいということがお客様のニーズです。
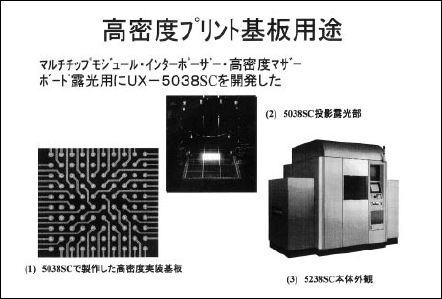
図1 高密度プリント基板用露光装置
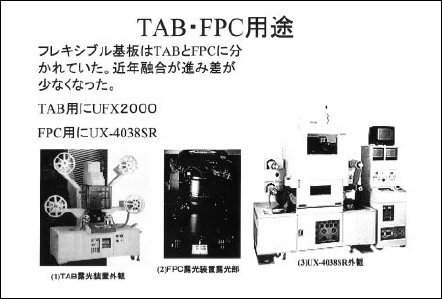
図2 TAB・FPC用露光装置
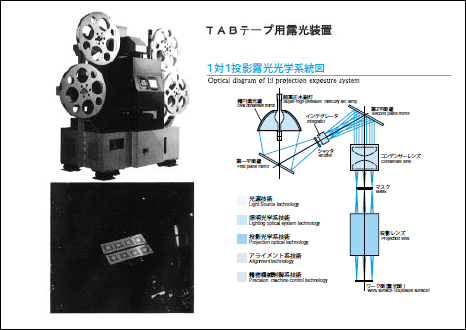
図3 TABテープ用露光装置
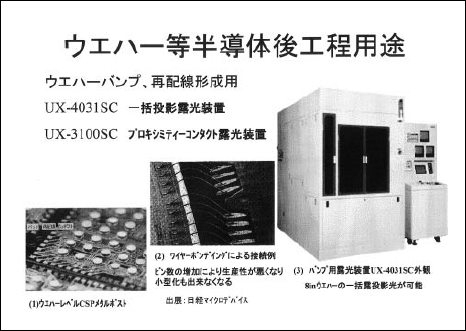
図4 半導体後工程用露光装置
このような装置を開発するにあたって、我々の固有技術として投影レンズがあります。投影レンズというのは大きな虫眼鏡のようなもので、等倍もしくは倍率を変えてマスク像を投影レンズに対して下の方向に結像させるという機能があります。
次にこのレンズの開発をどのように進めてきたのかについてお話しいたします。露光装置といわれるものの中で投影露光方式を取る装置としては半導体のステッパが最も代表的で有名です。図6はウシオ電機の開発したレンズの性能マップで、縦軸が解像度、横軸がフィールドサイズです。電子部品業界に貢献するためにはどのような投影レンズが必要かを考えたとき、なるべく有効口径が大きく、解像力を要求されない領域を狙っていこうということになりました。このことは半導体ステッパや液晶ステッパとは明かに異なり、これが我々の特徴でもあり最初にあった開発コンセプトです。当時(10数年前)はプロキシミティ露光機が全盛時代でした。このような状況でウシオが最初に開発したのはTABテープ用の露光装置でした。有効口径が約Φ100mm、解像力が10~12µm Line/Space程度でした。それ以降は通常のハイエンド領域に向けての開発は行わず、もう少し違った領域で開発を継続することになりました。このあたりの開発の歴史的な経緯は弊社発行のライトエッジという技術情報誌の23号において特集記事になっていますので興味のあるかたは請求してください。(システム事業部営業部:TEL045-901-2572)
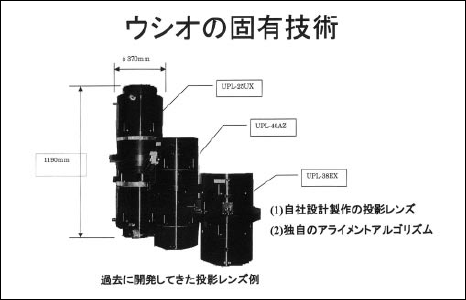
図5 投影レンズ
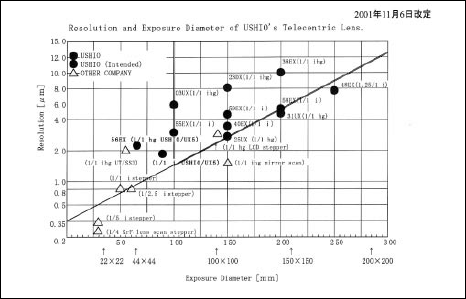
図6 解像度とレンズ口径
次にウシオの露光装置はどのようなものか、投影レンズを使った技術とは具体的にどういうものがあるかご紹介します。
まず投影露光方式についてです。露光光学系は照明光学系と結像光学系からできています。超高圧水銀ランプの光を第一平面鏡と呼ばれるもので折り返すことによって、必要な波長の切り出しを行います。その後インテグレータを通して整合を取り、第2平面鏡で折り返します。そして投影レンズに合わせるようにコンデンサレンズで光の整合性を取ります。さらにマスク像を投影レンズを介してワーク面に結像します。これが投影露光です。図7に示してありますが、上から入ってきた光は、一度入射瞳と呼ばれる部分に集光、光の強くなる部分を通って広がっていく構造になっています。
次に投影露光方式は、露光方式全体から見た場合、どのような位置づけなのかということについてお話しします。全体の露光方式は大きく分けて接触露光と非接触露光かに分かれます。接触露光はマスクとワークを物理的に接触させ、影絵のようにして露光するタイプで、接触の度合いによってハードコンタクト露光、ソフトコンタクト露光などと呼ぶことがあります。一方、接触式でない場合、一つはプロキシミティ露光というものがあります。ワークとマスクの間を通常であれば数10µm、多いもので100µm前後離して露光するタイプのものです。もう一つが投影露光という投影光学系を使った露光です。投影露光も、分割露光といわれている、いわゆるステッパーと、一括露光の二つに分類できます。
各露光方式に対するQCDを図9にまとめました。コンタクトの露光機は値段を安く装置を簡単にして、歩留まりは多少悪くても解像力を上げたいというケースで使われます。プロキシミティというのは、マスクとワークのすき間をあけて露光しますから、影絵がぼけるのと同じように解像力が多少悪くなります。1:1のミラープロジェクション、レンズプロジェクションというのはレンズを使って結像させますので、露光の原理が多少違ってきます。縮小レンズ光学系の半導体用のものは解像力が非常に高いのですが、代わりに焦点深度が非常に浅くなってしまいます。
装置のイニシャルコストは当然半導体用ステッパが一番高く、数億~10億近いものまであるのではないかと聞いています。それに比べて、コンタクト、プロキシミティというのは非常に安く、ミラー、レンズプロジェクションというのは中間くらいのポジションです。決定的に違うのは、非接触タイプのものはマスクの寿命が半永久的であるということです。コンタクトタイプの場合にはどうしても汚れ、欠損の問題を発生させてしまいます。
このようなことを理解していれば、露光装置の選定の時に役立つのではないでしょうか。
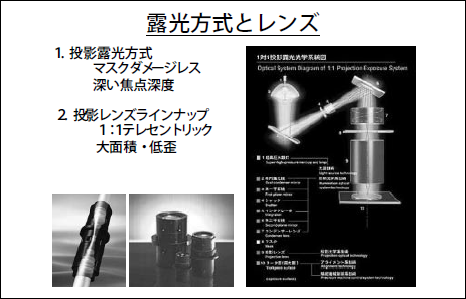
図7 投影方式とレンズ
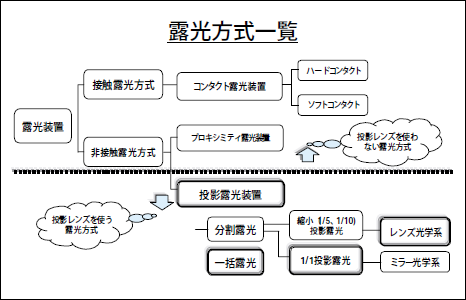
図8 露光方式
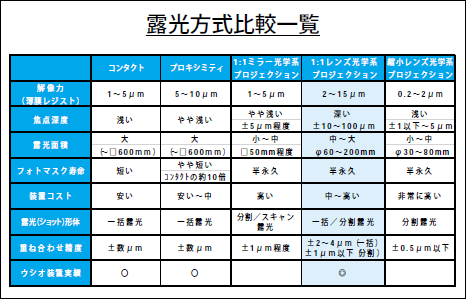
図9 露光方式の比較
投影露光で、マスクとワークがこんなに離れてしまって、どうやってアライメントするんだろうかということが大きな問題となることがあります。これはウシオのパテントになっているのですが、On AxisTTL alignmentという図10のような方法を用います。
マスクがあって、そこに露光光を当てて、まずアライメント用のカメラのキャリブレーションをしてしまいます。通常、露光光を当てますから、この時にワークが下にあっては露光されてしまいます。そこで、ワークが無い状態で行います。マスクとカメラのキャリブレーションが終わった状態で、上からの光を止めて、そのままの状態でワークを搬入します。そして、今度は非露光波長の光をワーク照明光として導入して、先程キャリブレーションしたマークに対してワークを動かしてアライメントします。この基本的なロジックでアライメントすることによってマスクとワークの相対的な位置をかなり精度良く露光することができます。これが弊社がOn AxisTTL alignmentと呼んでいるアライメント方法です。この動作をステップごとにn回のショットで繰り返し、全面を露光していくというのがアライメントのステップの代表的な例です。
もう一つの例として、オートスケールというものがあります。プリント板等の電子部品用材料の代表的なものは、材料自体が非均一な伸縮をしてしまう問題があります。それをクリアするためにウシオでは、実際のワークの伸縮率にあわせて、1ショット、1ショット投影倍率を調整するという機能を設けています。実際の基板のシュリンクを測りますから、毎回どの程度伸縮しているか、それに合わせるためにどの位を動かすかということを常に計測して、フィードバックをかけるという動作をしています。このような要求に対応するためにオートスケールと呼ばれる機能を装備しています。
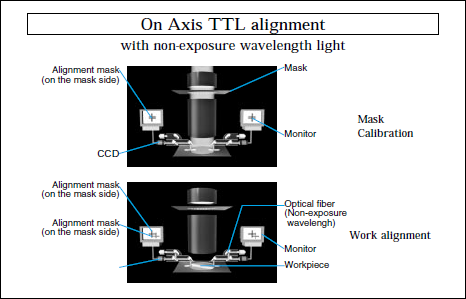
図10 On Axis TTL alignment
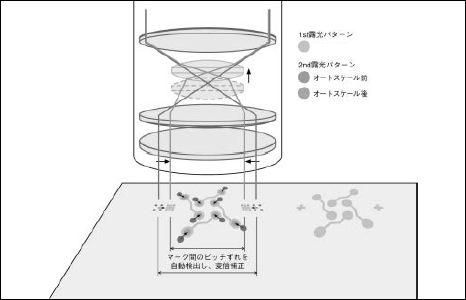
図11 オートスケール
また、投影レンズもテレセントリックというタイプのレンズを使って基板のうねりに対応するようなことを考えていますので、伸縮倍率調整にはズーム機構が必要となります。もう少しラフにやるためには、ダイバージェントタイプのレンズを使ってレンズの位置を動かすという手法もあります。しかし、基板のうねりには対応できないので、どうしてもテレセントリックタイプのレンズにズーム機構を使う方法が必要になると考えています。
投影露光技術の基本要素としては、投影レンズそのもの、アライメント、スケーリングの3つの技術があります。前述の通り、これらのそれぞれにウシオの基本技術のコンセプトが盛り込まれています。
PCBステッパUX-5038SCに、なぜ先程の技術が導入されたのかということについてお話しします。ウシオでは一括露光でガラスマスクを使って340×500や600×500というものを処理した場合、歩留まりを考えると重ね合わせの限界は±25µm程度が現実的なのではないかと考えました。20µm、15µmのところを狙うケースもあるのですが、ワークの中央部分や比較的部分的なところだけで製品を作るという使い方をしなければ実現は難しいと考えられます。これがPCBにステッパーを投入した第一の理由です。
第2点目は、パターンがファインになってパターン欠損で歩留まりが上がらなくなってきます。50µmL/Sまでは生産効率その他を考慮した場合、コンタクト露光機で行うのが良いと思います。弊社では30~50µmL/Sまでをグレーゾーンと呼び、どちらの方式が良いと断定することはできず使用状況によると考えています。30µmL/Sを下回ってくると、投影露光機の方が有利になってきます。この二つの問題点、解像力のアップに対する歩留まりの低下と、重ね合わせの歩留まりの低下が、プリント板用ステッパを開発した最初のトリガーです。
では、ワークの非均一性はどの程度あるのでしょうか。以前に採取したデータを見ると実際のばらつきは数十PPM程度あります。伸縮には傾向が無く、ショットにも基材にも依存せず、でたらめな伸び縮みをしています。
では、従来のものに対してステップ&リピートはどのようにシュリンクの効果を軽減しているのでしょうか。従来方式の一括露光では、基板の伸縮がダイレクトに精度が悪化します。一方ステップ&リピートではショットごとにアライメントしていくので、基板自体のシュリンクについてはこれによってアライメント精度が向上します。次に、オートスケールがあります。今までガラスマスクを使っていて伸縮が大きい場合は、伸縮率をある程度推定してマスクを数水準用意していたと思います。しかし、オートスケール機能を使えば、マスクは実際のワークの倍率に合わせて全ショット自動で合わせることができます。この二つが決定的な違いです。
では、このような機能を備えたことで、実際にどの程度精度が向上したのでしょうか。同一条件、同一プロセスで測定した結果、Contact to Contactで±45.3µm、Stepper to Contactで±18.2µm、Stepper toStepperで±4.33µm程度の精度が達成できました。その評価プロセスは、図13の通りです。
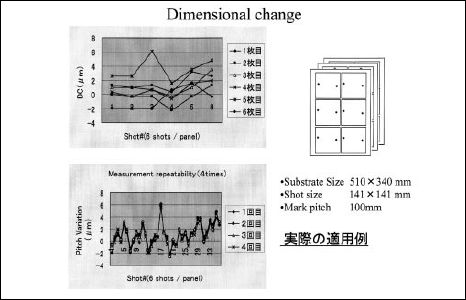
図12 ワークの非均一性
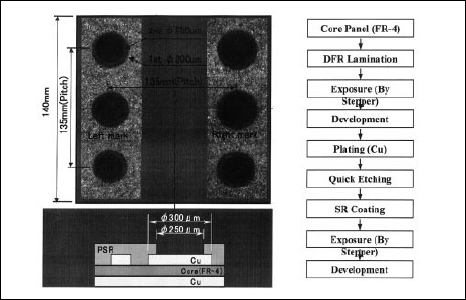
図13 評価プロセス
次に解像力やCDはどうだろうかということですが、まずレンズのラインナップを図14に示します。有効露光エリアはΦ150、Φ200、Φ250の3つに分けられます。そして、露光量の多いものに対しては、ihgの3線で露光します。UPL-58EXというのはドライフィルム用のものです。そして多少口径を大きくしたい場合はΦ250、ハイエンドでフリップチップ実装用基板などを対象にする場合は、Φ150で5µmという解像力のものを使うこともあります。
CDとはCritical Dimensionと呼ばれている線幅の安定性です。図15は15.6µmL/Sの設計値に対して、実際の線幅のばらつきがどの位あるか、かつDOFというピントの位置をわざと50µmずらした時の変化を測定したものです。これは何を意味しているかというと、基板が反ってうねる場合に、あるところは50µmくらい上になり、あるところでは50µmくらい下になるというケースが想定されます。従ってジャスピンだけでなく、わざとピントをずらした位置でのCD、つまり面の線幅のばらつきをデータとして取ったものです。図15ではレンジで50µmのDOFでレンジ2.1µmなので15.6µmL/Sに対して±1µm程度で仕上がっています。最近の厳しい要求では、20µmL/Sで5%くらいまでに入れてくれということもあります。
そして解像力と重ね合わせのロードマップですが、ウシオの装置で15µmL/Sを実施されているケースもあります。エッチングでもTABなどでは40~50µmピッチあたりを狙われています。そこでウシオでは図16のように比較的ラフで高露光量の領域、ドライフィルムのような配線を作る場合のハイエンドのものを開発しており、さらにUX-5という後継機の計画もあります。業界でも実装部品内蔵基板などのサブミクロン程度の解像力を要求されるようなケースもでてきています。
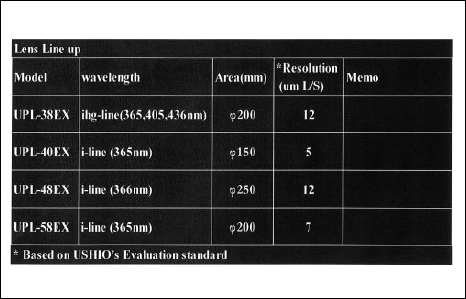
図14 レンズのラインナップ
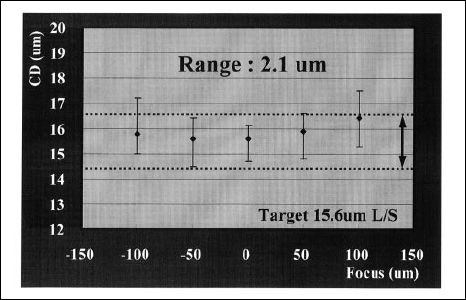
図15 ワークの非均一性
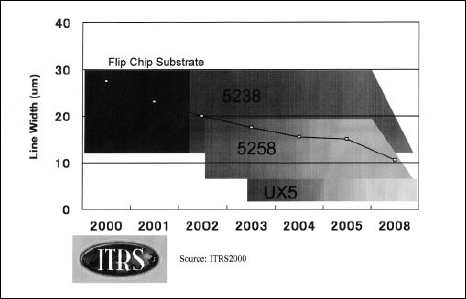
図16 ワークの非均一性
最後にマスクについて説明いたします。図17はマスクのQCD比較図です。ウシオでは装置用の推奨マスクとして一番性能の安定している、クロム膜の石英ガラスマスクを推奨させていただいております。しかし、現実的な組合せとしてはエマルジョン膜+ソーダライムとクロム膜+ソーダライムが半々くらいです。マスクに対して特に注意しておかなければいけないのは、エマルジョン+ソーダライムでは光の吸収率がかなり高いことです。弊社経験ではΔtで20~30°Cの温度上昇がある場合もあり、マスク自体の熱伸縮が懸念されます。特にピッチ寸法などの精度が厳しい場合などには石英を使用された方が好ましいと考えられます。しかしコストが大きく違いますので、常にQCD比較を頭に置いておく必要があります。
次に、マスク膜面保護の目的でペリクル膜を取りつけることがあります。これは半導体の方ではごく一般的に使われていて、枠の上に薄い膜が貼り付けてあります。通常投影レンズを通して結像する場合は、必ずマスクパターン面の像がワークに転写されます。この時マスクパターン面にゴミが付着した場合はゴミもそのままワークに転写されてしまします。この問題を回避するために、このペリクル膜をマスクのパターン面から数ミリ離れた(スタンドオフ)位置に貼り付けておくのです。そうすると、ゴミが飛んできて付いたとしても、ペリクルの膜より内側には入れず、ピントのずれた位置に結像するため、ワーク面上の結像像には影響が無いのです。プリント板の生産工程の中にマスクの掃除がありますが、ペリクル膜を使用した場合は、マスクの欠損が原理的に存在せず、検査も掃除もいらず、信頼性も上がります。しかし一方、ペリクルを貼り付ければその分ランニングコストが高くなってしまいます。従ってこれらのこともQCDでの比較の元に方針を決定する必要があります。
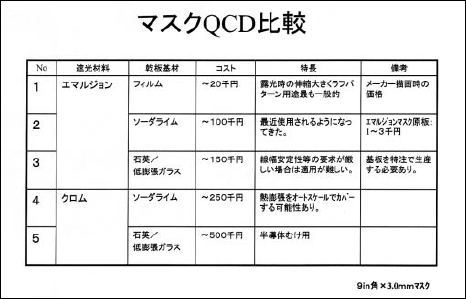
図17 マスクのQCDの比較
今までお話してきた内容をまとめますと次のようになります。
- 1.電子機器の高性能高機能化には電子部品の実装密度向上などが今後も必要となります。
- 2.ビルトアップ法での高密度から部品組み込み基板など高密度化にSOPやBBUL等、次の技術動向が出てきました。
- 3.従来のコンタクト露光手法では精度も限界に近づき、技術的には半導体技術のような最先端技術との融合が望ましい。しかし、COOは最重要項目であり、コンセプトが半導体製造装置でコストがプリント板業界でも満足できるといった融合となります。
- 4.露光装置以外にも半導体製造装置の様なコンセプトを持った電子部品用途の各種装置が今後必要になるでしょう。
- 5.合わせてクリーンルーム設備など製造環境整備、インフラ整備が進めなければなりません。ウシオ電機における露光装置の今後の開発はこれらの傾向を前提に、お客様のニーズにマッチした装置を開発することです。
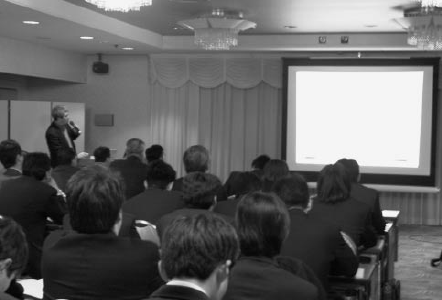
セミナー風景